748
How to make warm water floor with their hands
Warm water floor with his handsMount warm water floor with their hands – not an easy task. If no extra funds to hire professionals, you can rely on their own strength. A detailed study of the question and all accompanying instructions, you can make really high quality, warm floors, which will delight household.
Features warm water floorImmediately it should be noted that the warm water floor is best installed in a private or a country house. Housing conditions is quite difficult to connect the system to Central heating and there is generally a practical possibility to create something similar at home.
One of the main benefits of water sex is to significantly reduce heating costs. In addition, the heating will be more comfortable, because the room is warmed evenly, which just can not be done with traditional radiator heating.
Also it is important to choose the best type of pipes for floor heating. Today hardware stores offer several types of pipes for Underfloor heating. If you do not understand them, it is best to consult on this issue with experts.
The device of water floor- type installation, it is possible to distinguish two types of radiant floor. concrete and decking. Flat floors, in turn, are divided into wood and the polystyrene system.
The device of concrete floors means that the floor surface will be closed with a concrete screed.
Grazing from the concrete floors differ in that they excluded any "wet" works, due to which installation work is performed several times faster.
Installation of warm water floorBefore starting installation of the water floor, it is recommended to get acquainted with the peculiarities of work and instruction.
The most common system installation of warm water floor is a concrete system. In this case, the pipe circuits will be closed with a concrete screed, which does not need to use additional separators heat.
Technology installation is divided into several stages:
Installation of insulation materialsrough surface of the floor carefully trimmed and covered with insulating layer. Due to the presence of the thermal insulation coating will not be heat loss from the warm floor. The energy will only go up to the room. In the process of insulation can be used in a variety of materials that are suitable for a particular situation.
The most common material is polystyrene and polystyrene. The density of the insulating layer should be more than 35 kg/m 3. and a thickness of 30-150 mm (depends on thermal regime and the amount of heat loss).
Across sectors and along the perimeter of the room is required to lay a damping tape which is necessary to compensate for the expansion of ties. The layer of insulation is laid polyethylene.
Laying reinforcing mesh and pipe installationtypically mesh reinforcement is placed with the cell dimensions of 150x150 mm. allowed dual reinforcement, in which the layer of mesh is laid on top of the assembled pipes.
After the grid is to be laid, the installation pipes of the future water floor. Depending on the specific project, the pipe can be laid in increments of 50-300 mm. With plastic clamps pipe fixed to reinforcing mesh, and in places of expansion joints on the pipe to ensure the protection of installed corrugated pipe.
There are several schemes of laying the pipe circuits: a normal snake and double normal spiral and with a displaced center. In the process of laying pipes along the exterior walls need to decrease the step in order to prevent temperature changes on the floor. Feeding part of the loop you need to hold along the wall because there is higher heat loss.
Per 1 sqm of the surface of the flow tube in steps of 200 mm will be about 5 meters. In addition, during installation, you need to remember that whips longer than 100 m must not be put, because in the end of the loop will be significant heat loss.
Pressure testing and filling of a concrete rodOn the end of installation you want to press the system under the working pressure mechanical damage. In other words – to check the efficiency of the entire system. At this stage you can clearly see if everything was done correctly and efficiently and without serious cost to correct all identified deficiencies.
The concrete screed should be carried out only after crimping. The whole system is under operating pressure must be at least 24 hours. In addition, the system pressure must be in the process of pouring the concrete screed.
In most cases, the coupling is performed in several layers, and one layer thickness is 50-70 mm. For these purposes can be used in different blends designed specifically for Underfloor heating.
Once the concrete screed has dried, installation of finish flooring. The coating can be any by the owner.
The polystyrene system warm floorsystem Polystyrene is very light. It consists of polystyrene plates with grooves size mm. 30х300х1000 In the grooves set aluminum plates, which snap into pipe circuits. After testing on the system to put the finishing coat without the use of concrete ties, if it is assumed installation of hardwood or laminate flooring.
Wood floor heating systemHardwood systems for warm water floor can be divided into rack and modular. These systems, typically used for the device warm floors in the modular panel Board houses, and they are placed on the rough floor or wooden logs.
Modular ulatively type of presentation involves the use of finished particleboard panels with channels for installation of pipe and plates.
Particleboard with a thickness of 22 mm is necessary to secure the aluminum plates and create a hard surface. In this design the insulator must be provided in the overlap. Particle Board strips to be in accordance with the available project documentation and 20-mm intervals between them.
Depending on the step of the strip tube are taken with a thickness of 130 to 280 mm. aluminum plates are designed for modular stacking, there is a special profile with snaps, through which the heat transfer between the pipe and the plate is the most efficient. The size of the plates – 150-300 mm. On the plate must be mounted with a layer of slabs of gypsum-fiber Board. If the floor finish will be presented with parquet or laminate, gipsovolokno can be neglected.
Rack stackingWhen stacking rack for the device of water warm floor, in most cases, apply strips of boards or thickness of 28 mm particle Board go. Step – 150-300 mm, the distance between boards is 20 mm. the Rack system can be mounted directly on the joists. Between the joists the maximum allowable distance is 600 mm. If finished surface is to be arranged by means of ceramic tiles, 300 mm Between the joists as insulation is usually laid mineral wool or polystyrene. To the rack and pinion system, the insulation layer is much thinner, in contrast to the modular, so this way the device warm floor, it is recommended to use on floors between floors of wooden houses.
Rack for stacking for the device warm floors are aluminum plate, the step of stacking is 150-300 mm. Around the Windows and exterior walls must adhere to the step of laying 150 mm.
Schema systems, a warm water sex
published
Source: rahlina.com.ua/otoplenie-i-gazifikaciya/teplyj-vodyanoj-pol-svoimi-rukami/
Features warm water floorImmediately it should be noted that the warm water floor is best installed in a private or a country house. Housing conditions is quite difficult to connect the system to Central heating and there is generally a practical possibility to create something similar at home.
One of the main benefits of water sex is to significantly reduce heating costs. In addition, the heating will be more comfortable, because the room is warmed evenly, which just can not be done with traditional radiator heating.
Also it is important to choose the best type of pipes for floor heating. Today hardware stores offer several types of pipes for Underfloor heating. If you do not understand them, it is best to consult on this issue with experts.
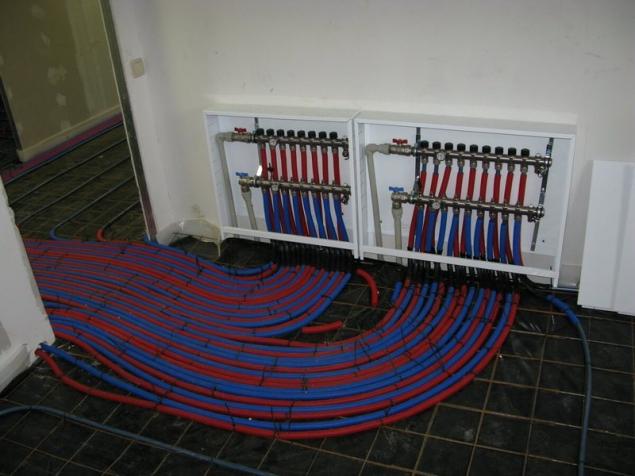
The device of water floor- type installation, it is possible to distinguish two types of radiant floor. concrete and decking. Flat floors, in turn, are divided into wood and the polystyrene system.
The device of concrete floors means that the floor surface will be closed with a concrete screed.
Grazing from the concrete floors differ in that they excluded any "wet" works, due to which installation work is performed several times faster.
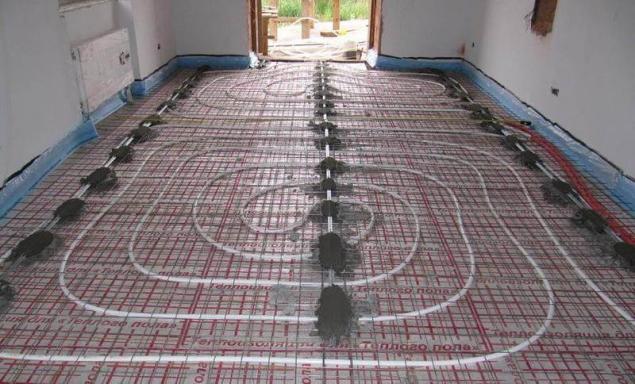
Installation of warm water floorBefore starting installation of the water floor, it is recommended to get acquainted with the peculiarities of work and instruction.
The most common system installation of warm water floor is a concrete system. In this case, the pipe circuits will be closed with a concrete screed, which does not need to use additional separators heat.
Technology installation is divided into several stages:
- The division of space into separate areas with a maximum size of 40 sq. m.;
- Laying on the rough floor insulation materials;
- The installation of wire mesh and the contours of the tubes;
- Compression work;
- Device couplers;
- The finishing coat.
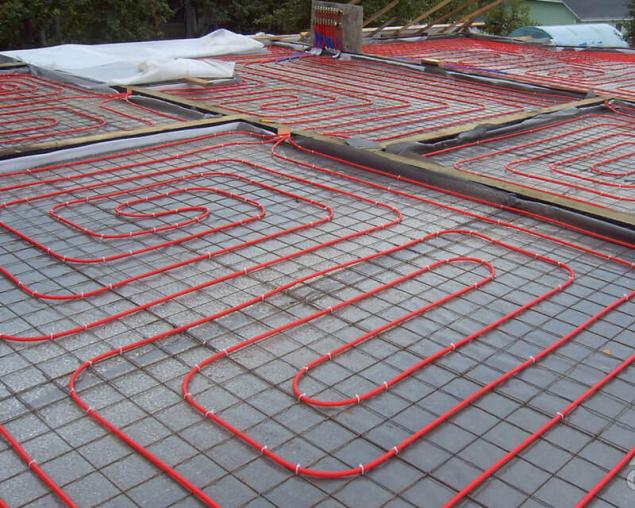
Installation of insulation materialsrough surface of the floor carefully trimmed and covered with insulating layer. Due to the presence of the thermal insulation coating will not be heat loss from the warm floor. The energy will only go up to the room. In the process of insulation can be used in a variety of materials that are suitable for a particular situation.
The most common material is polystyrene and polystyrene. The density of the insulating layer should be more than 35 kg/m 3. and a thickness of 30-150 mm (depends on thermal regime and the amount of heat loss).
Across sectors and along the perimeter of the room is required to lay a damping tape which is necessary to compensate for the expansion of ties. The layer of insulation is laid polyethylene.
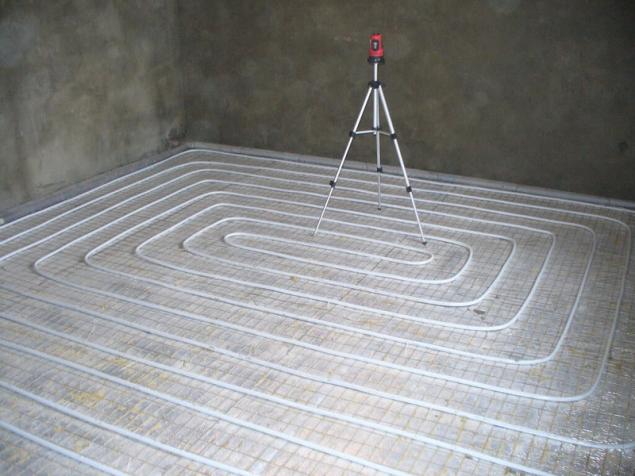
Laying reinforcing mesh and pipe installationtypically mesh reinforcement is placed with the cell dimensions of 150x150 mm. allowed dual reinforcement, in which the layer of mesh is laid on top of the assembled pipes.
After the grid is to be laid, the installation pipes of the future water floor. Depending on the specific project, the pipe can be laid in increments of 50-300 mm. With plastic clamps pipe fixed to reinforcing mesh, and in places of expansion joints on the pipe to ensure the protection of installed corrugated pipe.
There are several schemes of laying the pipe circuits: a normal snake and double normal spiral and with a displaced center. In the process of laying pipes along the exterior walls need to decrease the step in order to prevent temperature changes on the floor. Feeding part of the loop you need to hold along the wall because there is higher heat loss.
Per 1 sqm of the surface of the flow tube in steps of 200 mm will be about 5 meters. In addition, during installation, you need to remember that whips longer than 100 m must not be put, because in the end of the loop will be significant heat loss.
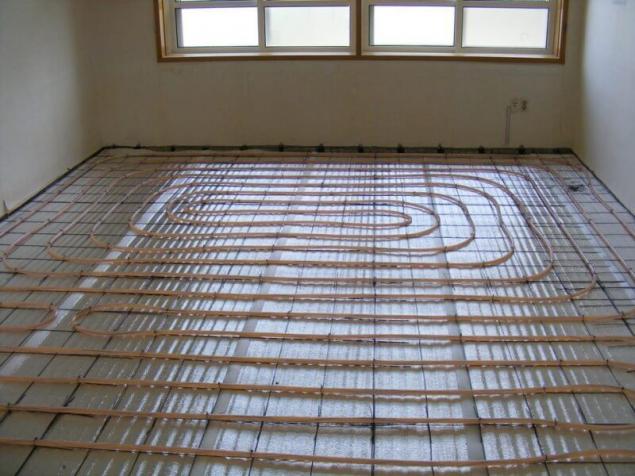
Pressure testing and filling of a concrete rodOn the end of installation you want to press the system under the working pressure mechanical damage. In other words – to check the efficiency of the entire system. At this stage you can clearly see if everything was done correctly and efficiently and without serious cost to correct all identified deficiencies.
The concrete screed should be carried out only after crimping. The whole system is under operating pressure must be at least 24 hours. In addition, the system pressure must be in the process of pouring the concrete screed.
In most cases, the coupling is performed in several layers, and one layer thickness is 50-70 mm. For these purposes can be used in different blends designed specifically for Underfloor heating.
Once the concrete screed has dried, installation of finish flooring. The coating can be any by the owner.
The polystyrene system warm floorsystem Polystyrene is very light. It consists of polystyrene plates with grooves size mm. 30х300х1000 In the grooves set aluminum plates, which snap into pipe circuits. After testing on the system to put the finishing coat without the use of concrete ties, if it is assumed installation of hardwood or laminate flooring.
Wood floor heating systemHardwood systems for warm water floor can be divided into rack and modular. These systems, typically used for the device warm floors in the modular panel Board houses, and they are placed on the rough floor or wooden logs.
Modular ulatively type of presentation involves the use of finished particleboard panels with channels for installation of pipe and plates.
Particleboard with a thickness of 22 mm is necessary to secure the aluminum plates and create a hard surface. In this design the insulator must be provided in the overlap. Particle Board strips to be in accordance with the available project documentation and 20-mm intervals between them.
Depending on the step of the strip tube are taken with a thickness of 130 to 280 mm. aluminum plates are designed for modular stacking, there is a special profile with snaps, through which the heat transfer between the pipe and the plate is the most efficient. The size of the plates – 150-300 mm. On the plate must be mounted with a layer of slabs of gypsum-fiber Board. If the floor finish will be presented with parquet or laminate, gipsovolokno can be neglected.
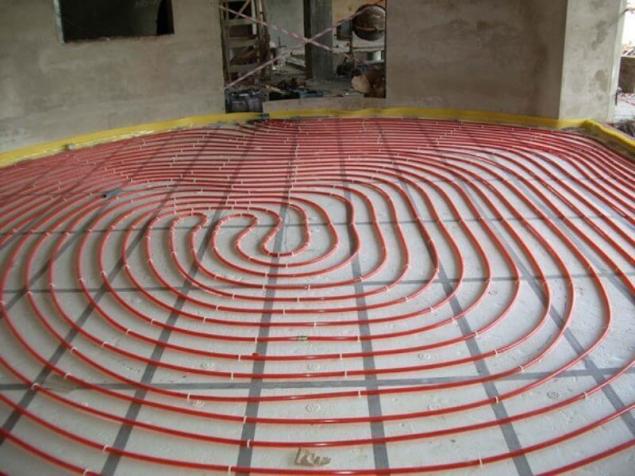
Rack stackingWhen stacking rack for the device of water warm floor, in most cases, apply strips of boards or thickness of 28 mm particle Board go. Step – 150-300 mm, the distance between boards is 20 mm. the Rack system can be mounted directly on the joists. Between the joists the maximum allowable distance is 600 mm. If finished surface is to be arranged by means of ceramic tiles, 300 mm Between the joists as insulation is usually laid mineral wool or polystyrene. To the rack and pinion system, the insulation layer is much thinner, in contrast to the modular, so this way the device warm floor, it is recommended to use on floors between floors of wooden houses.
Rack for stacking for the device warm floors are aluminum plate, the step of stacking is 150-300 mm. Around the Windows and exterior walls must adhere to the step of laying 150 mm.
Schema systems, a warm water sex
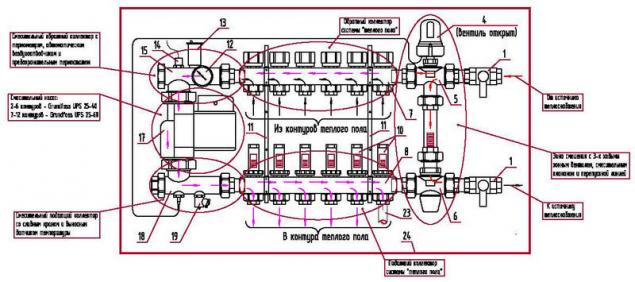
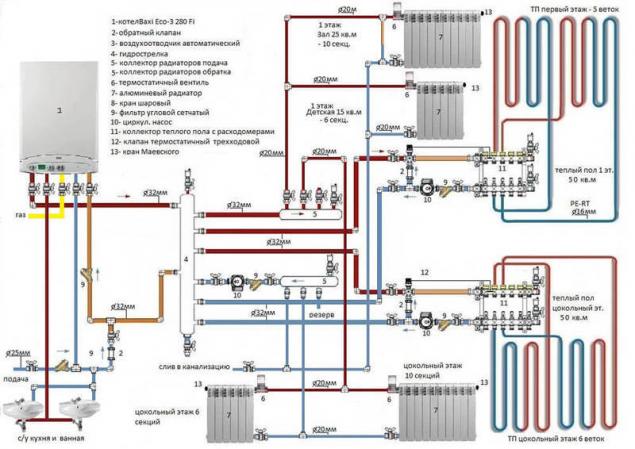
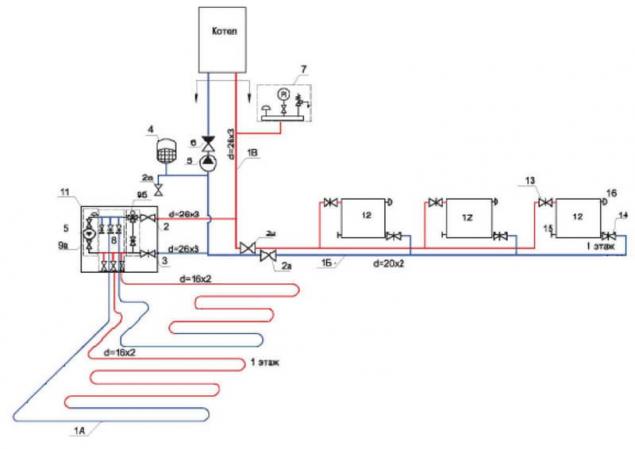
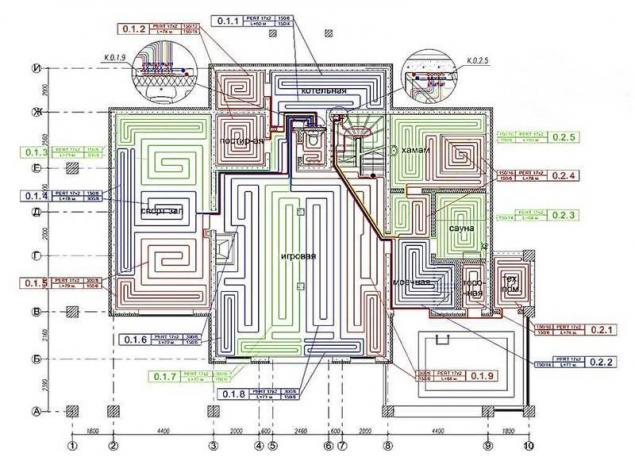
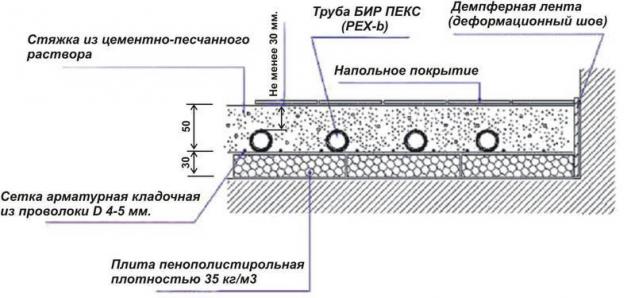
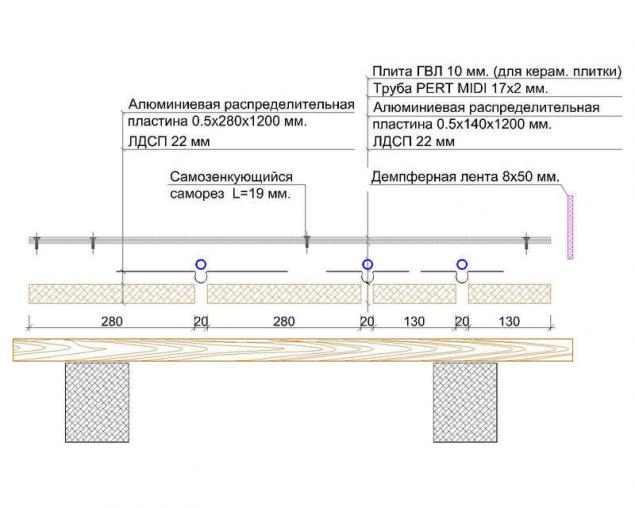
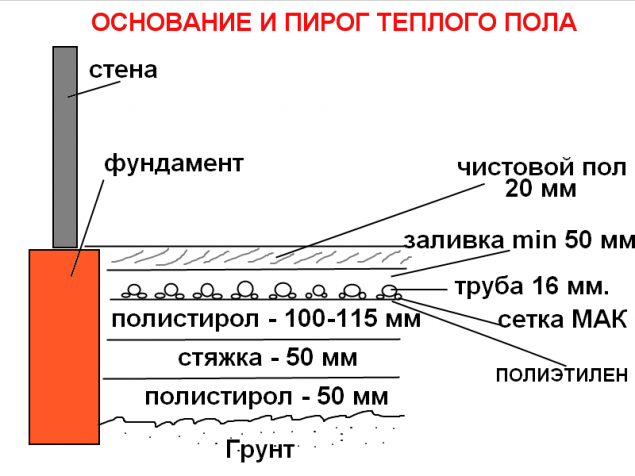
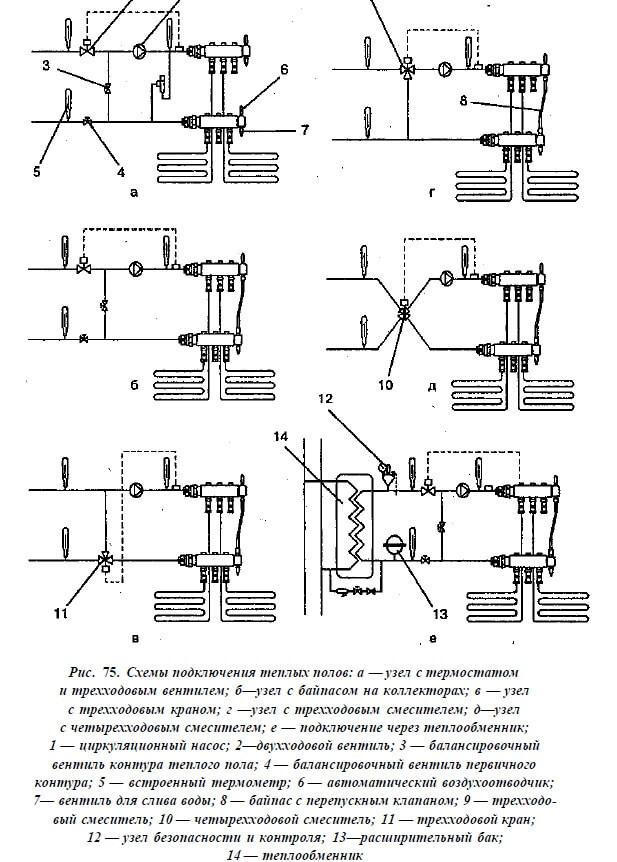
published
Source: rahlina.com.ua/otoplenie-i-gazifikaciya/teplyj-vodyanoj-pol-svoimi-rukami/