1050
The new Airbus aircraft over 1,000 pieces printed the 3D-printer
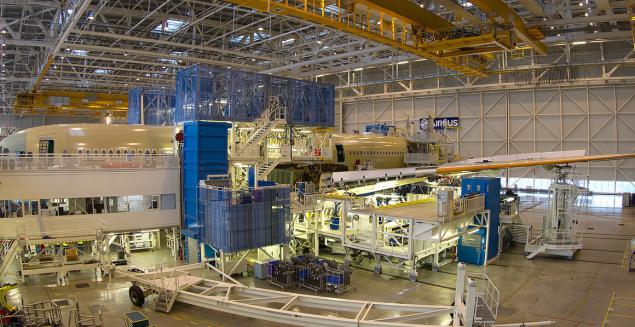
The new aircraft of the French company Airbus A350 XWB, whose headquarters is located in the district of Blagnac, contains more than 1000 different parts produced 3D-printing technique. They are made to order in a US-Israeli company Stratasys . The company claims that the final details are more easy, durable and less expensive than counterparts manufactured in the usual way.
The new model will be the first in a line of Airbus, in which the details of fuselage and wings are made of lightweight and durable carbon fiber. The first copies of the company plans to deliver in December for the airline Qatar Airways.
"We are pleased that the decisions about the three-dimensional printing by Stratasys will be applied in the new flagship model of the Airbus A350 XWB. Our companies find it necessary to use innovative technologies in the development and manufacture of generating lasting benefits, - said Vice President Stratasys Dan Jalonen. - Our production can produce items to order and to carry out the delivery on time. Reduction in production is achieved due to the lack of waste in the production ».
The company uses in the production of thermoplastic ULTEM 9085 , of which details are printed on the printer FDM. They not only get lighter and more durable, but also fireproof and non-toxic.
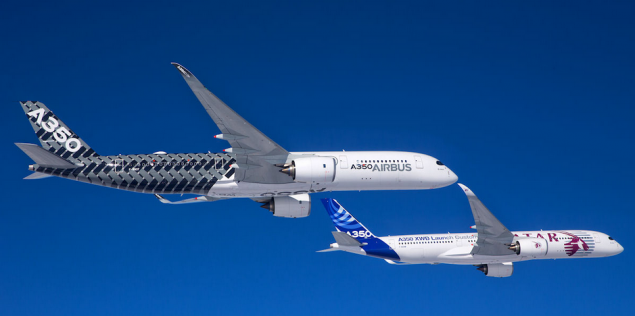
During the March announcement aircraft Peter Sander, head of innovation Airbus, said that the new method produced items weigh less than standard at 30-55%, and their production uses 90% less raw material and consumes 90% less energy compared with traditional methods
Modern 3D-printers are suitable for use in the aerospace industry, and not only for the manufacture of parts of the fuselage, but even to print these engines. Rocket Injector by NASA during testing withstand temperatures of 3300 ° C, while its manufacturing cost is much cheaper than the welding of 163 parts of a standard project. A Monash University (Australia) printed copy of the gas turbine Microturbo (Safran).
Source: geektimes.ru/post/250096/
NASA announced the contest "Journey to Mars": the best ideas to minimize dependence on the earth on the Red Planet will receive $ 5,000
Measuring the speed of light using a webcam