919
NanoShield for metal
Hello, GT!
I are inherently creepy choleric. Perhaps this is a general property of the people who are always interested in something new or are passionate about science. But sometimes I get bored. Another bout of creative blues last week I dispelled in society very brave people. To those I refer those who are not looking endemic dual-currency hysteria every crisis is not afraid to develop interesting technology, and even open up new production! Today I will talk about these brave souls who came up with evolving technology and micro-arc oxidation of non-ferrous metals.
About the technology
Microarc oxidation (MAO) - a special technology of surface treatment of various metals. Technique is that when a current of high density in a special electrolyte to the workpiece surface microplasma discharges start to occur. These bits are formed on a surface of a very high quality oxide-ceramic coating - a coating of a kind of metal oxide forms thereof and the substances dissolved in the electrolyte. This allows you to bring different parts amazing shades, and most importantly - to form the ceramic coating has a completely unique properties. Increased hardness, wear resistance, there are reflective or vice versa - light-absorbing properties. Also changes the structure of the surface increases adhesion to further coating or painting to the banal. Details are resistant to corrosion and protective coating has a dielectric strength of up to 2 kV. And this is not an exhaustive list of the newly established properties. After the arc which the workpiece is formed on the surface of a complicated structure because ultrahigh temperature and pressure at the interface "electrode-electrolyte interface." In the photo you can see how the process MDO. Details of light because microarcs.
It may seem that the part during machining is extremely hot. In fact, it is cold, and the entire process occurs in a layer a few microns thick. In the process of MAO is formed layer by layer defined nanostructure, which gradually build up to tens of microns in thickness, forming the final coating. Machining process takes five minutes to an hour. The time depends on the thickness of the coating which we want to get and what kind of coverage is necessary to generate the details. If necessary, complicated and thick coating (up to 50 md.) Coating process and can last for several hours. But in most applications, this is not required. MDO processing technology may be subjected to all the alloys of aluminum and titanium, magnesium and zinc.
Unfortunately my scanner was unable to transmit sensations of color on the type of parts covered by MAO technology. All the same I give this picture. Matte, very warm and looks expensive. The picture shows a square aluminum plate for a demonstration. Incidentally, the black coating has a 94% black, and can be used in optical components blackening where a sufficient black level.
What happens to the material? B>
Because of the action microarcs structure of the material changes. The surface becomes a slightly rough and covered with a very dense oxide film. If the task is not to change the color of the coating, as for example, is required to prepare the item for painting, it's just wonderful and expensive technology. Aluminum parts in a few minutes of treatment become milky and are perfectly applied any paint. It must be remembered that aluminum is not so easy to paint. Many paint on it poorly kept or not applied, curling up into small balls. After the MAO process item can paint just 10 minutes as soon as it is dry from the water in which the item is rinsed after MAO process. According to this technology can handle the most complex parts of forms. The coating occurs in all places. If somewhere coating is not necessary - it is necessary to isolate the place, for example, causing varnish. On the photo micrographs of the metal structure before (upper) and after (bottom) processing MAO. As can be seen on the surface formed microcraters. Thus, MAO coatings are porous ceramic composite structure which is formed by the oxidation of the metal and the inclusion in the coating composition of chemical elements from the electrolyte. This porous structure is, in turn, provides excellent properties of a covering with further coloring components. Competing MAO technology is anodizing, but unlike the technology in MDO has significant advantages. First of all, the quality of the coating and its adhesion, without complicated sample preparation and environmental components.
Where can I apply? B>
MAO technology allows replacement of expensive materials such as bronze, brass and stainless steel in the cheaper aluminum alloy coated with a ceramic oxide coating. In turn, this reduces the weight and cost reduction of parts cost due to machining. By MAO technology can produce high-performance heat sinks in electronics, efficient IR reflectors, gorgeous and affordable housing for appliances, designer materials and much more.
This technology can find the perfect application in mechanical engineering, aerospace, aviation. Has the potential of its use in microelectronics, which is still not otsenёn. For example, it is possible to create plates that are applied through dielectric layers ultra-bright light-emitting diodes, and the plate itself is blackened for efficient heat removal from the chip. Developers experiments were conducted on the coating of complex finned heat sinks, which increases the efficiency of the at times! This lets you save, because the effective heat sink can be smaller mass and size.
How does it work in practice? B>
Installation is simple and does not differ much from the hydrolysis of the bath. The most interesting is the processing conditions and the composition of the electrolyte. Wherein the electrolyte does not contain heavy metals, ions of chromium, cyanide and the strong acid.
Of course, an electrolyte drink is not necessary, but the production is quite eco-friendly. Used electrolyte is easily utilized - in fact there is almost no chemicals. They all go into the ceramic material on the surface of the metal, and ceramics itself is not a no-brainer - it's sintered structure exposed microarcs. In this case, the initial time of the arc is not visible to the eye. Bright glow occurs gradually and becomes visible when the coating becomes thick enough. Workpieces are limited only by the size of the bath. For example, at the moment of the bath up to 2 meters. The technology does not require a lot of energy.
And, of course, a short video to see with your own eyes.
PS It was a pleasure to meet and visit this interesting company. I want to somehow support the guys in their project. I do not give a direct link to the company to not get banned for advertising, but all the same if you have any questions or there is interest - please write me an email and I will give asmtomsk@gmail.com your questions directly to experts. Moreover, the company not only provides services for coating, but they themselves installation and chemistry for the electrolytes.
All have a nice day!
Source: geektimes.ru/post/242160/
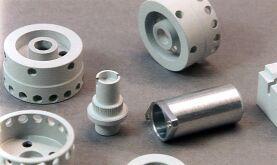
I are inherently creepy choleric. Perhaps this is a general property of the people who are always interested in something new or are passionate about science. But sometimes I get bored. Another bout of creative blues last week I dispelled in society very brave people. To those I refer those who are not looking endemic dual-currency hysteria every crisis is not afraid to develop interesting technology, and even open up new production! Today I will talk about these brave souls who came up with evolving technology and micro-arc oxidation of non-ferrous metals.
About the technology
Microarc oxidation (MAO) - a special technology of surface treatment of various metals. Technique is that when a current of high density in a special electrolyte to the workpiece surface microplasma discharges start to occur. These bits are formed on a surface of a very high quality oxide-ceramic coating - a coating of a kind of metal oxide forms thereof and the substances dissolved in the electrolyte. This allows you to bring different parts amazing shades, and most importantly - to form the ceramic coating has a completely unique properties. Increased hardness, wear resistance, there are reflective or vice versa - light-absorbing properties. Also changes the structure of the surface increases adhesion to further coating or painting to the banal. Details are resistant to corrosion and protective coating has a dielectric strength of up to 2 kV. And this is not an exhaustive list of the newly established properties. After the arc which the workpiece is formed on the surface of a complicated structure because ultrahigh temperature and pressure at the interface "electrode-electrolyte interface." In the photo you can see how the process MDO. Details of light because microarcs.
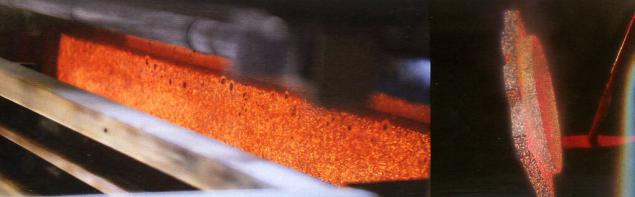
It may seem that the part during machining is extremely hot. In fact, it is cold, and the entire process occurs in a layer a few microns thick. In the process of MAO is formed layer by layer defined nanostructure, which gradually build up to tens of microns in thickness, forming the final coating. Machining process takes five minutes to an hour. The time depends on the thickness of the coating which we want to get and what kind of coverage is necessary to generate the details. If necessary, complicated and thick coating (up to 50 md.) Coating process and can last for several hours. But in most applications, this is not required. MDO processing technology may be subjected to all the alloys of aluminum and titanium, magnesium and zinc.
Unfortunately my scanner was unable to transmit sensations of color on the type of parts covered by MAO technology. All the same I give this picture. Matte, very warm and looks expensive. The picture shows a square aluminum plate for a demonstration. Incidentally, the black coating has a 94% black, and can be used in optical components blackening where a sufficient black level.
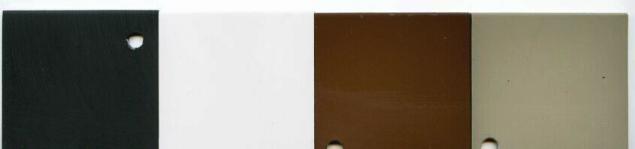
What happens to the material? B>
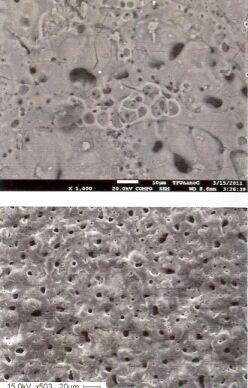
Because of the action microarcs structure of the material changes. The surface becomes a slightly rough and covered with a very dense oxide film. If the task is not to change the color of the coating, as for example, is required to prepare the item for painting, it's just wonderful and expensive technology. Aluminum parts in a few minutes of treatment become milky and are perfectly applied any paint. It must be remembered that aluminum is not so easy to paint. Many paint on it poorly kept or not applied, curling up into small balls. After the MAO process item can paint just 10 minutes as soon as it is dry from the water in which the item is rinsed after MAO process. According to this technology can handle the most complex parts of forms. The coating occurs in all places. If somewhere coating is not necessary - it is necessary to isolate the place, for example, causing varnish. On the photo micrographs of the metal structure before (upper) and after (bottom) processing MAO. As can be seen on the surface formed microcraters. Thus, MAO coatings are porous ceramic composite structure which is formed by the oxidation of the metal and the inclusion in the coating composition of chemical elements from the electrolyte. This porous structure is, in turn, provides excellent properties of a covering with further coloring components. Competing MAO technology is anodizing, but unlike the technology in MDO has significant advantages. First of all, the quality of the coating and its adhesion, without complicated sample preparation and environmental components.
Where can I apply? B>
MAO technology allows replacement of expensive materials such as bronze, brass and stainless steel in the cheaper aluminum alloy coated with a ceramic oxide coating. In turn, this reduces the weight and cost reduction of parts cost due to machining. By MAO technology can produce high-performance heat sinks in electronics, efficient IR reflectors, gorgeous and affordable housing for appliances, designer materials and much more.
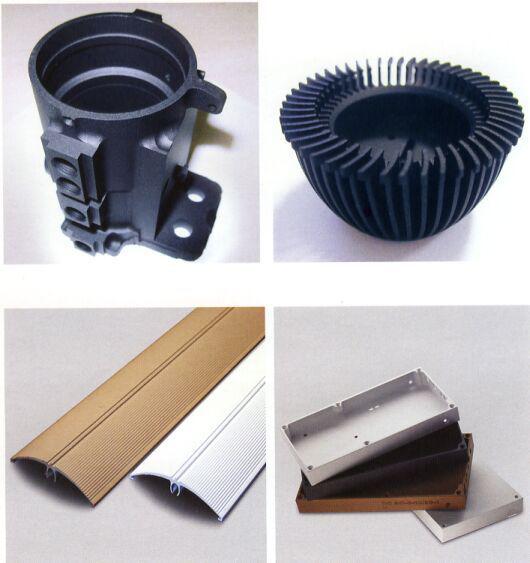
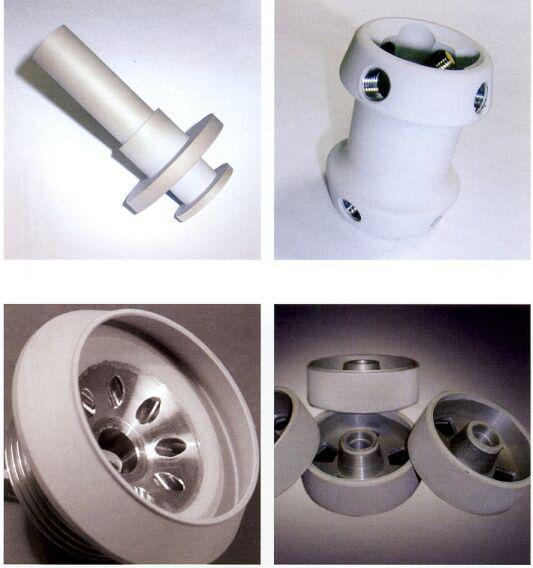
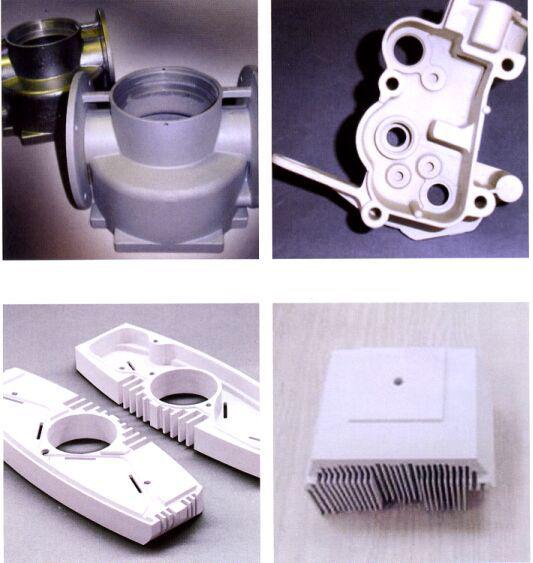
This technology can find the perfect application in mechanical engineering, aerospace, aviation. Has the potential of its use in microelectronics, which is still not otsenёn. For example, it is possible to create plates that are applied through dielectric layers ultra-bright light-emitting diodes, and the plate itself is blackened for efficient heat removal from the chip. Developers experiments were conducted on the coating of complex finned heat sinks, which increases the efficiency of the at times! This lets you save, because the effective heat sink can be smaller mass and size.
How does it work in practice? B>
Installation is simple and does not differ much from the hydrolysis of the bath. The most interesting is the processing conditions and the composition of the electrolyte. Wherein the electrolyte does not contain heavy metals, ions of chromium, cyanide and the strong acid.
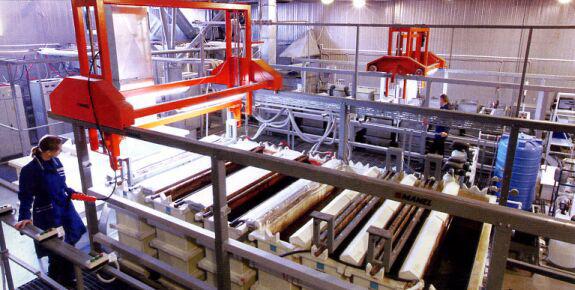
Of course, an electrolyte drink is not necessary, but the production is quite eco-friendly. Used electrolyte is easily utilized - in fact there is almost no chemicals. They all go into the ceramic material on the surface of the metal, and ceramics itself is not a no-brainer - it's sintered structure exposed microarcs. In this case, the initial time of the arc is not visible to the eye. Bright glow occurs gradually and becomes visible when the coating becomes thick enough. Workpieces are limited only by the size of the bath. For example, at the moment of the bath up to 2 meters. The technology does not require a lot of energy.
And, of course, a short video to see with your own eyes.
PS It was a pleasure to meet and visit this interesting company. I want to somehow support the guys in their project. I do not give a direct link to the company to not get banned for advertising, but all the same if you have any questions or there is interest - please write me an email and I will give asmtomsk@gmail.com your questions directly to experts. Moreover, the company not only provides services for coating, but they themselves installation and chemistry for the electrolytes.
All have a nice day!
Source: geektimes.ru/post/242160/