935
New process technology to reduce the cost twice the battery Li-Ion
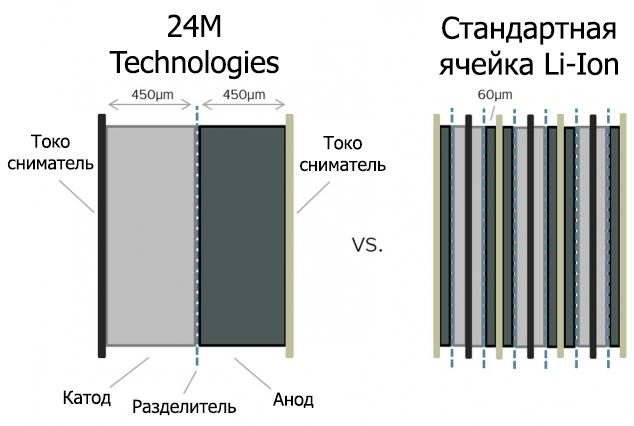
Researchers at the Massachusetts Institute of Technology and the company 24M developed an improved manufacturing process of lithium-ion batteries of the new design. According to the calculations of engineers, it is at least twice as reduce the cost of batteries by simplifying the process and reducing the number of necessary materials, while improving battery performance.
Li-Ion batteries - is the most expensive part electric. Only due to this "hack" the retail price of the car will be reduced significantly.
"We have reviewed all the technical process», - рассказывает Professor Chan Ming-Yett (Yet-Ming Chiang), co-founder 24M (previously it was also the co-founder of the battery manufacturer A123). The current manufacturing process of batteries, he says, practically unchanged for two decades since the invention of technology. It is inefficient and uses more steps than necessary.
By 2020, according to Chan, the company is able to produce 24M batteries for less than $ 100 per kilovatt⋅chas. According to мнению experts, it is this value is the price threshold for the mass distribution of electric vehicles. Now under construction megazavod Tesla Gigafactory 1 nadeesya also enter a value in 2017 due to mass production.
Currently, according to оценкам, the cost of Li-Ion batteries range from $ 300 to $ 500 per kilovatt⋅chas.
"Semisolid" batteries
The new process technology is a hybrid model between conventional solid battery and the so-called «fluid» battery (flow battery), in which the role of electrodes performing a suspension of tiny particles in a liquid, injected into various compartments of the battery. Actually, this design battery-five years ago he invented Professor Chan and colleagues.
In an embodiment, 24M, while the electrode material is not fluid, it still consists of similar "semi-solid" colloidal suspension. Actually, that Nazan "semi-solid" battery.
This approach greatly simplifies production of battery, and adds them to the flexibility and strength. In a study that Professor published in the journal «Journal of Power Sources» ( doi: 10.1016 / j.jpowsour. 2015.06.023 ), said that the new design is suitable for battery and low energy density and high energy density as in Li-Ion battery.
Standard fabrication process involves layering liquid on the rolls of substrate. Each layer must be dry before applying the next. The new method does not require any drying. Using a minimal number of electrodes with a smaller thickness, it is 80% reduces the number of layers in the battery and the number of non-working of the material inside akkulyatora.
If the electrodes are particles in suspension, the charged particles have to overcome a smaller distance - a property known as "tortuosity" that reduces the amount of material required for the electrodes.
The illustration shows that the new batteries can be bent and collapse, it does not affect their properties.
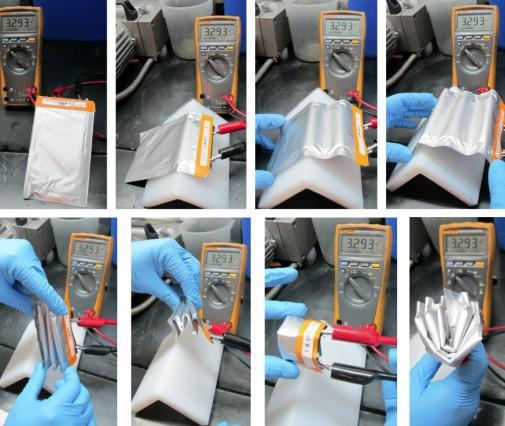
24M The company has already produced at the pilot plant of about 10,000 batteries for testing. The company has received eight patents pending is still 75 patent applications. Taking into account the $ 50 million received investment from venture capital firms, plus a grant from the US Department of Energy, it is clear that a serious business here.
Originally intended to use batteries as a backup power supply in alternative energy, but now Professor Chang and his colleagues decided that the new batteries are quite suitable for electric vehicles.
What is important, the new process technology allows a small factory to achieve the same production costs, as well as on the huge factory. Increasing the scale does not provide a significant economic benefit. So the economic outlook Gigafabriki Tesla Motors becoming a little more vague. However, Elon Musk will not be offended if without his help Li-Ion batteries will drop by several times.
Source: geektimes.ru/post/252538/
Conversation with God
The United States did not grant visas for more than two weeks due to a computer crash