2428
How to build a house in the southern United States?
Let's start talking about the technology of building homes in Houston, about where it all begins, as the area is ennobled as homes are built and what materials are used at the same time.
Thus, the construction begins with the master plan for the area. The area is not only home to the district also includes an irrigation system, drainage, treatment facilities, roads, infrastructure for leisure (tracks for walking, jogging and cycling, outdoor swimming pool, tennis courts, soccer fields, basketball, children's playgrounds site and just open parks with artificial lakes with fountains and water channels, and a large fenced area for dogs). The whole area is in turn divided into districts, about 90 - 150 houses (district plan we will see later). Infrastructure created separately for several districts, the people are not "crowd." The whole area will be in the already constructed system of shops, banks, hospitals and other public facilities that were built in advance in view of the ongoing construction of the area and increase the population.
Construction begins with a blank field in which laid all communications, gas pipes, plumbing, electrical cables, telephone. At first, everything is connected to the substation. Tractor for trenching (in the previous pictures - pipe layer).
Then, from the substation all communications are routed to shield houses. All electrical hiding in a box that will be located in a corner of the backyard of the house. Red tube is not hot water, it is fed by the cold water and hot water in the house will not be supplied because Each house will be is a gas or electric boiler. Green tube with a cap - a gas line, and later it will be hidden, as long as it sticks out like a marker.
After all utilities laid, preparing irrigation systems, in her Houston pay special attention, because Houston is subject to tropical storms and hurricanes. Typically, the depth of artificial reservoirs is about 10-12 meters. All pools have a system of locks and canals to divert water.
Beach concreted artificial pond at pond to protect and prevent erosion. To prevent water washed away the concrete part of the land near concrete reinforcing tape mud and rubble. Most recently it has been heavy rain, and water pumps pumping water from canals.
Then the construction of roads and sewerage. The roads provide quick and easy access of construction machinery, and also does not allow carry dirt from construction sites. Near all sewage stacked sandbags, their purpose - to hold the mud when it rains and to prevent clogging of sewers. Sewer pipes - plastic tube diameter of 60 cm from the start, increasing with the length of sewage. Begin laying pipe at a depth of 1.5 meters, respectively, as the depth increases with the length of the system. Pipes are laid at an angle of 0.18%. Sewer grates, there is usually no, instead of them - open water inlet, which is located inside the sewer pit, measuring approximately 2x2 meters. Incidentally, I note that all the pipes, if possible, are not under the road, and next to it, even though all repairs carried out of the mines.
Then, set all the road signs. Marking the roadway in residential areas is not because the speed limit here - 20 km / h. Speed limit signs, too, are not available, the rate registered in the SDA. Earlier, I asked about the height of the curb - it is 15 cm. The thickness of the concrete screed on the road - 21 cm.
It is very interesting to drive on such areas with all the characters apart, but the complete lack of homes. Pay attention to the tape grass, laid along the border, it prevents leaching of dirt from the lawn to the street in the rain.
Rashn designer datekted.
All surfaces, which can be scratched, damaged, soiled or in construction - closed.
In Russia still can not do the hatches on the road. Oh no no no.
Then prepare the site for homes. At the same time construction of 20-30 houses. They are built mainly around, it is easier to clean debris, and does not disturb those who are already living in populated and built houses. Exceptions are homes that have been purchased in advance for some specific areas. To lay the foundation excavate depth of one meter and is filled with a layer of gravel, sand and clay, all compacted, and then it turns out that's at the top of this cap. Note that this trick is possible only in Texas because of the very clayey ground. For example, in the north of the United States placed a deep strip foundation.
Then the supply of communications to the home (gas, cold water, sewer, electric cable, etc..)
It is going formwork for the foundation. All solid foundations, solid, clay soil allows their relatively thin screed thickness of about 25-30 cm, with the "pillars" of 1.5 meters.
Typically, the average size of the foundation - 20 to 15 meters.
Then the ground is covered with a thick dense plastic, fit fittings with diameters from 10 mm to 16 mm. It fits every 3-4 meters, "criss-cross", except in certain places, such as the garage door of the house, cut the foundation, here it fits a little differently, depending on the design of the house.
Reinforcement before casting will be stretched, seven days after the filling load is lifted slowly
Pouring the foundation is non-stop to complete the work. Permissible concrete strength of 60 to 90 MPa.
: Fresh screed. Sticking plate - a duralumin anchors (anchor) for walls.
Periodically, the concrete is poured water, preventing the formation of these cracks in it.
Crib.
Then filled screed applied marking walls and begins assembling wooden frame houses.
All the supporting structures are assembled at home from a tree commonly used board 15x5, 20x7 cm.
Then sheathed with plywood boards 2 cm thick.
It should be noted that all wood materials for the construction of houses pre-defined mixes and processed oils to protect against insects and water. At the same time, these chemical compounds are not harmful to human health.
All material is secured with nails and metal anchors. Also used screws, bolt ties, mainly in the critical "nodes." Bruce is almost never used, it is replaced with a few boards nailed together.
Once the frame is completed at home, inside start to conduct communication. Future in the kitchen sink. Sewer use plastic pipes with a diameter of 6 cm.
Also inside the house begins to "grow into" the various elements, such as a bar.
Held communication within the walls.
Held electrician.
Black wire - Television, yellow - electric, white - the Internet.
In the attic ventilation system is installed for heating and cooling the house. In fact - it is soft fiberglass pipe. On top of it has a shell of fire-retardant fiberglass, which is hidden under the glass wool, which is located inside the soft aluminum tube. Today, these ventilation pipes are used where the air flow rate does not exceed 30 m / s. At a higher speed air circulation using tougher ventilation system.
Output room.
Water unit. For water used plastic pipes with a diameter of 13 mm, can withstand the pressure of 0.7 MPa and a temperature of 95 C.
Bathroom and toilet.
Then set fireplace. These homes all have gas fireplaces, they are much easier to install because they do not require masonry and problems with the valves. In some houses commissioned by the buyer build real fireplaces.
By the way, nice gas fireplace warms the house. Although, of course, with a real fire can not be compared.
Then sheathe plywood wall on one side, on the other hand openings in the glass wool is inserted, after which the wall is sutured and plywood. Then the plywood sheathed with plasterboard. Note that insulation in the house is very good, in spite of this, the apparent fragility of the walls, and the cries of the children's zombies are not heard in the hall, as well as operating a loud TV in the bedroom. Thanks to high-quality glass wool.
Then drywall puttied.
Future jacuzzi. Gather different designs inside the house.
Shower.
Garage.
Then insert the window. The outer part of the house is sheathed with additional noise insulation and insulated polystyrene panels (blue on the left), with the value of R is 3, the thickness of the panels - 13mm. Top panels are sewn plastic and a layer of thick roofing material (black on the right).
Windows, used in construction, "southern", and can be used only in Texas, Louisiana, Florida, Southern California, Arizona and New Mexico. The windows have a U-value of 2, the coefficient of heat - 0.23, light transmission - 0.43.
Finally, the time comes to masonry.
Decorative brick, standard ASTM - SW. In addition to brick and stone used.
Between the wall and the masonry is left 5-6 inch gap for air circulation.
Accordingly, under the peak of left vent.
Fans details.
The color of brick and stone the customer can choose himself.
The quality of masonry brick is very good, to become a bricklayer is not so easy, this profession is considered to be one of the most prestigious among the Mexicans.
On the facade and side walls of the molding is completely absent, it can be used only on the front side of the house if you want to save a little on the price of the house, though generally a fundamental difference not.
Then, inside the house begins painting, laying tile, installed sockets and other trifles. Just begins to wrap up everything that can be scratched or damaged during work. Ulozheniju locked tiles just thick dense paper, all the windows are still in the films, all bathrooms were closed by special covers.
In parallel, flexible laying ridge tiles on the roof of tar board. In different parts of the roof are made all in the same color, using the same materials (shingles, roofing material, etc.)
Mexicans are working with all the amenities.
Generally Mexican builders in Texas, it is as guest workers in Moscow, the difference lies only in two things: first, Mexicans work legally, and secondly, the quality of the Mexicans are very high, because for hack fired.
Businesses are not profitable to build badly, claimed warranty on the house from 15-50 years (on items), so after each job the engineers check the quality, otherwise then the company will have to fix at their own expense.
The cleanliness of roads should be, they are constantly cleaned and washed.
As can be seen in many photographs of the area I went in the evening. And most builders have finished the job. But some of the material, equipment, tools - were lying here and there, and the houses were open. But to me, I never got approached and asked what I was doing there at a later time? While there, I was approached by two sales manager and asked if I did not help in the selection of the house? I replied that as long as I want to see myself, I left a business card and wished a good evening. About the camera no one even hinted. Why is this happening, and why such complacency? It's very simple - all areas reviewed a large number of cameras. Of course, to steal a hammer or a sheet of drywall can be easily, but the desire to talk with the sheriff after that personally I do not. On the panel on the left shows the county plan, of which I spoke earlier, namely ones and consist districts.
For several of these districts are building swimming pools, playgrounds and other infrastructure individually. Next time I'll show you a house built, ready for delivery. Let's look inside the house, talk about the conditions that the customer has when buying a house, and that the builders are willing to change, if the customer is capricious.
Source: mechanismone.livejournal.com
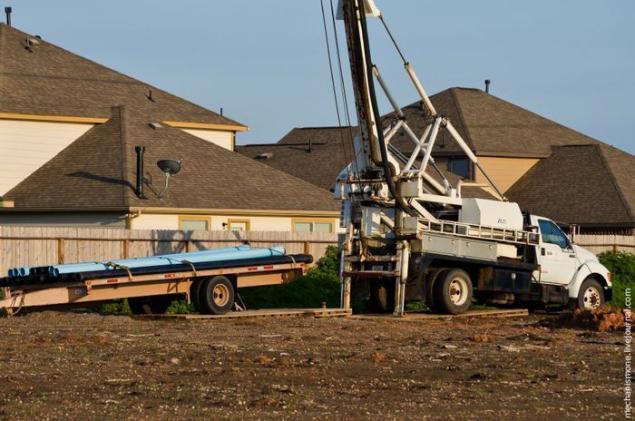
Thus, the construction begins with the master plan for the area. The area is not only home to the district also includes an irrigation system, drainage, treatment facilities, roads, infrastructure for leisure (tracks for walking, jogging and cycling, outdoor swimming pool, tennis courts, soccer fields, basketball, children's playgrounds site and just open parks with artificial lakes with fountains and water channels, and a large fenced area for dogs). The whole area is in turn divided into districts, about 90 - 150 houses (district plan we will see later). Infrastructure created separately for several districts, the people are not "crowd." The whole area will be in the already constructed system of shops, banks, hospitals and other public facilities that were built in advance in view of the ongoing construction of the area and increase the population.
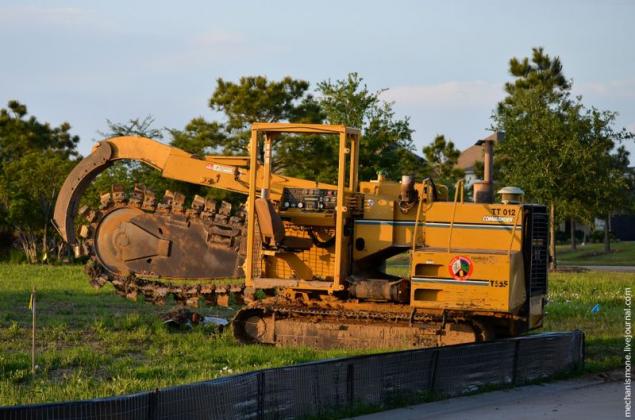
Construction begins with a blank field in which laid all communications, gas pipes, plumbing, electrical cables, telephone. At first, everything is connected to the substation. Tractor for trenching (in the previous pictures - pipe layer).
Then, from the substation all communications are routed to shield houses. All electrical hiding in a box that will be located in a corner of the backyard of the house. Red tube is not hot water, it is fed by the cold water and hot water in the house will not be supplied because Each house will be is a gas or electric boiler. Green tube with a cap - a gas line, and later it will be hidden, as long as it sticks out like a marker.
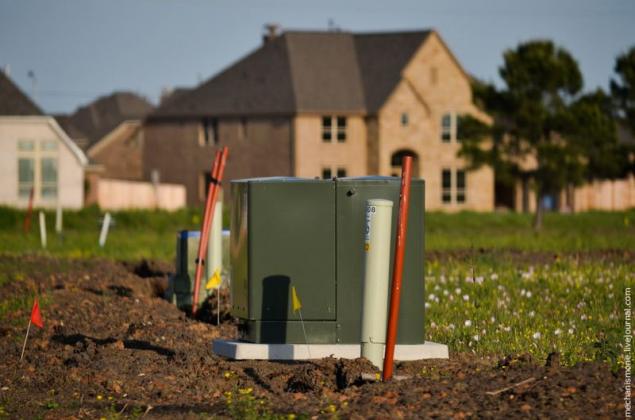
After all utilities laid, preparing irrigation systems, in her Houston pay special attention, because Houston is subject to tropical storms and hurricanes. Typically, the depth of artificial reservoirs is about 10-12 meters. All pools have a system of locks and canals to divert water.
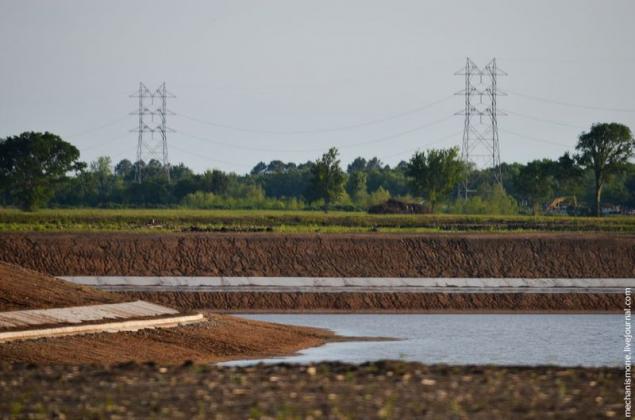
Beach concreted artificial pond at pond to protect and prevent erosion. To prevent water washed away the concrete part of the land near concrete reinforcing tape mud and rubble. Most recently it has been heavy rain, and water pumps pumping water from canals.
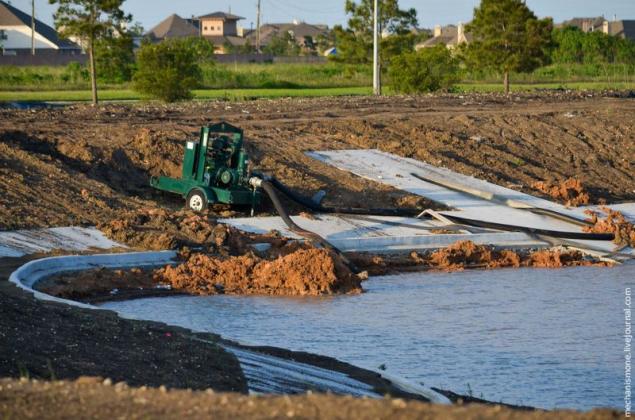
Then the construction of roads and sewerage. The roads provide quick and easy access of construction machinery, and also does not allow carry dirt from construction sites. Near all sewage stacked sandbags, their purpose - to hold the mud when it rains and to prevent clogging of sewers. Sewer pipes - plastic tube diameter of 60 cm from the start, increasing with the length of sewage. Begin laying pipe at a depth of 1.5 meters, respectively, as the depth increases with the length of the system. Pipes are laid at an angle of 0.18%. Sewer grates, there is usually no, instead of them - open water inlet, which is located inside the sewer pit, measuring approximately 2x2 meters. Incidentally, I note that all the pipes, if possible, are not under the road, and next to it, even though all repairs carried out of the mines.
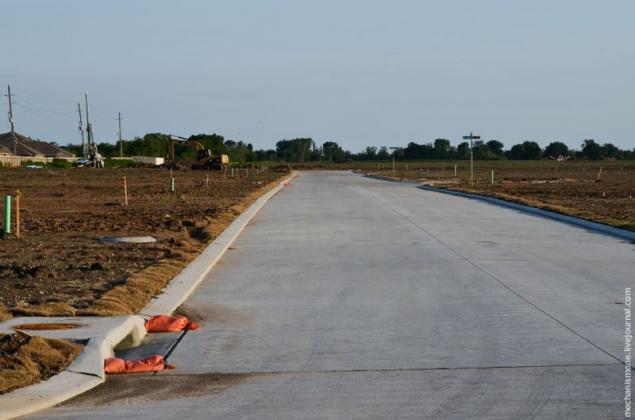
Then, set all the road signs. Marking the roadway in residential areas is not because the speed limit here - 20 km / h. Speed limit signs, too, are not available, the rate registered in the SDA. Earlier, I asked about the height of the curb - it is 15 cm. The thickness of the concrete screed on the road - 21 cm.
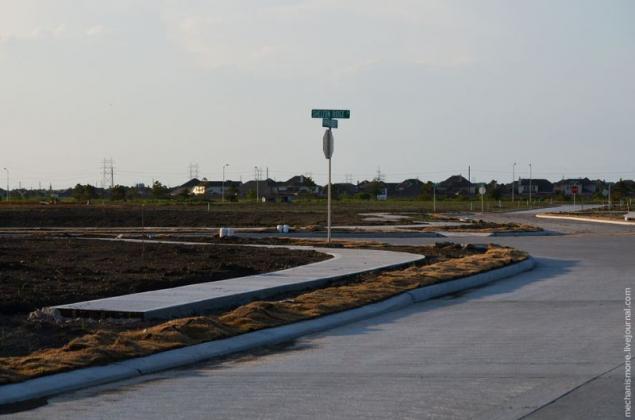
It is very interesting to drive on such areas with all the characters apart, but the complete lack of homes. Pay attention to the tape grass, laid along the border, it prevents leaching of dirt from the lawn to the street in the rain.
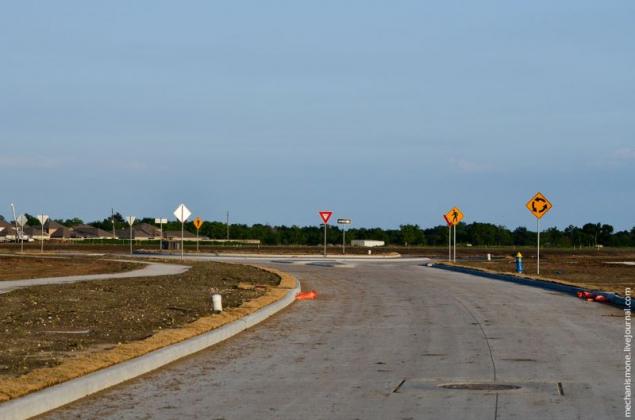
Rashn designer datekted.
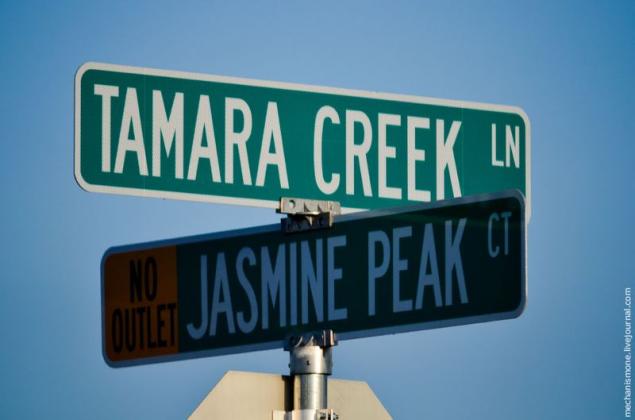
All surfaces, which can be scratched, damaged, soiled or in construction - closed.
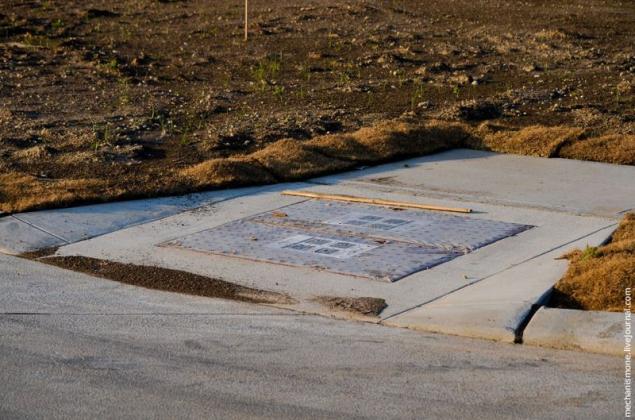
In Russia still can not do the hatches on the road. Oh no no no.
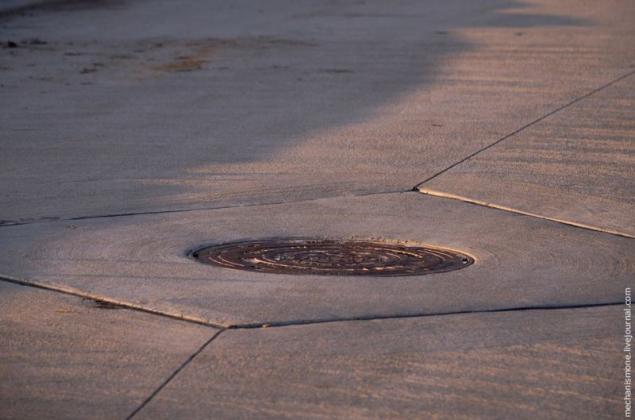
Then prepare the site for homes. At the same time construction of 20-30 houses. They are built mainly around, it is easier to clean debris, and does not disturb those who are already living in populated and built houses. Exceptions are homes that have been purchased in advance for some specific areas. To lay the foundation excavate depth of one meter and is filled with a layer of gravel, sand and clay, all compacted, and then it turns out that's at the top of this cap. Note that this trick is possible only in Texas because of the very clayey ground. For example, in the north of the United States placed a deep strip foundation.
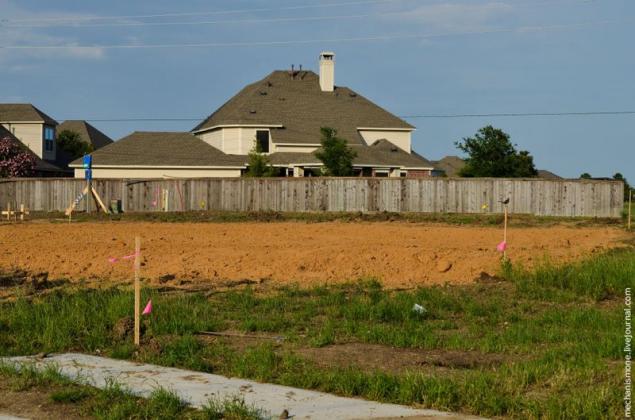
Then the supply of communications to the home (gas, cold water, sewer, electric cable, etc..)
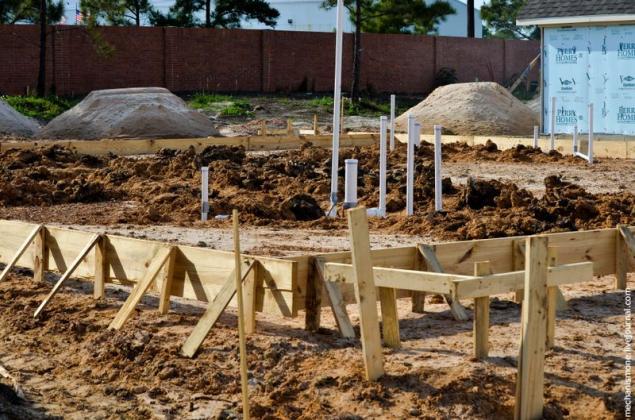
It is going formwork for the foundation. All solid foundations, solid, clay soil allows their relatively thin screed thickness of about 25-30 cm, with the "pillars" of 1.5 meters.

Typically, the average size of the foundation - 20 to 15 meters.
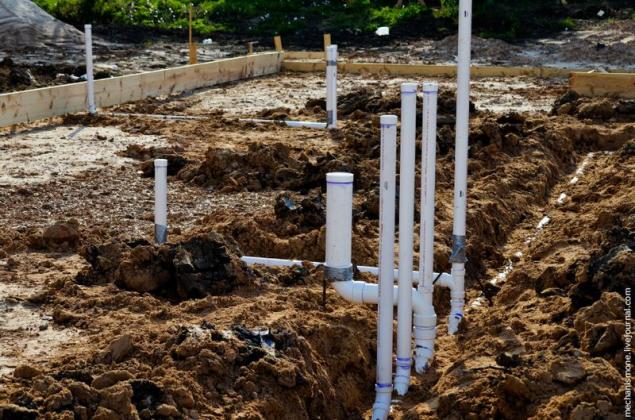
Then the ground is covered with a thick dense plastic, fit fittings with diameters from 10 mm to 16 mm. It fits every 3-4 meters, "criss-cross", except in certain places, such as the garage door of the house, cut the foundation, here it fits a little differently, depending on the design of the house.
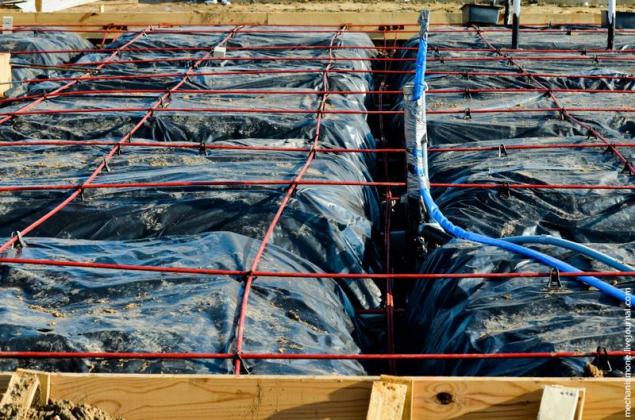
Reinforcement before casting will be stretched, seven days after the filling load is lifted slowly
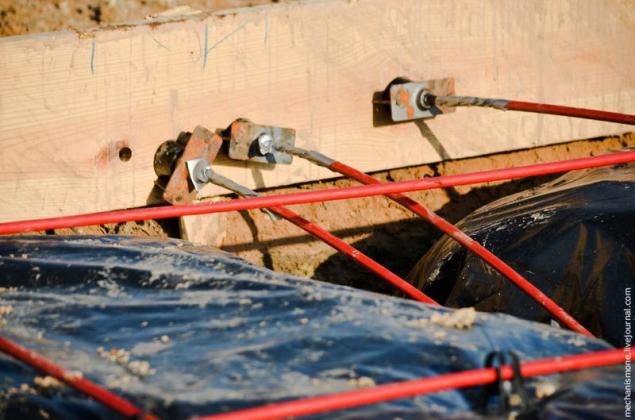
Pouring the foundation is non-stop to complete the work. Permissible concrete strength of 60 to 90 MPa.
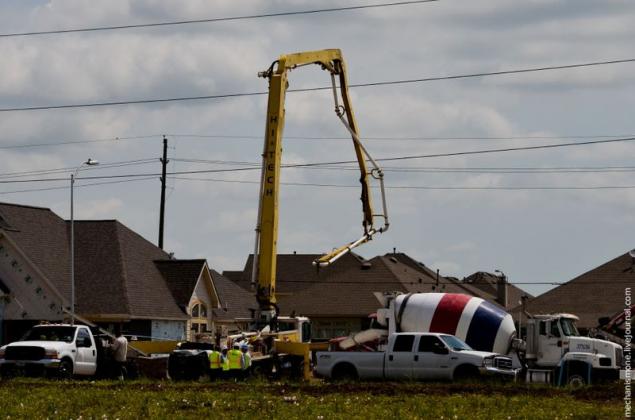
: Fresh screed. Sticking plate - a duralumin anchors (anchor) for walls.
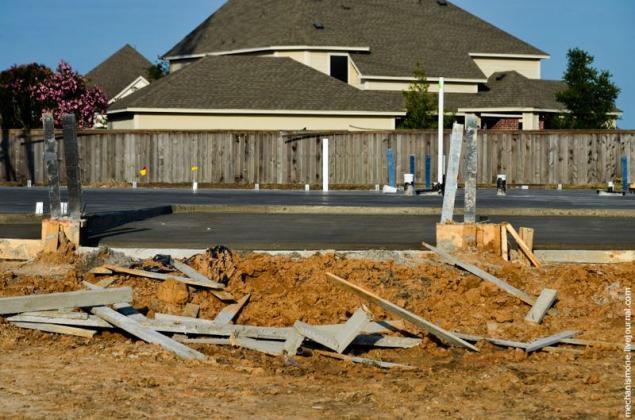
Periodically, the concrete is poured water, preventing the formation of these cracks in it.
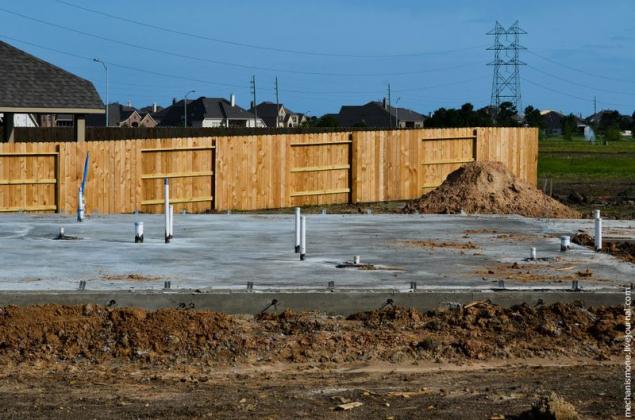
Crib.
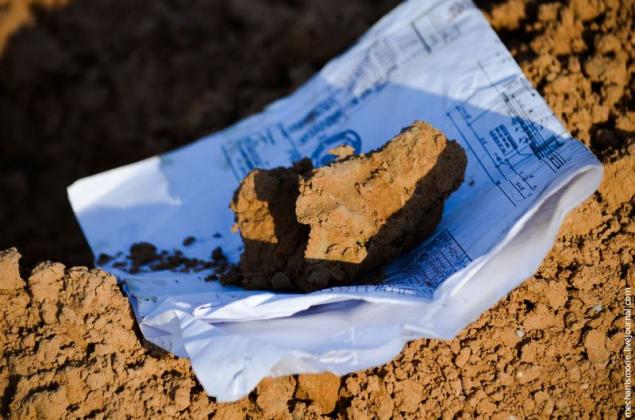
Then filled screed applied marking walls and begins assembling wooden frame houses.
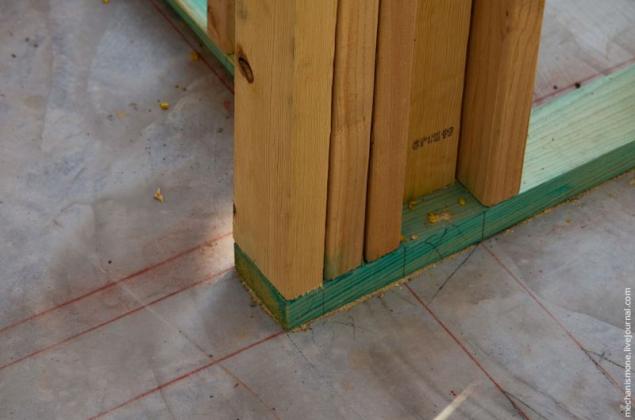
All the supporting structures are assembled at home from a tree commonly used board 15x5, 20x7 cm.
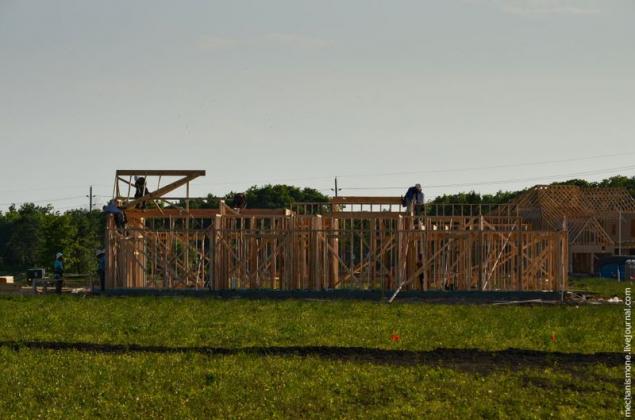
Then sheathed with plywood boards 2 cm thick.
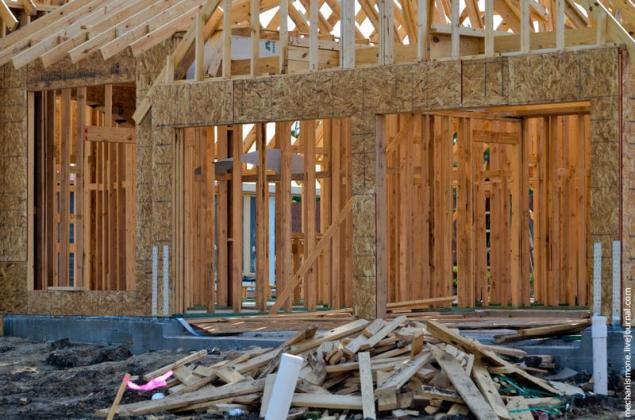
It should be noted that all wood materials for the construction of houses pre-defined mixes and processed oils to protect against insects and water. At the same time, these chemical compounds are not harmful to human health.
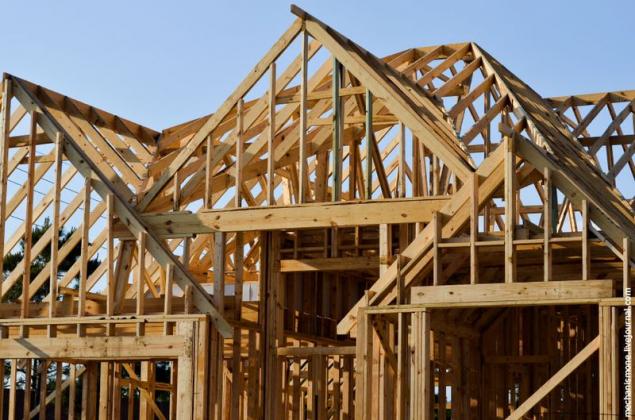
All material is secured with nails and metal anchors. Also used screws, bolt ties, mainly in the critical "nodes." Bruce is almost never used, it is replaced with a few boards nailed together.
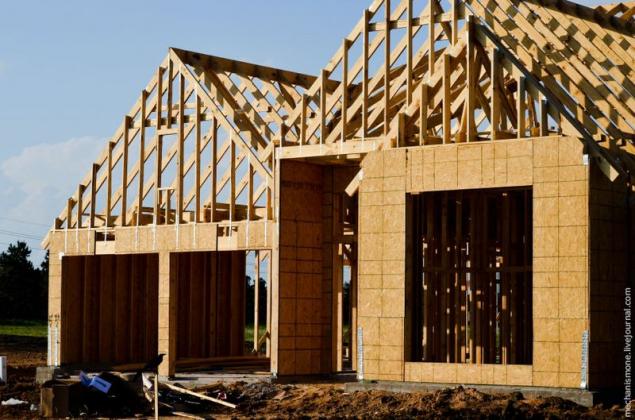
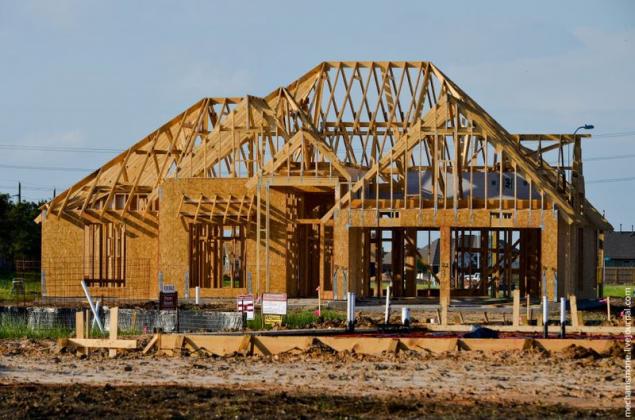
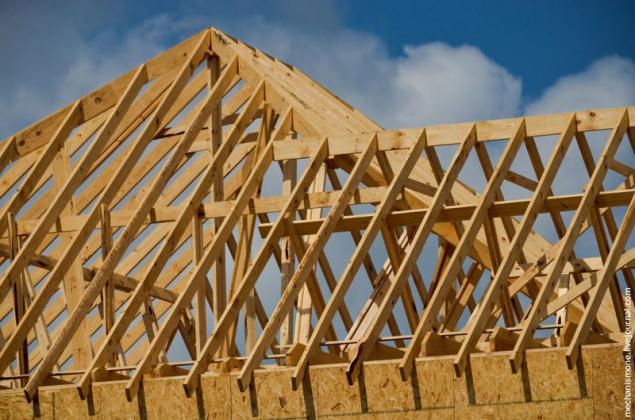
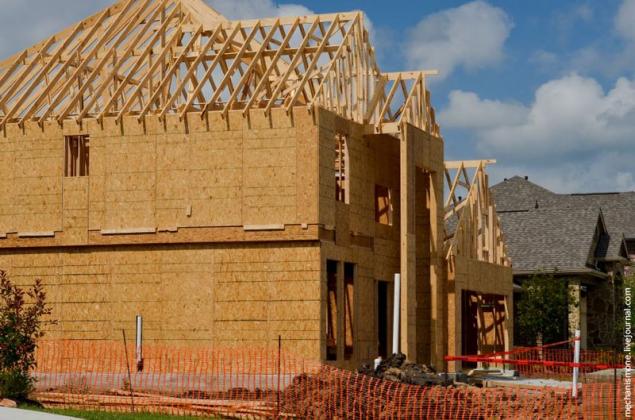
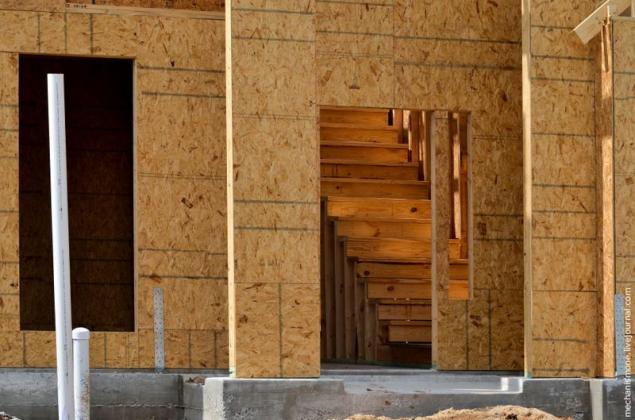
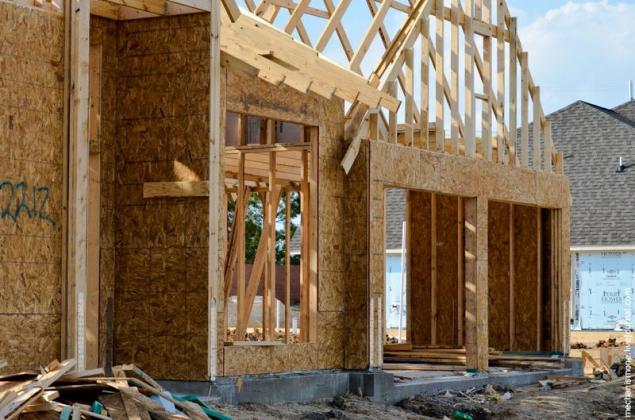
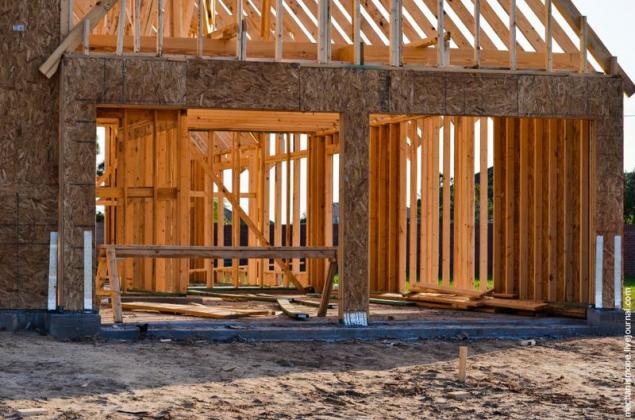
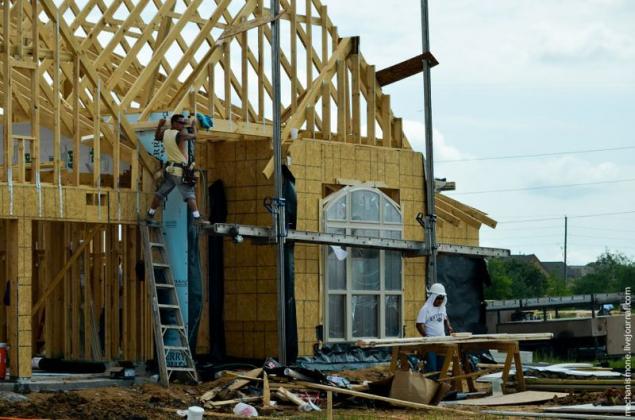
Once the frame is completed at home, inside start to conduct communication. Future in the kitchen sink. Sewer use plastic pipes with a diameter of 6 cm.
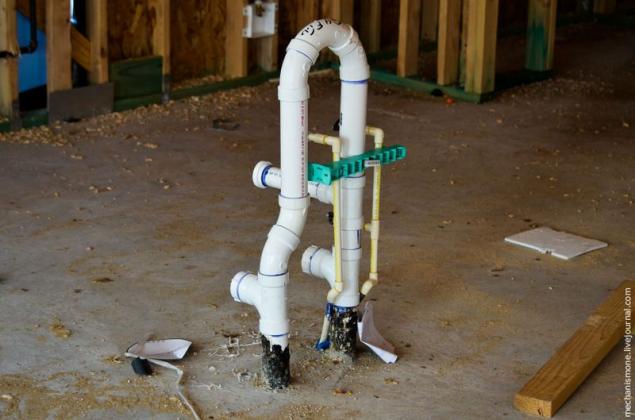
Also inside the house begins to "grow into" the various elements, such as a bar.
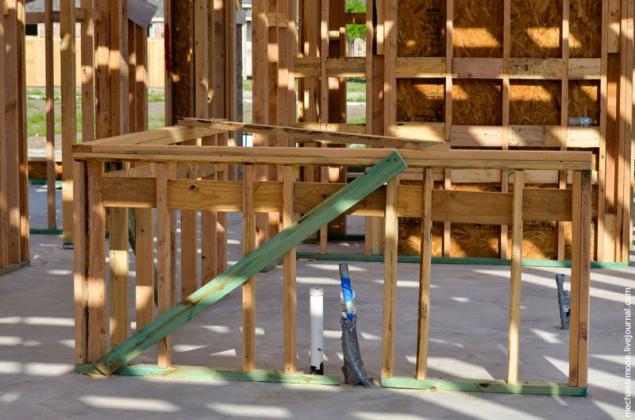
Held communication within the walls.
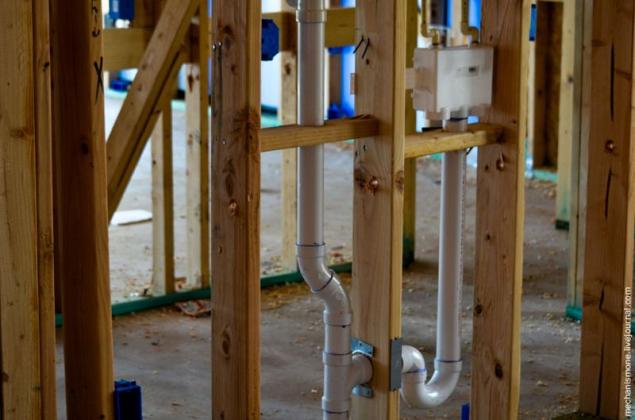
Held electrician.
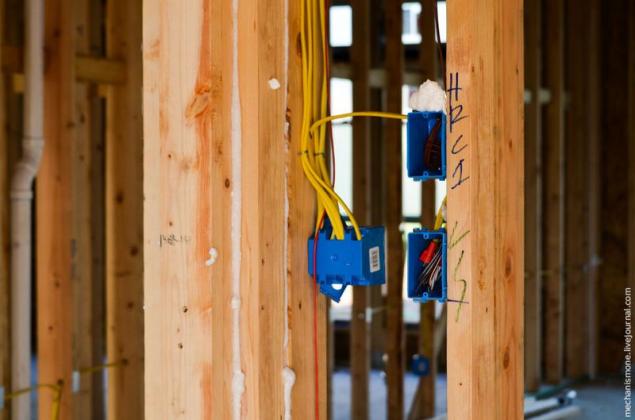
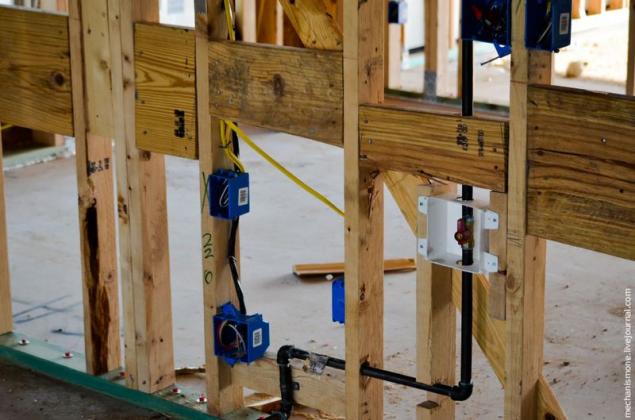
Black wire - Television, yellow - electric, white - the Internet.
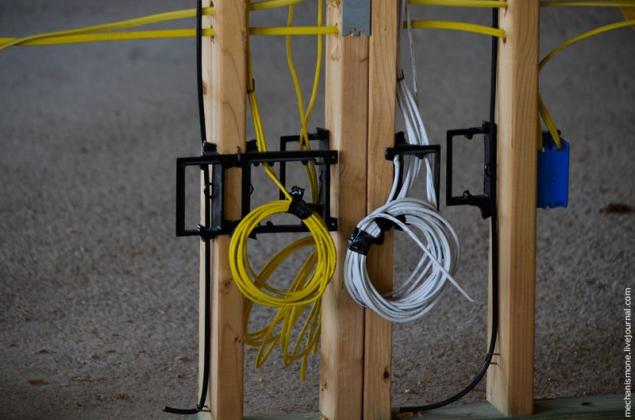
In the attic ventilation system is installed for heating and cooling the house. In fact - it is soft fiberglass pipe. On top of it has a shell of fire-retardant fiberglass, which is hidden under the glass wool, which is located inside the soft aluminum tube. Today, these ventilation pipes are used where the air flow rate does not exceed 30 m / s. At a higher speed air circulation using tougher ventilation system.

Output room.
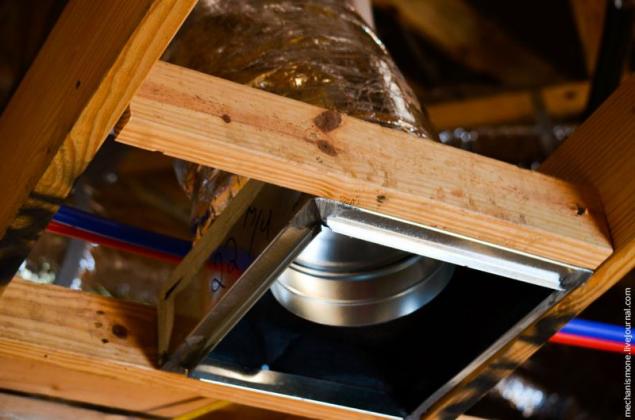
Water unit. For water used plastic pipes with a diameter of 13 mm, can withstand the pressure of 0.7 MPa and a temperature of 95 C.
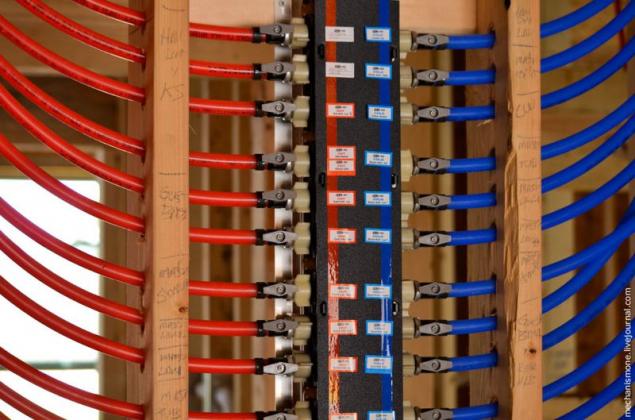
Bathroom and toilet.
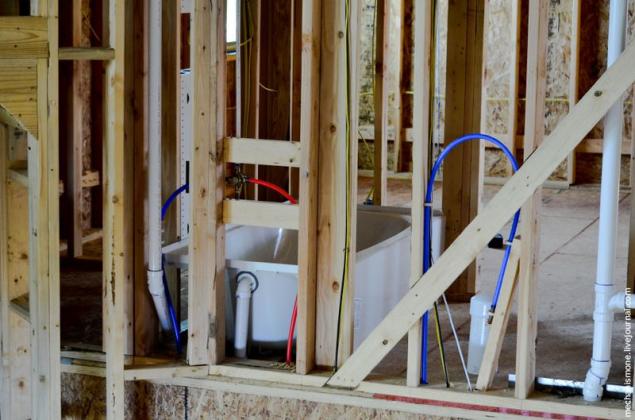
Then set fireplace. These homes all have gas fireplaces, they are much easier to install because they do not require masonry and problems with the valves. In some houses commissioned by the buyer build real fireplaces.
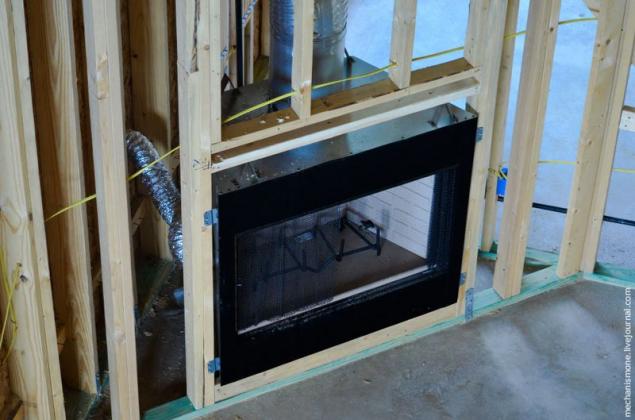
By the way, nice gas fireplace warms the house. Although, of course, with a real fire can not be compared.
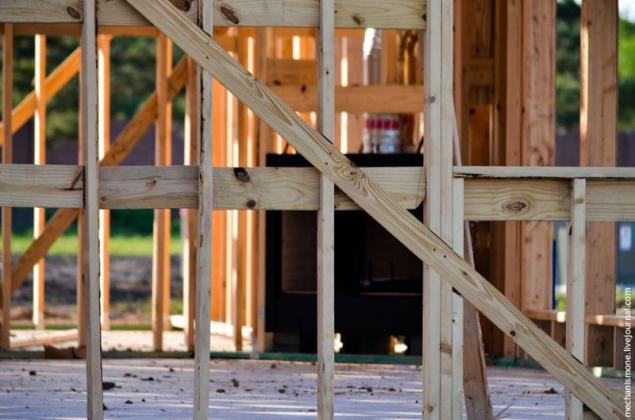
Then sheathe plywood wall on one side, on the other hand openings in the glass wool is inserted, after which the wall is sutured and plywood. Then the plywood sheathed with plasterboard. Note that insulation in the house is very good, in spite of this, the apparent fragility of the walls, and the cries of the children's zombies are not heard in the hall, as well as operating a loud TV in the bedroom. Thanks to high-quality glass wool.
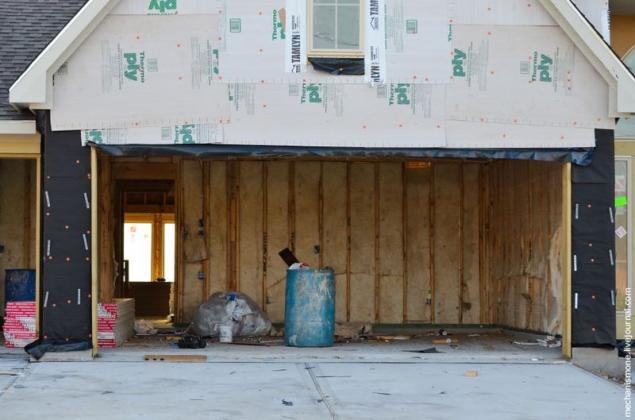
Then drywall puttied.
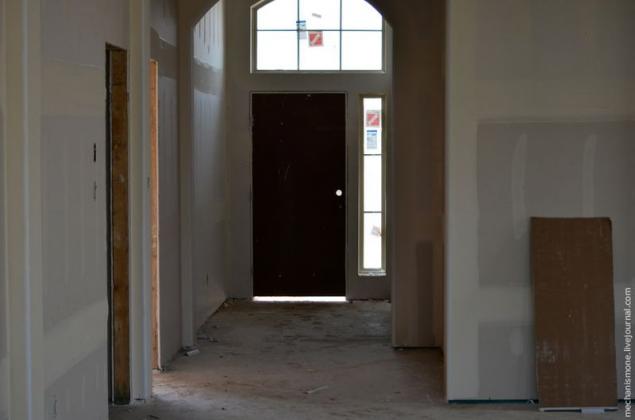
Future jacuzzi. Gather different designs inside the house.
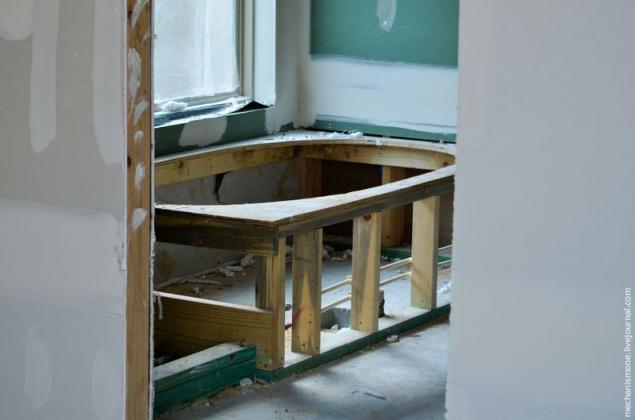
Shower.
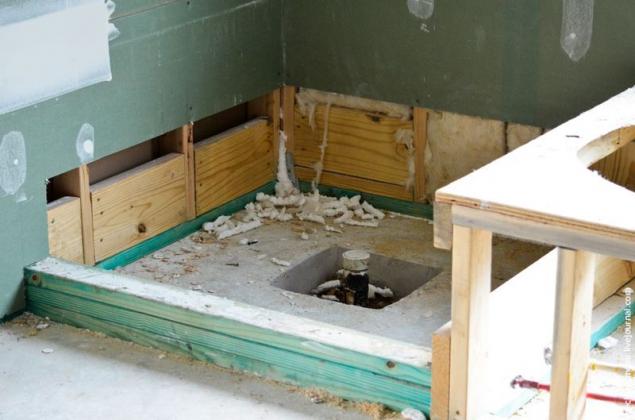
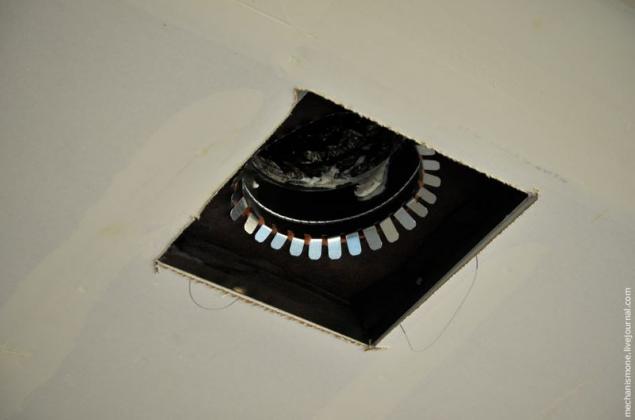
Garage.
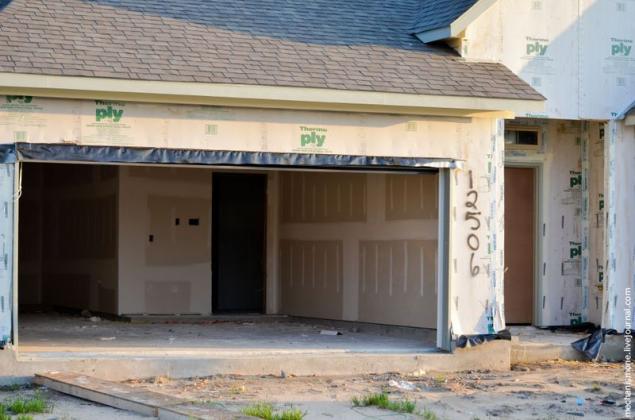
Then insert the window. The outer part of the house is sheathed with additional noise insulation and insulated polystyrene panels (blue on the left), with the value of R is 3, the thickness of the panels - 13mm. Top panels are sewn plastic and a layer of thick roofing material (black on the right).
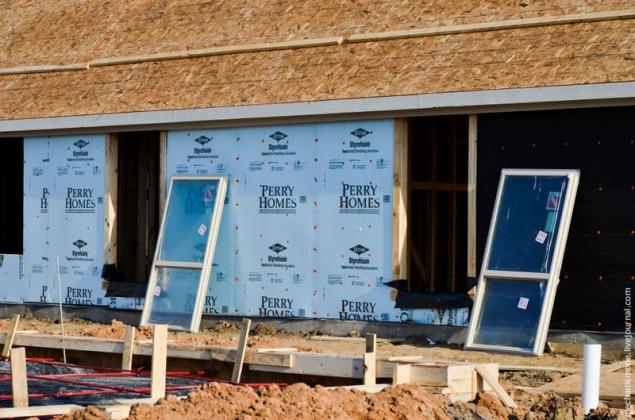
Windows, used in construction, "southern", and can be used only in Texas, Louisiana, Florida, Southern California, Arizona and New Mexico. The windows have a U-value of 2, the coefficient of heat - 0.23, light transmission - 0.43.
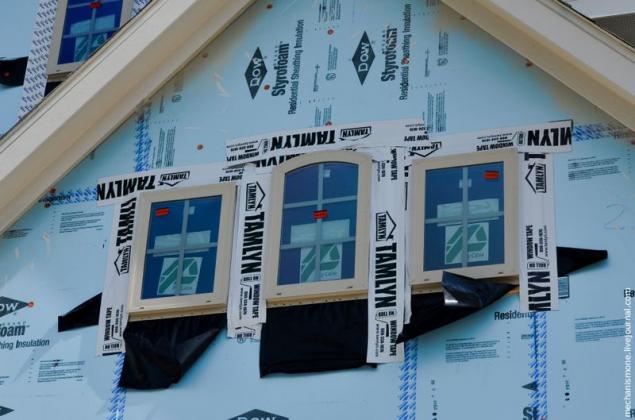
Finally, the time comes to masonry.
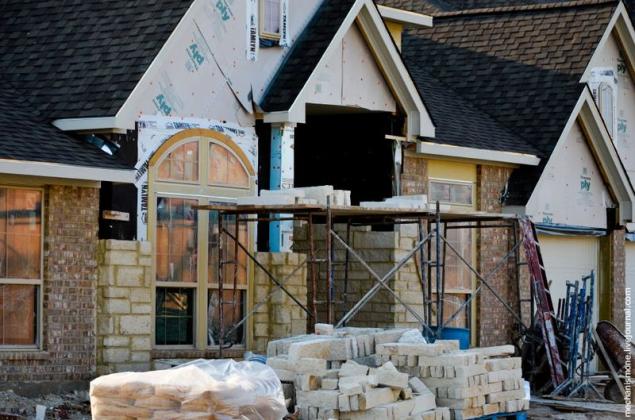
Decorative brick, standard ASTM - SW. In addition to brick and stone used.
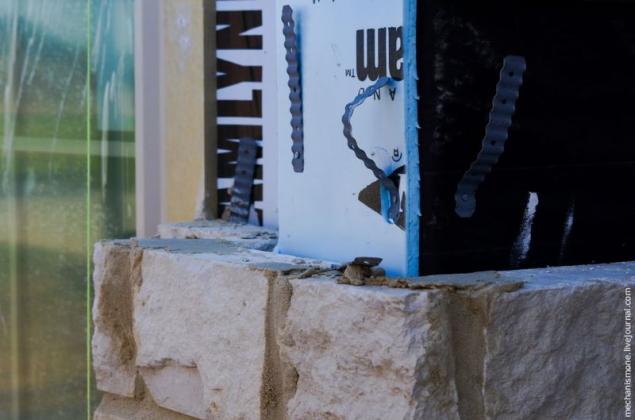
Between the wall and the masonry is left 5-6 inch gap for air circulation.
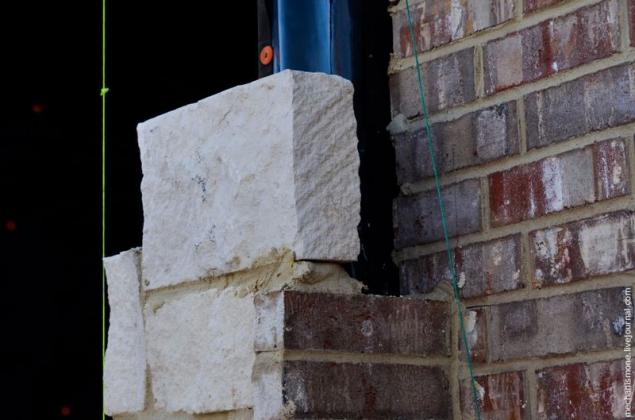
Accordingly, under the peak of left vent.
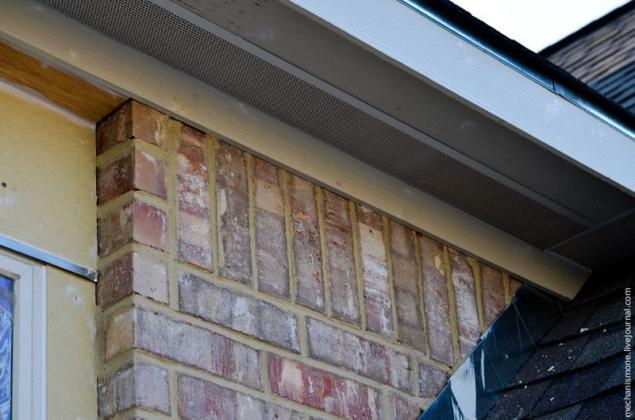
Fans details.
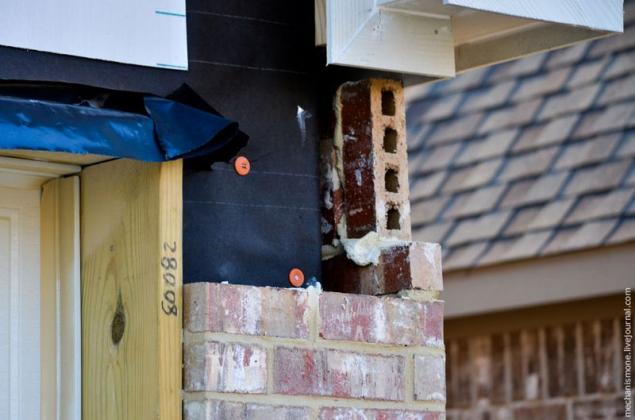
The color of brick and stone the customer can choose himself.
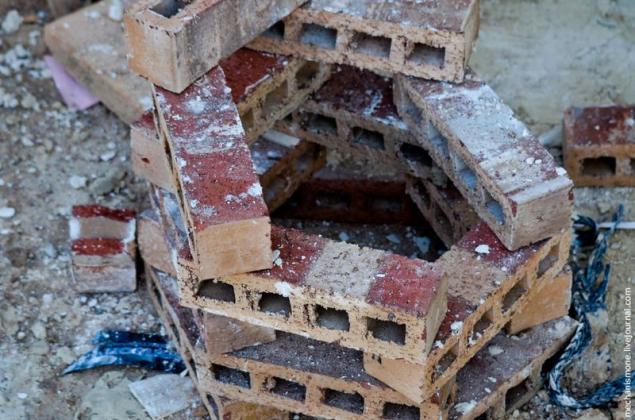
The quality of masonry brick is very good, to become a bricklayer is not so easy, this profession is considered to be one of the most prestigious among the Mexicans.
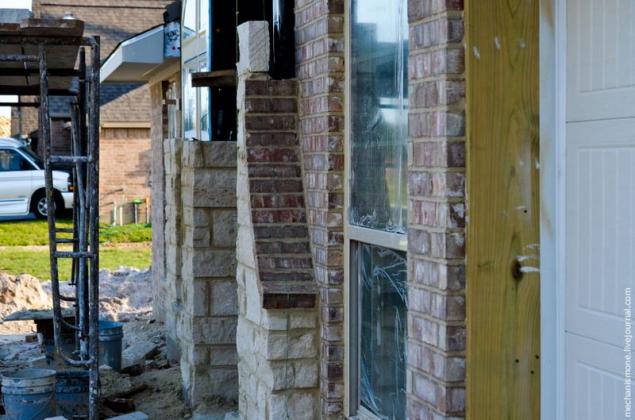
On the facade and side walls of the molding is completely absent, it can be used only on the front side of the house if you want to save a little on the price of the house, though generally a fundamental difference not.
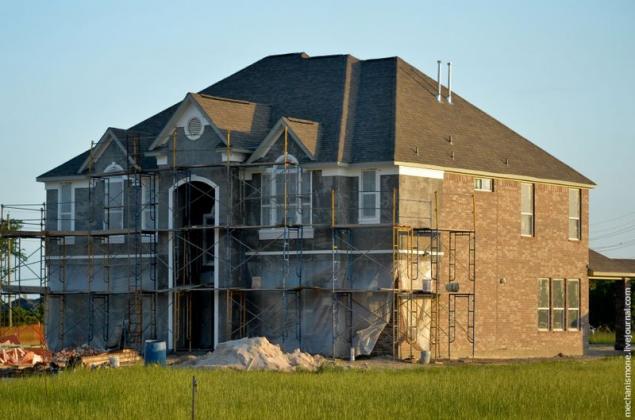
Then, inside the house begins painting, laying tile, installed sockets and other trifles. Just begins to wrap up everything that can be scratched or damaged during work. Ulozheniju locked tiles just thick dense paper, all the windows are still in the films, all bathrooms were closed by special covers.
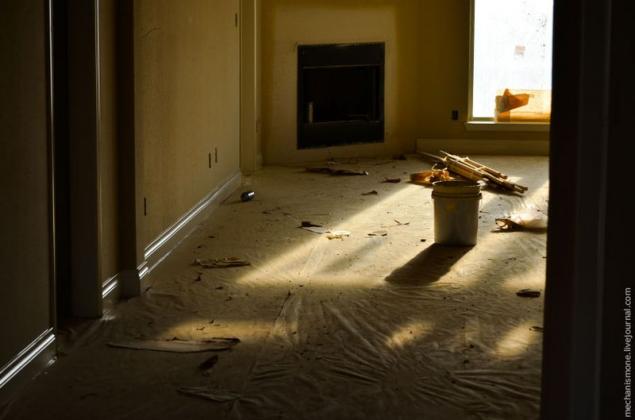
In parallel, flexible laying ridge tiles on the roof of tar board. In different parts of the roof are made all in the same color, using the same materials (shingles, roofing material, etc.)
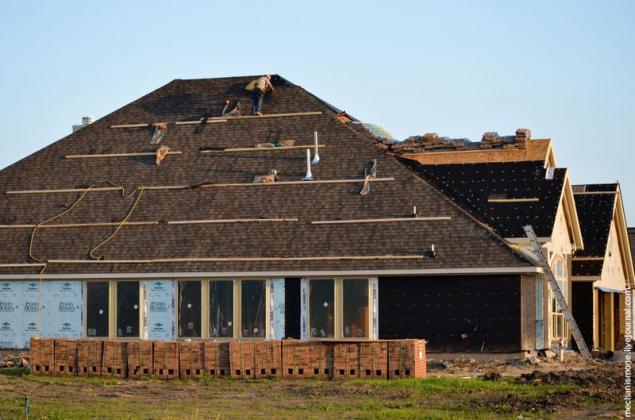
Mexicans are working with all the amenities.
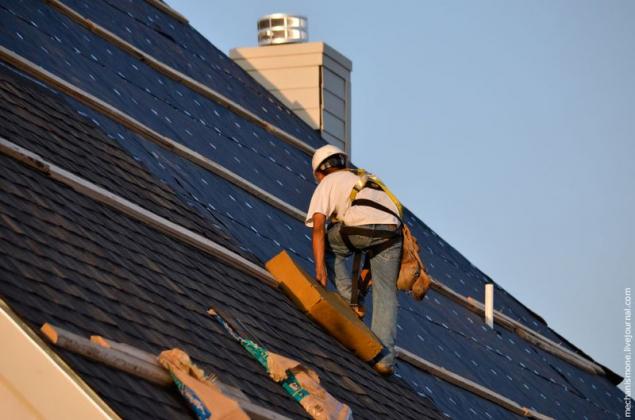
Generally Mexican builders in Texas, it is as guest workers in Moscow, the difference lies only in two things: first, Mexicans work legally, and secondly, the quality of the Mexicans are very high, because for hack fired.
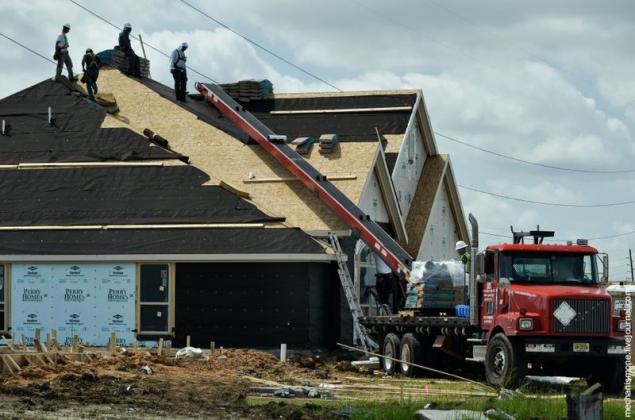
Businesses are not profitable to build badly, claimed warranty on the house from 15-50 years (on items), so after each job the engineers check the quality, otherwise then the company will have to fix at their own expense.
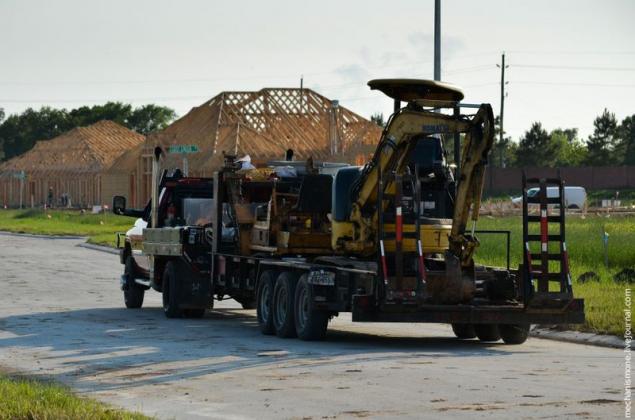
The cleanliness of roads should be, they are constantly cleaned and washed.
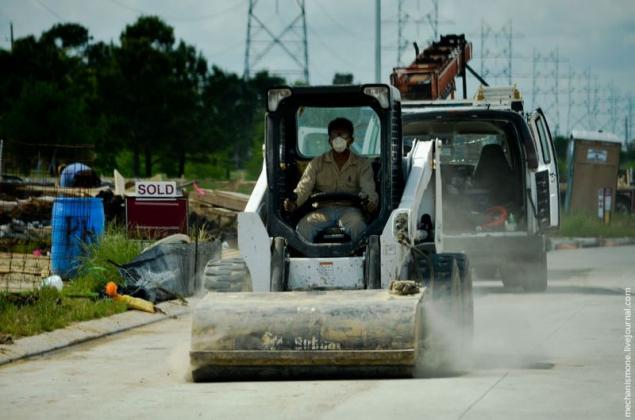
As can be seen in many photographs of the area I went in the evening. And most builders have finished the job. But some of the material, equipment, tools - were lying here and there, and the houses were open. But to me, I never got approached and asked what I was doing there at a later time? While there, I was approached by two sales manager and asked if I did not help in the selection of the house? I replied that as long as I want to see myself, I left a business card and wished a good evening. About the camera no one even hinted. Why is this happening, and why such complacency? It's very simple - all areas reviewed a large number of cameras. Of course, to steal a hammer or a sheet of drywall can be easily, but the desire to talk with the sheriff after that personally I do not. On the panel on the left shows the county plan, of which I spoke earlier, namely ones and consist districts.
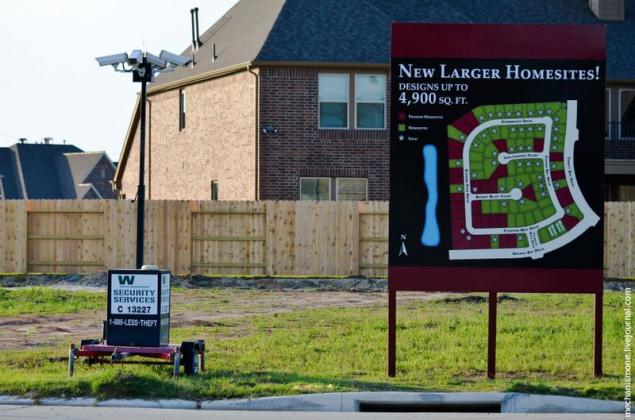
For several of these districts are building swimming pools, playgrounds and other infrastructure individually. Next time I'll show you a house built, ready for delivery. Let's look inside the house, talk about the conditions that the customer has when buying a house, and that the builders are willing to change, if the customer is capricious.
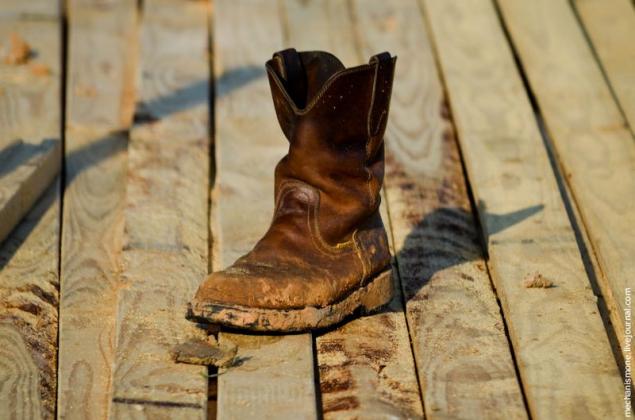
Source: mechanismone.livejournal.com