1749
How to collect the camera
Detailed photo story about how going to the legendary cameras.
Leica M8 early assembly stage. Many mechanical parts in place, but the viewfinder, lens and electronic components are missing.
Leica factory is located in the small town of Solms (Solms), in western Germany. Many employees working in the company for over 20 years. Stefan Daniels (Stefan Daniels), who currently heads the factory in Solms, one of them. He met with the Leica 15 years and received a technical degree thanks to the work in the company.
The technician inserts a CCD. CCD for Leica manufactured by Kodak. The surface is covered with a plurality of microlenses matrix, to alter the incoming light rays so that they are uniformly fall onto the sensor, one microlens opposite each pixel. Once inserted the CCD, workers assemble lightweight magnesium housing the camera. Body hides the upper and lower brass plate designed to protect the internal components.
Software is installed, and the camera can be operated at a basic level, allows the technician to carry out extensive testing on each individual cell. By the end of the test, Leica M8 will consist of 1,800 individual parts.
Workers are exposed every camera standard system checks: checking shutter rangefinder focusing system, as well as sensitivity and smooth operation of the CCD. At this stage, quality control, technology determines the accuracy of the camera's viewfinder. Each finder should be adjusted after installation, Leica and requires that the center of the image seen through the viewfinder is different from the real no more than 0 to 0001 millimeters.
The workplace is set to build analog cameras Leica. But as the M8 and M9 are almost identical composition of the items, they are going along with analog cameras. The entire process comprises 35, and takes about eight hours at the camera. Tiny particles of dust inside the camera can cause serious problems, so plant Leica create an access rule to the workplace. Employees are a low-static shoes to avoid attraction of dust. Dust-absorbing flooring is at the entrances to the assembly hall. All paper products on the conveyor, covered in plastic bags to, make sure that even small fibers that may escape from the pages will not be able to get into the room. And employees have to wear special hats.
Housing M7, ready for assembly at any time.
As said Christian Erhardt (Christian Erhardt), Deputy Director of Marketing - "The only reason our cameras so carefully made that almost every employee is a user of our products. It's in our blood. " By order Leica M7 camera can cover ostrich skin. Model "a la carte" allows the user to choose the cosmetic parts of the camera, such as color trim, buttons and leather case. Customers can also customize the size of the viewfinder and the location of its lines.
The technician makes minor adjustments to the rangefinder cameras to ensure its synchronous work with the lens. The main part of the Leica camera settings made with the participation of the human eye, rather than computers or sophisticated optical devices. Here, the technician checks and adjusts the manual focus mechanism, using the principle of inter-frame strip. In the M-series cameras do not have autofocus. Leica is very proud of this line of cameras.
In the photo inside view camera Leica S2. This large-format camera, is 37, 5-megapixel CCD (30x45 mm) by 56 per cent more than 24 x 36 mm on a 35 mm frame. Its price is 22000 $.
Haguenauer Ralph (Ralph Hagenauer), head of the Department for the dissemination of the company's products Leica, considering the range of cameras in the lobby of the central office.
They may look like giant cough lozenges, but the raw glass washers for grinding and polishing the lens elements for Leica 21mm f / 1.4. The company buys glass from major manufacturers around the world, depending on the optical purity, availability and prices.
A significant part of the production equipment at the plant Solms made to order, according to the specifications of Leica, and often uses its own processes, which the company keeps a secret.
Glass washer during grinding, which eventually will become part of the lens Leica 21mm f / 1.4
Working watching polishing lenses, while the lens-manufacturing process.
Leica lenses are polished with a tolerance of about 1/2, 000 millimeters, about a thousand times thinner than a human hair.
The glasses of pre-grinding and polishing. Next, the inspector will determine which of them are suitable for further processing.
Computer displays a graphical representation of light passing through the lens. He checks the light transmission from all sides and determines whether the lens surface more polished.
Each lens 43 has to coatings, depending on the model of the lens. Glass is placed in an oven where the coating material is applied in aerosol form, and then a strong liking for the glass layers by using the patented process. Each layer is designed to improve image quality and produces a color correction, distortion and other inaccuracies.
"Each lens, each piece of glass is unique, we just have to make sure that the end result is always of high quality," - says Ehrhardt.
Finished lenses designed for the lens Leica Noctilux-M 50mm f / 0.95 ASPH. The company claims that this is the most high-aperture aspherical lens in the world. Priced at $ 11,000 for the lens, this tray is worth more than 100.000 $
In one of the final stages of quality control technician projects the image of a homogeneous sample through the lens onto the wall. Then he makes a visual inspection to make sure that the image is quite sharp.
Tray finished lens Summilux Leica M-21mm F / 1.4.
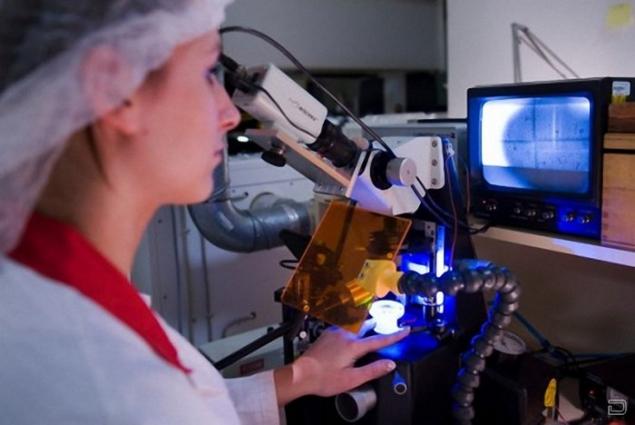
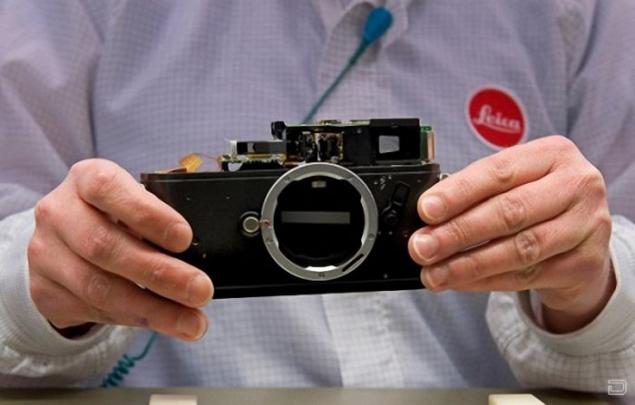
Leica M8 early assembly stage. Many mechanical parts in place, but the viewfinder, lens and electronic components are missing.
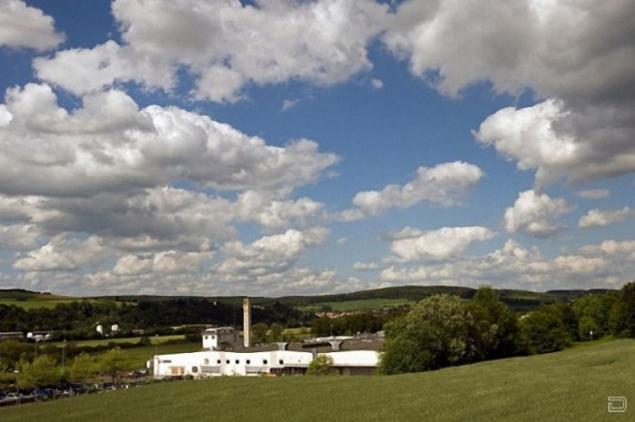
Leica factory is located in the small town of Solms (Solms), in western Germany. Many employees working in the company for over 20 years. Stefan Daniels (Stefan Daniels), who currently heads the factory in Solms, one of them. He met with the Leica 15 years and received a technical degree thanks to the work in the company.
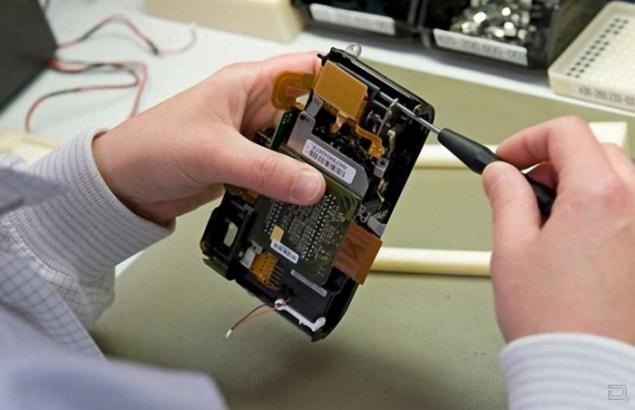
The technician inserts a CCD. CCD for Leica manufactured by Kodak. The surface is covered with a plurality of microlenses matrix, to alter the incoming light rays so that they are uniformly fall onto the sensor, one microlens opposite each pixel. Once inserted the CCD, workers assemble lightweight magnesium housing the camera. Body hides the upper and lower brass plate designed to protect the internal components.
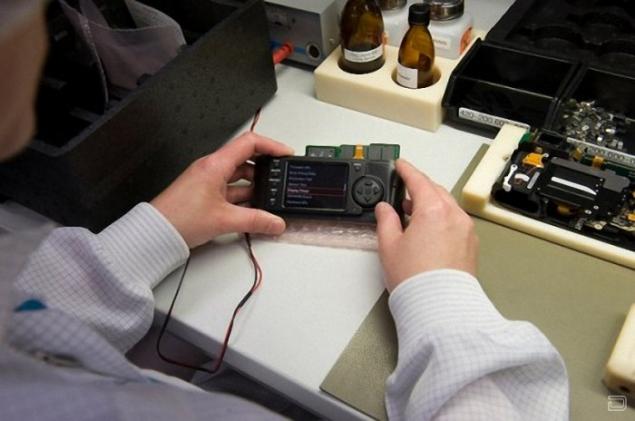
Software is installed, and the camera can be operated at a basic level, allows the technician to carry out extensive testing on each individual cell. By the end of the test, Leica M8 will consist of 1,800 individual parts.
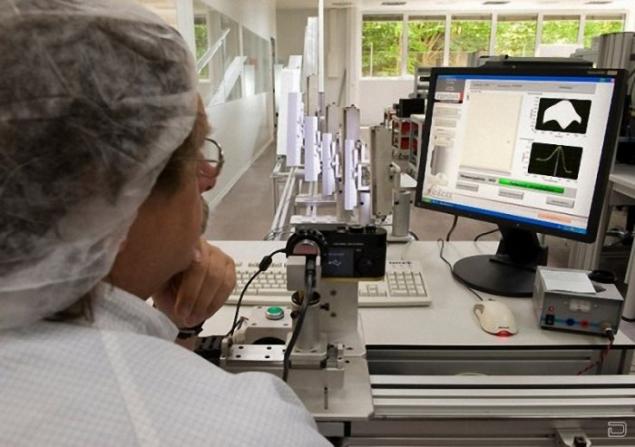
Workers are exposed every camera standard system checks: checking shutter rangefinder focusing system, as well as sensitivity and smooth operation of the CCD. At this stage, quality control, technology determines the accuracy of the camera's viewfinder. Each finder should be adjusted after installation, Leica and requires that the center of the image seen through the viewfinder is different from the real no more than 0 to 0001 millimeters.
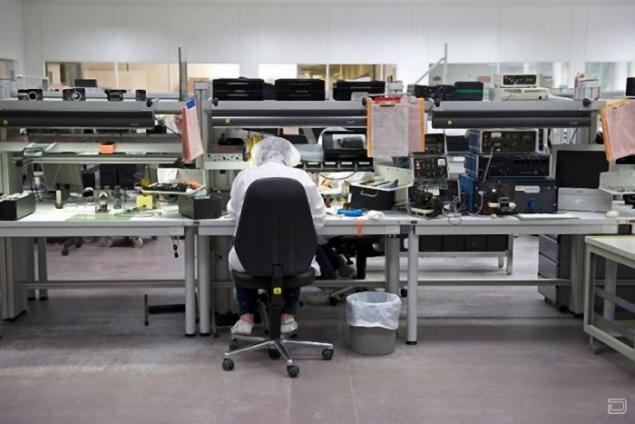
The workplace is set to build analog cameras Leica. But as the M8 and M9 are almost identical composition of the items, they are going along with analog cameras. The entire process comprises 35, and takes about eight hours at the camera. Tiny particles of dust inside the camera can cause serious problems, so plant Leica create an access rule to the workplace. Employees are a low-static shoes to avoid attraction of dust. Dust-absorbing flooring is at the entrances to the assembly hall. All paper products on the conveyor, covered in plastic bags to, make sure that even small fibers that may escape from the pages will not be able to get into the room. And employees have to wear special hats.
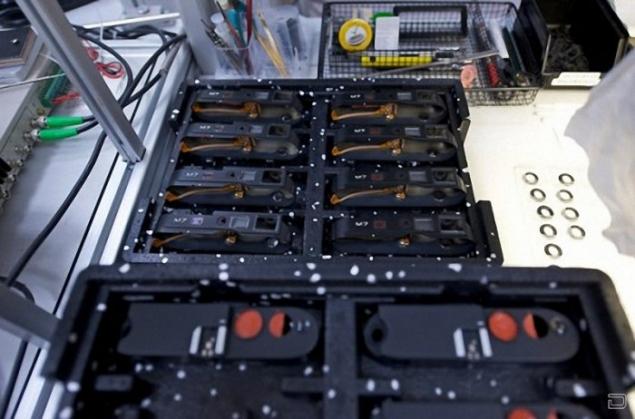
Housing M7, ready for assembly at any time.
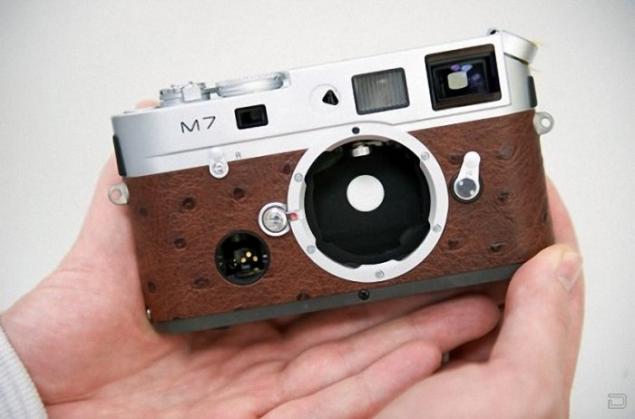
As said Christian Erhardt (Christian Erhardt), Deputy Director of Marketing - "The only reason our cameras so carefully made that almost every employee is a user of our products. It's in our blood. " By order Leica M7 camera can cover ostrich skin. Model "a la carte" allows the user to choose the cosmetic parts of the camera, such as color trim, buttons and leather case. Customers can also customize the size of the viewfinder and the location of its lines.
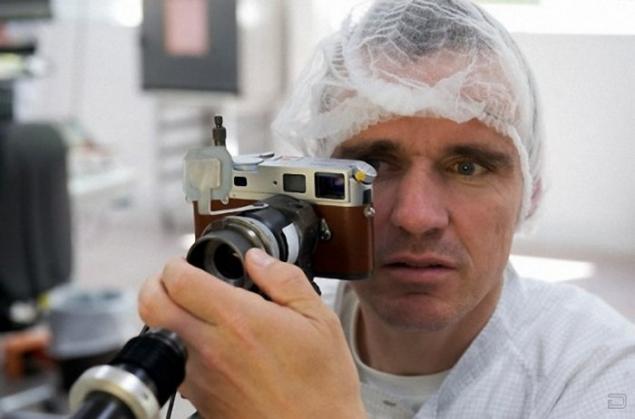
The technician makes minor adjustments to the rangefinder cameras to ensure its synchronous work with the lens. The main part of the Leica camera settings made with the participation of the human eye, rather than computers or sophisticated optical devices. Here, the technician checks and adjusts the manual focus mechanism, using the principle of inter-frame strip. In the M-series cameras do not have autofocus. Leica is very proud of this line of cameras.
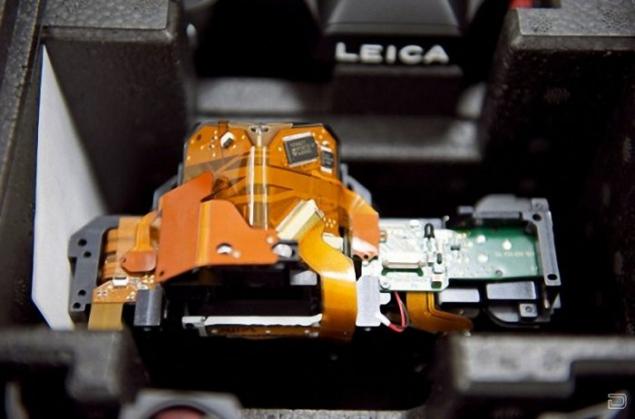
In the photo inside view camera Leica S2. This large-format camera, is 37, 5-megapixel CCD (30x45 mm) by 56 per cent more than 24 x 36 mm on a 35 mm frame. Its price is 22000 $.
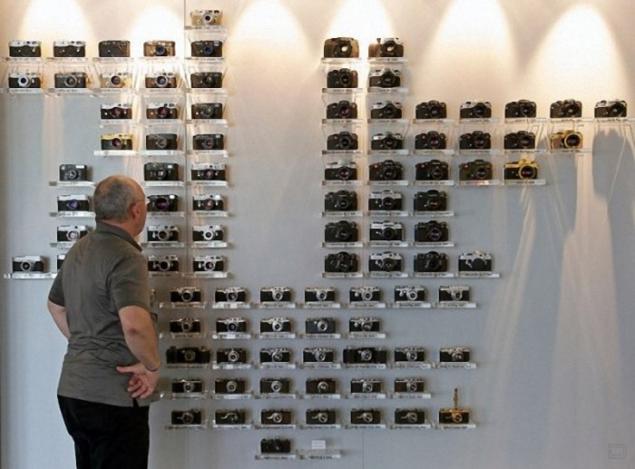
Haguenauer Ralph (Ralph Hagenauer), head of the Department for the dissemination of the company's products Leica, considering the range of cameras in the lobby of the central office.
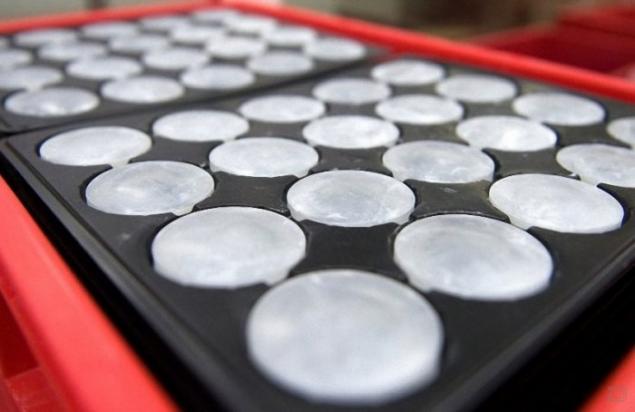
They may look like giant cough lozenges, but the raw glass washers for grinding and polishing the lens elements for Leica 21mm f / 1.4. The company buys glass from major manufacturers around the world, depending on the optical purity, availability and prices.
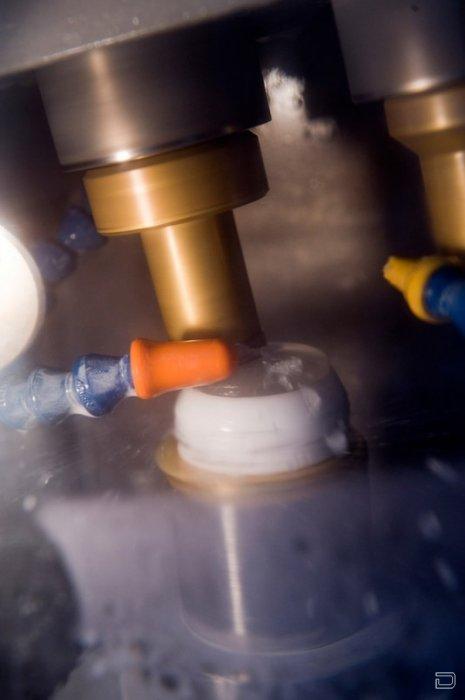
A significant part of the production equipment at the plant Solms made to order, according to the specifications of Leica, and often uses its own processes, which the company keeps a secret.
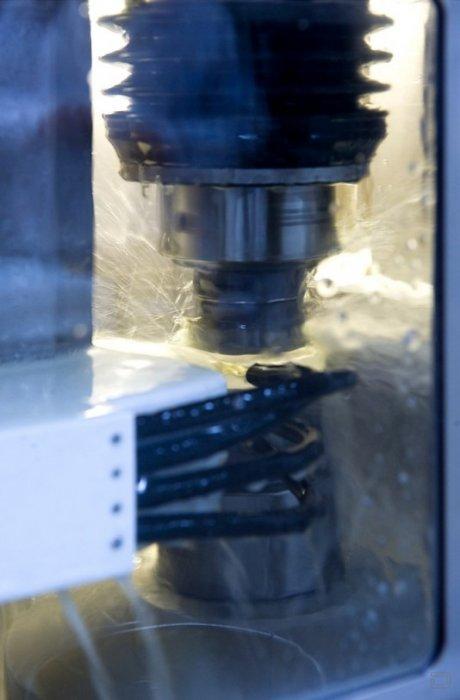
Glass washer during grinding, which eventually will become part of the lens Leica 21mm f / 1.4
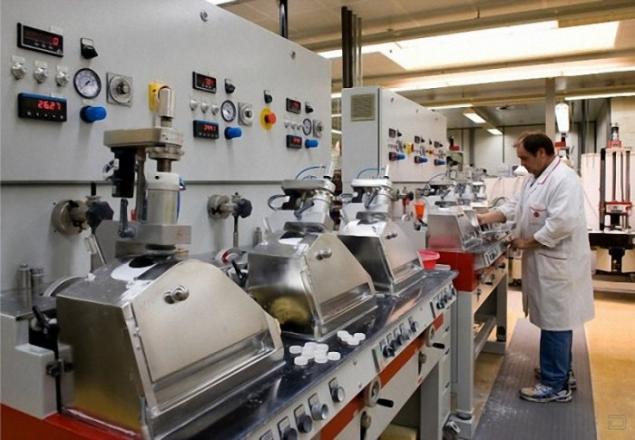
Working watching polishing lenses, while the lens-manufacturing process.
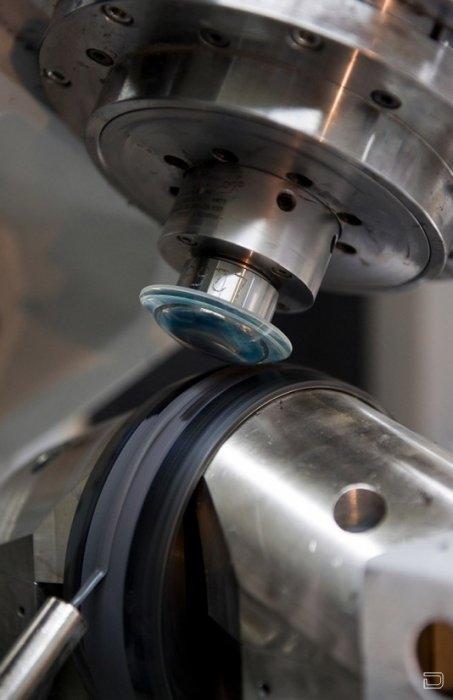
Leica lenses are polished with a tolerance of about 1/2, 000 millimeters, about a thousand times thinner than a human hair.
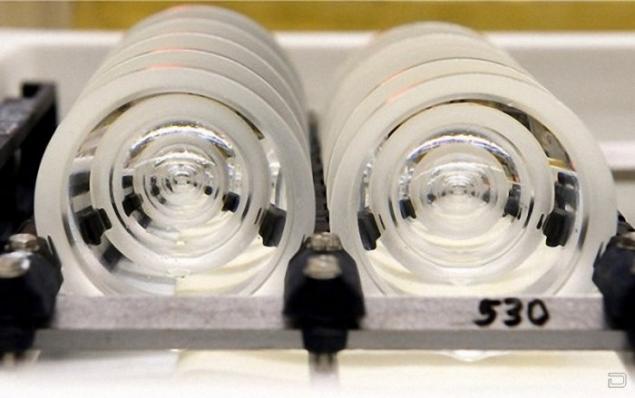
The glasses of pre-grinding and polishing. Next, the inspector will determine which of them are suitable for further processing.
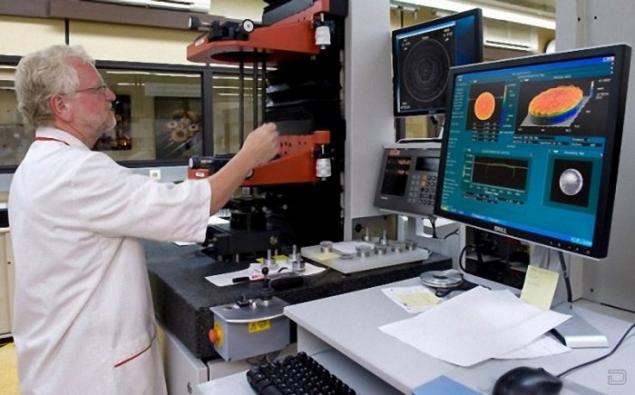
Computer displays a graphical representation of light passing through the lens. He checks the light transmission from all sides and determines whether the lens surface more polished.
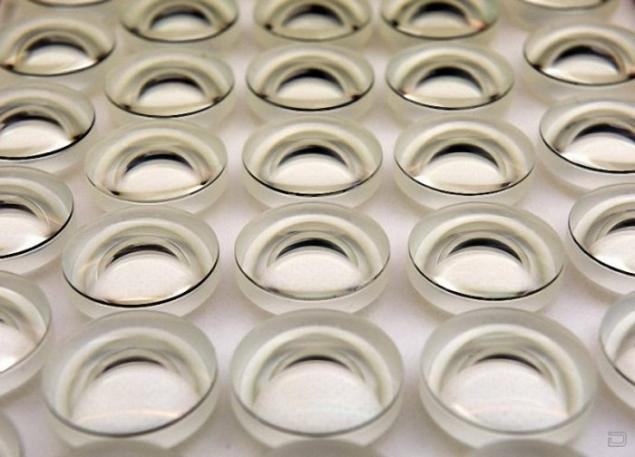
Each lens 43 has to coatings, depending on the model of the lens. Glass is placed in an oven where the coating material is applied in aerosol form, and then a strong liking for the glass layers by using the patented process. Each layer is designed to improve image quality and produces a color correction, distortion and other inaccuracies.
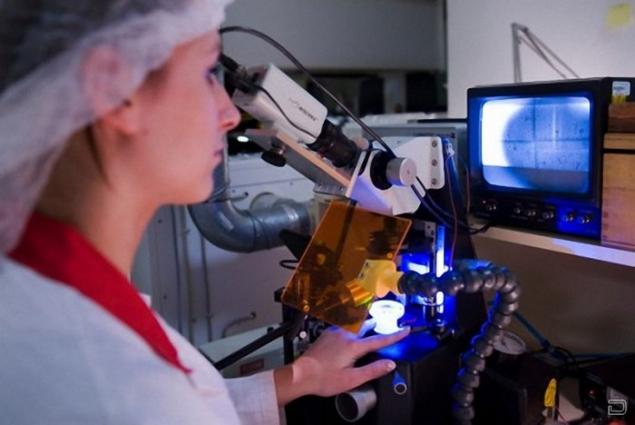
"Each lens, each piece of glass is unique, we just have to make sure that the end result is always of high quality," - says Ehrhardt.
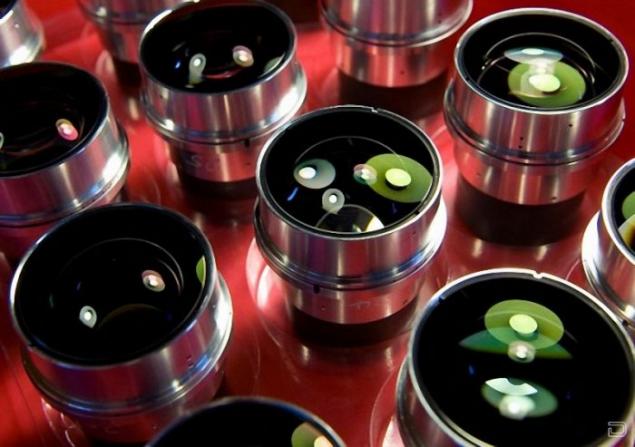
Finished lenses designed for the lens Leica Noctilux-M 50mm f / 0.95 ASPH. The company claims that this is the most high-aperture aspherical lens in the world. Priced at $ 11,000 for the lens, this tray is worth more than 100.000 $
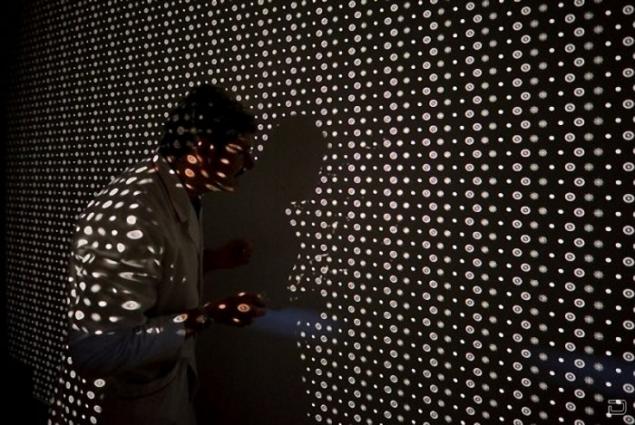
In one of the final stages of quality control technician projects the image of a homogeneous sample through the lens onto the wall. Then he makes a visual inspection to make sure that the image is quite sharp.
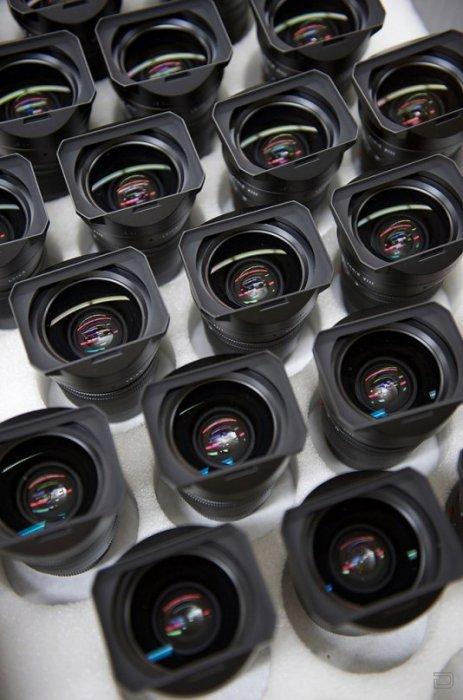
Tray finished lens Summilux Leica M-21mm F / 1.4.