1080
Laser Technology 3D-printing of several metals with a smooth transition between them
In the NASA Jet Propulsion Laboratory in conjunction with the California Institute of Technology and the University of Pennsylvania have developed technology 3D-printing of several metals simultaneously , which lets you create items with a smooth transition from one metal to another. Was based on a standard for 3D-printing technology for metal laser sintering of metal powder.
To dispensed into the print zone different metals, the print head had four nozzles, each of which was fed its powder form. Varying dosage of various metals with such heads can be accurate to about 1%. Besides conventional 3D-printing, in which the head is movable in all three axes, creating a product practically arbitrary shape, the method was tested radial press, whereby the workpiece in the form of a circular rod, as laid down in the rotating chuck deposited metal layers. In the resulting parts alloy composition varies smoothly from the center to the edges.
Details of such gradient alloys can be very useful where it is necessary to combine the design, very different in their physical properties, such as thermal expansion coefficient. For example, an alloy of scientists did mount carbon fiber panels (such panels, consisting of sheets of aluminum honeycomb with CFRP therebetween widely used in space). Fixing a hub, the inner part of which consists of steel and the outer Invar - alloy with a very low coefficient of thermal expansion. Steel thread on the inner side is in contact with stainless steel screw, and the outer side - with carbon. Smooth transition from steel to Invar avoids cracks and defects in sudden temperature changes, which are often found in space.
Unlike conventional printing parts of a single metal or alloy parts with a gradient almost impossible to make by any other means than 3D-printing. This is one of those cases where printing is not just saves time and material, and creates a new and unique features that do not allow other technologies. Although the possibility of gradient alloys scientists investigate more with the 70s, the real commercial use as long as it was hard to tell. 3D-printing makes this prospect much closer.
Source: habrahabr.ru/post/231677/

To dispensed into the print zone different metals, the print head had four nozzles, each of which was fed its powder form. Varying dosage of various metals with such heads can be accurate to about 1%. Besides conventional 3D-printing, in which the head is movable in all three axes, creating a product practically arbitrary shape, the method was tested radial press, whereby the workpiece in the form of a circular rod, as laid down in the rotating chuck deposited metal layers. In the resulting parts alloy composition varies smoothly from the center to the edges.
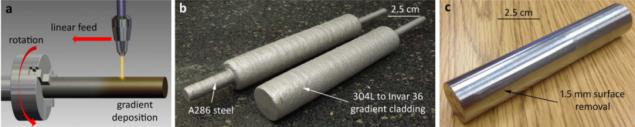
Details of such gradient alloys can be very useful where it is necessary to combine the design, very different in their physical properties, such as thermal expansion coefficient. For example, an alloy of scientists did mount carbon fiber panels (such panels, consisting of sheets of aluminum honeycomb with CFRP therebetween widely used in space). Fixing a hub, the inner part of which consists of steel and the outer Invar - alloy with a very low coefficient of thermal expansion. Steel thread on the inner side is in contact with stainless steel screw, and the outer side - with carbon. Smooth transition from steel to Invar avoids cracks and defects in sudden temperature changes, which are often found in space.
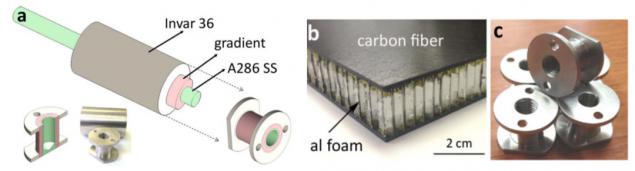
Unlike conventional printing parts of a single metal or alloy parts with a gradient almost impossible to make by any other means than 3D-printing. This is one of those cases where printing is not just saves time and material, and creates a new and unique features that do not allow other technologies. Although the possibility of gradient alloys scientists investigate more with the 70s, the real commercial use as long as it was hard to tell. 3D-printing makes this prospect much closer.
Source: habrahabr.ru/post/231677/