1527
How to create a product in the consumer electronics industry for a couple of weeks with a minimum budget
Not so long ago, I wrote a small post Habré on how to organize automatic watering houseplants on Arduino. In comments to the post, many have suggested that too just realized that there is no magic stick as wire and looks unsightly. Were also very sensible remarks on the functional units associated with the need to use the Soil Moisture Sensor and others. In the end, I decided for a relatively short time to make a device that both in appearance and over the filling would be comparable to a commercial product. Perhaps this story will inspire someone to create your own products or help in disseminating experience.
After publication, I decided that you can try to implement some of the ideas expressed in the comments. First of all, the proverbial magic - in the form of decent housing. Talked about the idea of the project to his friend. After some discussion, we came to the following requirements to the device:
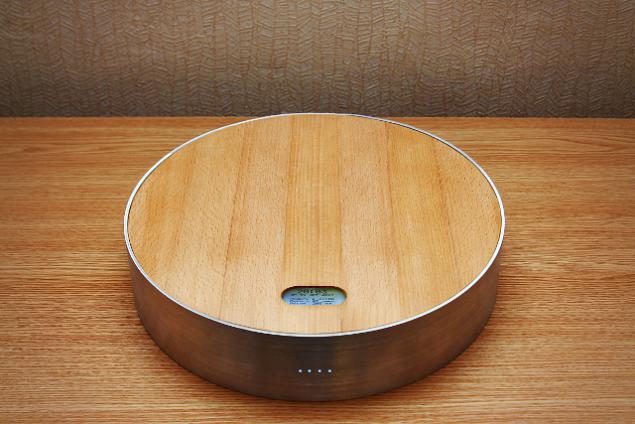
After publication, I decided that you can try to implement some of the ideas expressed in the comments. First of all, the proverbial magic - in the form of decent housing. Talked about the idea of the project to his friend. After some discussion, we came to the following requirements to the device:
- This device must be implemented as a stand under the pot with a potted plant and accommodate yourself at least two liters of water
- On the control panel, you must install the display settings to comfortably manage irrigation < /
- is necessary to control the water level in the tank, so that the device could just remind us of the need to add water
- It is also important to lay further extensibility to connect to the internet to be able to control the device through a web form or mobile application
Each of us have a bunch of major cases, so pay a lot of time side project, we could not come to the conclusion that it is necessary to try to make the device, it is not spending more than a week. The result was longer, but it is this concept we started working.
The basis of the management controller went to those items that were on hand. It was originally planned as a basis to take microcontroller family of 16 MicroChip and real time clock DS1302. But from the "peaks" on hand or controllers with a small number of conclusions, or in large buildings - DIP40, and board wanted to make a compact, then his arm caught a 32-bit ARM microcontroller STM32F100C8T6. Of the real-time clock were only PCF8283. As an indicator for the controller options were considered: Character display from WinStar, graphic display with a resolution of 128x64 controller ST7565R and still the possibility of using the display of a cell phone. Character display have disappeared at once, because they would look very bulky design polivalki among the remaining options graphic displays, the display on the controller display ST7565R conceded by nokia1100 in connection with a very simple installation and wiring of the last
So, now you must make a nice appearance of the device. To this end, I contact with a familiar industrial designer to help us with the form. After a couple of hours, he sends a few pictures:
Looks nice. Functional details, of course, can be discussed, but we do not do this, because our task to keep within a few days, and sometimes weeks to discuss possible design. Couple nights thinking through design solutions and choice of materials that will be used and before us a small pile of drawings and the need to produce 10 types of parts.
We start with the metal. To do this, go to one of hakspeysov Yekaterinburg, which has machines for metalworking and the opportunity to work with them for a small fee. Metal we need to do first, ring-body to get the saucepan on the design, and secondly, to carve the union, which will connect the hoses, and multiple racks with internal thread, which is installed with the electronics panel.
The most difficult thing - to do this aluminum ring - body: first cut down on the guillotine the right size strip of aluminum sheet and drilled her holes in the right places. Then rolled on rollers and get longer ring, which must be carefully boil. Especially for this master the welding with argon. (But killed half a day watching tutorials on youtube for welding and argon for a trip to the other end of the city). After a few workouts get less suitable seam.
We looked at two ways to make the metal surface attractive:
- anodizing
- accurate grinding
Stop for grinding, as in our opinion it is an easier way. When grinding is extremely important to the direction of movement of the grinding surface detail has always been constant, otherwise polishing will not neat. Therefore Master tooling for small drill, a spindle which stifle Flap grinding wheel.
Thus, the metal finished. Go to the plastic parts, which we have three: two covers that cover our body from above and below, and the panel electronics with holes for the buttons and the display window.
Laser-cut lid - for this we have to get out of hakspeysa, since the laser machine and there is no appeal to the company profile. Here is how the process of cutting through our drawings:
Panel for electronics make a thick Plexiglas. Since the layout has blind holes, the laser does not fit - cut on a milling machine cnc
It remains to make the top wooden lid, which will put a pot plant. It is important to choose the right kind of wood - firstly, it is necessary that the tree was beautiful pattern on the cut, and secondly - it is important that the tree does not lead during use. Therefore, we buy beech wood panels - you can buy in any store a profile. And cut the workpiece on a milling machine
Since the workpiece was 20 mm in height, and the height of the cover is less than 10 drawings, it is necessary first to cut more than half the height of our shield. Seeing as translated material remaining hakspeysovtsy indignant and scare me Lawrence P. Berey. But we set deadlines for the project and burn time trying to look for a sheet of the desired height is not, so dofrezerovyvaem and move on to the next stage - the assembly.
CNC justified and assembly of special problems have arisen - a little work with a file nevertheless had.
The first tests show that in general everything works as expected. Here is polivalki in:
In the future I plan to add control settings avtopolivom through the web interface.
I hope that this article will inspire someone to put into good-quality iron their findings and ideas.
Source: habrahabr.ru/post/216109/