Logistics automation for factories of the future
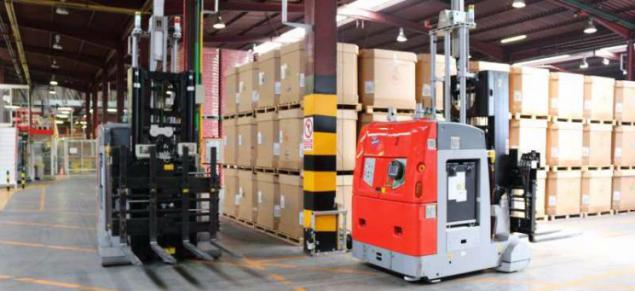
Today, mass production and packing factories in highly automated, while logistics is still lagging behind. Transportation of raw materials and finished products still depends on manual labor. However, the study automatically operated vehicles carried out EU foreshadows changes in this area in the next decade, as well as the emergence of thousands of jobs .
Transportation of raw materials and finished products at the plant - still a time-consuming process, which is implemented mainly by means of forklift trucks. This system is traditionally prone to errors, is costly, inefficient (in terms of scheduling and power consumption) and frequently results in accidents. Any kind of delay are commonplace even in the automated plants, making it difficult to timely delivery and inventory.
Project PAN-Robots, which involved six partners in five countries in the EU exists because of EU funding in the amount of 3, 33 million. Euro and is engaged in providing innovative technologies for the automation of logistics on the so-called "factory of the future» (FoF).
Automatic guided vehicles (AGVs), used in factories today are still at an early stage of its development. Companies applying them return investments quickly enough, but these systems can be significantly improved by on-board cameras, laser scanners and mapping systems, 3D-objects, - said Dr. Kay Fürstenberg, project coordinator of the German company SICK AG, which produces sensors .
Blockquote>
Robot with a wide viewing angle
PAN-Robots focused on our core operating areas and has: a system for 3D-display plant; extended system of perception on board automatically operated vehicles; modern control center for monitoring and infrastructure laser scanners distributed under the project.
The most innovative technology in the project - it is a stereo with a lens "Fisheye", established in the top of the AGV. It uses a 3D-image to watch for obstacles.
360-degree field of view camera («3D-perception") and laser scanners, safety checks («2D-security") ensures that the robot will not be "blind spots" and provides security for people who work with him at the factory or stock. The vehicle can be rotated a full overview, stop in front of obstacles encountered in its path, or bypass it. Perceptual system can even "see" what is around the corner, by interacting with laser scanners at intersections.
PAN-Robots have passed the first test on the Coca-Cola plant in Madrid. Now the team is preparing to take the test at the factory of soft drinks in Bilbao to check the car in the real world, and prepare the final demonstration of the closure of the project in October this year.
The results are very interesting, - said Dr. Furstenberg - experienced robot at two factories, we can demonstrate that the technology adapts to different environments.
Blockquote>
Results include self-localization innovative technology, which relies on the identification of natural landmarks in the warehouse, not the set of reflectors, saving 90% on the installation of reflectors.
Advanced AGV also use 50% less power than a conventional truck and will perform each of the operations than current AGVs, which means that in future minimal number of vehicles will be able to perform the same amount of work. Furthermore, the system PAN-Robots can be put into operation two, instead of six months, reducing the downtime of the plant.
The first product is ready for market entry
Now the partners are discussing several products to existing customers. There is a possibility that they will be released to the market in the next few years. As other projects will require more effort for their implementation, the partners seek to run the camera and other systems in the medium term.
There is a high probability that half of European plants 2030 a > will work with parks Automatically operated vehicles, says Dr. Furstenberg, and manufacturers of robots will create thousands of jobs over the next decade.
Source: geektimes.ru/company/robohunter/blog/253074/