1861
Russian leather
Author: This process many thousands of years. Perhaps even more likely, the person first learned to him, and then got hold of the fire.
I'm not talking about the process of reproduction, I'm talking about tanning. In Russia operates Europe's biggest tannery - Ryazan, he is ZAO "Russian skin". Come visit.
First, some numbers and stories in order to understand, so to speak, the full depth of our depths. The plant will soon be a hundred years, it was opened one year before the October Revolution. He successfully processed skin of cattle in Soviet times, and that is very rare, has not stopped its activity in any 90 or later. In 1988, he was practically rebuilt by Italian comrades, and modernization of the equipment takes time. Now the area of production in Ryazan is 480,000 square meters, has more than two thousand people. In 2006, the Chinese opened a branch factory. It is much smaller and mainly specializes in shoe leather.
Almost half of the production of its products are exported to Italy, Portugal, Spain, France and Asia. I will not show the very first stage of production. It happens acceptance salted in barrels skins, their primary sorting and soaking in the soaking-ash drums. 21 branch receives raw skin with virtually all the major meat processing facilities in Russia. This is about 5200 tons per month.
After soaking (Soaking) nude skins fall on the first conveyor. There with them are not particularly ceremony and ship fearsome machines.
I understand in this unit is part of the water is removed. The output of every four workers inspect the skin and cut a clear marriage and the remains of tissue and fat.
In the early stages of the hardest work. The skins are very slippery, sharp knives and you have no idea what there is smell. During the day, handled 6,000 skins.
Next to skin comes one of the most critical processes. These drums tanning occurs. During this process, using special chemicals are derived from hides all microorganisms, natural processes are terminated. Those. from the living skin material is converted into a standard corresponding to the stringent requirements, prefabricated.
The skin at this stage is called wet-blue and after chemical treatment with chrome she really blue. The skin, tanned by the old recipes, using organic tanning agents, can also be distinguished by color. It is either white or yellow-brown.
Along with the wet-blue move into the finishing shop.
So, pulled out and dried wet-blue fall on the table to these women. They are responsible for sorting and rejection at this stage.
The material is in the process of doubling. With planing machine skin stratifies into two or even three layers. It turns the front side and splits.
From the front of the skin produce the highest quality, but also make the skin splits cheaper. Most chips are used for the preparation of adhesives and technical gelatin.
Some customers prefer not to deal with the primary treatment of the skin, and produce at the further stages independent processing and buying from the factory products under wet-blue. It is an international standard, so this decision is nothing strange.
Further falls in blue leather dyeing zhirovalnye drums.
They are exactly the same as tanning, only processes which occur in others. At this stage, the most important properties are given future skin softness, wear resistance, elasticity. Here happens painting. As you know, the final product options are vast. The plant produces products under the order, so that the fate of each piece of material is predetermined.
These drums are used by many generations of tanners. Traditionally made of hardwood.
If you look inside, in the dark, you can see perfectly polished wall studs and leather for additional mixing.
Treated and painted the skin called the crust. It may be of different colors, with different properties. Something I thought that at any other production I have never seen so many brunettes ...
The drying process may be different, but often begins with pressing. Remember the ancient barrel washing machines with rubber rollers for pressing? It is a larger version.
A piece of glamor for a change :)
This atmospheric drying. Krusty make a big circle on the ceiling shop, to survey the neighborhood, at the same time and dried.
And this is another kind of drying - frame. In this position, four workers take the frame, remove the dried and steal, and pull new. His replacement takes about three minutes.
Rama go around. Behind the wall is a dryer, where the drying takes place. As I understand it, this method is used for drying, and expensive leather furniture. By the way, there can be clearly seen that the standard size of the crust exactly half of the skins. Furniture leather often whole.
Paragraph another quality control. Although production and mechanized / automated by 90%, but the human experience can not be replaced. An experienced controller in seconds determines the density, thickness and quality of the skin. Plus laboratory and coloristic control sample specimens from each batch.
Transferred to a finishing plant №2. Here comes the final processing and finished products. Again, some customers buy their own crust and brought it to mind, the remaining crust is subjected to finishing operations.
If at the stage of crust options set, then more of them. I even have no idea about how many kinds of skin can be obtained on these lines. During finishing gloss set, complementary colors, embossing, texture, and other special effects. Here crust is processed by spraying. In the long assembly line piece of skin goes through several stages of soaking and drying.
And then another principle that resembles lamination or printing press. The skin goes through an extensive coloring, while a drying machine.
After all the twists and turns of the skin is virtually no texture. This machine consists of, roughly speaking, the iron and press.
On a hot plate coated volume pattern that is transferred under pressure to the skin.
This skin is likely to go on manufacturing overalls and shoes.
And then, finally, finished leather gets to the warehouse of the final product.
There is a final quality control, formed the party. The skin can not add an envelope, so she rolled up a few pieces.
Time passing all stages of production is highly dependent on the complexity of manufacture.
Production of furniture leather and runs parallel to the steps already practically repeats what he saw.
After drying of the skin receives a frame on kunturirovanie. Two women with pnevmonozhami very smartly cut edge skin. See what they do, I managed a third or fourth call.
So it is the final impregnation of any substance. Leather furniture should be thicker and have a very high strength and wear characteristics.
Well, the final quality control and sorting. By the way, if the plant has its own factory for production of leather furniture, so you can order a completely exclusive options.
Of course, it was impossible to leave without visiting the holy of holies - the lab. By the way, 500 thousand square meters is really a lot, workers move on bicycles.
The lab is not only produced quality control, and development of new processing technologies, test new chemical compounds. Just under exclusive orders small parties here are made of leather with a few recipes for processing.
In a small shop a laboratory can reproduce any stage of the process. The only thing that I have not found, so it is an embossing press.
There are also drums, but several times smaller.
Impregnation and paint developed immediately.
Especially for me was donated a large piece of skin for the selection of a new color. Typically, a piece of colored four times less. I was asked to mention it :)
Finally, I was taken to the factory showroom. Customer reveal his name. Several dozen types of leather with a huge number of options embossing, color and density. From the usual "leather" skin with natural texture, to something acidic, the touch and the cut is more reminiscent of linoleum, from a thick belt to the finest glove.
Since childhood, I was very interested in the question of whether it is possible in times of trouble to cook soup of shoes or a snack belt. Now I can say with confidence - you can, but pointless and dangerous for health. After soaking in chemistry or limestone, tanning chrome or tannin, the nutritional properties of the skin is rapidly approaching zero. And in general to talk about "the natural material" may be a stretch. So if you are thinking of a difficult campaign, please be things rawhide - they can have :)
Picture for animal lovers.
Source: zizis.livejournal.com
I'm not talking about the process of reproduction, I'm talking about tanning. In Russia operates Europe's biggest tannery - Ryazan, he is ZAO "Russian skin". Come visit.
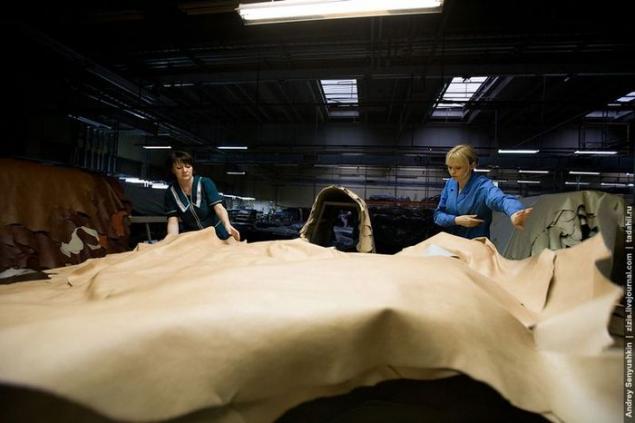
First, some numbers and stories in order to understand, so to speak, the full depth of our depths. The plant will soon be a hundred years, it was opened one year before the October Revolution. He successfully processed skin of cattle in Soviet times, and that is very rare, has not stopped its activity in any 90 or later. In 1988, he was practically rebuilt by Italian comrades, and modernization of the equipment takes time. Now the area of production in Ryazan is 480,000 square meters, has more than two thousand people. In 2006, the Chinese opened a branch factory. It is much smaller and mainly specializes in shoe leather.
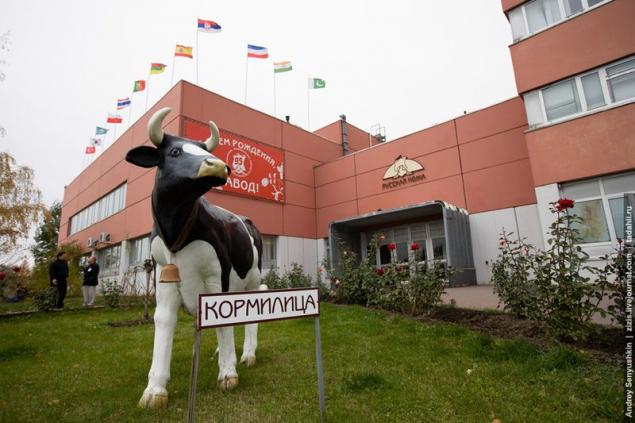
Almost half of the production of its products are exported to Italy, Portugal, Spain, France and Asia. I will not show the very first stage of production. It happens acceptance salted in barrels skins, their primary sorting and soaking in the soaking-ash drums. 21 branch receives raw skin with virtually all the major meat processing facilities in Russia. This is about 5200 tons per month.
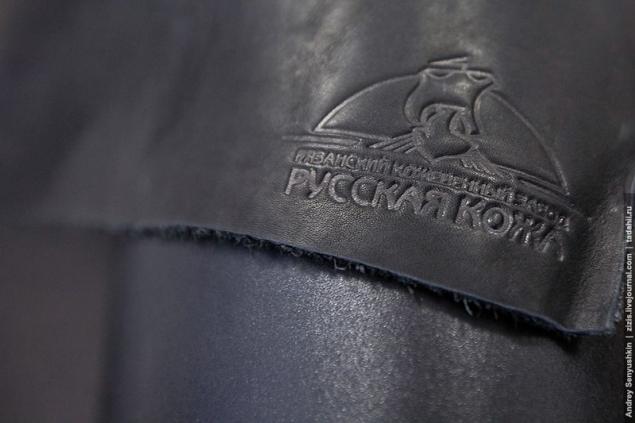
After soaking (Soaking) nude skins fall on the first conveyor. There with them are not particularly ceremony and ship fearsome machines.
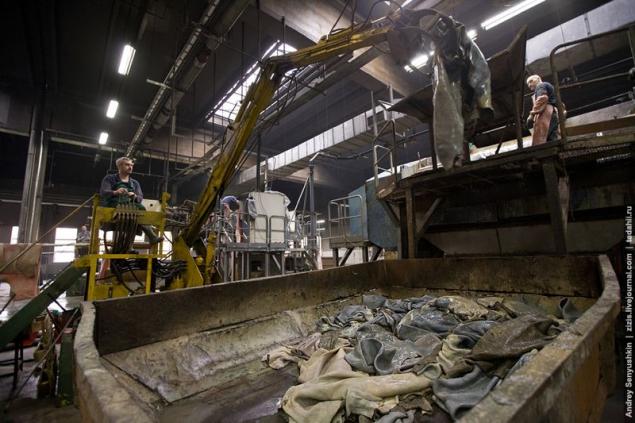
I understand in this unit is part of the water is removed. The output of every four workers inspect the skin and cut a clear marriage and the remains of tissue and fat.
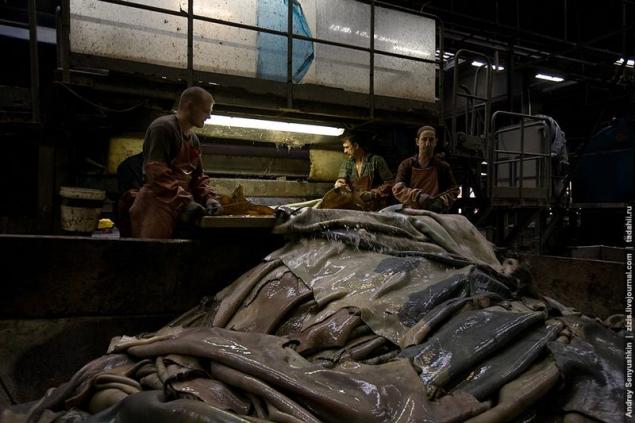
In the early stages of the hardest work. The skins are very slippery, sharp knives and you have no idea what there is smell. During the day, handled 6,000 skins.
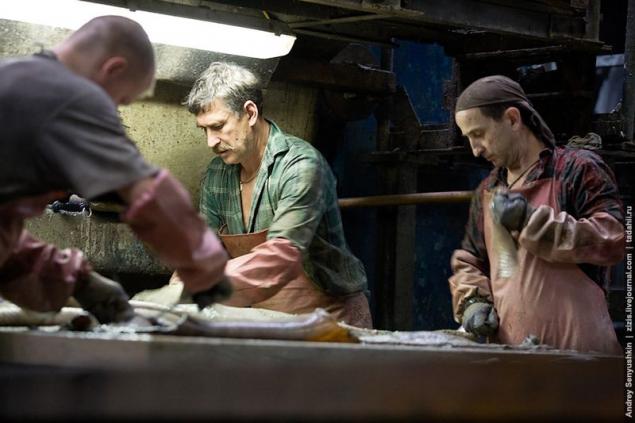
Next to skin comes one of the most critical processes. These drums tanning occurs. During this process, using special chemicals are derived from hides all microorganisms, natural processes are terminated. Those. from the living skin material is converted into a standard corresponding to the stringent requirements, prefabricated.
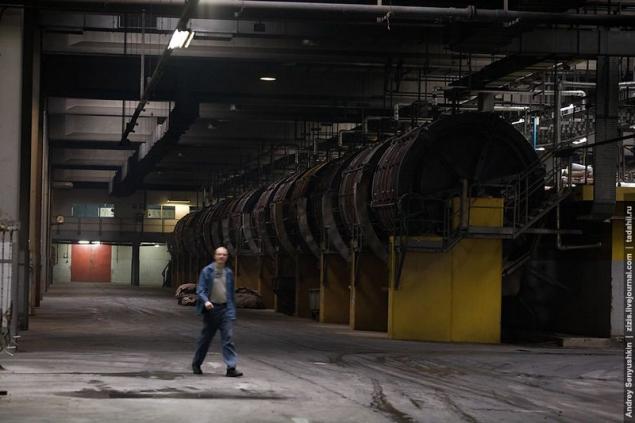
The skin at this stage is called wet-blue and after chemical treatment with chrome she really blue. The skin, tanned by the old recipes, using organic tanning agents, can also be distinguished by color. It is either white or yellow-brown.
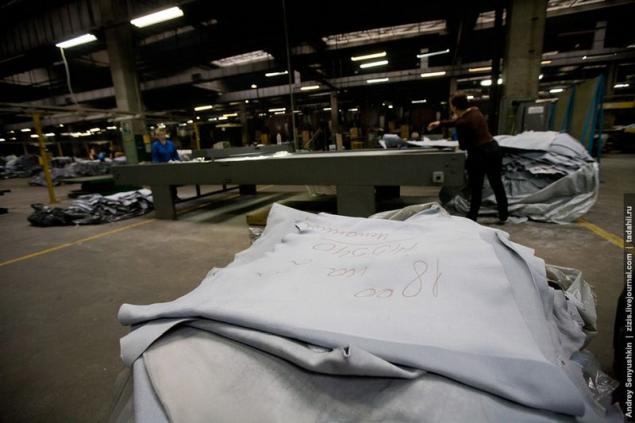
Along with the wet-blue move into the finishing shop.
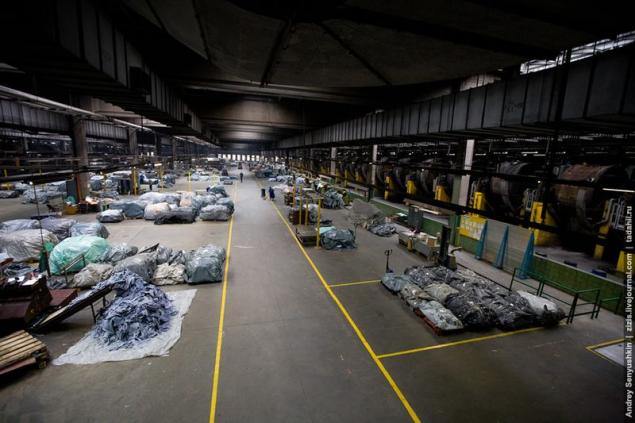
So, pulled out and dried wet-blue fall on the table to these women. They are responsible for sorting and rejection at this stage.
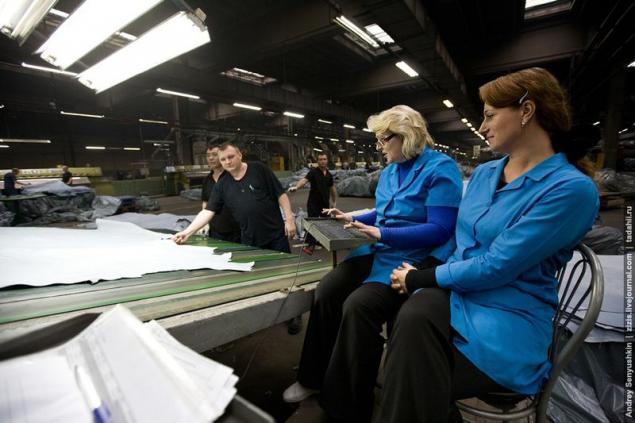
The material is in the process of doubling. With planing machine skin stratifies into two or even three layers. It turns the front side and splits.
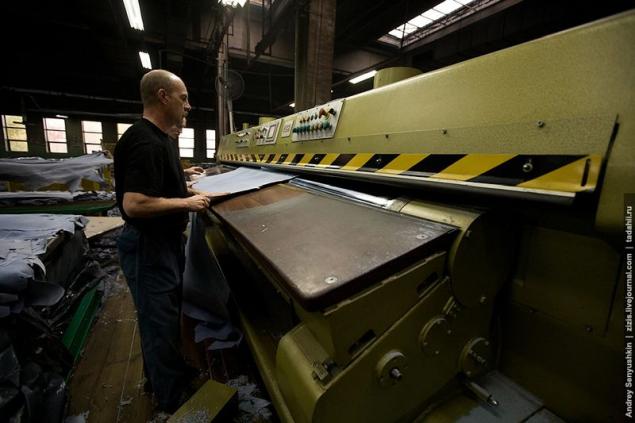
From the front of the skin produce the highest quality, but also make the skin splits cheaper. Most chips are used for the preparation of adhesives and technical gelatin.
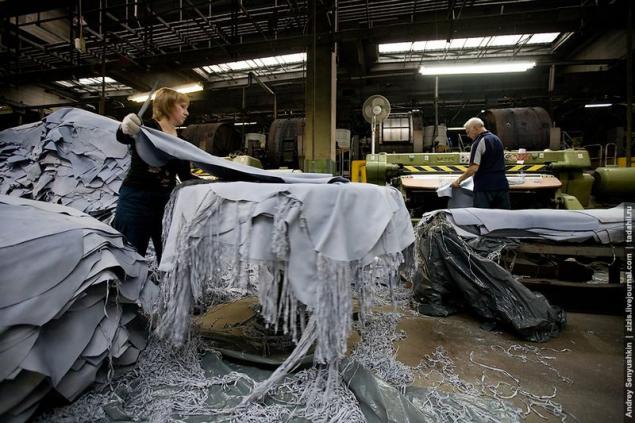
Some customers prefer not to deal with the primary treatment of the skin, and produce at the further stages independent processing and buying from the factory products under wet-blue. It is an international standard, so this decision is nothing strange.
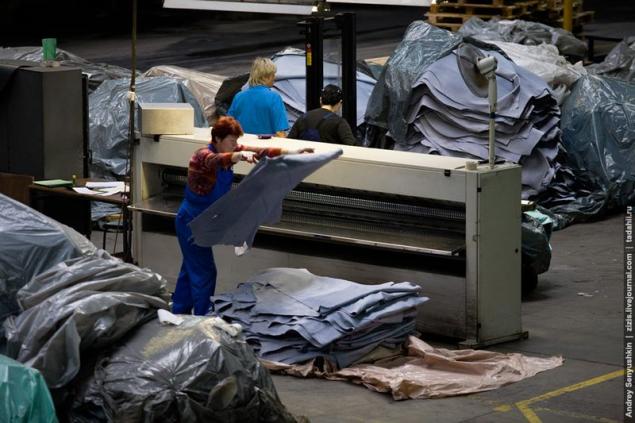
Further falls in blue leather dyeing zhirovalnye drums.
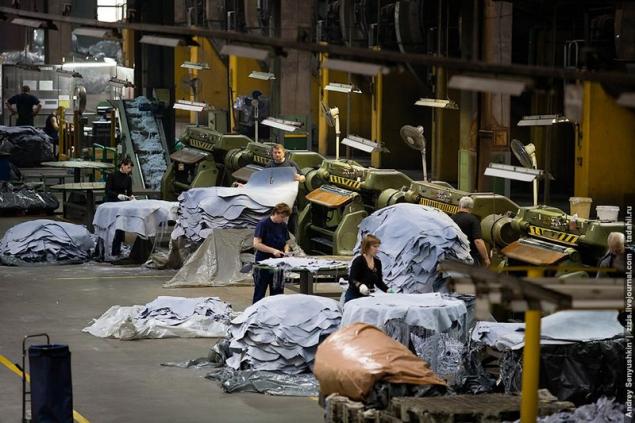
They are exactly the same as tanning, only processes which occur in others. At this stage, the most important properties are given future skin softness, wear resistance, elasticity. Here happens painting. As you know, the final product options are vast. The plant produces products under the order, so that the fate of each piece of material is predetermined.
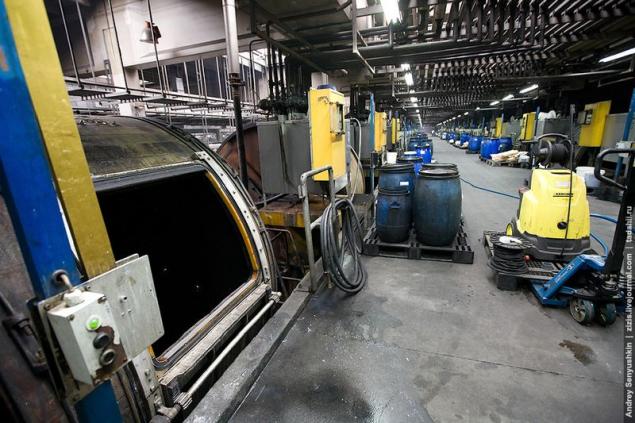
These drums are used by many generations of tanners. Traditionally made of hardwood.
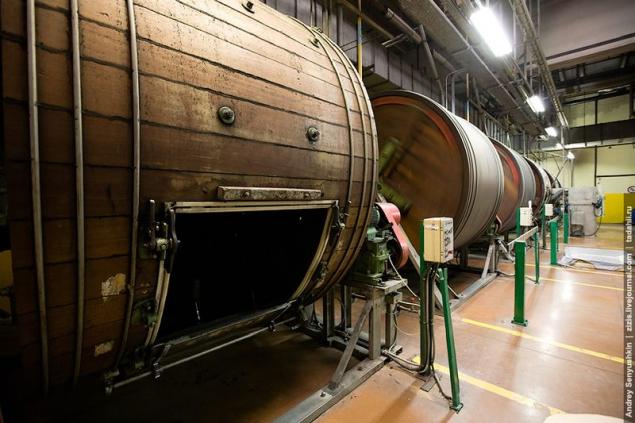
If you look inside, in the dark, you can see perfectly polished wall studs and leather for additional mixing.
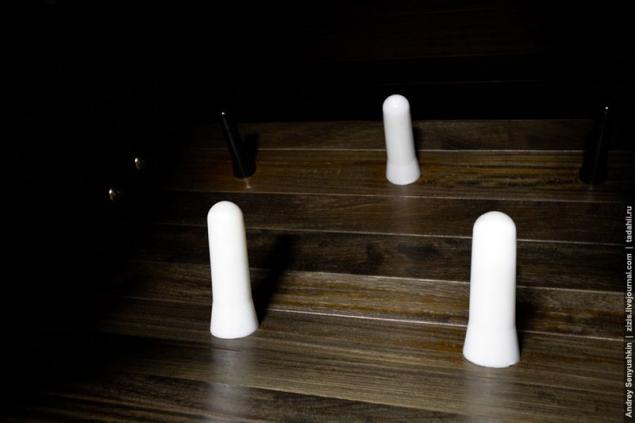
Treated and painted the skin called the crust. It may be of different colors, with different properties. Something I thought that at any other production I have never seen so many brunettes ...
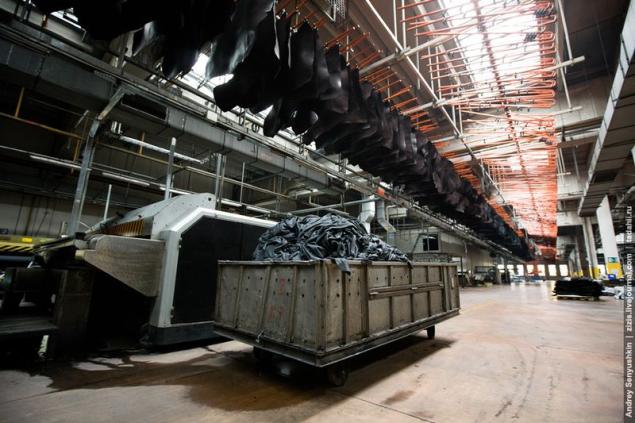
The drying process may be different, but often begins with pressing. Remember the ancient barrel washing machines with rubber rollers for pressing? It is a larger version.
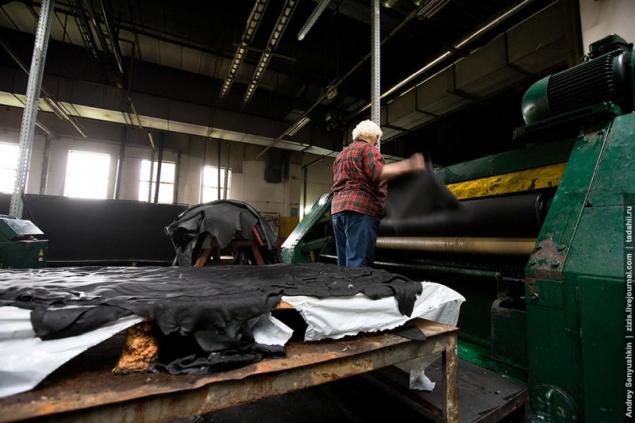
A piece of glamor for a change :)
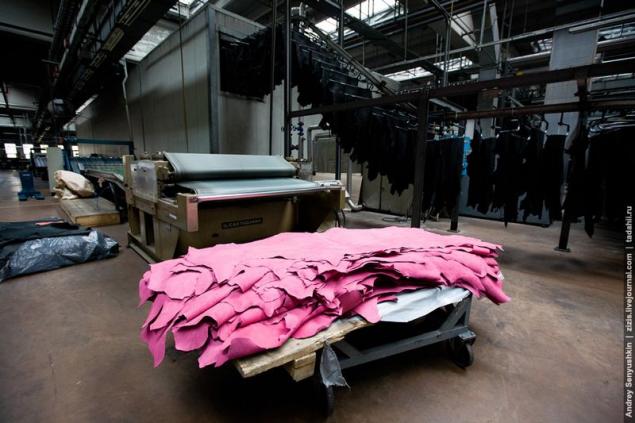
This atmospheric drying. Krusty make a big circle on the ceiling shop, to survey the neighborhood, at the same time and dried.
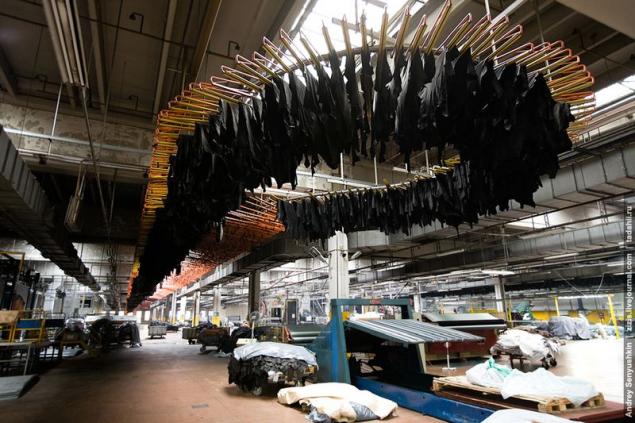
And this is another kind of drying - frame. In this position, four workers take the frame, remove the dried and steal, and pull new. His replacement takes about three minutes.
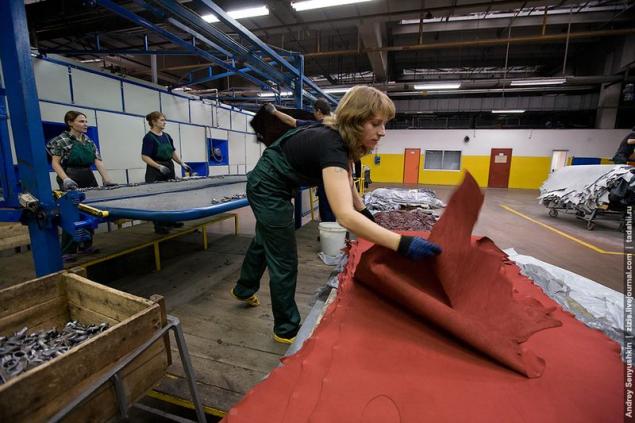
Rama go around. Behind the wall is a dryer, where the drying takes place. As I understand it, this method is used for drying, and expensive leather furniture. By the way, there can be clearly seen that the standard size of the crust exactly half of the skins. Furniture leather often whole.
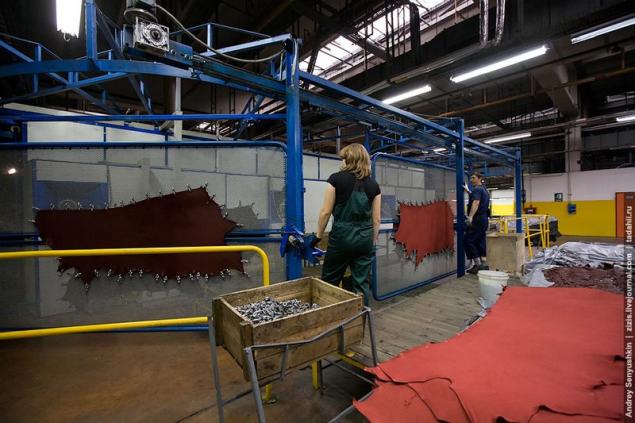
Paragraph another quality control. Although production and mechanized / automated by 90%, but the human experience can not be replaced. An experienced controller in seconds determines the density, thickness and quality of the skin. Plus laboratory and coloristic control sample specimens from each batch.
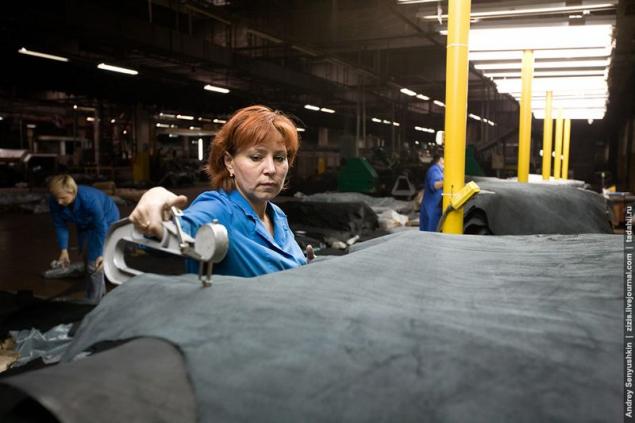
Transferred to a finishing plant №2. Here comes the final processing and finished products. Again, some customers buy their own crust and brought it to mind, the remaining crust is subjected to finishing operations.
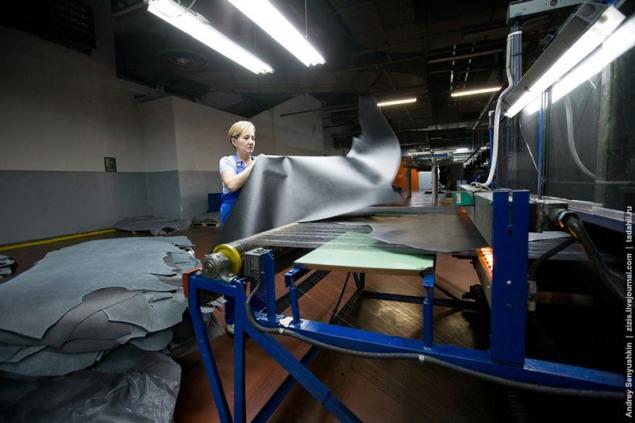
If at the stage of crust options set, then more of them. I even have no idea about how many kinds of skin can be obtained on these lines. During finishing gloss set, complementary colors, embossing, texture, and other special effects. Here crust is processed by spraying. In the long assembly line piece of skin goes through several stages of soaking and drying.
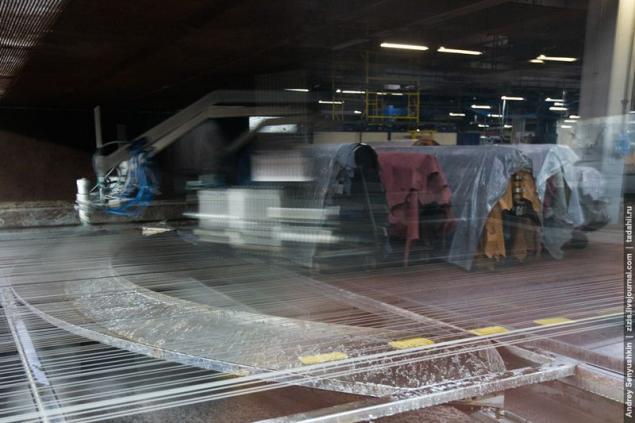
And then another principle that resembles lamination or printing press. The skin goes through an extensive coloring, while a drying machine.
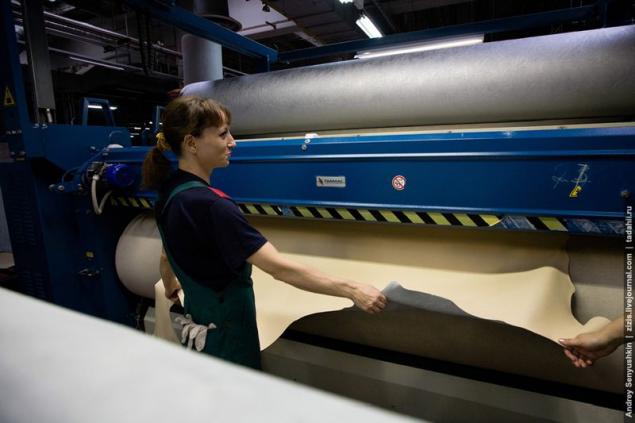
After all the twists and turns of the skin is virtually no texture. This machine consists of, roughly speaking, the iron and press.
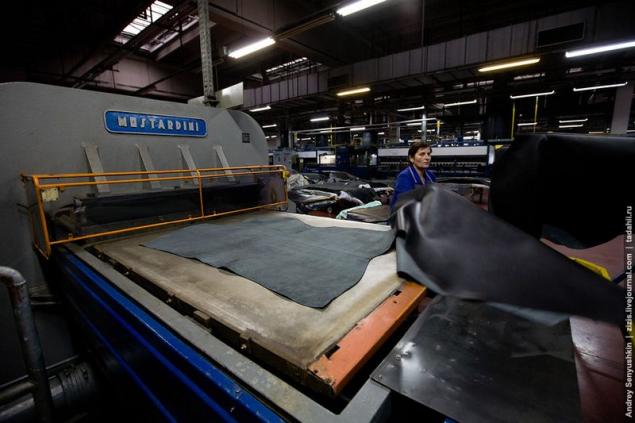
On a hot plate coated volume pattern that is transferred under pressure to the skin.
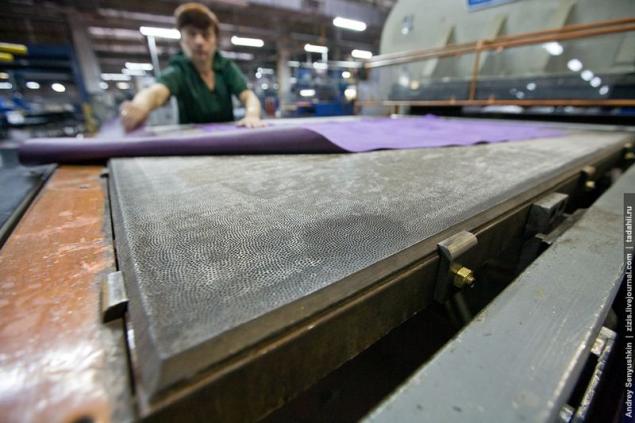
This skin is likely to go on manufacturing overalls and shoes.
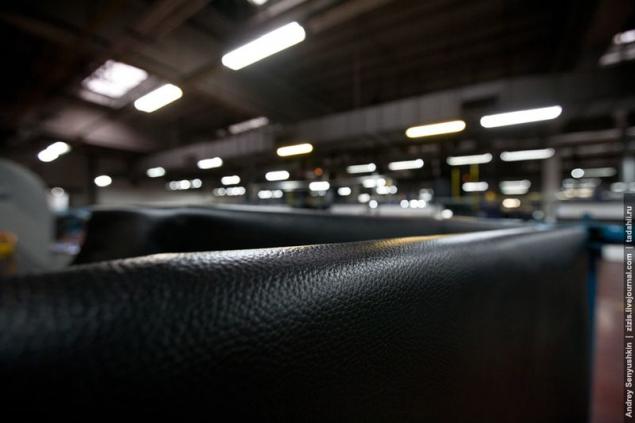
And then, finally, finished leather gets to the warehouse of the final product.
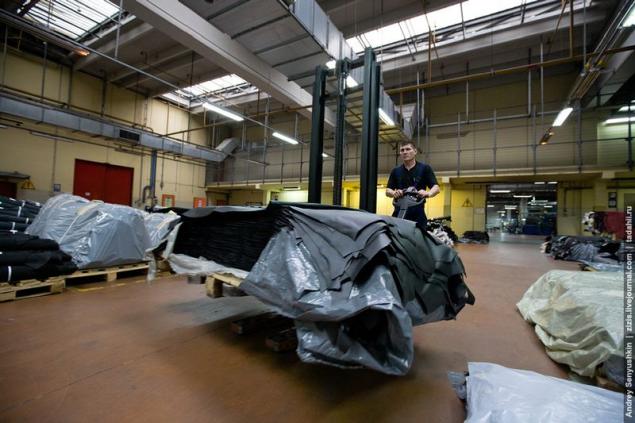
There is a final quality control, formed the party. The skin can not add an envelope, so she rolled up a few pieces.
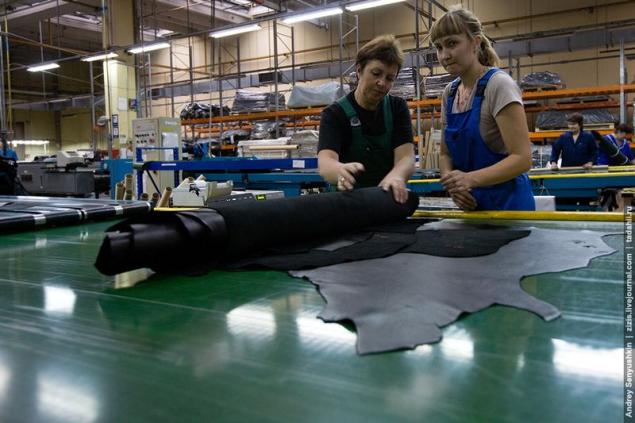
Time passing all stages of production is highly dependent on the complexity of manufacture.
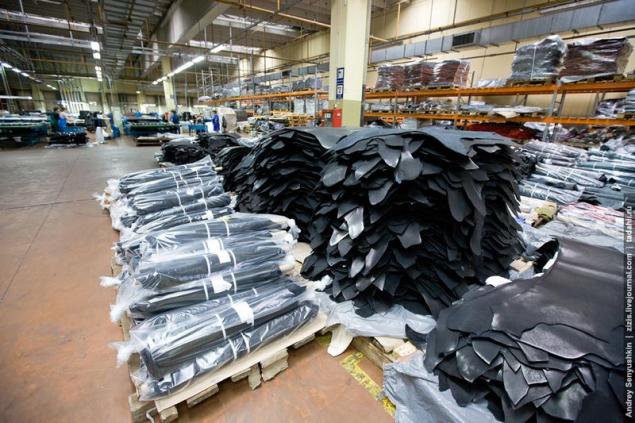
Production of furniture leather and runs parallel to the steps already practically repeats what he saw.
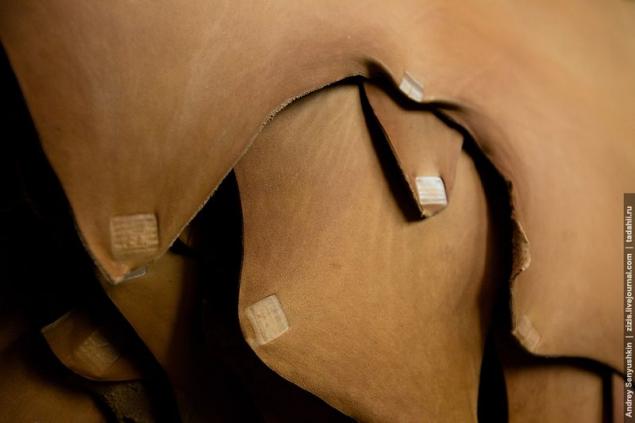
After drying of the skin receives a frame on kunturirovanie. Two women with pnevmonozhami very smartly cut edge skin. See what they do, I managed a third or fourth call.
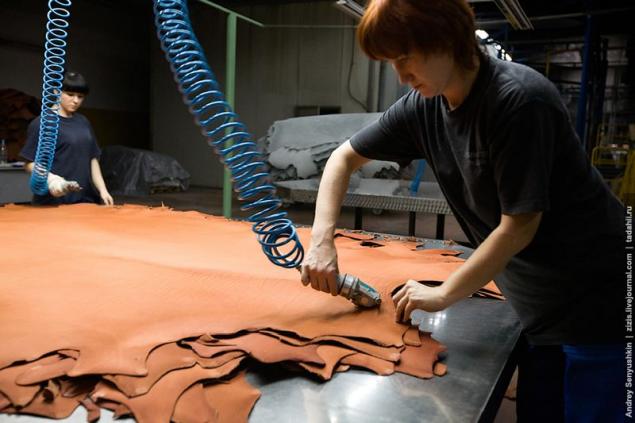
So it is the final impregnation of any substance. Leather furniture should be thicker and have a very high strength and wear characteristics.
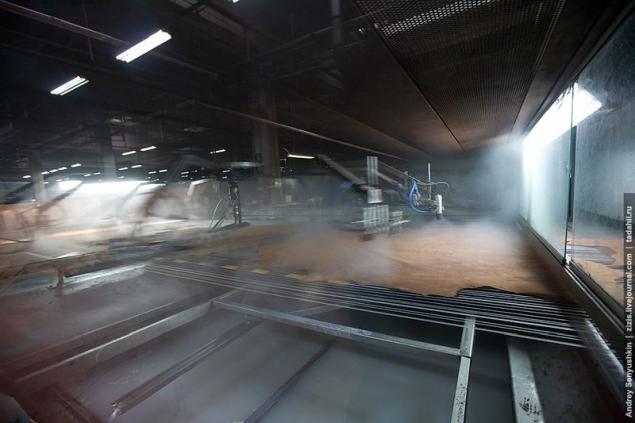
Well, the final quality control and sorting. By the way, if the plant has its own factory for production of leather furniture, so you can order a completely exclusive options.
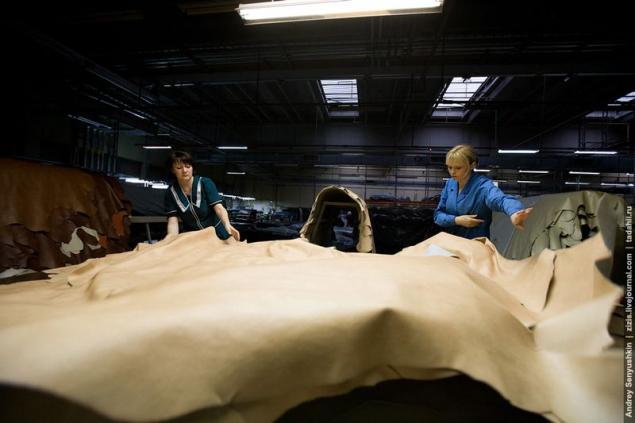
Of course, it was impossible to leave without visiting the holy of holies - the lab. By the way, 500 thousand square meters is really a lot, workers move on bicycles.
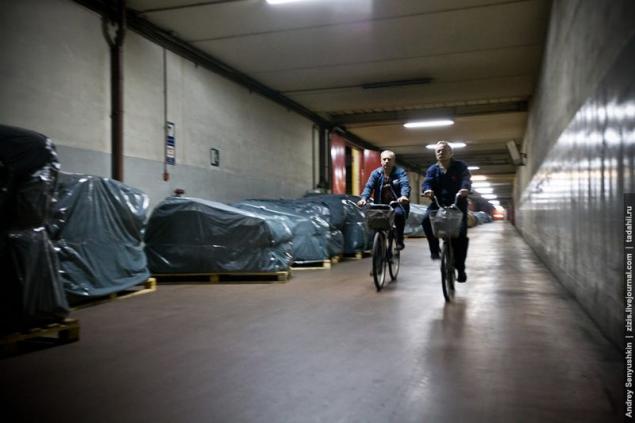
The lab is not only produced quality control, and development of new processing technologies, test new chemical compounds. Just under exclusive orders small parties here are made of leather with a few recipes for processing.
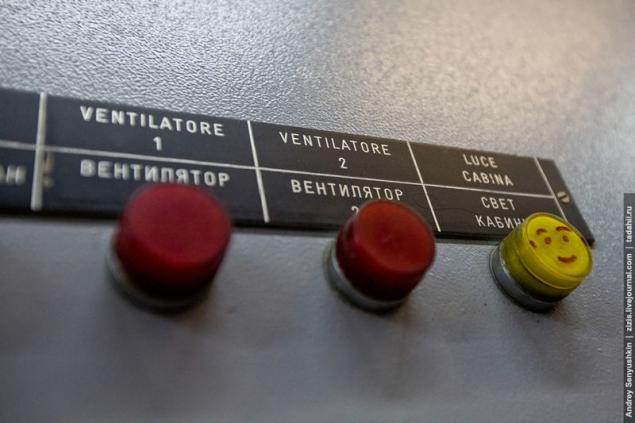
In a small shop a laboratory can reproduce any stage of the process. The only thing that I have not found, so it is an embossing press.
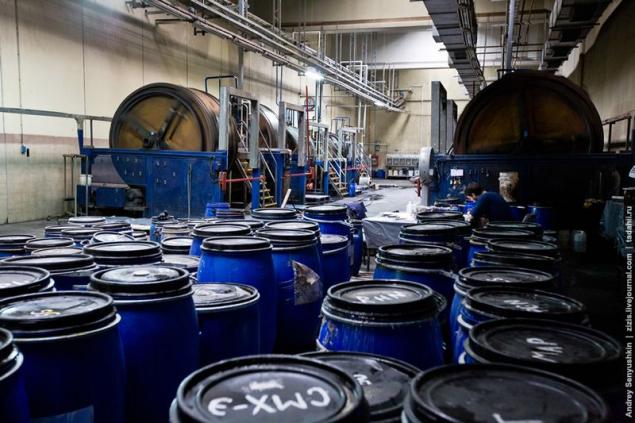
There are also drums, but several times smaller.
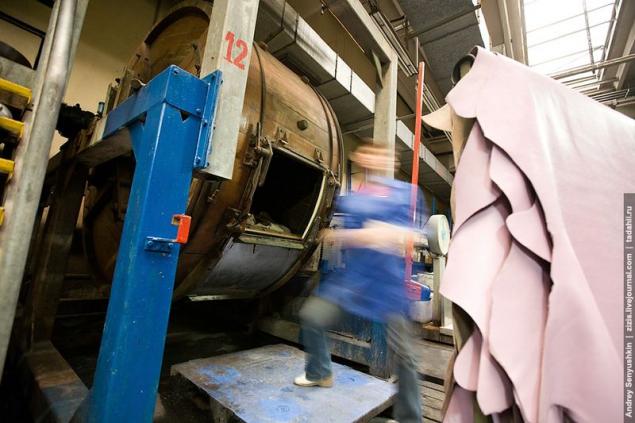
Impregnation and paint developed immediately.
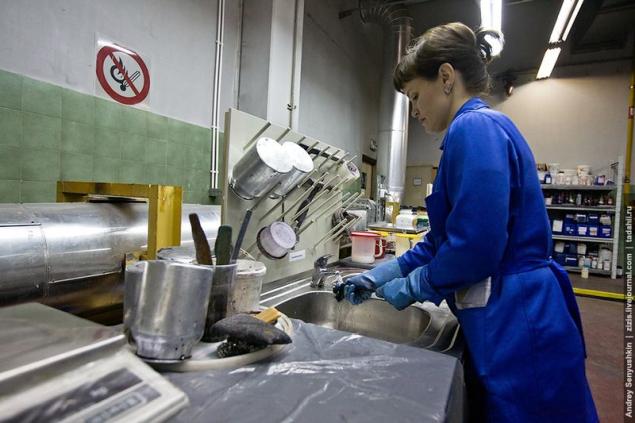
Especially for me was donated a large piece of skin for the selection of a new color. Typically, a piece of colored four times less. I was asked to mention it :)
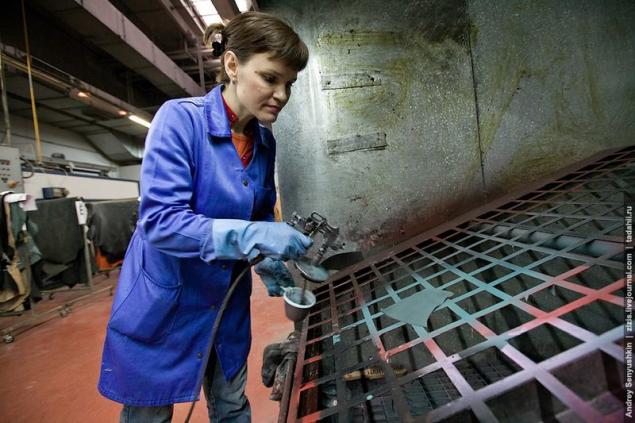
Finally, I was taken to the factory showroom. Customer reveal his name. Several dozen types of leather with a huge number of options embossing, color and density. From the usual "leather" skin with natural texture, to something acidic, the touch and the cut is more reminiscent of linoleum, from a thick belt to the finest glove.
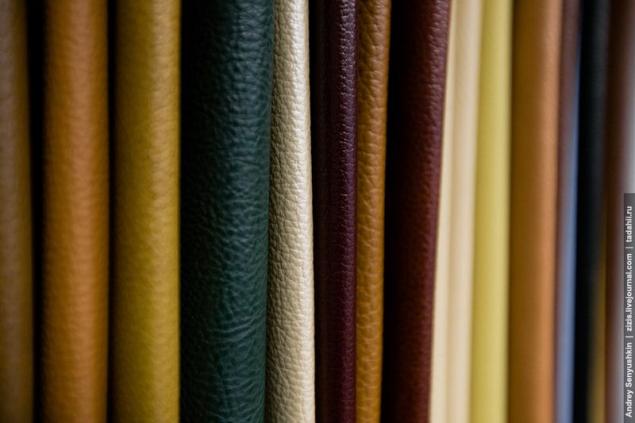
Since childhood, I was very interested in the question of whether it is possible in times of trouble to cook soup of shoes or a snack belt. Now I can say with confidence - you can, but pointless and dangerous for health. After soaking in chemistry or limestone, tanning chrome or tannin, the nutritional properties of the skin is rapidly approaching zero. And in general to talk about "the natural material" may be a stretch. So if you are thinking of a difficult campaign, please be things rawhide - they can have :)
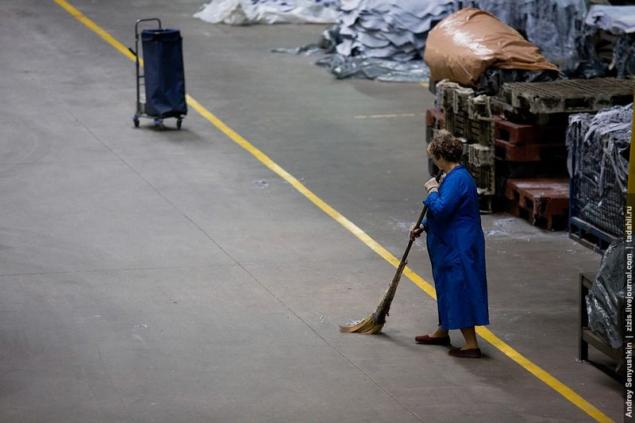
Picture for animal lovers.
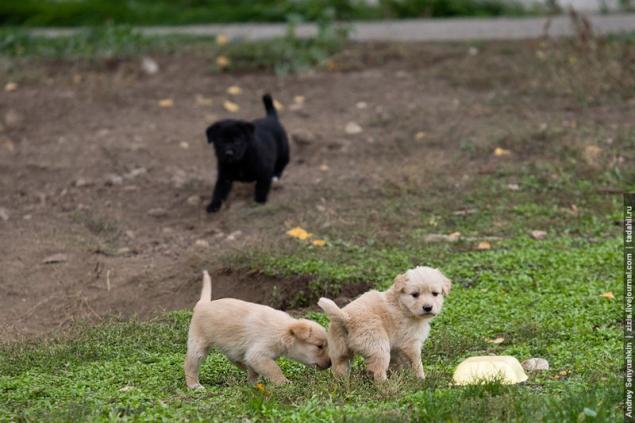
Source: zizis.livejournal.com