1608
As born SSD drives? Insight into the process
Many of us have either used or are thinking about how to put yourself SSD drives. But few people know which way they go from disparate set of parts to a beautiful factory packaging.
What distinguishes the production of SSD drives from the production of memory modules, say, or flash drives? Settings conveyor line and test environments. The boards are produced on the same assembly lines. Why I decided to tell it about the SSD? They're just like me.
Start the story could be far away. It might even be very far away - for example, here:
That's what a silicon metal, which is then melted in special furnaces, cut into thin disks and make chips. Of this I may even tell you somehow. In the meantime, let us imagine that the chips have already been made, PCB foil prepared, and we can move on.
PCB sheets loaded onto a conveyor line manually. Features conveyors different manufacturers differ slightly. Some line is fully automated, others some operations are carried out manually. For example, A-DATA and some Chinese manufacturers of hand made visual inspection of almost every board, and some factory hand even share list on the part of the PCB after soldering all the details.
Share it falls because almost until the end of the line list goes entirely. Workpiece etched tracks, slotted holes and marks inflicted or manufactured in the factory, or ordered from a private company, specializes in the manufacture of such boards. I was unable to find a quality photo blanks for SSD drives, because to create a rough idea of what it looks like below picture harvesting module RAM.
After the preparatory stages of the workpiece enters the machine, which automatically applies a stencil solder paste, a mixture of small particles of tin with flux (thanks Ocelot for clarification ). Presented below car with Kingston plant resembles a droid from any space saga.
Under dark glass - stencil with slots and a large roll of pasta, greyish viscous mass. From this droid workpiece enters the apparatus for checking the accuracy of applying the paste. Part of this unit and often serves as the human eye, but without a computer check is complete. After applying the workpiece enters the machine, SMT components are mounted (by Surface Mounting Technology, surface mount technology). All items, from the smallest resistor to controllers and memory chips are fed into the machine so that's machine-gun belts:
At the exit of the car - another check on the correctness of the details. Here ratio Automatic / person also varies depending on the plant. The test is successful, and our future disc is ready for baking. Yes, baking. Not to shoot laser sighting for each contact every detail, PCB together with all the details is simply baked.
This long process kiln, depending on the plant is divided into zones 7-12, wherein the temperature ranges from 90-150 degrees at the inlet to 250-280 in the hottest area closer to the exit (on the outlet temperature decreases rather quickly, and exits from the furnace already chilled product). Yes, now it can be safely called the product. It is not yet ready for use, but close.
After the furnace special devices produce validation soldering. Computer compare images of different areas of the card with sample photos, and if a problem is detected, the board sent to the manual check. In some plants solder additionally checked in X-rays.
After checking the soldering product label stickers on which the manufacturer will be able to track the full story, and finally separated. Comes the stage of testing. The first part takes place more on the line. At the time, the controller automatically loaded firmware and produce a short initial tests that take a few seconds, and if everything is in order, go to the shop and test firmware.
Because, Lite-On test speed produces a special aging chamber at an elevated temperature. This allows you to quickly identify the faulty chips. According to statistics, at this stage, be rejected only about 0, 1% of the party. The test lasts for a couple of hours to drive 64 GB to almost a day to drive 512GB. During the test produced a constant read-write in the cell.
At A-DATA testing occurs not as hard. Drives are connected to a special counter in an open area where additional testing is done, fill flash and layout of the file system.
If it comes to testing new, recently developed models, they will be checked for compatibility with most of today's popular platforms. Alone laptops on the test site Lite-On, there are hundreds, and every month added new ones. Just a laboratory for testing new models of products 85 racks, each containing 5 test platforms plus one for logging.
After testing the product packed in the body, glue stickers branded and packaged. This is mainly done by hand, fragile handles Asians. Would imagine one such lotochek?
And then it's simple. Discs are packed in original box and shipped to wholesalers. One plant is capable of producing millions, if not tens of millions of CDs per year. And they are all waiting for their moment when they get into your computers and servers.
In the near future I plan to talk about the different types of memory cells in the SSD drives, their advantages and disadvantages. Subscribe to our corporate blog and stay tuned.
Source: habrahabr.ru/company/ua-hosting/blog/222023/
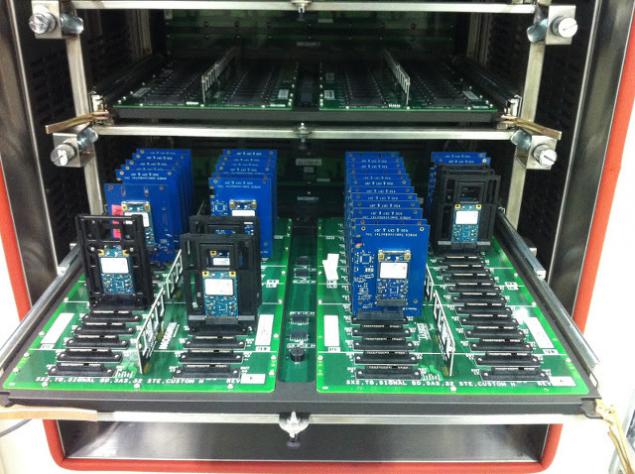
What distinguishes the production of SSD drives from the production of memory modules, say, or flash drives? Settings conveyor line and test environments. The boards are produced on the same assembly lines. Why I decided to tell it about the SSD? They're just like me.
Start the story could be far away. It might even be very far away - for example, here:
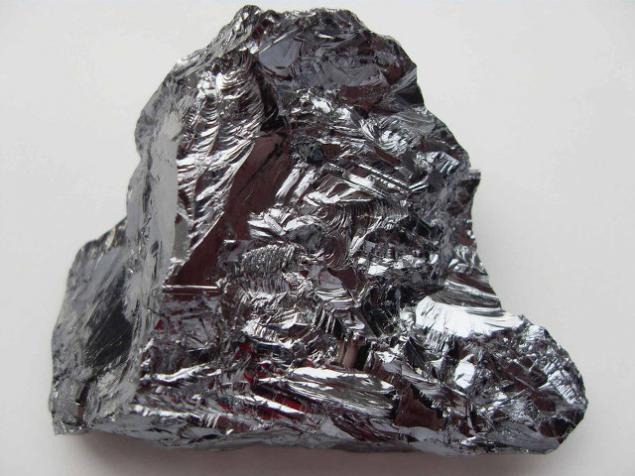
That's what a silicon metal, which is then melted in special furnaces, cut into thin disks and make chips. Of this I may even tell you somehow. In the meantime, let us imagine that the chips have already been made, PCB foil prepared, and we can move on.
PCB sheets loaded onto a conveyor line manually. Features conveyors different manufacturers differ slightly. Some line is fully automated, others some operations are carried out manually. For example, A-DATA and some Chinese manufacturers of hand made visual inspection of almost every board, and some factory hand even share list on the part of the PCB after soldering all the details.
Share it falls because almost until the end of the line list goes entirely. Workpiece etched tracks, slotted holes and marks inflicted or manufactured in the factory, or ordered from a private company, specializes in the manufacture of such boards. I was unable to find a quality photo blanks for SSD drives, because to create a rough idea of what it looks like below picture harvesting module RAM.
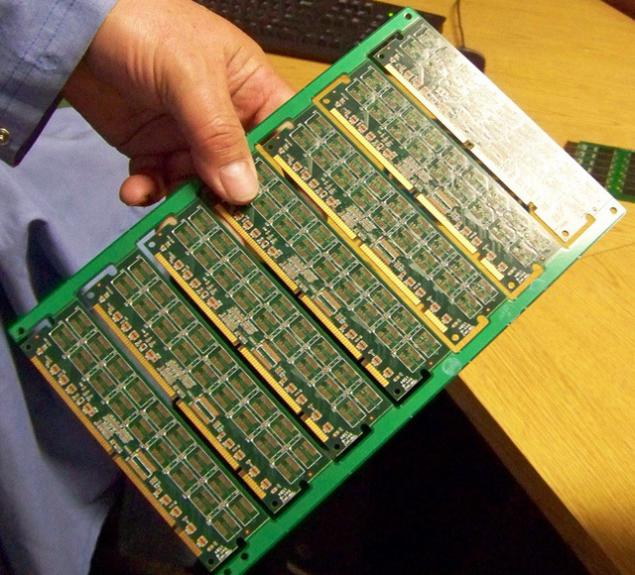
After the preparatory stages of the workpiece enters the machine, which automatically applies a stencil solder paste, a mixture of small particles of tin with flux (thanks Ocelot for clarification ). Presented below car with Kingston plant resembles a droid from any space saga.
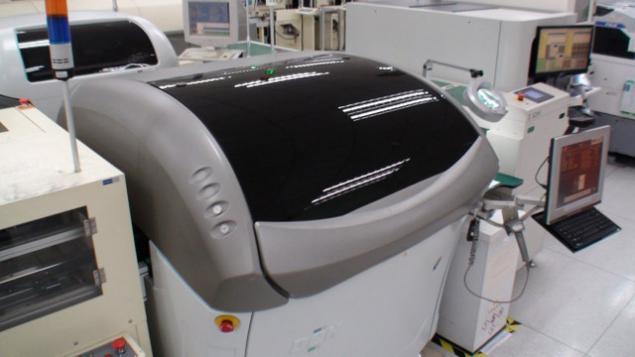
Under dark glass - stencil with slots and a large roll of pasta, greyish viscous mass. From this droid workpiece enters the apparatus for checking the accuracy of applying the paste. Part of this unit and often serves as the human eye, but without a computer check is complete. After applying the workpiece enters the machine, SMT components are mounted (by Surface Mounting Technology, surface mount technology). All items, from the smallest resistor to controllers and memory chips are fed into the machine so that's machine-gun belts:

At the exit of the car - another check on the correctness of the details. Here ratio Automatic / person also varies depending on the plant. The test is successful, and our future disc is ready for baking. Yes, baking. Not to shoot laser sighting for each contact every detail, PCB together with all the details is simply baked.
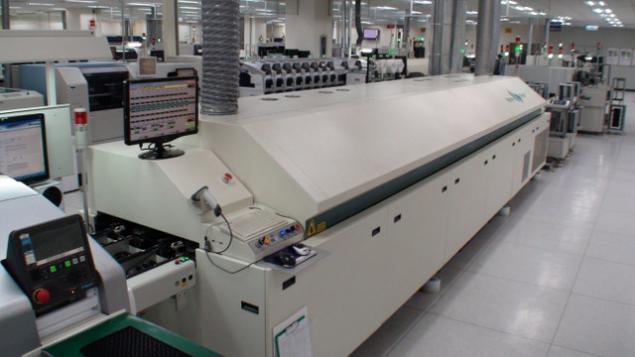
This long process kiln, depending on the plant is divided into zones 7-12, wherein the temperature ranges from 90-150 degrees at the inlet to 250-280 in the hottest area closer to the exit (on the outlet temperature decreases rather quickly, and exits from the furnace already chilled product). Yes, now it can be safely called the product. It is not yet ready for use, but close.
After the furnace special devices produce validation soldering. Computer compare images of different areas of the card with sample photos, and if a problem is detected, the board sent to the manual check. In some plants solder additionally checked in X-rays.
After checking the soldering product label stickers on which the manufacturer will be able to track the full story, and finally separated. Comes the stage of testing. The first part takes place more on the line. At the time, the controller automatically loaded firmware and produce a short initial tests that take a few seconds, and if everything is in order, go to the shop and test firmware.
Because, Lite-On test speed produces a special aging chamber at an elevated temperature. This allows you to quickly identify the faulty chips. According to statistics, at this stage, be rejected only about 0, 1% of the party. The test lasts for a couple of hours to drive 64 GB to almost a day to drive 512GB. During the test produced a constant read-write in the cell.
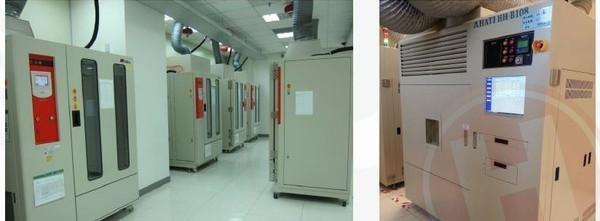
At A-DATA testing occurs not as hard. Drives are connected to a special counter in an open area where additional testing is done, fill flash and layout of the file system.
If it comes to testing new, recently developed models, they will be checked for compatibility with most of today's popular platforms. Alone laptops on the test site Lite-On, there are hundreds, and every month added new ones. Just a laboratory for testing new models of products 85 racks, each containing 5 test platforms plus one for logging.
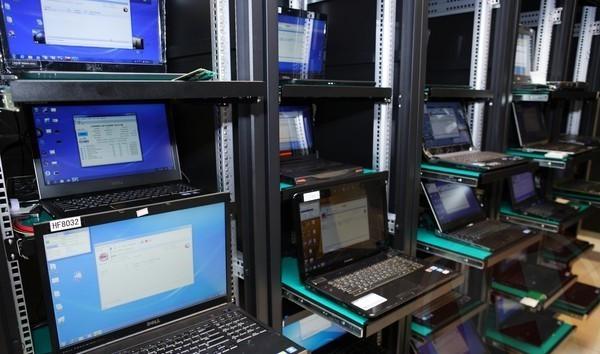
After testing the product packed in the body, glue stickers branded and packaged. This is mainly done by hand, fragile handles Asians. Would imagine one such lotochek?
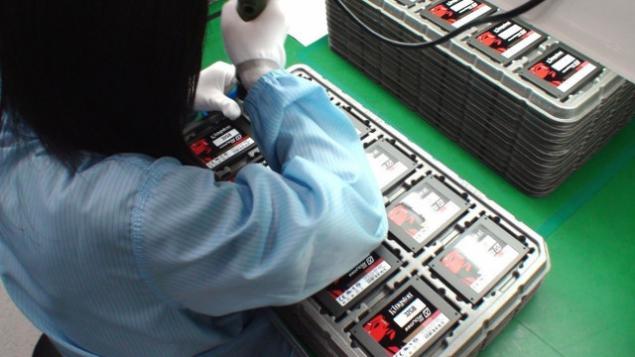
And then it's simple. Discs are packed in original box and shipped to wholesalers. One plant is capable of producing millions, if not tens of millions of CDs per year. And they are all waiting for their moment when they get into your computers and servers.
In the near future I plan to talk about the different types of memory cells in the SSD drives, their advantages and disadvantages. Subscribe to our corporate blog and stay tuned.
Source: habrahabr.ru/company/ua-hosting/blog/222023/