668
How to produce TVs
Report from the production of the blogger victorprofessor
Today we will go to the factory for the production of television sets. The program of inspection - plant for the production of housings, foam packaging, two lines of SMD (surface mounted) with automatic and manual feeding of components, assembly and packaging line.
All this in more detail in 37 photos.
2. Let's start with the production of plastic parts. On the factory bring such plastic pellets.
3. Which are mixed in a special machine.
4. Next, the pipes granulate enters the stamping plant. In the lower right corner of the visible mold.
5. Machines for stamping are set in a mold.
6. This is how it looks. Here you can see the compressed mold, which is filled with liquid plastic.
7. Open the press ready to trim the TV screen, which currently takes a special device.
8. And further transmit frame on a conveyor line.
9. Where to put the logo on her special swab.
10. This next room with more sophisticated presses.
11. All production is fully automated. Typically, 2 person service shop of 6 presses. Intervention in the process is minimal.
12. Then go to the workshop production of the foam.
13. There also are special molds for stamping.
14. First, foamed polystyrene by heat treatment in the machine. Obtain granules with a diameter of about 5 mm.
14. First, foamed polystyrene by heat treatment in the machine. Obtain granules with a diameter of about 5 mm.
16. The molding takes place by blow steam due to sintering pellets with each other.
17. Formulations piping hot.
18. All of this is stored in rows in height up to 5 meters.
19. And now the fun. Line SMD (Surface mounted device) - Surface Mount.
20. At the first stage, the application of solder paste onto the contact pads of the board.
21. At a special tape into the machine mounted components supplied
22. Here comes the installation of components.
23. The process is fully automated, and the equipment is quite versatile and allows for minimal time to adapt to new line card.
24. After the installation is happening mass soldering paste reflow oven.
25. The output of the production line testing phase occurs each board. Marriage is reduced to a minimum.
26. is willing to pay are going to stand.
27. Storage and transportation until the next shop.
28. Here, on the same board mounted larger components.
29. These operations are performed by hand - it is cheaper from an economic point of view.
30. diagnostic equipment assembled boards.
31.
32. And now the final stage - screwdriver assembly of the finished product and send it to the warehouse.
33. The case of the matrix and electronics are going in a few hands, the TV manually transferred through the pipeline.
34. Assembled TV immediately gets on the diagnostic stands, where in a few seconds and check its performance by turning off pass on.
35. On the next line of collected plasma TVs. Unfortunately, we can not see how the process of assembling matrices.
36. The plant mainly young workers, mostly women.
37. After checking the TV is placed in a box, sealed and transported to the warehouse.
That is so simple. ))
Source:
Today we will go to the factory for the production of television sets. The program of inspection - plant for the production of housings, foam packaging, two lines of SMD (surface mounted) with automatic and manual feeding of components, assembly and packaging line.
All this in more detail in 37 photos.
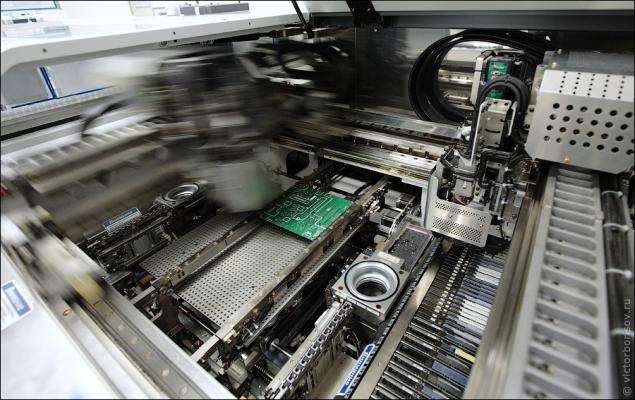
2. Let's start with the production of plastic parts. On the factory bring such plastic pellets.
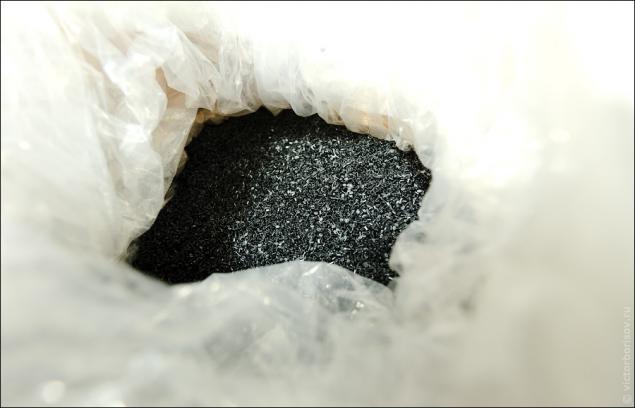
3. Which are mixed in a special machine.
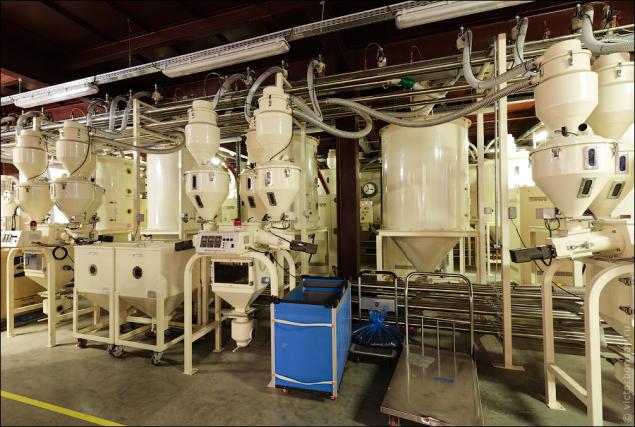
4. Next, the pipes granulate enters the stamping plant. In the lower right corner of the visible mold.

5. Machines for stamping are set in a mold.
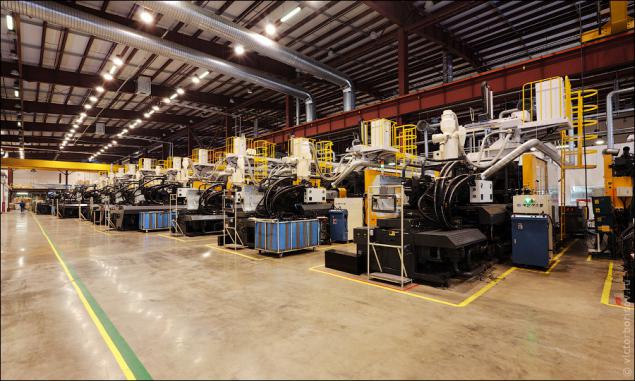
6. This is how it looks. Here you can see the compressed mold, which is filled with liquid plastic.
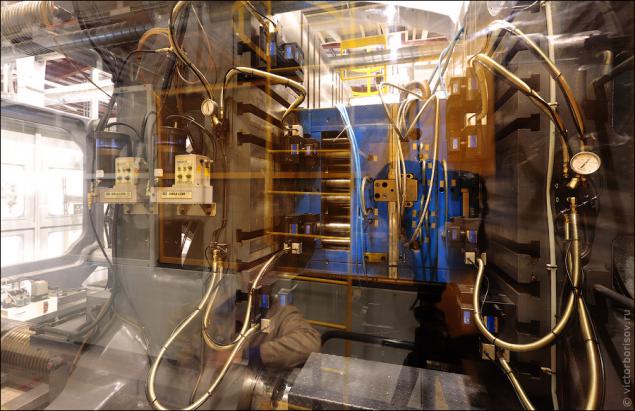
7. Open the press ready to trim the TV screen, which currently takes a special device.
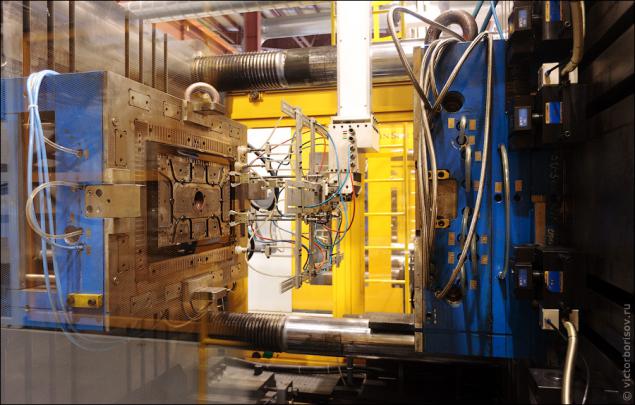
8. And further transmit frame on a conveyor line.

9. Where to put the logo on her special swab.
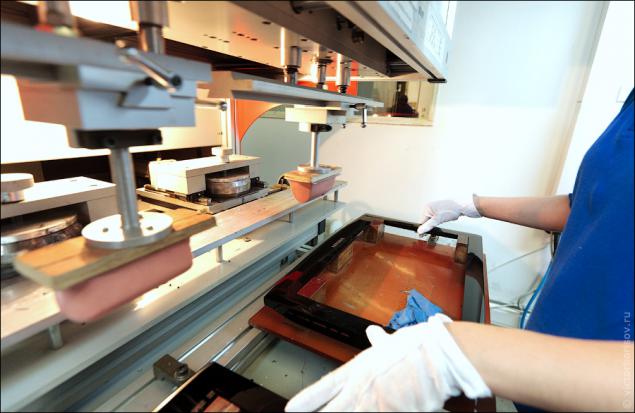
10. This next room with more sophisticated presses.
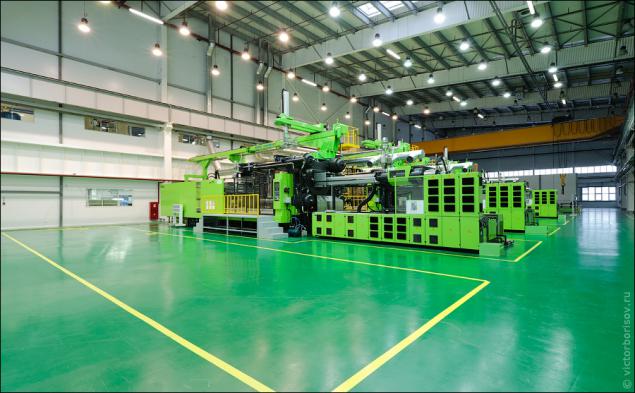
11. All production is fully automated. Typically, 2 person service shop of 6 presses. Intervention in the process is minimal.
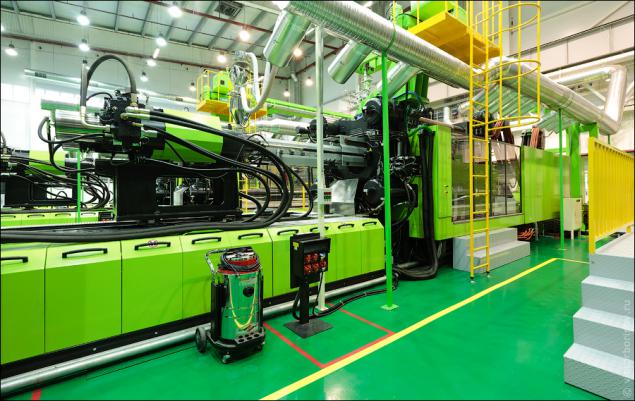
12. Then go to the workshop production of the foam.
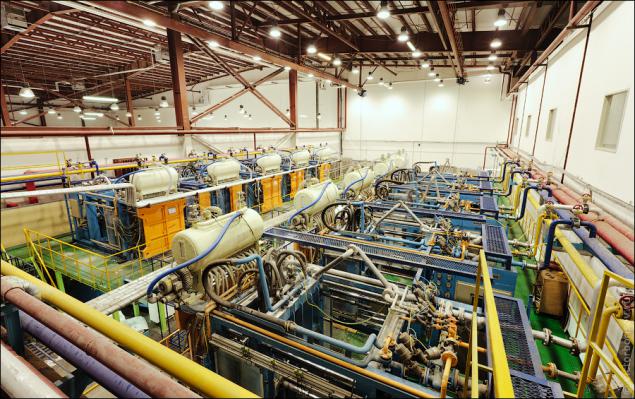
13. There also are special molds for stamping.
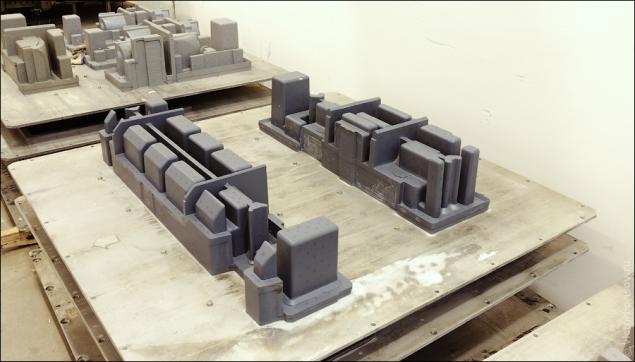
14. First, foamed polystyrene by heat treatment in the machine. Obtain granules with a diameter of about 5 mm.
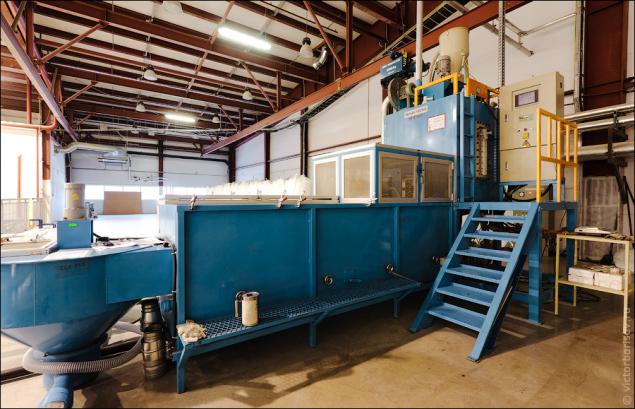
14. First, foamed polystyrene by heat treatment in the machine. Obtain granules with a diameter of about 5 mm.
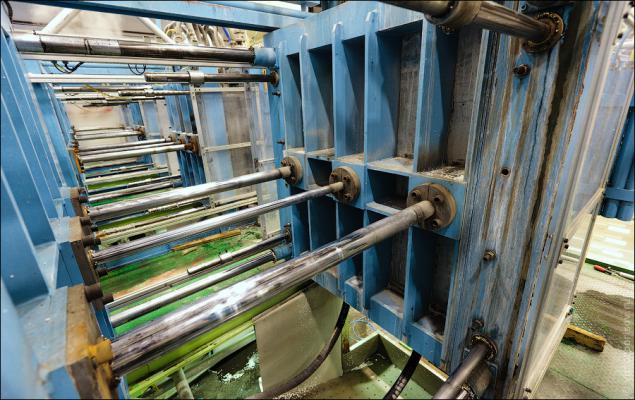
16. The molding takes place by blow steam due to sintering pellets with each other.
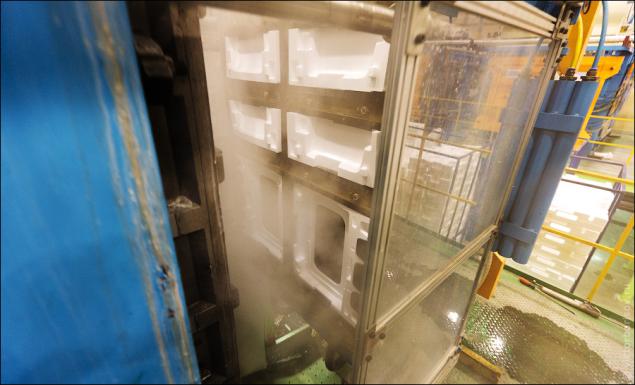
17. Formulations piping hot.
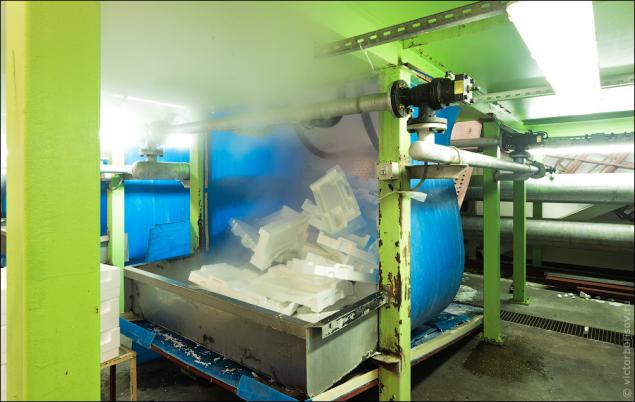
18. All of this is stored in rows in height up to 5 meters.
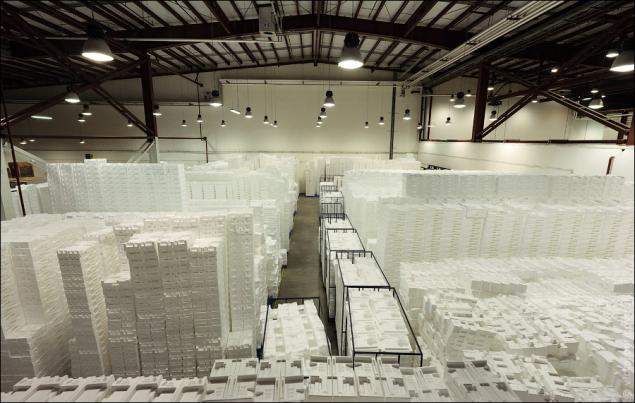
19. And now the fun. Line SMD (Surface mounted device) - Surface Mount.
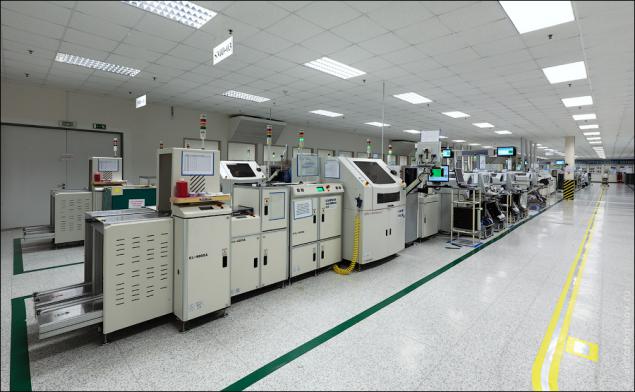
20. At the first stage, the application of solder paste onto the contact pads of the board.
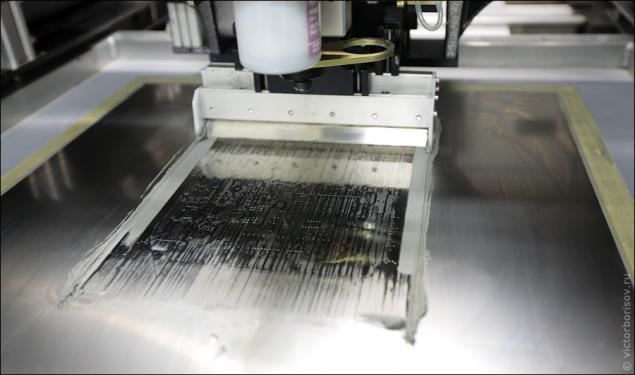
21. At a special tape into the machine mounted components supplied
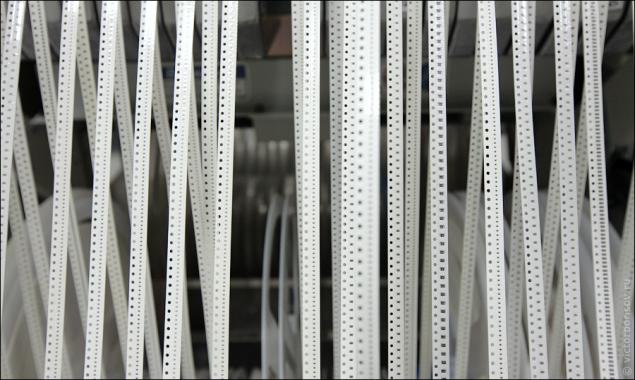
22. Here comes the installation of components.
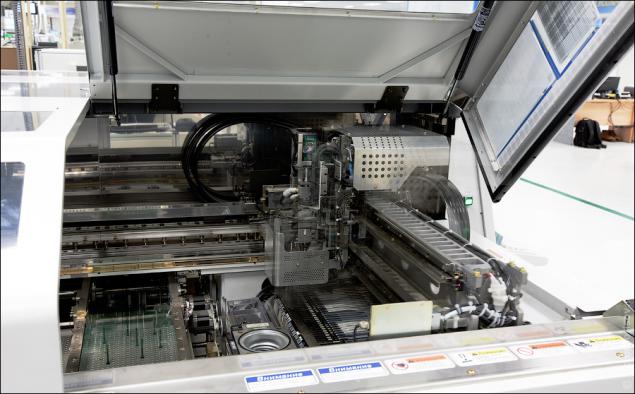
23. The process is fully automated, and the equipment is quite versatile and allows for minimal time to adapt to new line card.
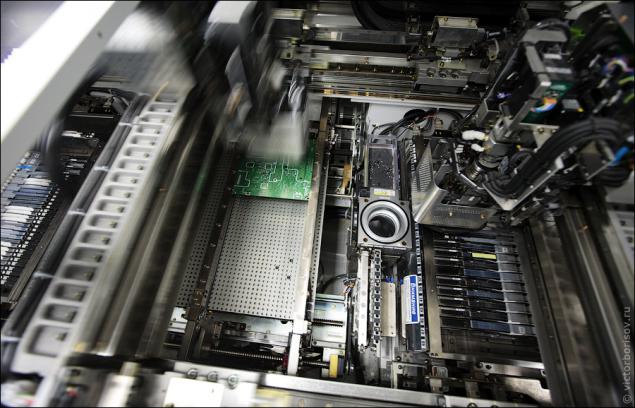
24. After the installation is happening mass soldering paste reflow oven.
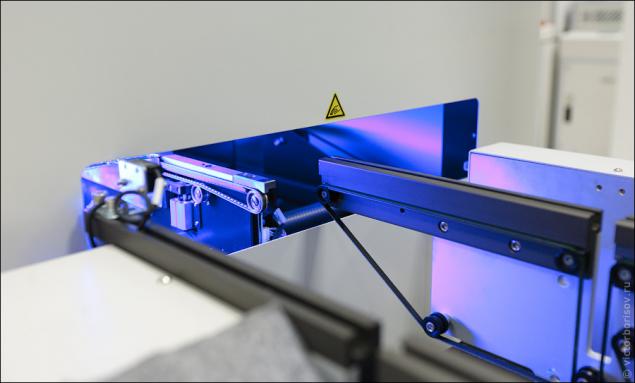
25. The output of the production line testing phase occurs each board. Marriage is reduced to a minimum.
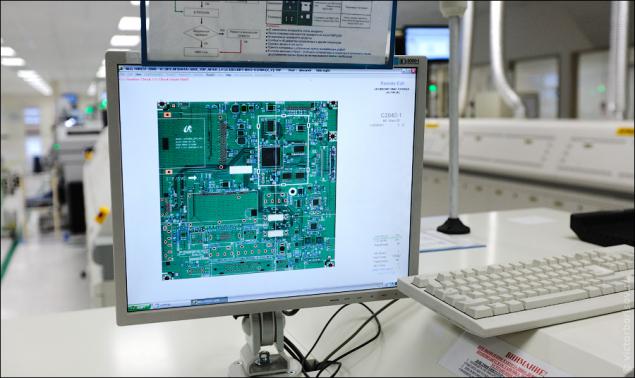
26. is willing to pay are going to stand.
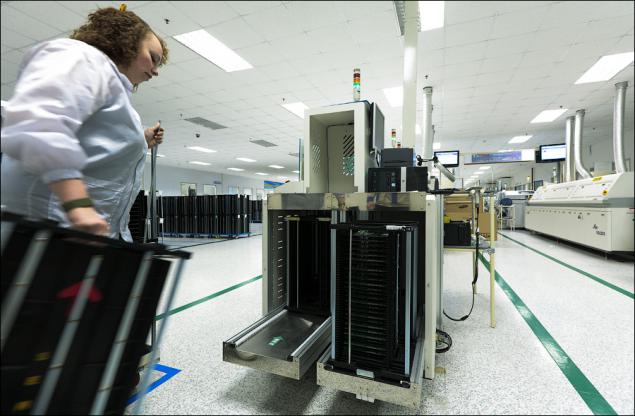
27. Storage and transportation until the next shop.
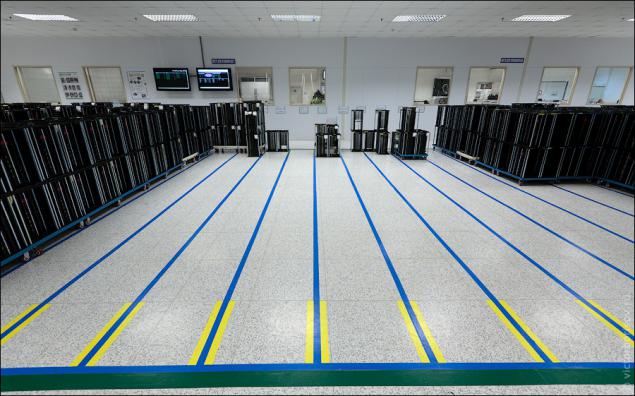
28. Here, on the same board mounted larger components.
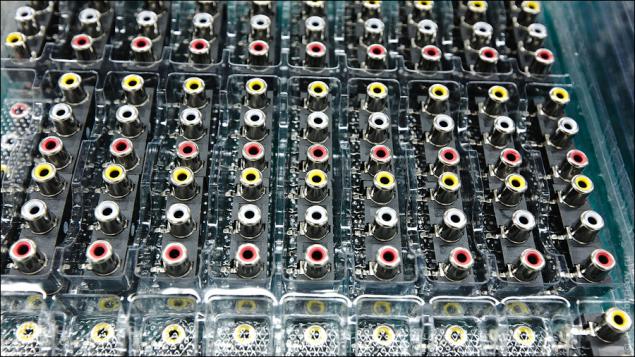
29. These operations are performed by hand - it is cheaper from an economic point of view.
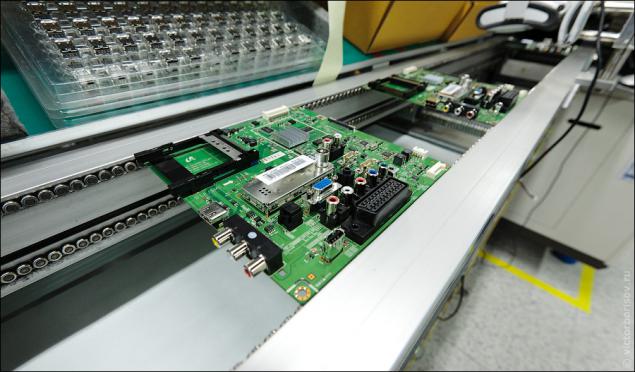
30. diagnostic equipment assembled boards.
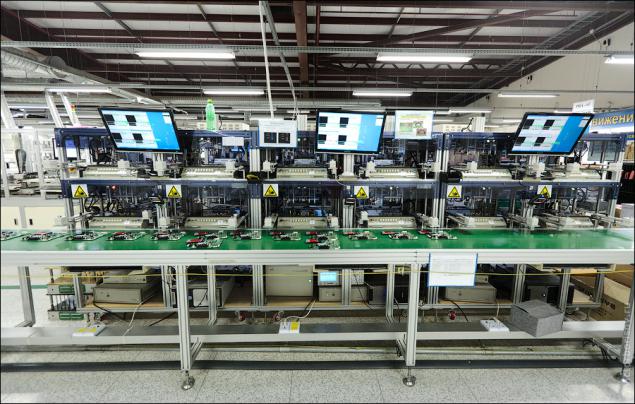
31.
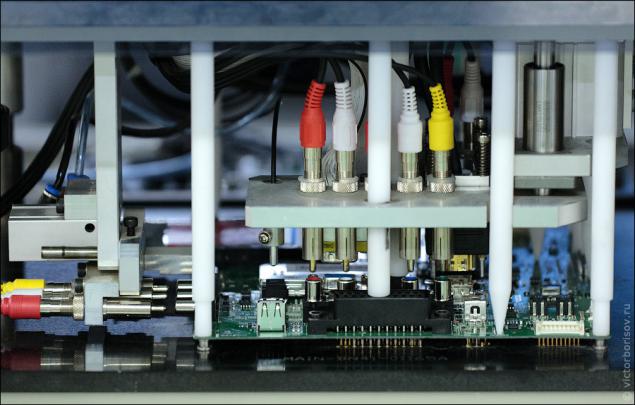
32. And now the final stage - screwdriver assembly of the finished product and send it to the warehouse.
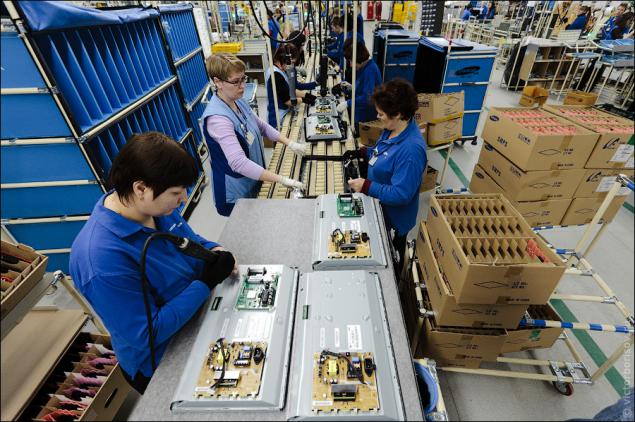
33. The case of the matrix and electronics are going in a few hands, the TV manually transferred through the pipeline.
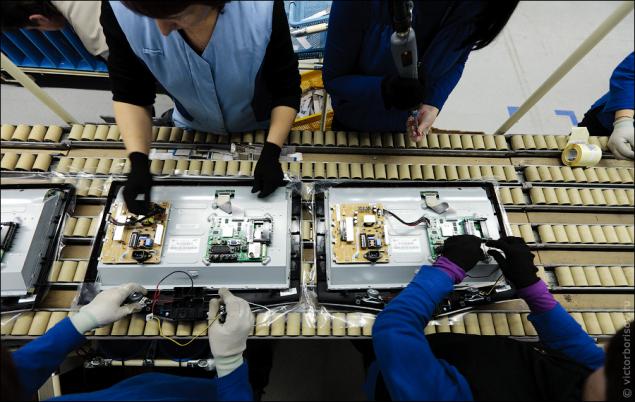
34. Assembled TV immediately gets on the diagnostic stands, where in a few seconds and check its performance by turning off pass on.
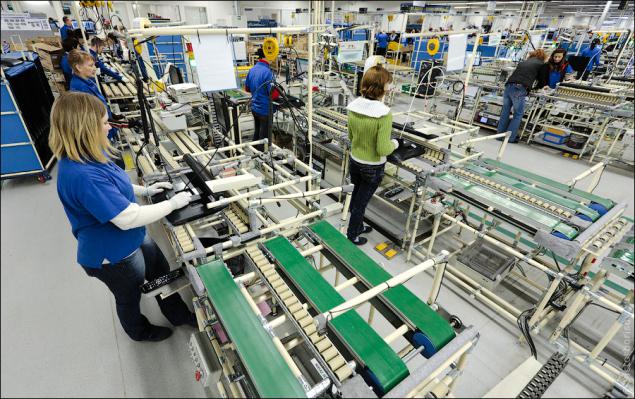
35. On the next line of collected plasma TVs. Unfortunately, we can not see how the process of assembling matrices.
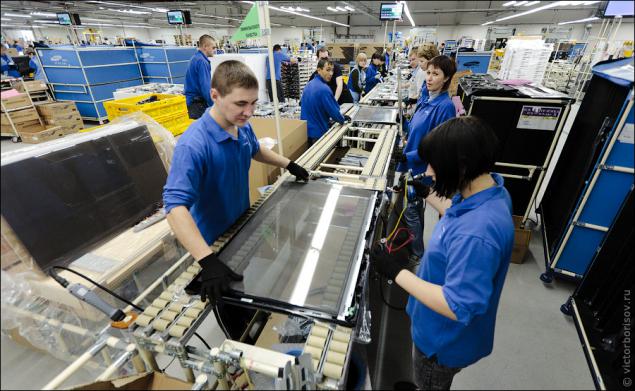
36. The plant mainly young workers, mostly women.
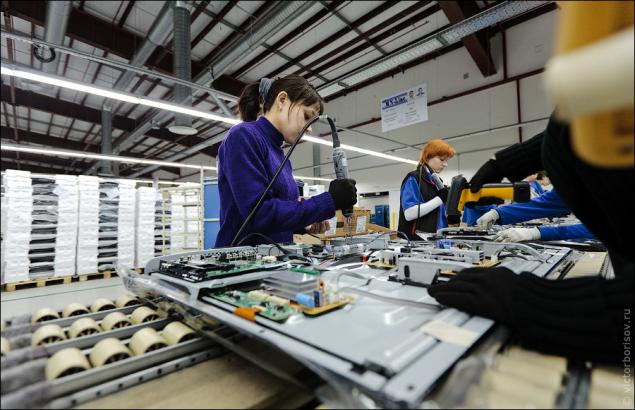
37. After checking the TV is placed in a box, sealed and transported to the warehouse.
That is so simple. ))
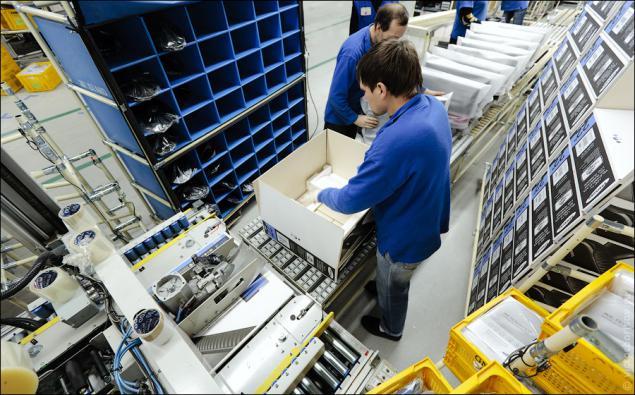
Source: