1392
How to build American roads?
Writes blogger engineering-ru:
Roads - an integral part of today's urban landscape. For someone roading - enjoying fast comfortable ride for someone the problem and many hours shaking with traffic jams on the narrow roads.
Today we will go to several construction sites in Texas and look at how to build a highway, why concrete pavement is 30 years without major repairs (And why, in fact, concrete?), A well as see why trucks from thirty six ton "tails" are not forced road.
Under the cut 40 photos
1.
2. Traditionally, we start with history. The first concrete road has been laid in the United States in 1930, in Indiana, and later in Illinois in 1940. In Texas, the first concrete highway appeared only in 1951 in the city of Fort Worth. Texas Department of Transportation (DOT) is very quick to recognize the correctness of the chosen path and began actively laying of concrete highway along and across the entire state of Texas, and today is the leader in the United States by the length of concrete roads, with 20,117 km of highway.
3. All US road can be divided into some large groups, some of which in turn consist of classes. Thus, starting from the most significant to less significant, roads are classified into the following groups: Interstate Highways (indicated by the letter I), US Highways (US), State Highways (in this case - TX), FM roads (FM, meaning Farm to Market ), Local Roads (this group includes other roads, such as Road (Rd), Avenue (Ave), Junction (Jct) and others).
4. The Government, represented by the US DOT establishes certain requirements for the construction of roads, and these requirements vary from class to class roads. I'll note that in contrast to the small transport issues, such as speed limits or route of road design standards can not be changed shtatovskih DOT, all states are subject to US DOT and construction standards.
5. Also note that in contrast to the design (which is uniform in all states, signs, signs, markings), construction technology a little different in different states, it is connected with seismic Some states, winter conditions, wetlands, etc. Shtatovskih DOT conduct their research on technologies of laying roads and amend building codes DOT. In general, the chain of command codes and shtatovkih to US DOT DOT is very confusing for the layman must then write a separate post.
6. I do not think that ever come back to the DOT and the more so, I will write a review of road construction, because immediately after graduation at the university, I spun the fate of the building in a completely different jungle. But once I myself wrote a thesis on transport issues for the construction of bridges TX DOT, as it turned out, the old not wriggle.
7. So, before you start construction, DOT assigns a public hearing (usually in the courthouse or at the office). Upon hearing can come any resident of the area, where it will build or repair roads and express their opinions.
8. The project can be modified to collect opinions. For example, people can look at the plan and say that you need to close the output that's the road to the highway, security, or install anti-noise wall along the road to neighboring cafe was quiet.
9. Any reasonable offer will be investigated and if the people are right, the amendment will be included in the project. The hearing is appointed usually early in the project when a draft is made, in order then to remodel less in the case of total amendments. After the project with the local lads utryasut residents to DOT given the green light to work.
10. All highway, indexed by I, and US made of concrete (with very few exceptions). This is due to the fact that it is on these roads is transit traffic, and the largest flow of both vehicles and cargo. You what! I road ah-some-there of asphalt! Reared some readers. Yes, the roads are often covered with asphalt - and so, it is a fake, under the asphalt - concrete. Just after the deterioration of the concrete, it is covered with asphalt to repair. This trick is to prolong the life of the road and pulling the cap. repair, because shift concrete problematic and more expensive than throw top layer of asphalt.
11. The choice of concrete was made in connection with several recent features - its strength, durability, ruggedness to load and preponderance of trucks. Of the minuses concrete pavement - its problematic installation and repair. If the paver road ready in 8 hours for the traffic, the road to open the concrete is required several months of work, but the result justified.
12. Thus, having received the green light for work, DOT first thing begins to think about how close the road without creating traffic jams. To do this, made a temporary band somewhere on the side of the road (usually makeshift concocting asphalt) or redesigns road to the imposition by the wayside. But in any case, DOT can not block the path of more than 30% bandwidth.
13. The most common DOT cunning, and repairing or building a section of the strip, first make one side of the road, shifting all the strips in the opposite direction, and then let flow on the road, taking the middle road and the road, and starts messing around with another old road.
14. All repairs are always identified areas for drivers marks, chips, and information boards where the builders write quick messages on the current state of the road and the planned closure of some bands in the future. On a high-speed roads current area fenced off curbs, because of traffic on the road continues to move at a speed of 100 km / h.
15. Also note that the builders did not forget about counting, she performed as a temporary "pipok" glued to the roadbed, such button clearly visible at night (often in repair areas is not light, because the pillars are not yet installed) as well as a felt wheel at running, giving the driver know that he gape.
16. By the way, the penalties in the areas of construction always doubled for all types of violations, especially speeding fiercely punished because Sometimes builders are working without safety curbs. The police, in turn, loves to watch offenders in such areas.
17. After all fenced and prepared for work will begin immediately the construction process.
18. The first step is to shovel about a meter of rocks usually breed is not shipped away because it can be used for any bulk or refining area. If there is a repair, they begin to shoot the old paint.
19. Then fit cushion for the road, usually gravel, sand and clay, all carefully compacted after laying each layer, then there is nothing for the earth to spread in different directions. Just built all communications and collectors.
20. Each laid layer watered, and then calcium chloride - or rather 35% solution of CaCl2 or a mortar, and then run with bulldozers "plugs", which plow laid layer, after which it again tamped. What for? The fact that the pillow is not as if ramming in its natural form, it is water (especially in the sand and clay), and when the water evaporates, the pillow gives way to reduce the percentage of subsidence, poured lime. Due to the chemical reaction of lime holding a water without letting it evaporate and leave the pad, ie restrains a constant percentage of water in the bed without letting it sink. Studies show that health indicators of a cushion of 80% better compared to just rammed a pillow.
21. After the airbag is stacked, a double layer of asphalt is laid, this relatively thin layer, the thickness of each layer is typically 5-7 cm.
22. What concrete is laid under the asphalt? There are several reasons. First concrete fragile to failures, and in the case of land subsidence cracks appear immediately, but as I mentioned above, to repair concrete is not so simple. The cause of the drawdown of the earth - it is water. When placing a layer of dense asphalt concrete, preparing a smooth surface and removed any possible drawdown since asphalt tightly compacted and takes any small holes and cracks in the ground, and secondly it serves as waterproofing for water, not allowing it to get under concrete by thermal seams of concrete joints.
23. Let me remind you that the percentage of water being laid in a bed, will vary very little throughout the life of the road because of the lime. Thus, the road surface is not prone to subsidence, and if the drawdown happens (sometimes gives up the ground under the pillow), it turns smooth monotonic pit at which a pleasure to drive, and that does not cause cracks in the concrete, thanks to flexible asphalt.
24. After all these problems finally begins installation of reinforcement for the concrete canvas. Typically, a standard steel reinforcement diameter of 16 mm (413 MPa). After collecting the valve on the ground, it is raised on plastic or metal base. The ideal position of the valve - between 1/3 and 1/2 the thickness of the tie from the upper edge, in other words - a little above the middle of the screed.
25. The reasons for this are two: if you put fitting too close to the surface - fittings can rust from lack of material from the top, if put in too deep - steel will protect concrete from cracks in the top layer of concrete.
26. Steel reinforcement comes to the construction site on the rods 18 meters, at the junction fitting fits overlap, which is calculated by engineers. Throughout the history of the building, the engineers "brought" technology overlap, which is the removal of the valve overlap throughout the width of the roadway in one place. Today, the most commonly used chess move that is perfectly visible in this photo.
27. Reinforcement for concrete is used in load balancing and prevent occurrence of cracks in the coating. The percentage of steel in the cross section (perpendicular to the direction of travel) is typically 0.60% in the longitudinal (in the direction of movement of cars) - 0.85%.
28. Most of the cracks in the coating occurs at a distance of 1-3 meters, the road cross section (perpendicular to the movement of vehicles), as cars forced wheel cover while moving. Where concrete tension stress exceeds the allowable design load - crack appears. Concrete is very misbehaves in tension, and steel - very well, so together they compensate for each other's shortcomings.
29. By the way, for a long time found a linear ratio of the number and position of cracks in the concrete to the steel volume, located in the screed. Thus, it was proved that the reduction in contact area with steel and concrete, there is an increase of the distance between the cracks.
30. Then paver starts to fill a piece of road. In the process of laying the builders are actively ram concrete vibrators to expel as much air from the cover, the air reduces the strength of concrete. For once handler should fill the plot of a thermal weld seam to the other, the whole piece of road to be monolithic and concrete without joints. To a mixture of used concrete type III, since particles of concrete are smaller in comparison, for example, the type I, but you must not forget that the use of smaller particles, increases the heat transfer in the solidification of the concrete, which brings its own problems in the aging process of the concrete. Temperature environmental factor greatly influences the formation of cracks in the coating.
31. In hot climates (Texas, Florida), usually try to lay concrete at night because mixture loses less moisture. Recommended temperature range laying concrete from 10 to 25 C degrees. Otherwise watering system builders use concrete to avoid cracking during hardening of the concrete. But we must not forget that the addition of water reduces the percentage strength of the concrete, so used for watering small number of its technologies and tricks - mostly concrete Kuta cellophane.
32. Another factor that strongly influences the concrete cover and its durability - it is the type of gravel, for example, river rock or gravel quarry have different indicators of thermal expansion, strength and flexibility. Thus, various rubble is one cause of cracking in the case of neglect of its properties. A detailed study of various types of rubble was carried out in the 1960s.
33. When filling each section, made of concrete cylinders of 10 (diameter) x 20 (H) cm or 15h30 cm, which leaves near the flooded portion after 3 days they will be taken to the lab and broken, then will be calculated the strength of the poured concrete. This is done in order to ensure that the poured concrete meets all the requirements. This is done precisely on-site operation, the cylinders are in the same conditions as the concrete. If you fill cylinders at the plant reinforced concrete where cement mixers are very often obtained inflated figures. If the concrete does not pass the test - coating have to dismantle and perezalit.
34. Typically the thickness of the screed mezhshtatovkisih highway - 30 cm, smaller highway - 20 cm. In practice, this thickness of the concrete, laid on an asphalt pad provides excellent resistance to load and does not require a second steel mesh. When the thickness of the concrete - cracks because Concrete does not have enough steel for load distribution, with decreasing thickness - concrete can not withstand the load of cars.
35. After penetration, paver usually draws a rough surface, which helps run the water when it rains, as well as increases the coefficient of friction of the wheels of cars and the road surface. Sometimes roughness just do not, and cut after using a special machine. Usually this happens on solid bridges.
36. Just after pouring on the road do not forget to sign when the segment has been filled in, then it is useful in the repair order, as well as to know when you can open the way for the transit of construction machinery in the process of work. Concrete should be based on a minimum of 7 days without stress, after seven days on the road, you can travel light construction equipment, but we must not forget that the full strength of the concrete will gain only 28 days, and if for some reason on the cover gets heavy machinery, the structure concrete can be completely damaged. Therefore, if you need somewhere to move the road a heavy crane - under a stele mats or concrete poured a thick layer of sand.
37. After 28 days, the road is completely ready to work. The service life of the road without major repairs - 25 years. In the cities of Houston and Dallas have a stretch of highway, flooded in 1960, and are in perfect condition until now. These areas are used for research and observation. Scientific papers simmer two largest and most prestigious universities in Texas - in Austin (capital of Texas) and in Houston.
38. Today, the US is a relatively large experimental areas of concrete pavement since Transport Department sees concrete way of the future. These segments are located in all four climatic zones in the country and have different design. By 2001, from a few hundred flooded areas during the period from 1961 to 2001 left 89 sections of the monitored.
39. On the basis of experiments conducted in 1999 and 2001 on the basis of areas in age from 25 to 40 years, there were several conclusions:
- Depending on the design and materials, concrete cover capable of withstanding loads without cracking over 34 years (compared to an average of 8 years, asphaltic concrete);
- After 34 years for the next 5 years, only 16 pieces fell into disrepair and were to be completely replaced;
- Within 20 years, motorists have complained about the deterioration of the ride comfort, but in some areas, "surrendered" supports ground, forming small ravines flowing without causing cracks in the top layer covering the roadway;
- By 2012, 89 pilot sites, 34 are active (17 are in Texas). Their average age today - 31 year. The remaining sections were pereulozheny due to the current expansion of roads, and scientific works to date rudder were successfully completed.
40. Experience in laying concrete roads actively adopt the US Asia and beyond. Laying of concrete highways actively China and Japan as well as Australia and some European countries, using the accumulated experience of the American road builders. In the United States, as much as possible, trying to build a new states only road made of concrete, reducing the costs of maintaining roads during their operation.
Source:
Roads - an integral part of today's urban landscape. For someone roading - enjoying fast comfortable ride for someone the problem and many hours shaking with traffic jams on the narrow roads.
Today we will go to several construction sites in Texas and look at how to build a highway, why concrete pavement is 30 years without major repairs (And why, in fact, concrete?), A well as see why trucks from thirty six ton "tails" are not forced road.
Under the cut 40 photos
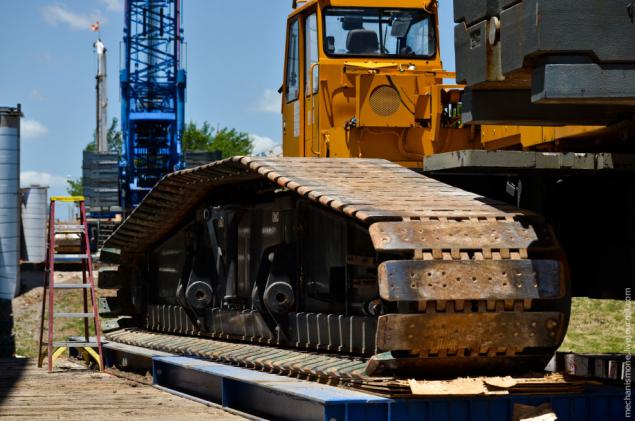
1.
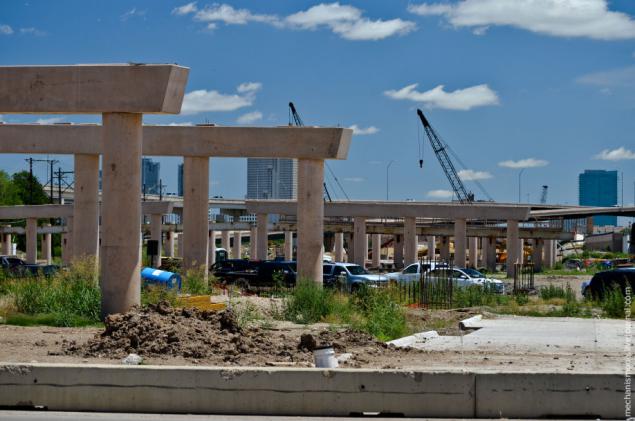
2. Traditionally, we start with history. The first concrete road has been laid in the United States in 1930, in Indiana, and later in Illinois in 1940. In Texas, the first concrete highway appeared only in 1951 in the city of Fort Worth. Texas Department of Transportation (DOT) is very quick to recognize the correctness of the chosen path and began actively laying of concrete highway along and across the entire state of Texas, and today is the leader in the United States by the length of concrete roads, with 20,117 km of highway.
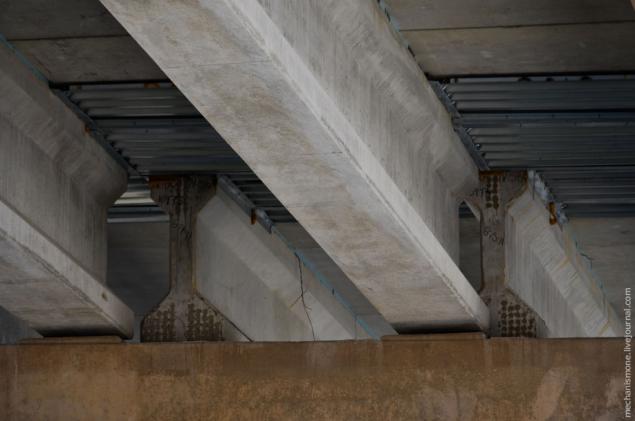
3. All US road can be divided into some large groups, some of which in turn consist of classes. Thus, starting from the most significant to less significant, roads are classified into the following groups: Interstate Highways (indicated by the letter I), US Highways (US), State Highways (in this case - TX), FM roads (FM, meaning Farm to Market ), Local Roads (this group includes other roads, such as Road (Rd), Avenue (Ave), Junction (Jct) and others).
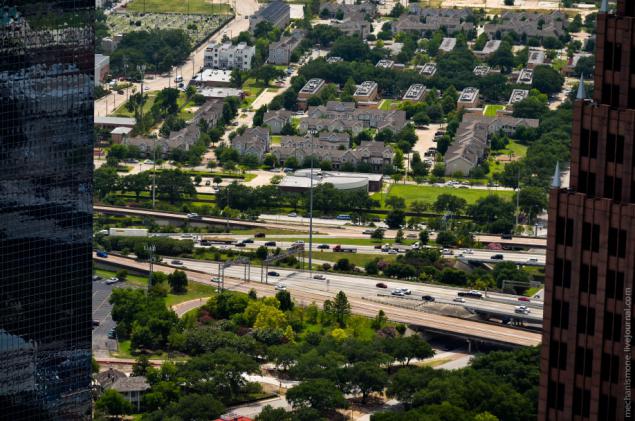
4. The Government, represented by the US DOT establishes certain requirements for the construction of roads, and these requirements vary from class to class roads. I'll note that in contrast to the small transport issues, such as speed limits or route of road design standards can not be changed shtatovskih DOT, all states are subject to US DOT and construction standards.
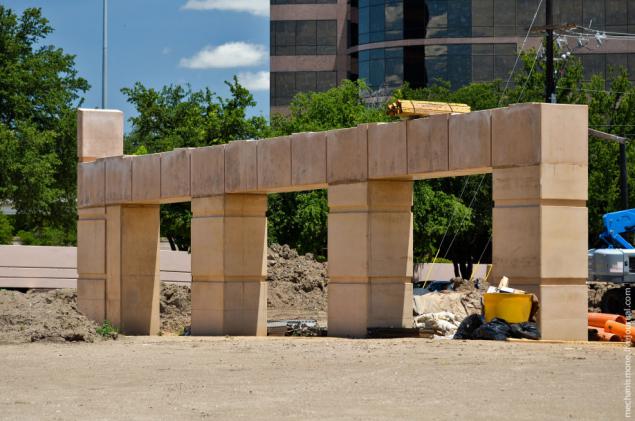
5. Also note that in contrast to the design (which is uniform in all states, signs, signs, markings), construction technology a little different in different states, it is connected with seismic Some states, winter conditions, wetlands, etc. Shtatovskih DOT conduct their research on technologies of laying roads and amend building codes DOT. In general, the chain of command codes and shtatovkih to US DOT DOT is very confusing for the layman must then write a separate post.
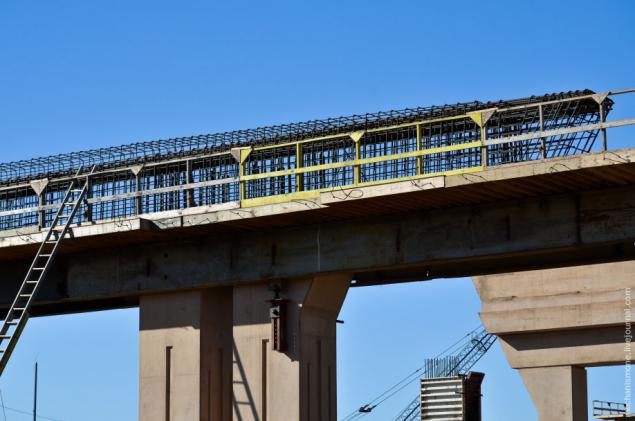
6. I do not think that ever come back to the DOT and the more so, I will write a review of road construction, because immediately after graduation at the university, I spun the fate of the building in a completely different jungle. But once I myself wrote a thesis on transport issues for the construction of bridges TX DOT, as it turned out, the old not wriggle.
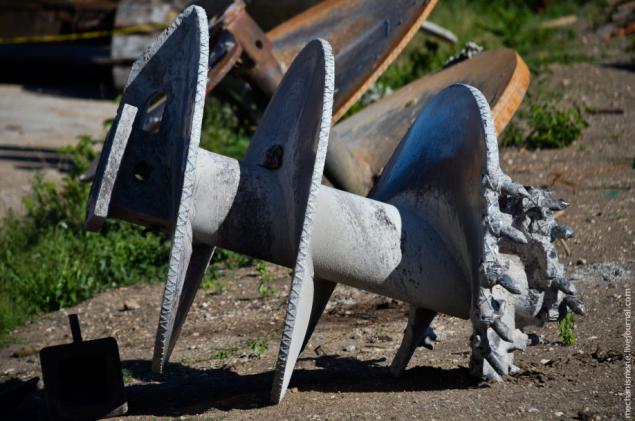
7. So, before you start construction, DOT assigns a public hearing (usually in the courthouse or at the office). Upon hearing can come any resident of the area, where it will build or repair roads and express their opinions.
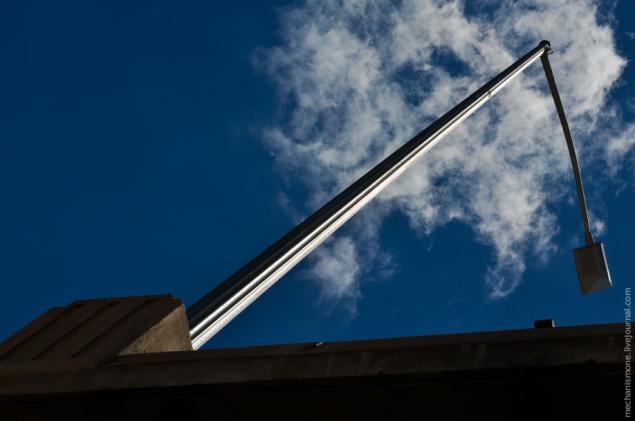
8. The project can be modified to collect opinions. For example, people can look at the plan and say that you need to close the output that's the road to the highway, security, or install anti-noise wall along the road to neighboring cafe was quiet.

9. Any reasonable offer will be investigated and if the people are right, the amendment will be included in the project. The hearing is appointed usually early in the project when a draft is made, in order then to remodel less in the case of total amendments. After the project with the local lads utryasut residents to DOT given the green light to work.
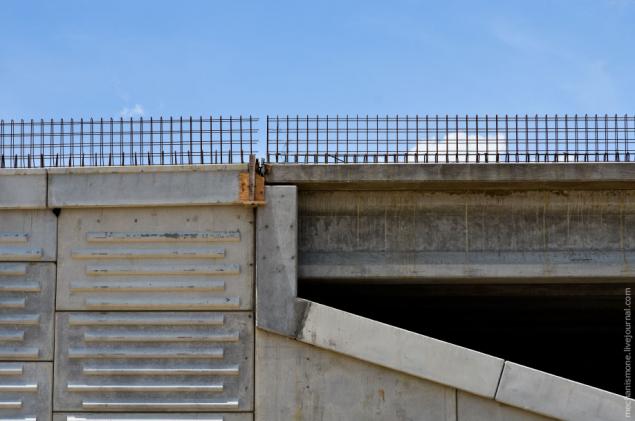
10. All highway, indexed by I, and US made of concrete (with very few exceptions). This is due to the fact that it is on these roads is transit traffic, and the largest flow of both vehicles and cargo. You what! I road ah-some-there of asphalt! Reared some readers. Yes, the roads are often covered with asphalt - and so, it is a fake, under the asphalt - concrete. Just after the deterioration of the concrete, it is covered with asphalt to repair. This trick is to prolong the life of the road and pulling the cap. repair, because shift concrete problematic and more expensive than throw top layer of asphalt.
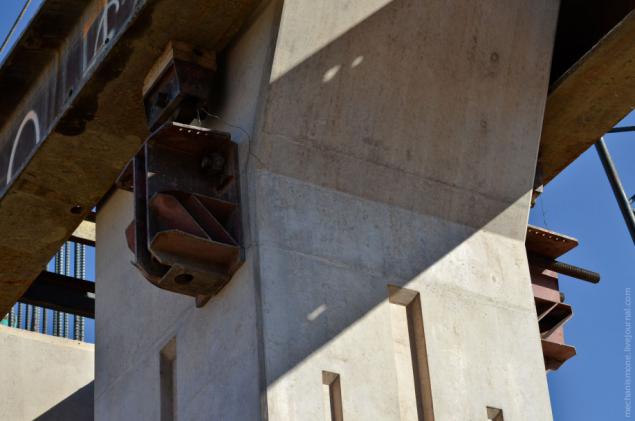
11. The choice of concrete was made in connection with several recent features - its strength, durability, ruggedness to load and preponderance of trucks. Of the minuses concrete pavement - its problematic installation and repair. If the paver road ready in 8 hours for the traffic, the road to open the concrete is required several months of work, but the result justified.
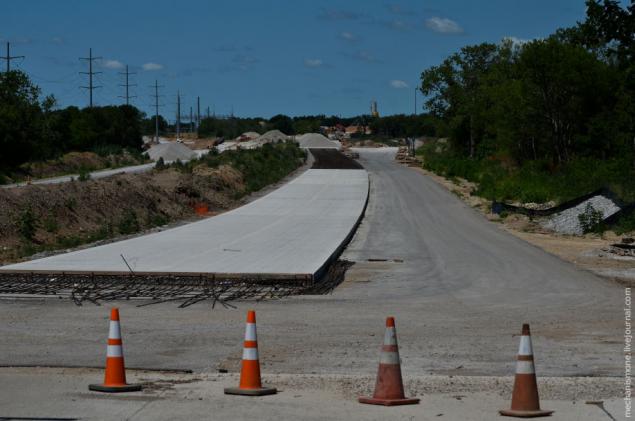
12. Thus, having received the green light for work, DOT first thing begins to think about how close the road without creating traffic jams. To do this, made a temporary band somewhere on the side of the road (usually makeshift concocting asphalt) or redesigns road to the imposition by the wayside. But in any case, DOT can not block the path of more than 30% bandwidth.
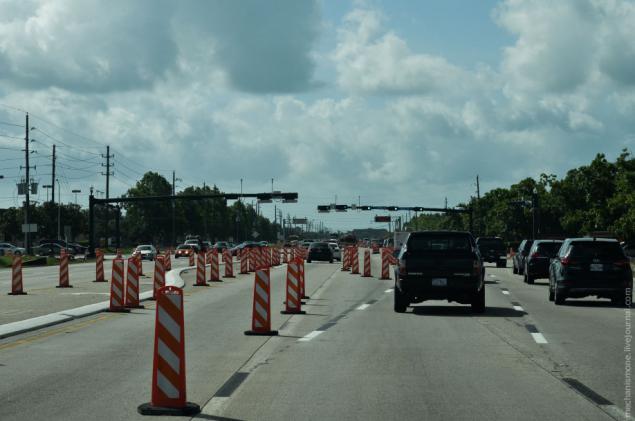
13. The most common DOT cunning, and repairing or building a section of the strip, first make one side of the road, shifting all the strips in the opposite direction, and then let flow on the road, taking the middle road and the road, and starts messing around with another old road.
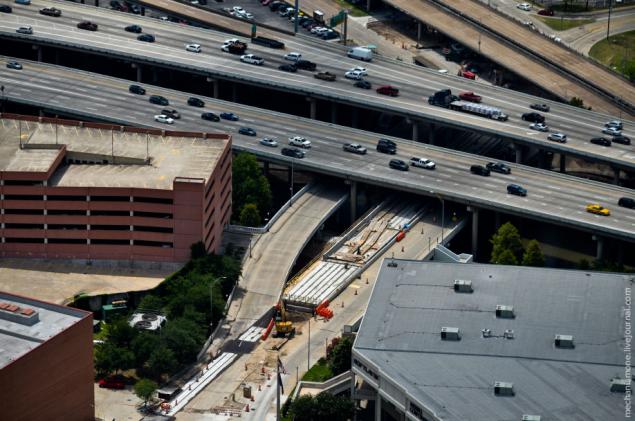
14. All repairs are always identified areas for drivers marks, chips, and information boards where the builders write quick messages on the current state of the road and the planned closure of some bands in the future. On a high-speed roads current area fenced off curbs, because of traffic on the road continues to move at a speed of 100 km / h.
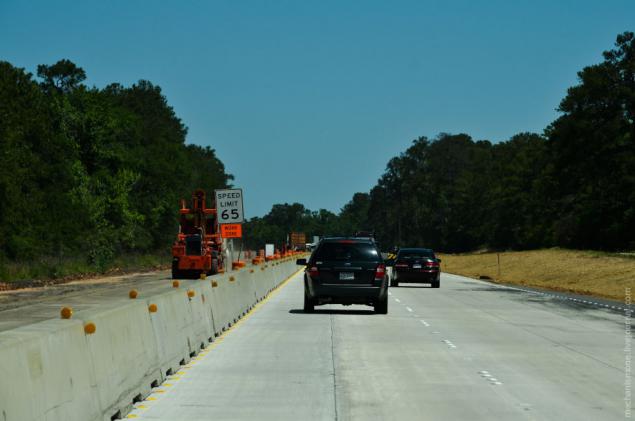
15. Also note that the builders did not forget about counting, she performed as a temporary "pipok" glued to the roadbed, such button clearly visible at night (often in repair areas is not light, because the pillars are not yet installed) as well as a felt wheel at running, giving the driver know that he gape.
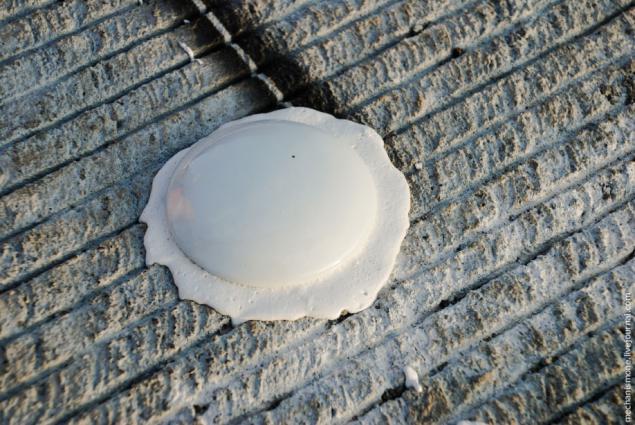
16. By the way, the penalties in the areas of construction always doubled for all types of violations, especially speeding fiercely punished because Sometimes builders are working without safety curbs. The police, in turn, loves to watch offenders in such areas.
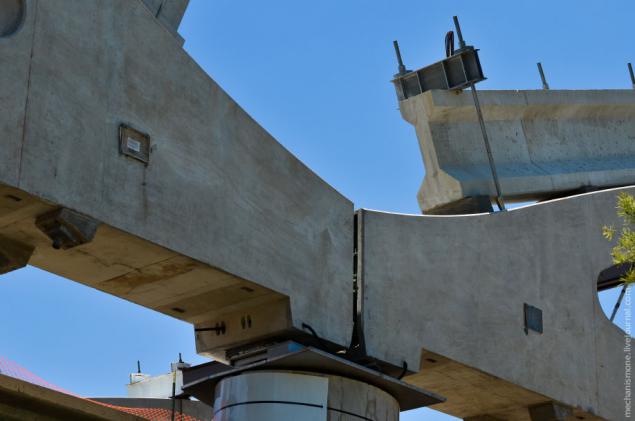
17. After all fenced and prepared for work will begin immediately the construction process.
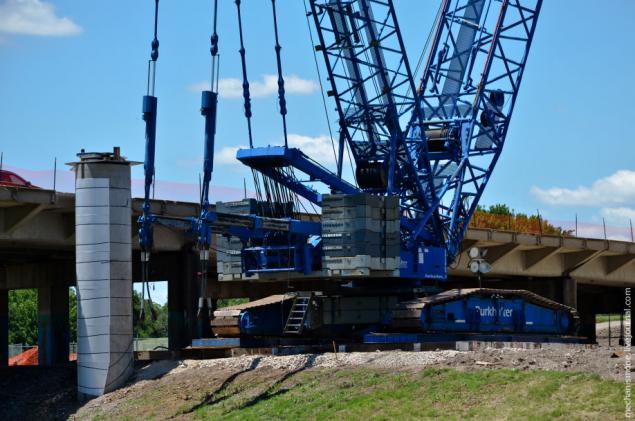
18. The first step is to shovel about a meter of rocks usually breed is not shipped away because it can be used for any bulk or refining area. If there is a repair, they begin to shoot the old paint.
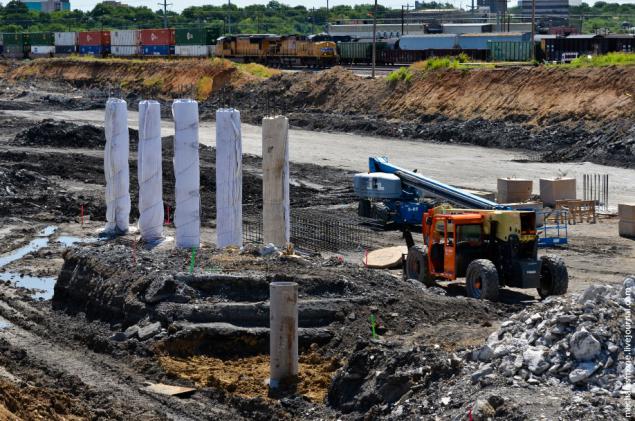
19. Then fit cushion for the road, usually gravel, sand and clay, all carefully compacted after laying each layer, then there is nothing for the earth to spread in different directions. Just built all communications and collectors.
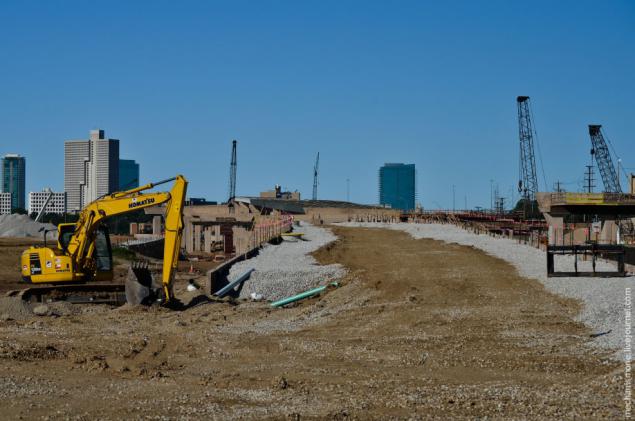
20. Each laid layer watered, and then calcium chloride - or rather 35% solution of CaCl2 or a mortar, and then run with bulldozers "plugs", which plow laid layer, after which it again tamped. What for? The fact that the pillow is not as if ramming in its natural form, it is water (especially in the sand and clay), and when the water evaporates, the pillow gives way to reduce the percentage of subsidence, poured lime. Due to the chemical reaction of lime holding a water without letting it evaporate and leave the pad, ie restrains a constant percentage of water in the bed without letting it sink. Studies show that health indicators of a cushion of 80% better compared to just rammed a pillow.
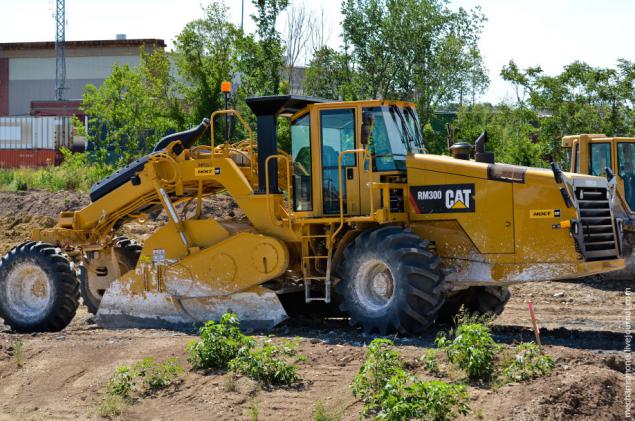
21. After the airbag is stacked, a double layer of asphalt is laid, this relatively thin layer, the thickness of each layer is typically 5-7 cm.
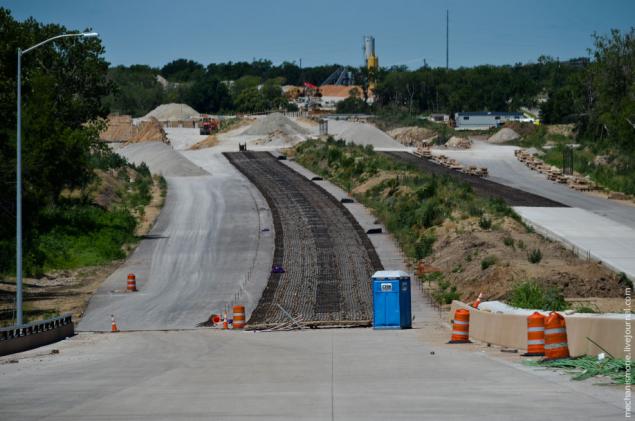
22. What concrete is laid under the asphalt? There are several reasons. First concrete fragile to failures, and in the case of land subsidence cracks appear immediately, but as I mentioned above, to repair concrete is not so simple. The cause of the drawdown of the earth - it is water. When placing a layer of dense asphalt concrete, preparing a smooth surface and removed any possible drawdown since asphalt tightly compacted and takes any small holes and cracks in the ground, and secondly it serves as waterproofing for water, not allowing it to get under concrete by thermal seams of concrete joints.
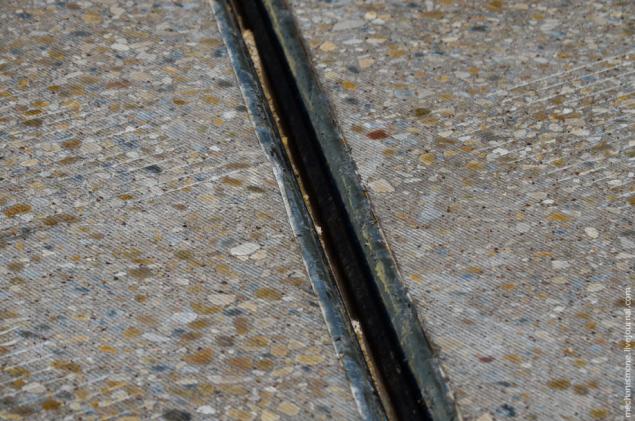
23. Let me remind you that the percentage of water being laid in a bed, will vary very little throughout the life of the road because of the lime. Thus, the road surface is not prone to subsidence, and if the drawdown happens (sometimes gives up the ground under the pillow), it turns smooth monotonic pit at which a pleasure to drive, and that does not cause cracks in the concrete, thanks to flexible asphalt.
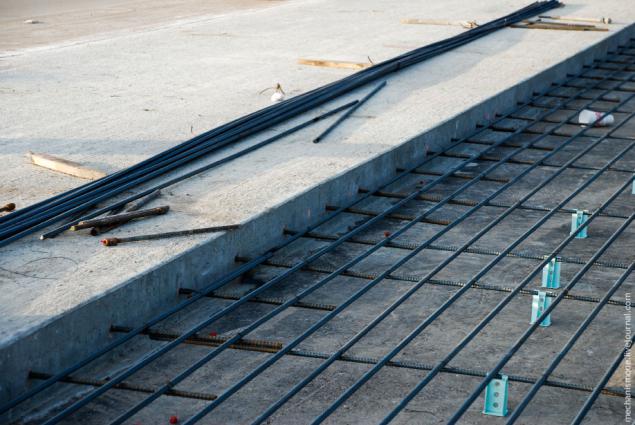
24. After all these problems finally begins installation of reinforcement for the concrete canvas. Typically, a standard steel reinforcement diameter of 16 mm (413 MPa). After collecting the valve on the ground, it is raised on plastic or metal base. The ideal position of the valve - between 1/3 and 1/2 the thickness of the tie from the upper edge, in other words - a little above the middle of the screed.
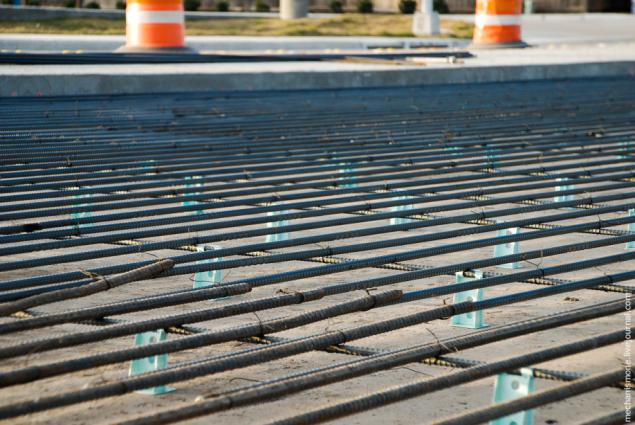
25. The reasons for this are two: if you put fitting too close to the surface - fittings can rust from lack of material from the top, if put in too deep - steel will protect concrete from cracks in the top layer of concrete.
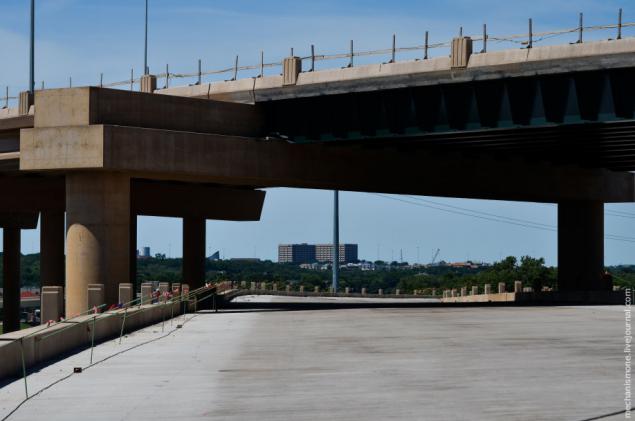
26. Steel reinforcement comes to the construction site on the rods 18 meters, at the junction fitting fits overlap, which is calculated by engineers. Throughout the history of the building, the engineers "brought" technology overlap, which is the removal of the valve overlap throughout the width of the roadway in one place. Today, the most commonly used chess move that is perfectly visible in this photo.
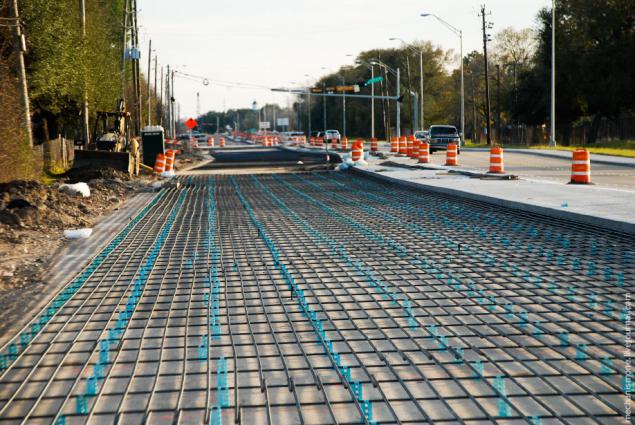
27. Reinforcement for concrete is used in load balancing and prevent occurrence of cracks in the coating. The percentage of steel in the cross section (perpendicular to the direction of travel) is typically 0.60% in the longitudinal (in the direction of movement of cars) - 0.85%.
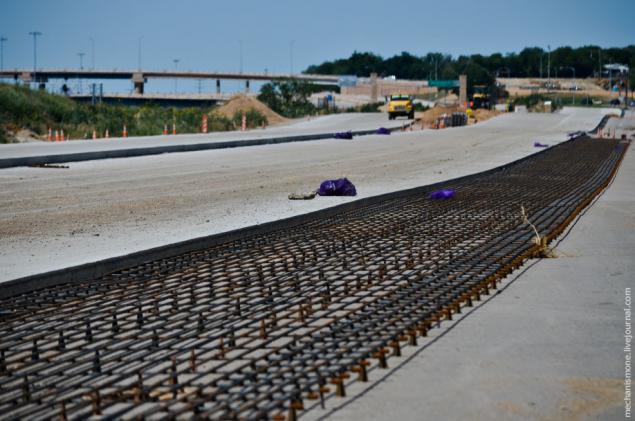
28. Most of the cracks in the coating occurs at a distance of 1-3 meters, the road cross section (perpendicular to the movement of vehicles), as cars forced wheel cover while moving. Where concrete tension stress exceeds the allowable design load - crack appears. Concrete is very misbehaves in tension, and steel - very well, so together they compensate for each other's shortcomings.
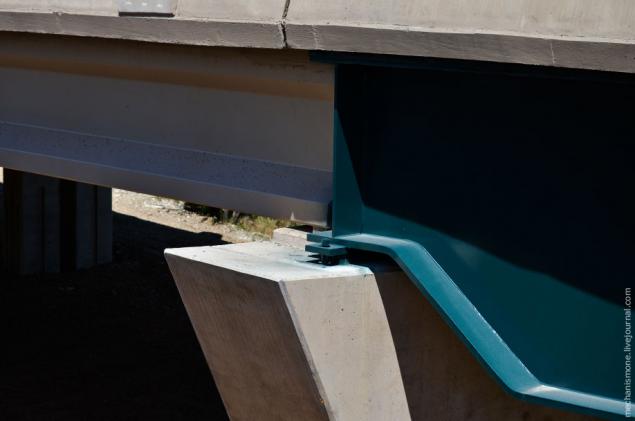
29. By the way, for a long time found a linear ratio of the number and position of cracks in the concrete to the steel volume, located in the screed. Thus, it was proved that the reduction in contact area with steel and concrete, there is an increase of the distance between the cracks.
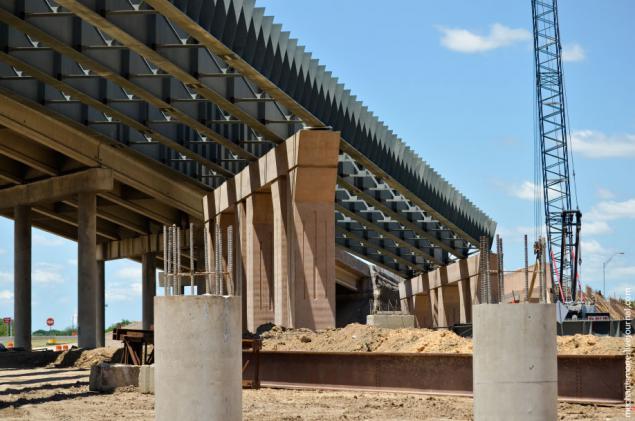
30. Then paver starts to fill a piece of road. In the process of laying the builders are actively ram concrete vibrators to expel as much air from the cover, the air reduces the strength of concrete. For once handler should fill the plot of a thermal weld seam to the other, the whole piece of road to be monolithic and concrete without joints. To a mixture of used concrete type III, since particles of concrete are smaller in comparison, for example, the type I, but you must not forget that the use of smaller particles, increases the heat transfer in the solidification of the concrete, which brings its own problems in the aging process of the concrete. Temperature environmental factor greatly influences the formation of cracks in the coating.
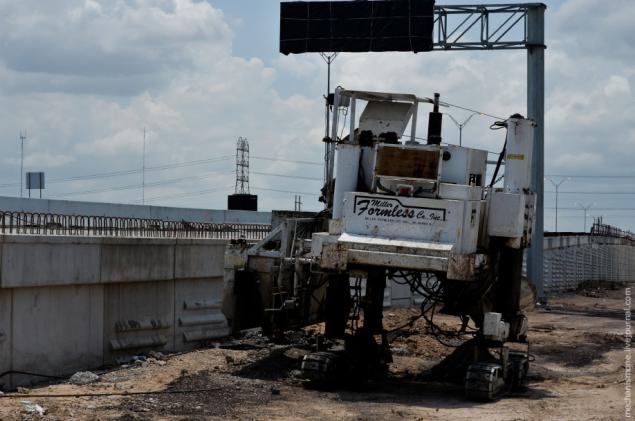
31. In hot climates (Texas, Florida), usually try to lay concrete at night because mixture loses less moisture. Recommended temperature range laying concrete from 10 to 25 C degrees. Otherwise watering system builders use concrete to avoid cracking during hardening of the concrete. But we must not forget that the addition of water reduces the percentage strength of the concrete, so used for watering small number of its technologies and tricks - mostly concrete Kuta cellophane.
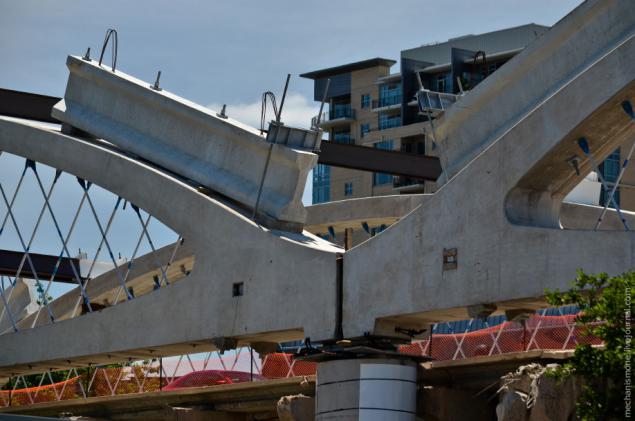
32. Another factor that strongly influences the concrete cover and its durability - it is the type of gravel, for example, river rock or gravel quarry have different indicators of thermal expansion, strength and flexibility. Thus, various rubble is one cause of cracking in the case of neglect of its properties. A detailed study of various types of rubble was carried out in the 1960s.
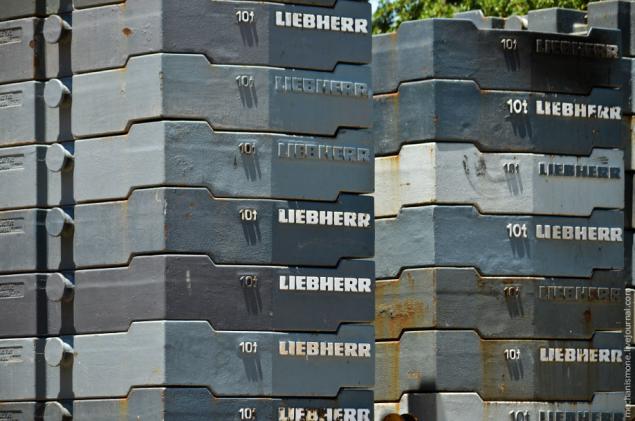
33. When filling each section, made of concrete cylinders of 10 (diameter) x 20 (H) cm or 15h30 cm, which leaves near the flooded portion after 3 days they will be taken to the lab and broken, then will be calculated the strength of the poured concrete. This is done in order to ensure that the poured concrete meets all the requirements. This is done precisely on-site operation, the cylinders are in the same conditions as the concrete. If you fill cylinders at the plant reinforced concrete where cement mixers are very often obtained inflated figures. If the concrete does not pass the test - coating have to dismantle and perezalit.
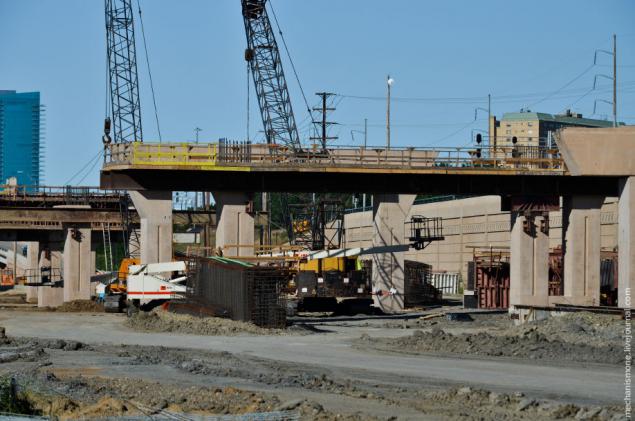
34. Typically the thickness of the screed mezhshtatovkisih highway - 30 cm, smaller highway - 20 cm. In practice, this thickness of the concrete, laid on an asphalt pad provides excellent resistance to load and does not require a second steel mesh. When the thickness of the concrete - cracks because Concrete does not have enough steel for load distribution, with decreasing thickness - concrete can not withstand the load of cars.
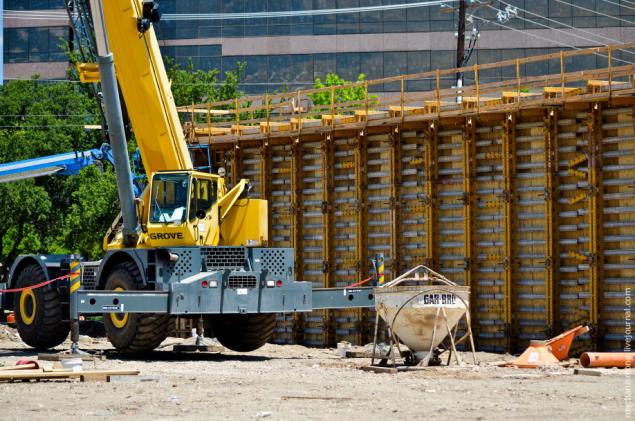
35. After penetration, paver usually draws a rough surface, which helps run the water when it rains, as well as increases the coefficient of friction of the wheels of cars and the road surface. Sometimes roughness just do not, and cut after using a special machine. Usually this happens on solid bridges.
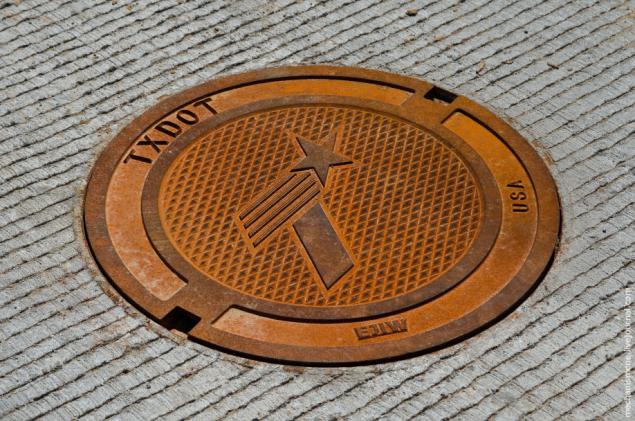
36. Just after pouring on the road do not forget to sign when the segment has been filled in, then it is useful in the repair order, as well as to know when you can open the way for the transit of construction machinery in the process of work. Concrete should be based on a minimum of 7 days without stress, after seven days on the road, you can travel light construction equipment, but we must not forget that the full strength of the concrete will gain only 28 days, and if for some reason on the cover gets heavy machinery, the structure concrete can be completely damaged. Therefore, if you need somewhere to move the road a heavy crane - under a stele mats or concrete poured a thick layer of sand.
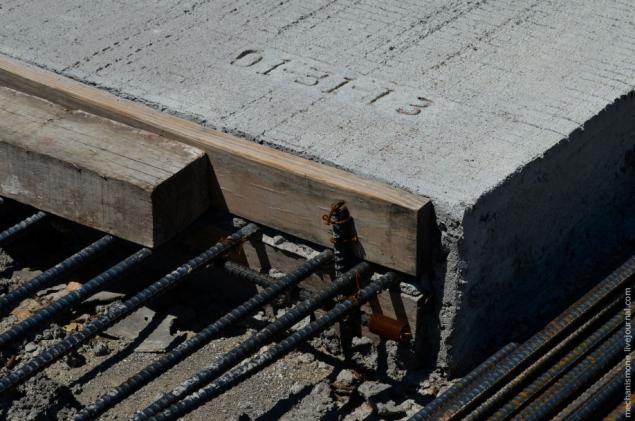
37. After 28 days, the road is completely ready to work. The service life of the road without major repairs - 25 years. In the cities of Houston and Dallas have a stretch of highway, flooded in 1960, and are in perfect condition until now. These areas are used for research and observation. Scientific papers simmer two largest and most prestigious universities in Texas - in Austin (capital of Texas) and in Houston.
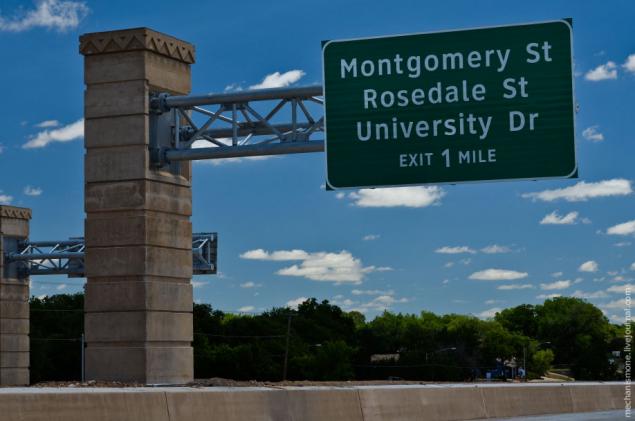
38. Today, the US is a relatively large experimental areas of concrete pavement since Transport Department sees concrete way of the future. These segments are located in all four climatic zones in the country and have different design. By 2001, from a few hundred flooded areas during the period from 1961 to 2001 left 89 sections of the monitored.
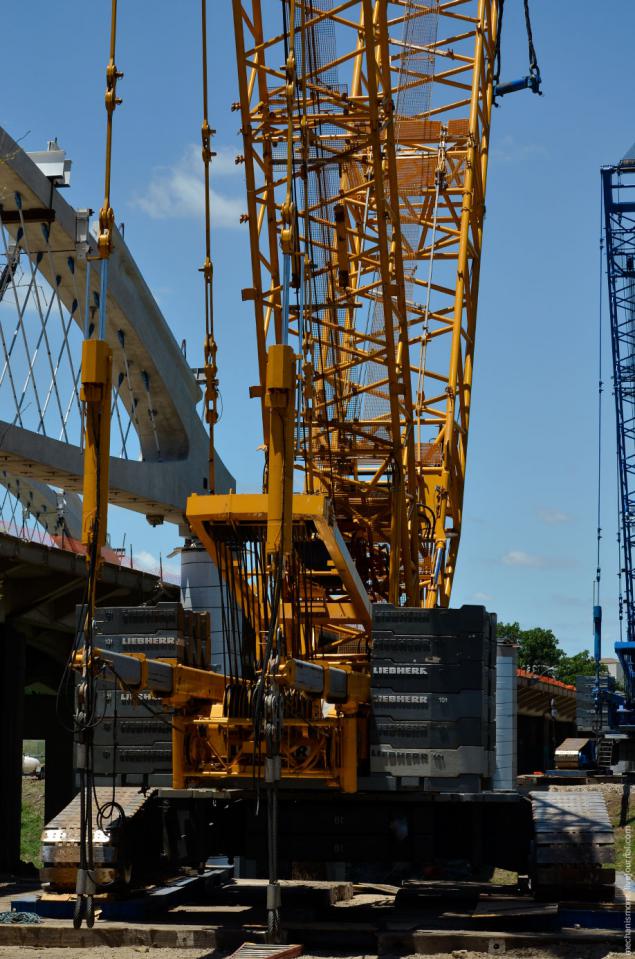
39. On the basis of experiments conducted in 1999 and 2001 on the basis of areas in age from 25 to 40 years, there were several conclusions:
- Depending on the design and materials, concrete cover capable of withstanding loads without cracking over 34 years (compared to an average of 8 years, asphaltic concrete);
- After 34 years for the next 5 years, only 16 pieces fell into disrepair and were to be completely replaced;
- Within 20 years, motorists have complained about the deterioration of the ride comfort, but in some areas, "surrendered" supports ground, forming small ravines flowing without causing cracks in the top layer covering the roadway;
- By 2012, 89 pilot sites, 34 are active (17 are in Texas). Their average age today - 31 year. The remaining sections were pereulozheny due to the current expansion of roads, and scientific works to date rudder were successfully completed.

40. Experience in laying concrete roads actively adopt the US Asia and beyond. Laying of concrete highways actively China and Japan as well as Australia and some European countries, using the accumulated experience of the American road builders. In the United States, as much as possible, trying to build a new states only road made of concrete, reducing the costs of maintaining roads during their operation.
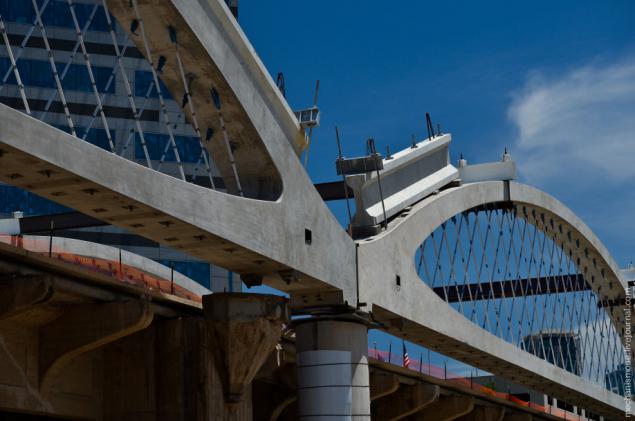
Source: