7182
Технології лазерного додавання металу
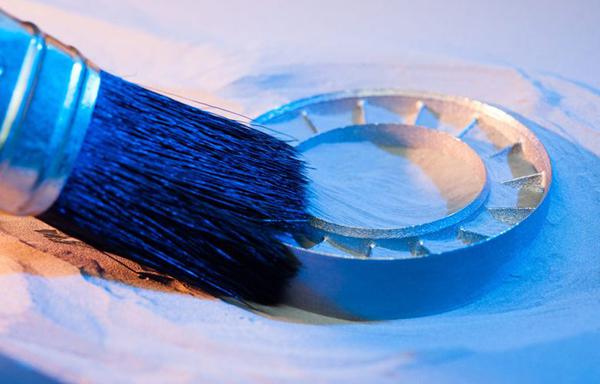
У цьому огляді я спробував в популярній формі надати основну інформацію про виробництво металопродукції методом лазерного добавленого виробництва - порівняно новий і цікавий технологічний метод, який виник в кінці 80-х і став перспективним технологією для маломасштабного або єдиного виробництва в галузі медицини, літаків і ракетної техніки.
Коротко описують принцип роботи заводу з виробництва добавок з використанням лазерного випромінювання можна наступним чином. Пристрій для нанесення і вирівнювання порошкового шару знімає порошковий шар від живильника і рівномірно розподіляє поверхню підкладки. Після цього лазерний промінь сканує поверхню цього шару порошку і плавленням або зимою утворює продукт. Наприкінці сканування порошкового шару платформа з виробленим виробом нижча до товщини наноситься шар, а майданчик з порошком піднімається, а процес нанесення порошкового шару і сканування повторюється. Після завершення процесу, платформа з продуктом піднімається і очищається від невикористаного порошку.
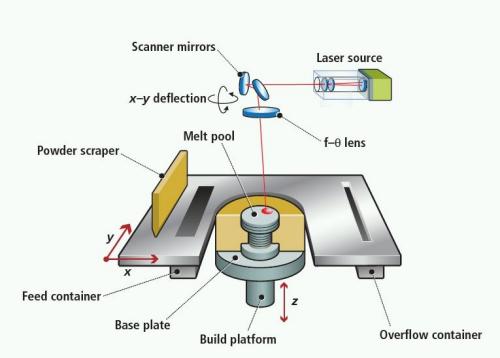
Однією з основних частин в добавках виробництва рослин є лазерна система, яка використовує CO2, Nd:YAG, ітербінові волокна або дискові лазери. Встановлено, що використання лазерів з довжиною хвилі 11.1 мкм до теплових металів і карбідів бажано, так як вони 25-65% краще поглинати випромінювання, що генерується лазером. У той же час за допомогою лазера CO2 з довжиною хвилі 10,64 мкм найкраще підходить для матеріалів, таких як полімери та оксидна кераміка. Висока ємність поглинання дозволяє збільшити глибину плавлення і варіювати параметри процесу в більш широкому діапазоні. Як правило, лазери, що використовуються в надбавних роботах у безперервному режимі. У порівнянні з ними використання лазерів, що працюють в імпульсному режимі і в модульованій якості через їх велику пульсову енергію і коротку тривалість імпульсу (наносекунди) дозволяє поліпшити міцність зв'язку між шарами і зменшити температурний вплив зони. У висновку можна відзначити, що характеристика лазерних систем, що використовуються лежанки в межах: лазерна потужність - 50-500 W, швидкість сканування до 2 м / с, швидкість позиціонування до 7 м / с, діаметр фокусованої плями - 35-400 мкм.
Крім лазерного, електрон-променевого опалення можна використовувати як джерело опалення порошку. Цей параметр Arcam запропонував і реалізовано у своїх установках у 1997 році. Монтаж з катодом-променем характеризується відсутністю рухомих частин, так як електрон пучка зосереджена і спрямована на використання магнітного поля і дефлектори, а створення вакууму в камері позитивно впливає на якість продукції.
Одним з важливих умов у виробництві добавок є створення захисного середовища, що запобігає окислення порошку. Аргон або азот використовується для виконання цього стану. Однак використання азоту як захисного газу обмежена, що асоціюється з можливістю утворення нітридів (наприклад, AlN, TiN у виробництві виробів з алюмінієвих та титанових сплавів), що призводять до зменшення пластичності матеріалу.
Методи лазерного добавленого виробництва відповідно до особливостей процесу фільтрації матеріалу можна розділити на селективну лазерну зиму (Selective Laser Sintering (SLS), непряме лазерне замикання металу (ILMS), прямий лазерний зимів металів (пряме лазерне замикання металу (DLMS)) та вибіркове лазерне плавлення (Selective Laser Melting (SLM)). У першому варіанті герметизація порошкового шару відбувається через твердофазну зиму. У другому - через просочення пучка пористої рами, попередньо утвореної лазерним випромінюванням. Пряма лазерна зима металів базується на ущільнювачі за допомогою механізму рідкофазного замикання через розплавлення легкоплаваючого компонента в порошковій суміші. У останньому варіанті герметизація відбувається через повне розплавлення і поширення плавлення. Варто відзначити, що ця класифікація не універсальна, оскільки один тип добавки виробничого процесу може експонувати механізми ущільнення, характерні для інших процесів. Наприклад, в DLMS і SLM може виникати твердофазні зимівлі, що відбувається в SLS, в той час як в SLM, може виникати рідкофазні зимівлі, які більш характерні для DLMS.
Вибірковий лазерний Sintering (SLS)
Суцільнофазний вибірковий лазерний зимівля не широко використовується, оскільки відносно тривалий вплив при лазерному променю необхідний для більш повного потоку об'ємної та поверхневої дифузії, в'язкої витрати та інших процесів, що відбуваються при зимуванні порошку. Це призводить до довгострокової лазерної операції та низької продуктивності процесу, що робить цей процес неекономічно. Крім того, виникають труднощі з утриманням температури процесу в інтервалі між точками плавлення і температурою суцільнофазних зимів. Перевага твердої фази вибіркового лазерного зиму є можливість використання більш широкого спектру матеріалів для виготовлення виробів.
Непряме лазерне зимування металів
Процес, відомий як непряма металева зима, був розроблений DTMcorp of Austin в 1995 році, що належить 3D-системам з 2001 року. Процес ILMS використовує суміш порошку і полімеру або порошку, покритого полімером, де полімер виступає в якості пучка і забезпечує необхідну міцність для подальшого термообробки. На стадії термообробки полімер дистильований, каркас зміщений і пористий каркас просочений метал-лігами, в результаті чого виходить готовий продукт.
Для ILMS можна використовувати порошки обох металів і кераміки або сумішей. Підготовка порошкової суміші з полімером здійснюється шляхом механічного змішування, в той час як вміст полімеру становить близько 2-3% (за вагою), а в разі використання порошкової суміші з полімером, товщина шару на поверхні частинок становить близько 5 мкм. В якості пучка використовуються епоксидні смоли, рідке скло, поліаміди та інші полімери. Температура дистиляції полімеру визначається температурою його розплавлення і розкладання і в середньому 400-650 oC. Після дистиляції полімеру пористість виробу перед просоченням становить близько 40%. При просоченні печі нагрівається 100-200 ° С вище точки плавлення просочення матеріалу, так як при підвищенні температури кут змочування знижується і в'язкість плавлення знижується, що вигідно впливає на процес просочення. Як правило, просочення майбутньої продукції здійснюється в заправці алюмінієвого оксиду, який грає роль опорної рами, так як в період від дистиляції полімеру до утворення сильних міжчастинкових контактів є ризик руйнування або деформації виробу. Захист від окислення здійснюється шляхом створення інертного або зменшення середовища в печі. Для просочення можна використовувати досить різноманітні метали і сплави, які задовольняють такі умови. Матеріал для просочення повинен характеризується повною відсутністю або невеликою міжфазною взаємодією, невеликим кутом мокротиння і має точку плавлення, що нижче бази. Наприклад, якщо компоненти взаємодіють один з одним, небажані процеси можуть виникати в процесі просочення, такі як утворення більш вогнетривких сполук або твердих розчинів, які можуть призвести до зупинки процесу просочення або несприятливо впливають на властивості і розміри продукту. Зазвичай бронза використовується для просочення металевої рами, при цьому усадка виробу становить 25%.
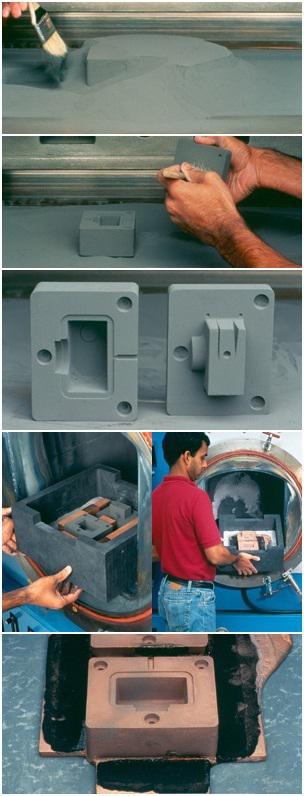
Одним з недоліків ILMS є відсутність здатності регулювати вміст фази вогнетривкості (основний матеріал) в широкому діапазоні. З моменту свого відсотка в готовому виробі визначається сипучою щільністю порошку, яка в залежності від характеристик порошку може бути три або більше разів менше теоретичної щільності порошкового матеріалу.
Матеріали та їх властивості, що використовуються для ILMS

Прямі лазерні замикання металів (DLMS)
Процес прямого лазерного замикання металів схожий на ILMS, але відрізняється тим, що замість полімеру використовуються сплави або сполуки з низькою точкою плавлення, і не існує такої технологічної операції як просочення. У самому серці створення концепції DMLS була німецька компанія EOS GmbH, яка в 1995 році створила комерційну інсталяцію для прямого лазерного зим замиканням системи бронзового порошку сталевого нікель. Отримання різних продуктів методом DLMS базується на потокі сформованого плавлення в порожнечі між частинками під дією капілярних сил. При цьому успішно виконувати процес, сполуки з фосфором додають в порошкову суміш, яка зменшує поверхневий натяг, в'язкість і ступінь окислення розплаву, тим самим покращуючи стійкість. Порошок, що використовується як зв'язок, як правило, менший за розмірами, ніж базовий порошок, оскільки він дозволяє збільшити об'ємну щільність суміші порошку і прискорити процес формування плавлення.
Матеріали та їх властивості, що використовуються для DLMS by EOS GmbH

Вибірковий лазерний плавлення (SLM)
Подальше вдосконалення добавних виробництв рослин пов'язане з можливістю використання більш потужного лазера, меншого фокусу, діаметра плями і більш тонкого шару порошку, що дозволило використовувати SLM для виготовлення виробів з різних металів і сплавів. Зазвичай вироби, отримані цим методом, мають пористість 0-3%.
Як у вищезазначених методах (ЛМС, ДМЛС), зносостійкості, поверхневого натягу і плавлення в'язкості грають важливу роль в процесі виробництва продукції. Однією з чинників, що протипоказають використання різних металів і сплавів для SLM, є ефект «утворення кулі» або сфероїдизация, що проявляється у вигляді падаючого окремо один від крапель, а не безперервного шляху розплаву. Причиною цього є поверхневий натяг під дією якого плавлення прагне зменшити вільної енергії поверхні шляхом формування форми з мінімальною площею поверхні, тобто м'ячем. В той же час ефект Марангоні спостерігається в розтопленій смузі, яка проявляється у вигляді конвекційних потоків через поверхневий напружений градієнт як функцію температури, і якщо конвекційні витрати досить сильні, розплавна смуга ділиться на окремі краплі. Крім того, краплі плавлення під впливом поверхневих натяжних пасток поблизу порошкових частинок в себе, що призводить до утворення плювати навколо краплі і, в кінцевому підсумку, для збільшення пористості.
191038 р.
Сфероїдизація сталевих М3/2 при субоптимальних режимах SLM
Вплив сфероїдизації також сприяє наявності кисню, що розчиняється в металі, збільшує в'язкість плавлення, що призводить до погіршення поширення і переносності розплаву нижче основного шару. З вищезазначених причин не можна отримати вироби з таких металів як олов, мідь, цинк, свинець.
Варто відзначити, що формування високоякісної розплавної смуги пов'язана з пошуком оптимальної площі параметрів процесу (основна радіаційна потужність і швидкість сканування), яка зазвичай досить вузька.
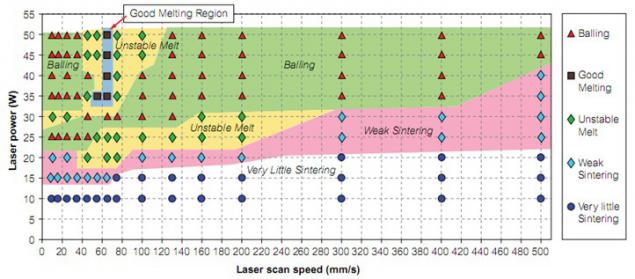
Вплив параметрів SLM золота на якість сформованих шарів
Ще одним фактором, що впливає на якість продукції, є поява внутрішніх напружень, наявність і величина яких залежить від геометрії продукту, швидкості опалення і охолодження, коефіцієнта теплового розширення, фази і структурних змін в металі. Значні внутрішні напруження можуть призвести до деформації продуктів, утворення мікро- та макро тріщин.
Частково зменшити негативний вплив вищевказаних факторів можна за допомогою нагрівальних елементів, які зазвичай розташовуються всередині установки навколо підкладки або живильника з порошком. Опалення порошку також дозволяє видалити адсорбовану вологу з поверхні частинок і тим самим зменшити ступінь окислення.
При вибірковому лазерному плавленні металів, таких як алюміній, мідь, золото не є невід'ємним питанням, є їх висока рефлекторність, що викликає необхідність використання потужної лазерної системи. Але збільшення потужності лазерного променя може негативно вплинути на точність розмірів виробу, так як при надмірному нагріві порошок буде плавати і зимувати зовні лазерного плями через теплообмін. Висока потужність лазера також може привести до зміни хімічного складу в результаті випаровування металу, яка особливо характерна для сплавів, що містять компоненти освітлення і має більш еластичність пар.
Механічні властивості матеріалів, отриманих методом SLM (EOS GmbH)
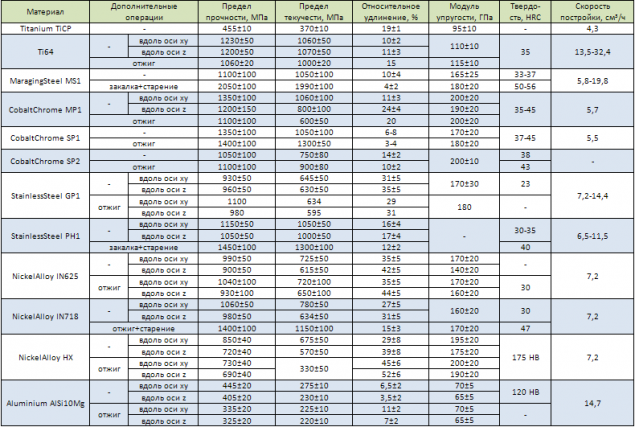
Якщо виріб, отриманий одним з вищевказаних методів, має залишкову пористість, то при необхідності використовуються додаткові технологічні операції для збільшення її щільності. Для цього використовуються методи порошкової металургії - sintering або гарячого ізостатичного пресування (HIP). Зима усуває залишкову пористість і збільшує фізико-механічні властивості матеріалу. Варто підкреслити, що сформовані властивості матеріалу в процесі зимівлі визначається складом і характером матеріалу, розміром і кількістю пори, наявністю дефектів і інших численних факторів. GIP - це процес, в якому заготовка, розміщена в газостаті, ущільнюється під дією високої температури та комплексної стиснення вхідного газу. Робочий тиск і максимальна температура, що досягається газостатом, залежить від його дизайну і обсягу. Наприклад, газостаття має розміри робочої камери 900×1800 мм, здатний розвивати температуру 1500 ° С і тиск 200 МПа. Використання GIP для усунення пористості без використання герметичної оболонки можливо, якщо пористість не більше 8%, так як з більшою вартістю газ через пори вводять продукт, тим самим запобігаючи ущільнюванню. Можна виключити проникнення в газовий продукт, зробивши сталеву герметичну оболонку, що повторює форму поверхні виробу. Однак, продукція, отримана при добавці, є переважно складною формою, яка не дозволяє виробляти таку оболонку. У цьому випадку можна використовувати вакуумну герметичну ємність для ущільнення, в якій продукт поміщається в розпушене середовище (Al2O3, BNhex, графіт), що передає тиск на стінах виробу.
Після добавки виробництва методом SLM, матеріали характеризуються анізотропією властивостей, підвищеною міцністю і зниженою протокою через наявність залишкових стресів. Для видалення залишкових навантажень, отримання більш збалансованої структури, збільшення в'язкості і пластичності матеріалу здійснюється загоєння.
За даними, можна відзначити, що вироби, отримані за допомогою селективного лазерного розплавлення, в деяких випадках посилюються на 2-12%. Це можна пояснити невеликими розмірами зернових і мікроструктурних компонентів, які утворюються в результаті швидкого охолодження плавлення. Швидкий гіпотермія плавлення значно збільшує кількість ембріонів твердих фаз і зменшує їх критичний розмір. У той же час кристали швидко ростуть на ембріонах, торкнувшись один до одного, починають запобігати їх подальшому росту, тим самим утворюючи дрібнозерну структуру. Проростки кристалізації, як правило, неметалічні включення, газові бульбашки або частинки, випущені з плавлення з їх обмеженим розчином в рідкому фазі. І в цілому, згідно з коефіцієнтом Хол-Петч, з зменшенням розміру зерна, міцність металу підвищується через розвинену мережу зернових меж, що є ефективним бар'єром для руху відтоків. Слід зазначити, що завдяки різному хімічному складу сплавів і їх властивостей, умовам ЛМ, вищевказаних явищ, які виникають при охолодженні плавлення, проявляються різними інтенсивністю.
Механічні властивості матеріалів, отриманих SLM і литтям
108352р.
Звичайно, це не означає, що продукти, отримані за допомогою селективного лазерного плавлення, краще, ніж продукти, отримані традиційними методами. Завдяки великій гнучкості традиційних методів отримання продукції, можна варіювати широко властивості виробу. Наприклад, за допомогою таких методів, як зміна температурних умов кристалізації, допінгу і введення модифікаторів в плавлення, термоциклування, порошкова металургія, термомеханічна обробка і т.д., можливе досягнення значного збільшення міцних властивостей металів і сплавів.
Особливий інтерес - використання вуглецевої сталі для виробництва добавок як дешевого та високомеханічного матеріалу. Відомо, що при збільшенні вуглецевого вмісту у сталі, її плинності та підвищенні працездатності. У зв'язку з цим можна отримати прості продукти, що містять 0,6-1% C з щільністю 94-99%, при цьому в разі чистого заліза щільність становить близько 83%. У процесі селективного лазерного розплавлення вуглецевої сталі, плавлення доріжки при швидкому охолодженні піддається загартуванню і випускати до структури трооститу або сорбітолу. У той же час через теплові напруження і структурні трансформації можуть виникати значні стреси в металі, що призводять до появи тріщин продукту або до утворення тріщин. Геометрія виробу також важлива, так як гострі перерізні переходи, невеликі радіуси округлення і гострі краї викликають утворення тріщин. Якщо після «друкування» сталі не має заздалегідь визначеного рівня механічних властивостей і її необхідно піддавати додатковому тепловому обробці, необхідно враховувати раніше зазначені обмеження на форму виробу, щоб уникнути появи загартування дефектів. Це зменшує перспективу використання SLM для вуглецевих сталей в певній мірі.
При отриманні виробів традиційними методами, одним з способів уникнути тріщин і лейшів при бронюванні виробів складної форми є використання сплавних сталей, в яких присутні сплавні елементи, крім збільшення механічних і фізико-хімічних властивостей, затримки трансформації аустеніту при охолодженні, в результаті чого критична швидкість гасіння знижується і збільшується затвердіння сплаву сталі. У зв'язку з низькою критичною швидкістю гасіння, сталь може бути виведена в маслі або в повітрі, що знижує рівень внутрішніх стресів. Однак, завдяки швидкому видаленню тепла, неможливості регулювання швидкості охолодження і наявності вуглецевої сталі в сплаві, ця техніка не уникає появи значних внутрішніх напружень при селективному лазерному плавленні.
У зв'язку з вищезазначеними особливостями, мартензитні сталі (MS 1, GP 1, PH 1) використовуються для SLM, при якому загартування і збільшення твердості досягається шляхом ізоляції диспергованих міжметалічних фаз при термообробці. У цих сталей міститься невелика кількість вуглецевих (поганих відсотках), в результаті чого утворюється мартенітна решітка при швидкому охолодженні характеризується невеликою ступенем спотворення і тому має низьку твердість. Невисока твердість і висока провітрність мартензиту забезпечує розслаблення внутрішніх напружень при загартуванні, а високий вміст сплаву елементів дозволяє сталевим калібрувати велику глибину практично на будь-якій швидкості охолодження. Завдяки цьому, за допомогою SLM, комплексні вироби можуть бути виготовлені та спекотні, оброблені без страху тріщин або бородавки. Крім мартензійно-знімних сталей, можна використовувати деякі аустенітні нержавіючі сталі, такі як 316L.
У висновку можна відзначити, що зараз зусилля вчених і інженерів спрямовані на більш детальне вивчення впливу параметрів процесу на структуру, механізм і особливості ущільнення різних матеріалів під дією лазерного випромінювання для поліпшення механічних властивостей і збільшення асортименту матеріалів, придатних для лазерного виробництва.
Джерело: habrahabr.ru/post/218271/