1548
Tutaevsky bells
There is something fascinating in kolokolah.Ved they are not just tools for creating special sound quality and exceptional purity. Bells also a means to communicate with God and men. They seem to draw his attention to the events taking place in the church. After the bell ringing is solemn and mournful, he can report the good news or just enjoy hearing music that creates a bell-ringer.
But not only. Each bell, in itself, is also a work of art.
In a small town in the north Tutaev Yaroslavl region has a bell factory. He is best known, perhaps, for the whole world. Tutaevsky bells ringing in churches throughout Russia, Ukraine and Kazakhstan.
No, bell, of course, "begins" wrong. First, the necessary calculations, it is necessary to calculate on paper, what will be the new bell, then cut patterns that will determine its shape. And only then begins a long process, during which the axle (pin) layer upon layer of clay is pushed. And even clay here feature - its taken out of a certain career in the Yaroslavl region. But do not ask what: it's a secret Tutaevsky masters.
Owner and soul of the plant is Nikolai Shuvalov. Actually, it is called: Nicholas Bell plant Shuvalov. And who better than he can tell us about the bells and during their manufacture ?!
On the blank layer by layer superimposed clay, and its quality is improving gradually: it is becoming thinner and thinner, until finally, on the spindle is not quite "comfortable" bell. But clay and not copper. And it is still the inner surface of the bell. Then on the rod is put another curve, according to which "cut" the external profile of the future bell. Layer after layer of lies clay, but of a different quality. And on the next picture can be seen in the bell varying degrees of readiness.
And here you can see patterns, elated over the clay bell piece. Leka moves around the form, making more than a hundred rounds a day.
And when the form is ready, it imposed decorations. It is also very hard work: first jewelry made from clay and then cast in special forms, of which there is a new cast - this time in wax. And on clay bell superimposed wax letters and images. It turns out that something like this:
When the external shape of the bell is ready, carefully lifting the upper casing, and beneath it is a replica of the future bell. But clay. It is removed and destroyed.
And now, after more than two months of work comes the moment of casting. Casting itself lasts a little more than ten minutes. Well, for the great bell, probably about twenty. Then the metal cools, and that he had almost finished the bell!
To it is necessary to attach the language. One of these here. And maybe one of these.
And yet, the bell is ready.
It is possible to call. And Vladimir Degtyarev, artist and ringer, making it an elegant craftsmanship.
Each bell has its own "voice" - and the purer the sound, the more valuable bell. On some bells are seen chalk - it notes that she sings them.
And if you look at the small bell in the center of the picture, we can see what it says. To its credit, the president must be said that this bell is quite modest in size.
But not only. Each bell, in itself, is also a work of art.
In a small town in the north Tutaev Yaroslavl region has a bell factory. He is best known, perhaps, for the whole world. Tutaevsky bells ringing in churches throughout Russia, Ukraine and Kazakhstan.
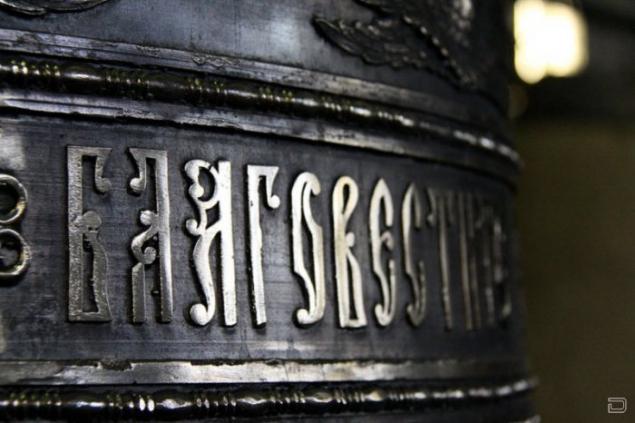
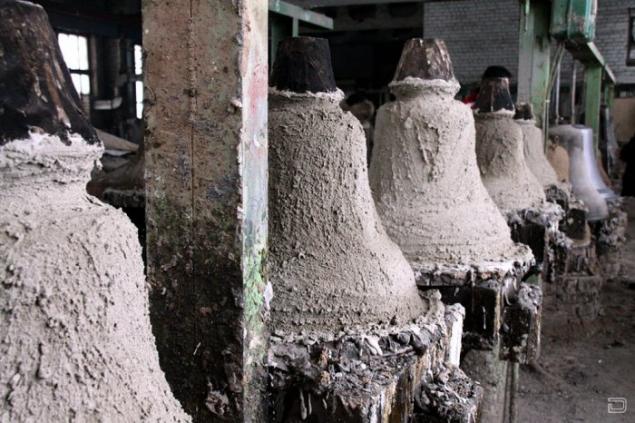
No, bell, of course, "begins" wrong. First, the necessary calculations, it is necessary to calculate on paper, what will be the new bell, then cut patterns that will determine its shape. And only then begins a long process, during which the axle (pin) layer upon layer of clay is pushed. And even clay here feature - its taken out of a certain career in the Yaroslavl region. But do not ask what: it's a secret Tutaevsky masters.
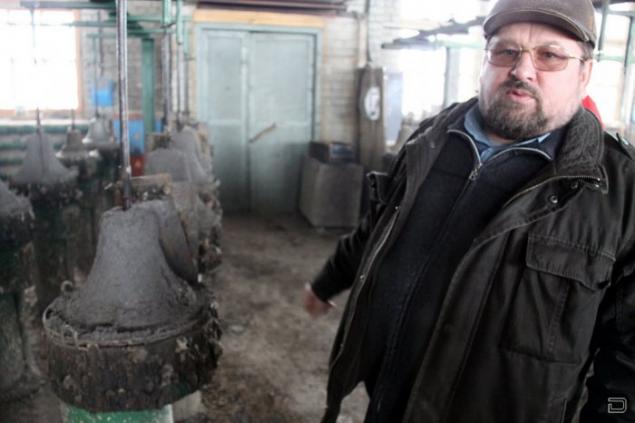
Owner and soul of the plant is Nikolai Shuvalov. Actually, it is called: Nicholas Bell plant Shuvalov. And who better than he can tell us about the bells and during their manufacture ?!
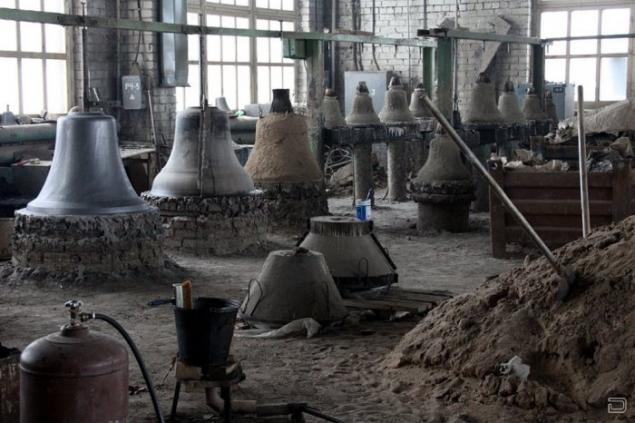
On the blank layer by layer superimposed clay, and its quality is improving gradually: it is becoming thinner and thinner, until finally, on the spindle is not quite "comfortable" bell. But clay and not copper. And it is still the inner surface of the bell. Then on the rod is put another curve, according to which "cut" the external profile of the future bell. Layer after layer of lies clay, but of a different quality. And on the next picture can be seen in the bell varying degrees of readiness.
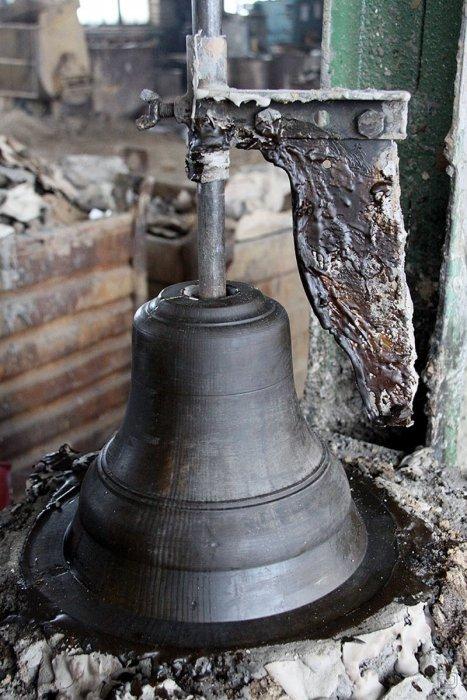
And here you can see patterns, elated over the clay bell piece. Leka moves around the form, making more than a hundred rounds a day.
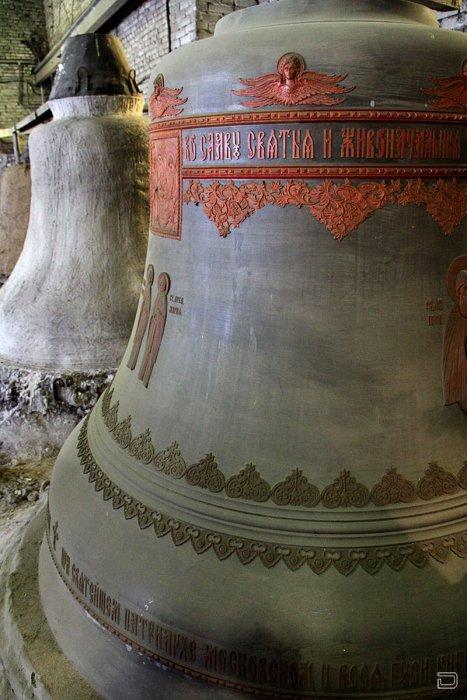
And when the form is ready, it imposed decorations. It is also very hard work: first jewelry made from clay and then cast in special forms, of which there is a new cast - this time in wax. And on clay bell superimposed wax letters and images. It turns out that something like this:
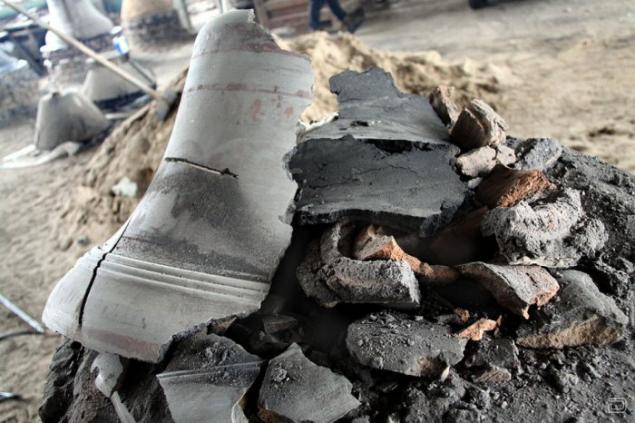
When the external shape of the bell is ready, carefully lifting the upper casing, and beneath it is a replica of the future bell. But clay. It is removed and destroyed.
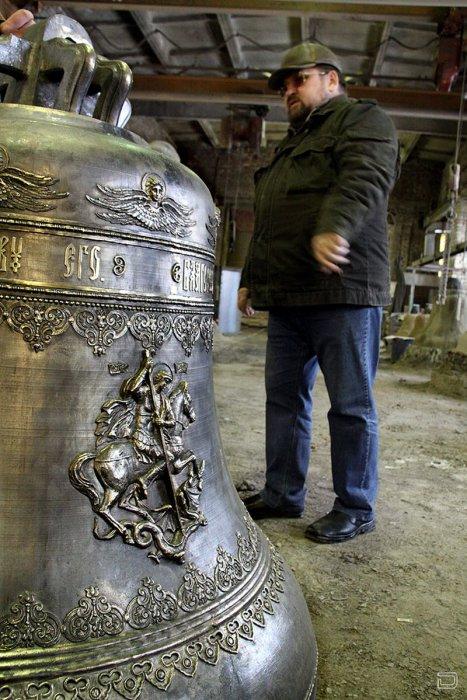
And now, after more than two months of work comes the moment of casting. Casting itself lasts a little more than ten minutes. Well, for the great bell, probably about twenty. Then the metal cools, and that he had almost finished the bell!
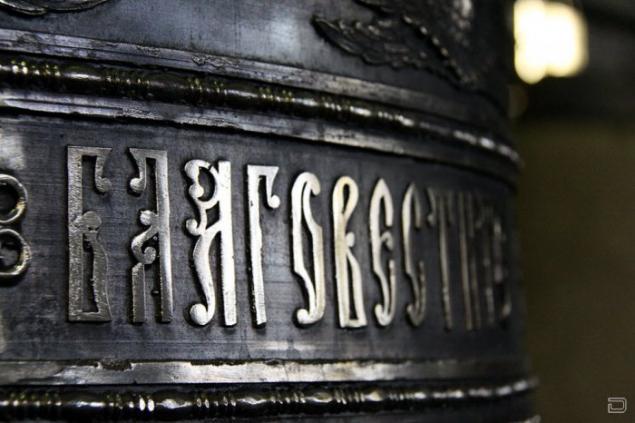
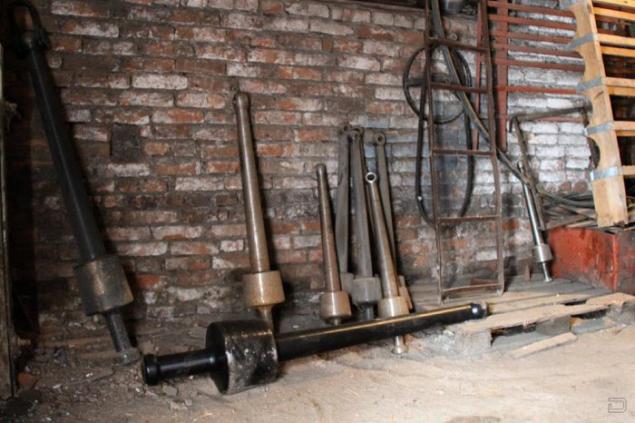
To it is necessary to attach the language. One of these here. And maybe one of these.
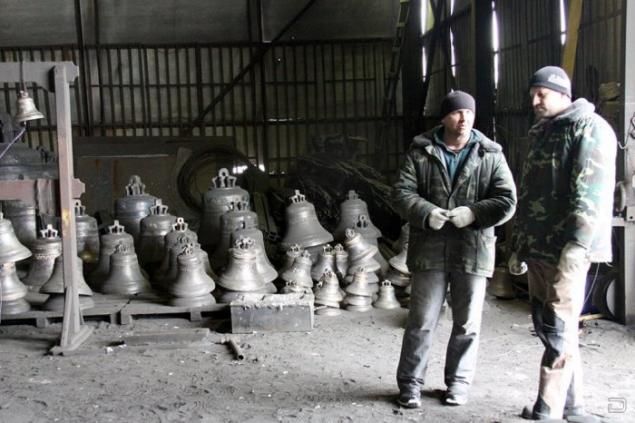
And yet, the bell is ready.
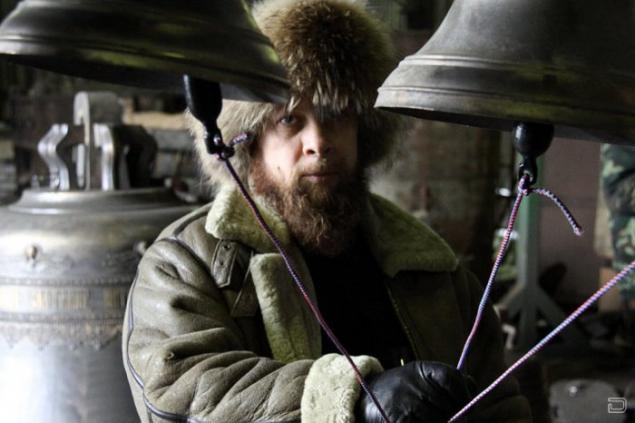
It is possible to call. And Vladimir Degtyarev, artist and ringer, making it an elegant craftsmanship.
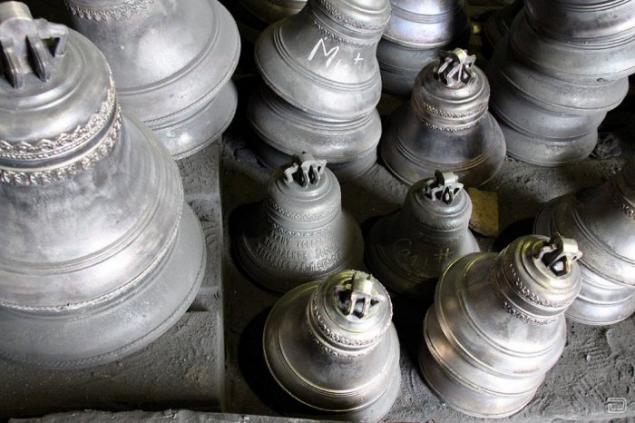
Each bell has its own "voice" - and the purer the sound, the more valuable bell. On some bells are seen chalk - it notes that she sings them.
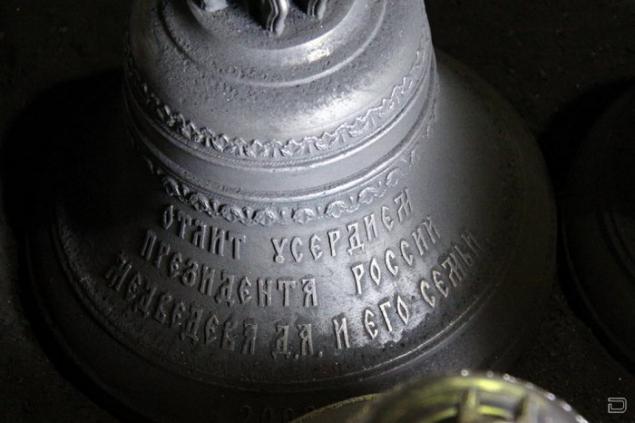
And if you look at the small bell in the center of the picture, we can see what it says. To its credit, the president must be said that this bell is quite modest in size.