667
Backup solid fuel products: composites based on biomass, peat and biochar
Presents the achievements of the past 20-years anniversary for the establishment of solid fuel products from renewable raw materials, waste, forestry-, wood-, torturerack and APK. Receptorsare composites with high calorific value, hydrophobic and quite resistant to biodegradation opens the possibility of their application for environmentally friendly combustion technologies in small power boilers, lime kilns, industrial production. These fuel products suitable for long storage as a backup fuel.
The problem of creation of composites based on biomass, peat, waste, forestry and wood processing, pulp and paper industries, municipal solid waste and biochar relevant in scientific and practical terms. In scientific terms, the urgency relates to the need of theoretical foundations of receptorsare solid products based on renewable raw materials, peat and other with predetermined properties. In practical terms, the relevance is determined by the calls for improving waste management.
In achieving the goal of reducing CO2 emissions, the key role is full or partial replacement of coal fuel based on renewable raw materials. At the moment the use of coal-fired power stations instead of coal and in boiler equipment of distributed energy of the mixture of wood and solid fuel products bio-coal or bio-coal composite briquettes and pellets instead of fuel oil is low-cost and realistic way to reduce greenhouse gas emissions. In addition, it is possible to use composite instead of standard fuels (natural gas and coal) as part of resource saving and energy saving additives in industry: in cement kilns, and glass and steel plants. We stand on the threshold of rapid development of bio-coal market. According to forecasts of the consulting and engineering company Poyry in 2020 the production of biochar will be 7.5 million tons. This increase in the production of biochar is associated with two expanding niches in the market its application: as a component of the fuel products and to enhance soil fertility.
In recent decades, product lines on the basis of renewable raw materials has been manifested an increased interest in connection with the concept of sustainable development policies, and in connection with the increased significance of environmental issues. The result is a market potential of this environmentally friendly product line is rapidly growing by 10-20 % per year. It is correlated with improvement of technological capacity of priority agropolymer and biomass, which accounts for the fact that biodegradable polymers have become the subject of numerous scientific fields, not only in science, but also in marketing. Many experts make efforts to explore properties, especially thermal, "green" polymers and expand their practical application.
However, Biodegradability refers to the number of characteristics of the fuel products based on renewable raw materials that you need — and we are committed to this — to overcome using various techniques and preparations composite of biofuels, introducing in their composition, for example, biochar and solid hydrophobic plasticizer-binder. Thus, the article attempts to expand the practical applications of lignocellulosic polymers based on renewable raw materials, including in the form of biofuels, mainly based on monographs, patents and articles by the author [1-5].
The development of chemistry and technology of production of environmentally friendly polymers (green polymers) are also important in scientific and practical terms is the key to sustainable development that can maintain our comfortable life. Russia, as you know, is not only rich in hydrocarbon raw material resources, but also bio-energy resources: cultural arable lands comprise 9% of total world reserves annual lignocellulosic materials, as the forests store 25% of world reserves of wood (perennial lignocellulosic materials). While fossil fuels dominate the fuel balance of transport, production of heat and electrical energy.
Application on coal-fired power plants instead of coal and in boiler equipment of distributed energy of the mixture of wood and solid fuel products bio-coal or bio-coal composite briquettes and pellets instead of fuel oil is low-cost and realistic way to reduce greenhouse gas emissions
The energy development strategy of Russia until 2020 (approved by Government Resolution of the Russian Federation of 28.08.2003 №1234-PP), which indicated the need for greater use of peat and different types of waste, including municipal solid waste and wood residues production/agriculture, production of heat and power implies increasing the share of renewable energy in total energy consumption to 7% after 2020. Technical potential of biomass in Russia is 53 million tons of coal equivalent. The scheme of circulation of polysaccharides, saccharides and in the nature shown in Fig. 1.
Now supermolecular structure of "green" polymers began to be studied at the nanoscale, since it became possible to observe individual molecules and molecular clusters under athanasiadou microscopy (AFM). ASM directly visualize the heterogeneity of both biopolymers in crystalline or amorphous state. In addition, morphological observations can be correlated with the results obtained by other physical measurements. AFM was used to observe supermolecular structure of cellulose and lignin, using their water soluble derivatives such as sodium carboxymethyl cellulose (the NaCMC) and lignosulfonate sodium (Ials). Samples deposited on mica were examined by AFM.
The images of ASM No. CMC clearly observed hard thread. The thickness of the strands arranged in mono - or double layers, is about 0.7 nm. It is believed that the hydrophobic part of the molecule is attached to the surface of mica, and carboxymethyl group distributed on the outer surface. The width of the filaments ranges from 15.2 to 18.2 m nm. The results obtained by x-ray diffractometry showed that four to five molecules were linked together and observed as a filament [6].
Lignins produced from renewable resources such as trees, plants and crops. About 30 % of the components of wood is lignin. Lignins are non-toxic and very versatile in the physical-chemical and operational characteristics. Most industrial lignins obtained in the pulping processes of Kraft and sulfite pulp. Ligniny Kraft usually burned as fuel for pulp mills, the Annual production capacity of lignin in Japan is estimated to be around 8 million tons. In addition, the lignin obtained in the hydrolysis process in ethanol production. The production of lignin in the world is about 30 million tons per year. However, it should be noted that this value is only estimated, as no reliable statistical data because it is often burned directly after production. About a million tons of water-soluble derivatives of lignosulfonates, which are byproducts of cooking sulphite cellulose, is used in Japan as chemicals, such as dispersants.
Industrial lignin is a byproduct of the cellulose industry, as mentioned above, and is separated mainly from wood during chemical pulping process. As described above, the core technology of delignification processes used in the pulping Kraft sulfite methods. Other technologies of delignification is the process of solvolysis using organic solvents or steam high pressure to remove lignin from plants.
Normally lignins are natural polymers with arbitrary mesh structure, their physical and chemical properties differ depending on the extraction processes. The highest structure of lignin, which consists of elements of phenylpropane, amorphous. Three phenylpropanoid monomer, such as coniferious alcohol, snapily alcohol and coumarinyl alcohol, connected and create a three-dimensional network in the process of radical-based lignin biosynthesis. For the above reason, the lignin has a regular structure (like cellulose) is a physically and chemically heterogeneous material, the chemical structure of which is not precisely known.
Since each molecule of lignin has more than two hydroxyl groups, based on polyurethane lignin derivatives, derivatives of polycaprolactone and epoxy resin can be obtained by using hydroxyl groups.
Cellulose, the structural formula of which is described in [1, 2], is a linear polysaccharide built from parts С6Н10О5. Chain containing up to 10 thousand glucosidic links, strapped in bundles by hydrogen bonds. Twisted beams form the so-called fibrils, which, through hemicellulosic and ligninase components as if "glued" to each other into a single rigid structure. Hemicellulose is a branched polysaccharide constructed largely from parts С5Н8О4 shorter than cellulose chains.
Renewable energy sources based on lignocellulosic raw materials can provide a wide range of energy services for a long time: a reliable supply of heat, electricity, and energy for transport without emissions of greenhouse gases and impact on climate (in accordance with the Kyoto Protocol). Russia's ratification of the UN Convention on climate change 1994 (Kyoto Protocol) and the Paris agreement of 2016 make clear that the need to seek and apply new strategies and technological solutions to reduce carbon dioxide emissions. What's more, was adopted by the UN Strategy of energy development until 2030, which envisages the expansion of the use of renewable energy sources to increase their share in energy consumption of up to 7 °%. According to some estimates, a partial transition from fossil fuels to biomass in Russia will allow to save from 10 to 20 million tons of fossil hydrocarbons and coal per year. Also decrease the emission of carbon dioxide into the atmosphere. The use of biomass may create additional investment incentives for the regions, as well as new jobs.
Currently in Russia there are two main directions of energy production from biomass: use of waste wood production and wood processing for the production of heat and electricity, production of fuel pellets (the main part of them is exported) and briquettes for the domestic market; production of liquid biofuels for transport biodiesel and bioethanol (Fig. 2).
Biodegradation, that is the biodegradation of biomass and composites, pellets and briquettes based on it in the environment may be due to different factors and processes: oxidation, hydrolysis, mechanochemical decay, photo - and biodegradation
Having large reserves of plant raw materials, waste which can be used as fuel, Russian companies were not able to implement them in the domestic market and in Europe market because of a number of difficulties due to peculiarities of biomass is their low bulk density (80-250 kg/m3), high humidity, and Biodegradability.
Biodegradation (biodegradation) of biomass and composites, pellets and briquettes based on it in the environment may be due to different factors and processes: oxidation, hydrolysis, mechanochemical decay, photo - and biodegradation. A tendency or, conversely, resistance to the processes of biodegradation is determined on the basis of a set of field and laboratory tests, which includes, in accordance with the standard testing materials ASTM measurement of physical-mechanical parameters and chemical composition of degradation products in a result of aerobic and anaerobic degradation of the polymer in different environments. These difficulties apply to the safety of solid fuel products during their storage, transport, as well as reduced burning, etc.
A partial solution to this problem became possible due to the increase in bulk weight and density, thermal effect of combustion by pelletization, i.e. the production of fuel pellets. Despite the fact that the development of the industry of production of fuel pellets and optimistic forecasts, the production of energy from biomass faces a number of obstacles that hinder its widespread (in Russia and in the countries of the European Union). As noted in "the technology development of biomass-based" Commission of the European communities, currently produced from biomass 4 % from the total amount of energy required, and by 2020 this figure will increase to 20 %. In the energy balance of the Russian Federation will continue to dominate fossil fuel. It should also be noted that Russia is in third place in the list of States with maximum CO2 emissions after the United States and people's Republic of China.
Renewable raw materials for solid biofuels is a pulp and ligninase mixture composed of annual and perennial agricultural plants, wood (chips, chunks, shavings, sawdust, powder), pulp and paper industries, as well as of animal origin in pelletierine or brittoniana — this is the kind of raw materials for industrial production. Biomass is not only solid fuel for stoves, fireplaces and boilers Autonomous dwellings, power plants of low and medium power, but also liquid or gaseous fuel for transport.
In recent years in Western Europe, North America and Japan, sharply increasing the production of granulated biofuel. Biogranules in contrast to the original biomass have a relatively high bulk density (600-700 kg/m3), low humidity content (below 10 %), relatively high calorific value (average of 18 MJ/kg).
The author developed and patented formulation of fuel pellets, briquettes and technologies for their production (as based on the reproduced materials, e.g., sawdust and other waste wood, woodworking, pulp and paper mill wastes, agro-industrial complex, or any carbon-containing compounds of coal, peat, waste, oil products), patented in 2016, the compositions for the production of solid propellant products which have advantages in relation to traditional due to new additives [3, 4] and can be used to create a backup of biofuels because of their hydrophobicity, durability and resistant to biodegradation.
In recent years in Western Europe, North America and Japan, sharply increasing the production of granulated biofuel. Biogranules in contrast to the original biomass have a relatively high bulk density, low humidity, relatively high calorific value (average 20 MJ/kg)
Thermal properties of the aforementioned components of the raw materials and fuel composites can be characterized by different types of physical and chemical research, including thermogravimetry (TG), differential thermal analysis (DTA), differential scanning calorimetry (DSC), thermomechanical (TMA), dynamic mechanical analysis (DMA), and calorimetry combustion. At the same time we were combining thermal methods with different measurements, including spectral methods, such as TG — Fourier transform infrared spectrometry (FTIR), and TG-DTA. Molecular structure of cellulose and lignin, the researchers paid particular attention over the last 100 years, as both biopolymer are major components of plant materials. Lately there are more structure-sensitive methods, and crystal structure of cellulose was investigated using x-ray diffractometry and spectrometry solid state nuclear magnetic resonance (NMR). On the other hand, the physical structure of lignin in the amorphous state is almost not studied.
Continues prototype testing of new formulations and methods of production of fuel pellets. Together with our partners that have the equipment for production of pellets and briquettes, it is planned to continue works to improve formulations and conducting testing of new formulations and methods of production of fuel pellets.
The advantages and novelty of the patent for the invention (the year 2016 [4]) and the clean technology compared to traditional fuel products described below:
1. Renewable raw materials, coal and peat is the main material of biofuel (solid products) and composites. It is a kind of industrial fuel. Solid plasticizer in the composition of the composite fuel product — binder, in contrast to the liquid binder, the type of adhesives as well as hot water and its vapour (which is traditionally used for plasticization by steaming), provides improvement of all operational parameters of briquettes/pellets and the reduction of Biodegradability:
3. Increase the efficiency of the briquetted/platinovogo fuel up to 80-90 % compared to coal and firewood. The possibility of transformation of the energy produced, for example, of heat into electricity. To heat the housing and industrial premises briquettes/ pellets are cheaper than electric energy.
4. The versatility of the fuel products from the biochar and the use of boilers domestic and industrial purposes, in power plants and thermal power stations or, for example, as a sorbent. That is, the ability to use both on the fuel market, and market products for soil improvement.
5. Demand on the European market and exported goods.
6. Fuel products, unlike the original biomass, have a relatively high bulk density (600-700 kg/m3), low humidity content (below 10 %), relatively high calorific value (average of 16-18 MJ/ kg, reaching 30 MJ/kg in accordance with the invention Patent of the Russian Federation, 2016).
7. Autonomy — in conjunction with low fire hazard and convenient storage, and transportation (as the briquettes/ pellets have a high value of the bulk mass). Can automatically feed-download the boiler and the automation of the process of obtaining thermal energy.
Insights
Thus, one of the most important achievements of scientific-technical progress in the research of new energy systems (for the partial replacement of fossil coal and gas) for the last 20 years has been the study, creation and introduction of technologies of production of composite solid fuel product, the fuel has a high calorific value and a combination of these properties, such as hydrophobicity and resistance to biodegradation, which contribute to its long-term storage and use as a backup fuel, and the use of multipurpose appointment including as part of the construction of the composites and to increase the fertility of the soil in the fertilizer composition. published
Source: www.c-o-k.ru/articles/rezervnye-tverdotoplivnye-izdeliya-kompozity-na-osnove-biomassy-torfa-i-biouglya
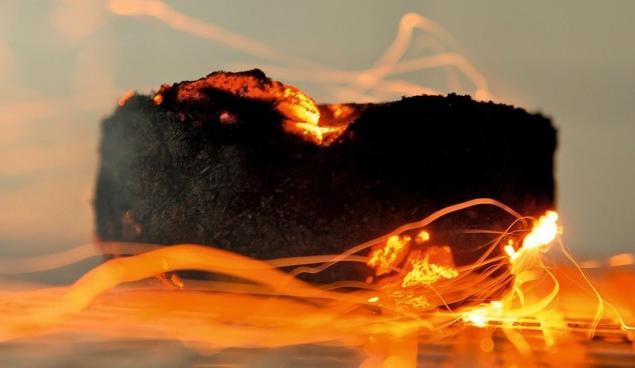
The problem of creation of composites based on biomass, peat, waste, forestry and wood processing, pulp and paper industries, municipal solid waste and biochar relevant in scientific and practical terms. In scientific terms, the urgency relates to the need of theoretical foundations of receptorsare solid products based on renewable raw materials, peat and other with predetermined properties. In practical terms, the relevance is determined by the calls for improving waste management.
In achieving the goal of reducing CO2 emissions, the key role is full or partial replacement of coal fuel based on renewable raw materials. At the moment the use of coal-fired power stations instead of coal and in boiler equipment of distributed energy of the mixture of wood and solid fuel products bio-coal or bio-coal composite briquettes and pellets instead of fuel oil is low-cost and realistic way to reduce greenhouse gas emissions. In addition, it is possible to use composite instead of standard fuels (natural gas and coal) as part of resource saving and energy saving additives in industry: in cement kilns, and glass and steel plants. We stand on the threshold of rapid development of bio-coal market. According to forecasts of the consulting and engineering company Poyry in 2020 the production of biochar will be 7.5 million tons. This increase in the production of biochar is associated with two expanding niches in the market its application: as a component of the fuel products and to enhance soil fertility.
In recent decades, product lines on the basis of renewable raw materials has been manifested an increased interest in connection with the concept of sustainable development policies, and in connection with the increased significance of environmental issues. The result is a market potential of this environmentally friendly product line is rapidly growing by 10-20 % per year. It is correlated with improvement of technological capacity of priority agropolymer and biomass, which accounts for the fact that biodegradable polymers have become the subject of numerous scientific fields, not only in science, but also in marketing. Many experts make efforts to explore properties, especially thermal, "green" polymers and expand their practical application.
However, Biodegradability refers to the number of characteristics of the fuel products based on renewable raw materials that you need — and we are committed to this — to overcome using various techniques and preparations composite of biofuels, introducing in their composition, for example, biochar and solid hydrophobic plasticizer-binder. Thus, the article attempts to expand the practical applications of lignocellulosic polymers based on renewable raw materials, including in the form of biofuels, mainly based on monographs, patents and articles by the author [1-5].
The development of chemistry and technology of production of environmentally friendly polymers (green polymers) are also important in scientific and practical terms is the key to sustainable development that can maintain our comfortable life. Russia, as you know, is not only rich in hydrocarbon raw material resources, but also bio-energy resources: cultural arable lands comprise 9% of total world reserves annual lignocellulosic materials, as the forests store 25% of world reserves of wood (perennial lignocellulosic materials). While fossil fuels dominate the fuel balance of transport, production of heat and electrical energy.
Application on coal-fired power plants instead of coal and in boiler equipment of distributed energy of the mixture of wood and solid fuel products bio-coal or bio-coal composite briquettes and pellets instead of fuel oil is low-cost and realistic way to reduce greenhouse gas emissions
The energy development strategy of Russia until 2020 (approved by Government Resolution of the Russian Federation of 28.08.2003 №1234-PP), which indicated the need for greater use of peat and different types of waste, including municipal solid waste and wood residues production/agriculture, production of heat and power implies increasing the share of renewable energy in total energy consumption to 7% after 2020. Technical potential of biomass in Russia is 53 million tons of coal equivalent. The scheme of circulation of polysaccharides, saccharides and in the nature shown in Fig. 1.
Now supermolecular structure of "green" polymers began to be studied at the nanoscale, since it became possible to observe individual molecules and molecular clusters under athanasiadou microscopy (AFM). ASM directly visualize the heterogeneity of both biopolymers in crystalline or amorphous state. In addition, morphological observations can be correlated with the results obtained by other physical measurements. AFM was used to observe supermolecular structure of cellulose and lignin, using their water soluble derivatives such as sodium carboxymethyl cellulose (the NaCMC) and lignosulfonate sodium (Ials). Samples deposited on mica were examined by AFM.
The images of ASM No. CMC clearly observed hard thread. The thickness of the strands arranged in mono - or double layers, is about 0.7 nm. It is believed that the hydrophobic part of the molecule is attached to the surface of mica, and carboxymethyl group distributed on the outer surface. The width of the filaments ranges from 15.2 to 18.2 m nm. The results obtained by x-ray diffractometry showed that four to five molecules were linked together and observed as a filament [6].
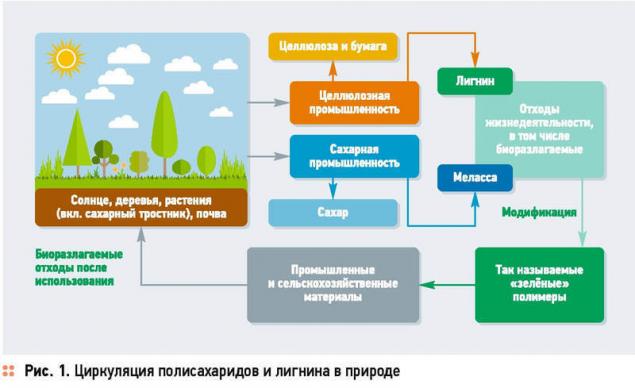
Lignins produced from renewable resources such as trees, plants and crops. About 30 % of the components of wood is lignin. Lignins are non-toxic and very versatile in the physical-chemical and operational characteristics. Most industrial lignins obtained in the pulping processes of Kraft and sulfite pulp. Ligniny Kraft usually burned as fuel for pulp mills, the Annual production capacity of lignin in Japan is estimated to be around 8 million tons. In addition, the lignin obtained in the hydrolysis process in ethanol production. The production of lignin in the world is about 30 million tons per year. However, it should be noted that this value is only estimated, as no reliable statistical data because it is often burned directly after production. About a million tons of water-soluble derivatives of lignosulfonates, which are byproducts of cooking sulphite cellulose, is used in Japan as chemicals, such as dispersants.
Industrial lignin is a byproduct of the cellulose industry, as mentioned above, and is separated mainly from wood during chemical pulping process. As described above, the core technology of delignification processes used in the pulping Kraft sulfite methods. Other technologies of delignification is the process of solvolysis using organic solvents or steam high pressure to remove lignin from plants.
Normally lignins are natural polymers with arbitrary mesh structure, their physical and chemical properties differ depending on the extraction processes. The highest structure of lignin, which consists of elements of phenylpropane, amorphous. Three phenylpropanoid monomer, such as coniferious alcohol, snapily alcohol and coumarinyl alcohol, connected and create a three-dimensional network in the process of radical-based lignin biosynthesis. For the above reason, the lignin has a regular structure (like cellulose) is a physically and chemically heterogeneous material, the chemical structure of which is not precisely known.
Since each molecule of lignin has more than two hydroxyl groups, based on polyurethane lignin derivatives, derivatives of polycaprolactone and epoxy resin can be obtained by using hydroxyl groups.
Cellulose, the structural formula of which is described in [1, 2], is a linear polysaccharide built from parts С6Н10О5. Chain containing up to 10 thousand glucosidic links, strapped in bundles by hydrogen bonds. Twisted beams form the so-called fibrils, which, through hemicellulosic and ligninase components as if "glued" to each other into a single rigid structure. Hemicellulose is a branched polysaccharide constructed largely from parts С5Н8О4 shorter than cellulose chains.
Renewable energy sources based on lignocellulosic raw materials can provide a wide range of energy services for a long time: a reliable supply of heat, electricity, and energy for transport without emissions of greenhouse gases and impact on climate (in accordance with the Kyoto Protocol). Russia's ratification of the UN Convention on climate change 1994 (Kyoto Protocol) and the Paris agreement of 2016 make clear that the need to seek and apply new strategies and technological solutions to reduce carbon dioxide emissions. What's more, was adopted by the UN Strategy of energy development until 2030, which envisages the expansion of the use of renewable energy sources to increase their share in energy consumption of up to 7 °%. According to some estimates, a partial transition from fossil fuels to biomass in Russia will allow to save from 10 to 20 million tons of fossil hydrocarbons and coal per year. Also decrease the emission of carbon dioxide into the atmosphere. The use of biomass may create additional investment incentives for the regions, as well as new jobs.
Currently in Russia there are two main directions of energy production from biomass: use of waste wood production and wood processing for the production of heat and electricity, production of fuel pellets (the main part of them is exported) and briquettes for the domestic market; production of liquid biofuels for transport biodiesel and bioethanol (Fig. 2).
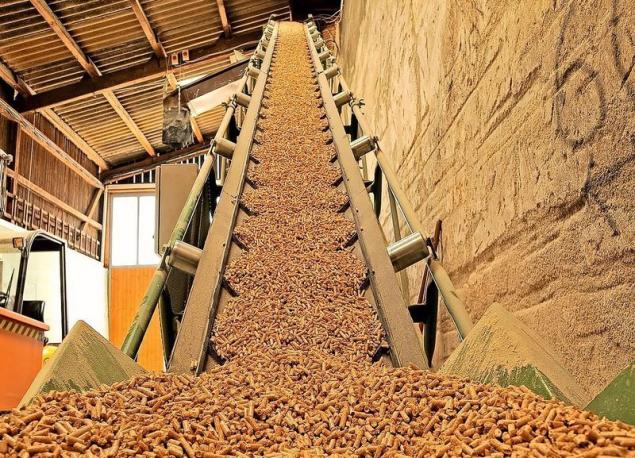
Biodegradation, that is the biodegradation of biomass and composites, pellets and briquettes based on it in the environment may be due to different factors and processes: oxidation, hydrolysis, mechanochemical decay, photo - and biodegradation
Having large reserves of plant raw materials, waste which can be used as fuel, Russian companies were not able to implement them in the domestic market and in Europe market because of a number of difficulties due to peculiarities of biomass is their low bulk density (80-250 kg/m3), high humidity, and Biodegradability.
Biodegradation (biodegradation) of biomass and composites, pellets and briquettes based on it in the environment may be due to different factors and processes: oxidation, hydrolysis, mechanochemical decay, photo - and biodegradation. A tendency or, conversely, resistance to the processes of biodegradation is determined on the basis of a set of field and laboratory tests, which includes, in accordance with the standard testing materials ASTM measurement of physical-mechanical parameters and chemical composition of degradation products in a result of aerobic and anaerobic degradation of the polymer in different environments. These difficulties apply to the safety of solid fuel products during their storage, transport, as well as reduced burning, etc.
A partial solution to this problem became possible due to the increase in bulk weight and density, thermal effect of combustion by pelletization, i.e. the production of fuel pellets. Despite the fact that the development of the industry of production of fuel pellets and optimistic forecasts, the production of energy from biomass faces a number of obstacles that hinder its widespread (in Russia and in the countries of the European Union). As noted in "the technology development of biomass-based" Commission of the European communities, currently produced from biomass 4 % from the total amount of energy required, and by 2020 this figure will increase to 20 %. In the energy balance of the Russian Federation will continue to dominate fossil fuel. It should also be noted that Russia is in third place in the list of States with maximum CO2 emissions after the United States and people's Republic of China.
Renewable raw materials for solid biofuels is a pulp and ligninase mixture composed of annual and perennial agricultural plants, wood (chips, chunks, shavings, sawdust, powder), pulp and paper industries, as well as of animal origin in pelletierine or brittoniana — this is the kind of raw materials for industrial production. Biomass is not only solid fuel for stoves, fireplaces and boilers Autonomous dwellings, power plants of low and medium power, but also liquid or gaseous fuel for transport.
In recent years in Western Europe, North America and Japan, sharply increasing the production of granulated biofuel. Biogranules in contrast to the original biomass have a relatively high bulk density (600-700 kg/m3), low humidity content (below 10 %), relatively high calorific value (average of 18 MJ/kg).
The author developed and patented formulation of fuel pellets, briquettes and technologies for their production (as based on the reproduced materials, e.g., sawdust and other waste wood, woodworking, pulp and paper mill wastes, agro-industrial complex, or any carbon-containing compounds of coal, peat, waste, oil products), patented in 2016, the compositions for the production of solid propellant products which have advantages in relation to traditional due to new additives [3, 4] and can be used to create a backup of biofuels because of their hydrophobicity, durability and resistant to biodegradation.
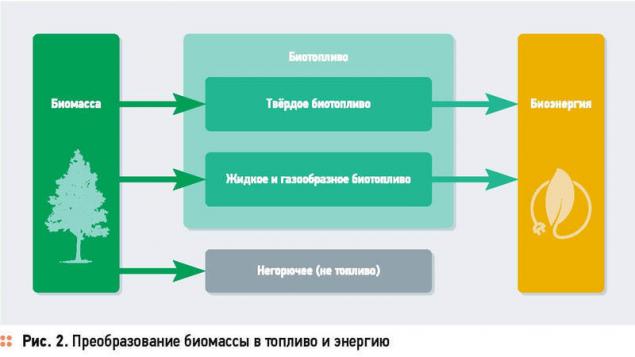
In recent years in Western Europe, North America and Japan, sharply increasing the production of granulated biofuel. Biogranules in contrast to the original biomass have a relatively high bulk density, low humidity, relatively high calorific value (average 20 MJ/kg)
Thermal properties of the aforementioned components of the raw materials and fuel composites can be characterized by different types of physical and chemical research, including thermogravimetry (TG), differential thermal analysis (DTA), differential scanning calorimetry (DSC), thermomechanical (TMA), dynamic mechanical analysis (DMA), and calorimetry combustion. At the same time we were combining thermal methods with different measurements, including spectral methods, such as TG — Fourier transform infrared spectrometry (FTIR), and TG-DTA. Molecular structure of cellulose and lignin, the researchers paid particular attention over the last 100 years, as both biopolymer are major components of plant materials. Lately there are more structure-sensitive methods, and crystal structure of cellulose was investigated using x-ray diffractometry and spectrometry solid state nuclear magnetic resonance (NMR). On the other hand, the physical structure of lignin in the amorphous state is almost not studied.
Continues prototype testing of new formulations and methods of production of fuel pellets. Together with our partners that have the equipment for production of pellets and briquettes, it is planned to continue works to improve formulations and conducting testing of new formulations and methods of production of fuel pellets.
The advantages and novelty of the patent for the invention (the year 2016 [4]) and the clean technology compared to traditional fuel products described below:
1. Renewable raw materials, coal and peat is the main material of biofuel (solid products) and composites. It is a kind of industrial fuel. Solid plasticizer in the composition of the composite fuel product — binder, in contrast to the liquid binder, the type of adhesives as well as hot water and its vapour (which is traditionally used for plasticization by steaming), provides improvement of all operational parameters of briquettes/pellets and the reduction of Biodegradability:
- increases the values of strength (and reduces crochemore);
- improves surface gloss and, in some formulations increases the white;
- promotes increase of density values up to 1.2 g/cm3 or more;
- increases the duration of combustion (burning without smoke, exactly);
- increases the calorific value (heat of combustion effect within 16-18-30 MJ/kg);
- lowers energy consumption due to lower pressure during the pressing and "drying effect" in relation to the moisture content of the feedstock.
3. Increase the efficiency of the briquetted/platinovogo fuel up to 80-90 % compared to coal and firewood. The possibility of transformation of the energy produced, for example, of heat into electricity. To heat the housing and industrial premises briquettes/ pellets are cheaper than electric energy.
4. The versatility of the fuel products from the biochar and the use of boilers domestic and industrial purposes, in power plants and thermal power stations or, for example, as a sorbent. That is, the ability to use both on the fuel market, and market products for soil improvement.
5. Demand on the European market and exported goods.
6. Fuel products, unlike the original biomass, have a relatively high bulk density (600-700 kg/m3), low humidity content (below 10 %), relatively high calorific value (average of 16-18 MJ/ kg, reaching 30 MJ/kg in accordance with the invention Patent of the Russian Federation, 2016).
7. Autonomy — in conjunction with low fire hazard and convenient storage, and transportation (as the briquettes/ pellets have a high value of the bulk mass). Can automatically feed-download the boiler and the automation of the process of obtaining thermal energy.
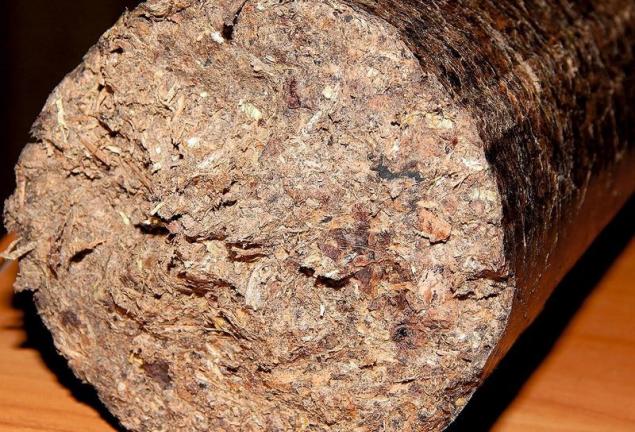
Insights
Thus, one of the most important achievements of scientific-technical progress in the research of new energy systems (for the partial replacement of fossil coal and gas) for the last 20 years has been the study, creation and introduction of technologies of production of composite solid fuel product, the fuel has a high calorific value and a combination of these properties, such as hydrophobicity and resistance to biodegradation, which contribute to its long-term storage and use as a backup fuel, and the use of multipurpose appointment including as part of the construction of the composites and to increase the fertility of the soil in the fertilizer composition. published
Source: www.c-o-k.ru/articles/rezervnye-tverdotoplivnye-izdeliya-kompozity-na-osnove-biomassy-torfa-i-biouglya
Gödel's incompleteness theorem in 20 minutes
Self-organized particles will improve the efficiency of perovskite LEDs