960
How do Gazelle
59 photos
"Blog trucker" continues to publish photo reports from auto plants successfully operating in Russia. Today, our readers have a unique opportunity to walk through the shops of one of the oldest plants of our country. We will visit the conveyor Gorky Automobile Plant and see how collected the most popular commercial vehicles in Russia.
1. To view the pictures was not too boring, I try to dilute his PHOTOS small excursion into the past and present of gas.
2. In January of this year marked 80 years since the founding of the Gorky Automobile Plant - the largest enterprise of the Russian automotive industry occupying a leading position in the domestic market for commercial vehicles.
3. The automobile plant was built in 18 months, came into operation January 1, 1932, and on January 29 with the first truck rolled off the line - "lorry" GAZ-AA. Since then, the plant has given the country millions of available cars, trucks equipped the agriculture, the army provided special military equipment, tanks and armored vehicles. In October 2011, descended from the conveyor of GAZ 18 millionth car.
4. As 80 years ago, the most massive car in the Automobile line, remains the same as lorry. The successful combination of capacity and size give it timeless. All upgrades and improvements do not change the main essence of Gazelle.
5. And our tour, as usual, originates from the welding shop. It was here, on the assembly line welding shop, we can already see the first outlines of the cabin, for the future of the best-selling small business.
7. On the assembly line has more than 120 industrial welding robots, the German company KUKA.
8. The first Gazelle left the assembly line in 1994. You could say that thanks to the launch of the car in the series, in the difficult conditions of the transition period, managed to keep the team and the productive capacity of the plant.
9. And it is no exaggeration to say that it Gazelle, was one of those impulses which marked the beginning of the development of the entire economy.
10. Work on the improvement and modernization of the Gazelle is permanent. In order to improve the corrosion resistance of the body, plant engineers have acquired their departure deadline taxis who worked in St. Petersburg and Nizhny Novgorod. The machines were disassembled to the last screw, and sawed up and down.
11. The result of this work was the introduction of double-sided galvanized forty-seven parts of the body. The pictures unpainted cabin clearly visible these details.
12. Let us return to the conveyor. Note, in the hands of the women's press, with which she beats tasting rooms cab.
13. Happy owners, look in their PTAs. Maybe this is the number stamped on your machine?
14. At this stage, the future car prescribe quality passport, which follows him to the end of the conveyor
15. After each operation in the passport and put a note the change area to carry out work on this car.
16. Polishing is the finishing touch, and the cabin leaves the welding shop.
17. We will also move into the hall of the main assembly line. First, let's see how the cabin equipped with all the necessary machines.
18. In 2011, the Gazelle has a new instrument panel. There was more space to store personal belongings and pleasant things as cup holders, cigarette lighter, ashtray and additional outlet to 12V.
19. Plot inserts windshields.
20. The operator applies adhesive to the windshield.
21. Do not have time to blink an eye as glass takes its original position.
22. Krepjat wipers. By the way the former owners had a lot of complaints about the work of this unit. Gas and now take into account the wishes of all the cars set gear motors firm «BOSCH».
23. With the "Suite" everything else is added to ABS, branded CD MP3 audio system with control buttons on the steering wheel, powered mirrors, USB connector, air conditioning, preheater.
24. Immediately, near the assembly line is a section of practical training. It is worth noting that the average wage in Gaza in 2011, is about 24 thousand rubles. In the car factory employs 25 thousand people.
25. In the meantime, we come to the most interesting part of our trip. A branch of the conveyor on which of the components is going a whole. Today, there is a conveyor assembly of GAZ-3302 - Business Gazelle. Yet bare frame, waiting for their turn on the conveyor.
26. One of the first parts are mounted on a frame spring.
27. Two pneumatic cylinder is compressed to a size number of openings, and spring - on the basis of!
28. Most front.
29. Rear axle.
30. Ladders rear axle.
31. The stabilizer and shock absorber rear axle. Since 2011, the Gazelle put the dampers on the company «Sachs».
32. As from 2011, all vehicles put on the maintenance free cardan shafts, the Turkish company «Tirsan Kardan», FORD, too, puts products on their cars this company.
33. Up to this point on the conveyor frame is moved in the upside. After installing the muffler and fuel tank, it will make a revolution around its axis.
35. We also continue to follow. From above, the conveyor motors swim.
36. Who set the Gazelle, gasoline: UMP - 4216-40 and diesel: MMZ D-245 and Cummins ISF (pictured).
37. Every two and a half minutes coming off the assembly line brand new Gazelle. Thus, it is difficult to calculate how long it takes each transaction.
39. Perhaps our colleagues reproach me for lack of portrait photos, but by God, the rhythm of conveyor gas will not let me even for a moment distract workers from their case.
40. Who is on the line, is fitted as standard automotive gas equipment company «OMVL» (Italy).
41. Just to Verkhoturov sailing cabin.
42. Two minutes and the cabin standing on the frame.
43. The rhythm of the assembly line is so high that sometimes I just do not have time to monitor workers. But it was clear that with every movement on the car there were new details.
44. There are already a radiator and headlights
45. Second floor assembly plant used solely for the purpose of transportation of components and assemblies to the assembly point. Top with an accuracy of a second hand wheel down.
46. More time, and the wheels are already on the vehicle.
47. The local gas station.
48. Each brand new car, gets ten gallons of fuel.
49. bagels.
50. Install the bumper. Perhaps the most noticeable difference Business Gazelle series, from its predecessor. With his appearance had improved visual perception of the car, and significantly reduce the technological gap.
51. Body. Since 2011, the body held a 100% priming sides and base platform by cathodic electrodeposition.
52. The metal sleeve, with its help, in the braking system of the car creates a vacuum at the same time served the brake fluid.
53. The car is on wheels. Who will be the first start the engine, then the car is already moving under its own power.
54. In the enclosed space passes running - three-kilometer run.
55. Freshly car arrived at the point of acceptance of the quality department.
56. Specialist conducts a final inspection, but that's not all.
57. In conclusion, the car gets into the camera body to check for leaks.
58. Ready to ship cars to buyers waiting for transporters.
59. For the promotion and conduct of tours "Blog trucker" expresses deep gratitude to the press secretary of the Gorky Automobile Plant Erasova Paul.
© «Blog trucker» 08.04.2012
Source:
"Blog trucker" continues to publish photo reports from auto plants successfully operating in Russia. Today, our readers have a unique opportunity to walk through the shops of one of the oldest plants of our country. We will visit the conveyor Gorky Automobile Plant and see how collected the most popular commercial vehicles in Russia.
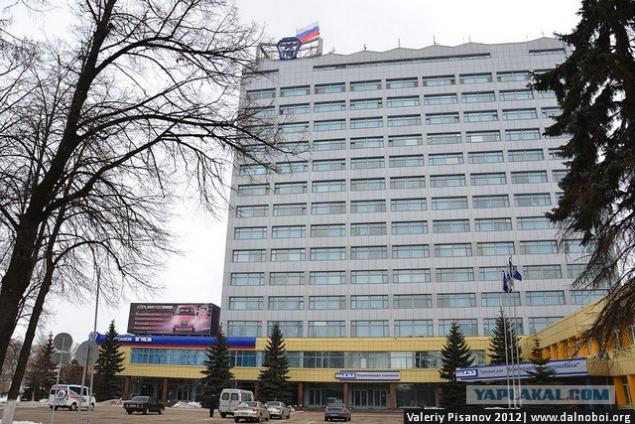
1. To view the pictures was not too boring, I try to dilute his PHOTOS small excursion into the past and present of gas.
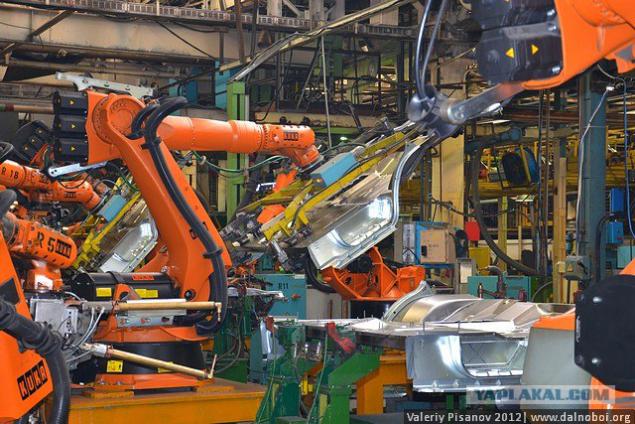
2. In January of this year marked 80 years since the founding of the Gorky Automobile Plant - the largest enterprise of the Russian automotive industry occupying a leading position in the domestic market for commercial vehicles.
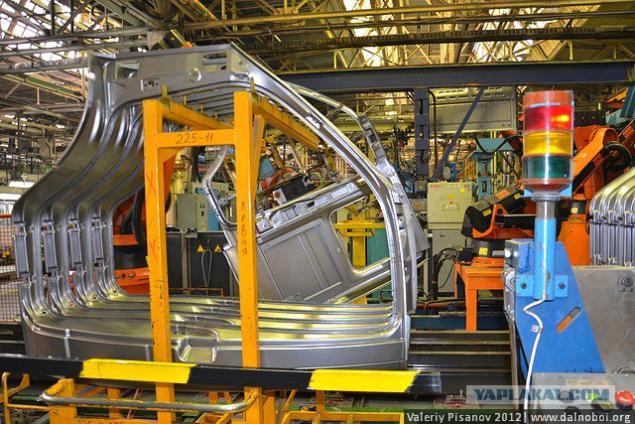
3. The automobile plant was built in 18 months, came into operation January 1, 1932, and on January 29 with the first truck rolled off the line - "lorry" GAZ-AA. Since then, the plant has given the country millions of available cars, trucks equipped the agriculture, the army provided special military equipment, tanks and armored vehicles. In October 2011, descended from the conveyor of GAZ 18 millionth car.
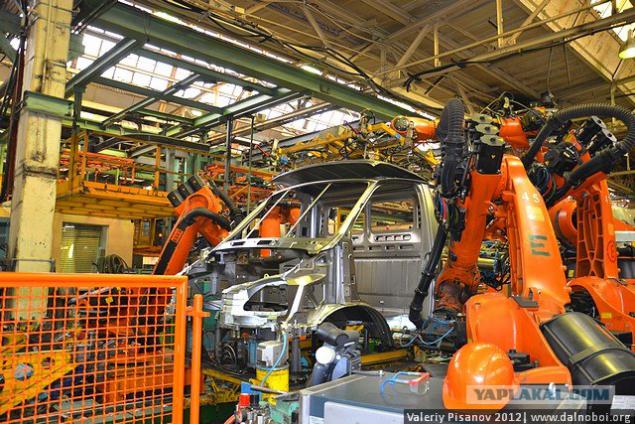
4. As 80 years ago, the most massive car in the Automobile line, remains the same as lorry. The successful combination of capacity and size give it timeless. All upgrades and improvements do not change the main essence of Gazelle.
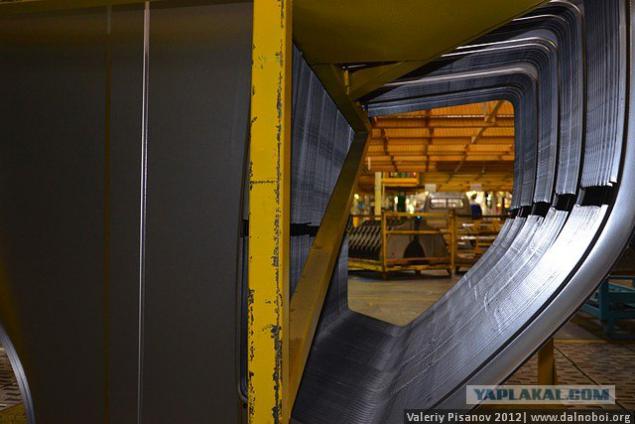
5. And our tour, as usual, originates from the welding shop. It was here, on the assembly line welding shop, we can already see the first outlines of the cabin, for the future of the best-selling small business.
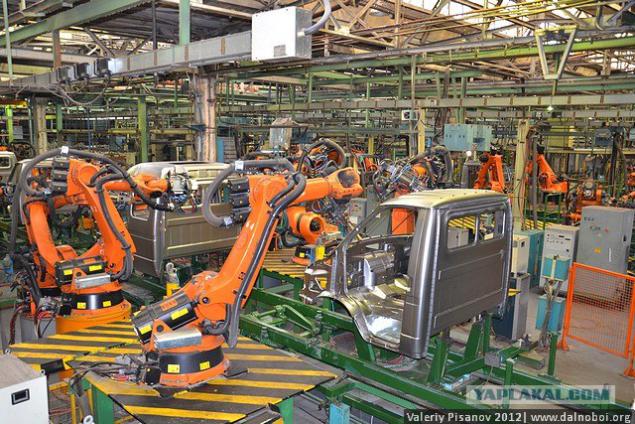
7. On the assembly line has more than 120 industrial welding robots, the German company KUKA.
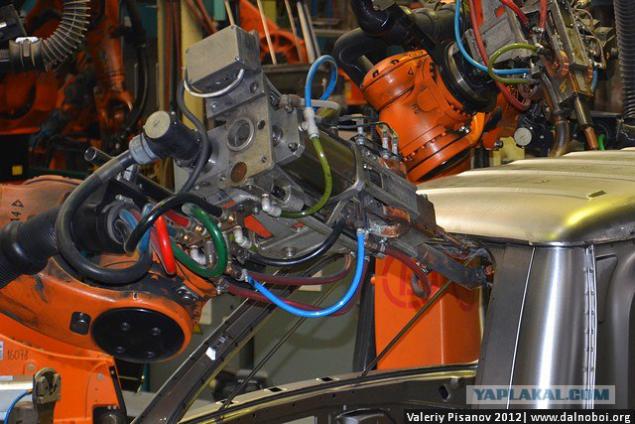
8. The first Gazelle left the assembly line in 1994. You could say that thanks to the launch of the car in the series, in the difficult conditions of the transition period, managed to keep the team and the productive capacity of the plant.
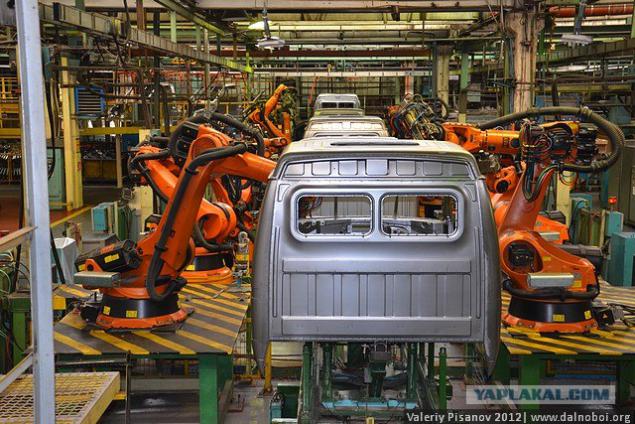
9. And it is no exaggeration to say that it Gazelle, was one of those impulses which marked the beginning of the development of the entire economy.
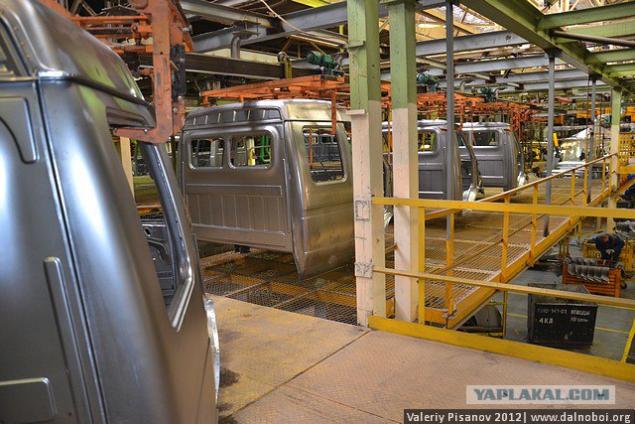
10. Work on the improvement and modernization of the Gazelle is permanent. In order to improve the corrosion resistance of the body, plant engineers have acquired their departure deadline taxis who worked in St. Petersburg and Nizhny Novgorod. The machines were disassembled to the last screw, and sawed up and down.
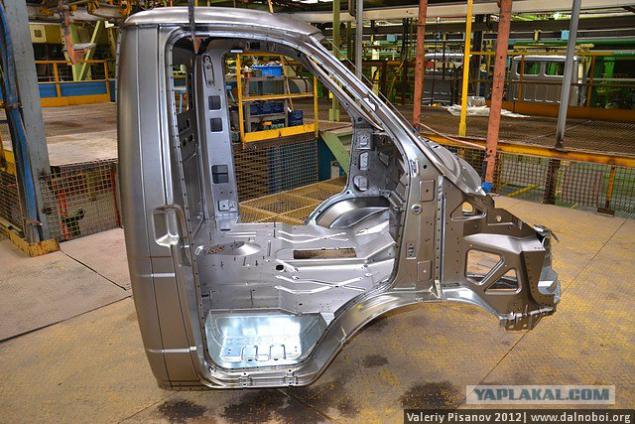
11. The result of this work was the introduction of double-sided galvanized forty-seven parts of the body. The pictures unpainted cabin clearly visible these details.
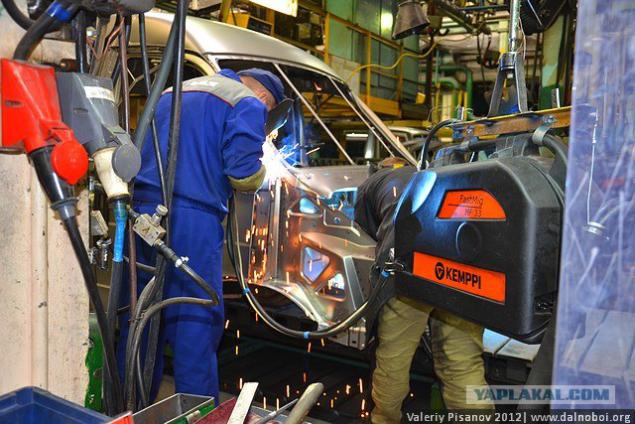
12. Let us return to the conveyor. Note, in the hands of the women's press, with which she beats tasting rooms cab.
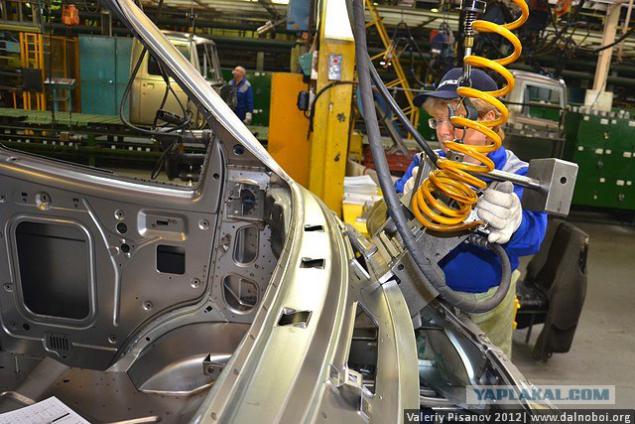
13. Happy owners, look in their PTAs. Maybe this is the number stamped on your machine?
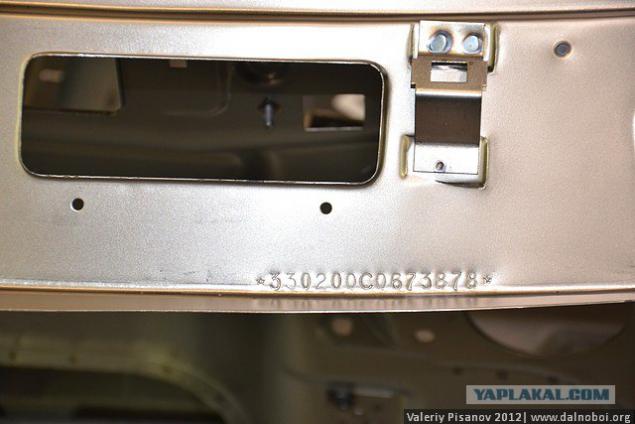
14. At this stage, the future car prescribe quality passport, which follows him to the end of the conveyor
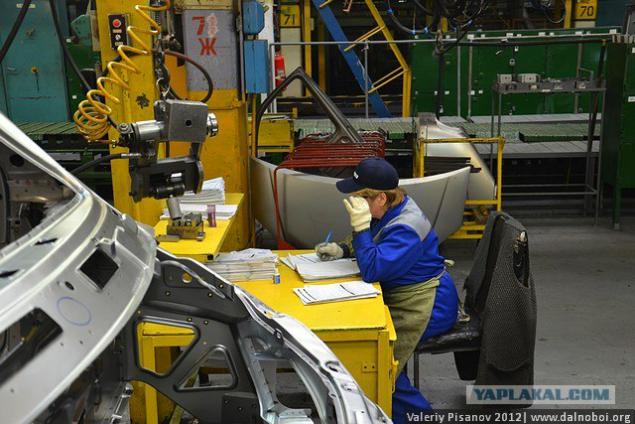
15. After each operation in the passport and put a note the change area to carry out work on this car.
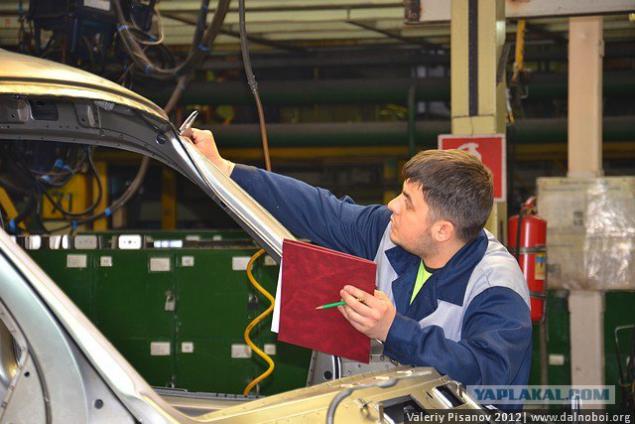
16. Polishing is the finishing touch, and the cabin leaves the welding shop.
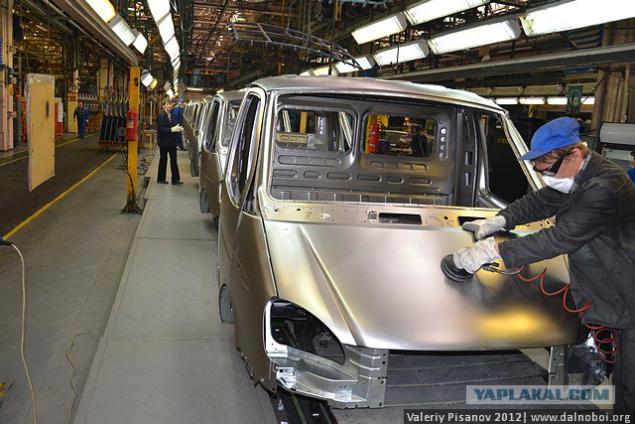
17. We will also move into the hall of the main assembly line. First, let's see how the cabin equipped with all the necessary machines.
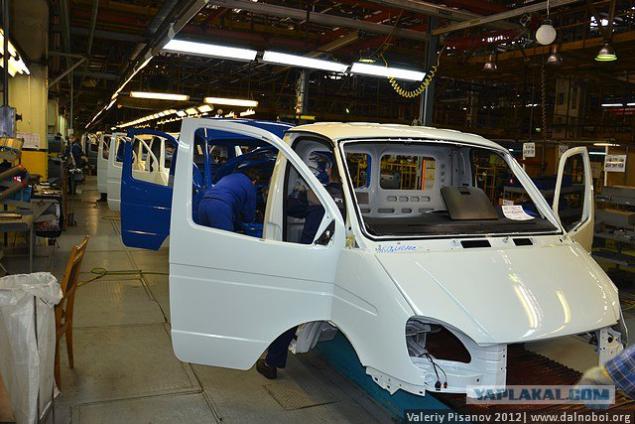
18. In 2011, the Gazelle has a new instrument panel. There was more space to store personal belongings and pleasant things as cup holders, cigarette lighter, ashtray and additional outlet to 12V.
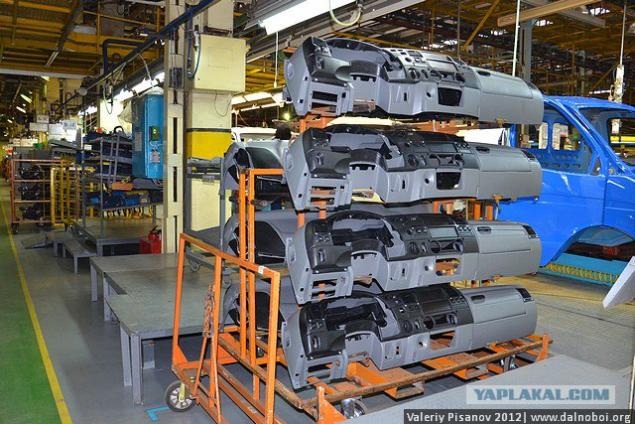
19. Plot inserts windshields.
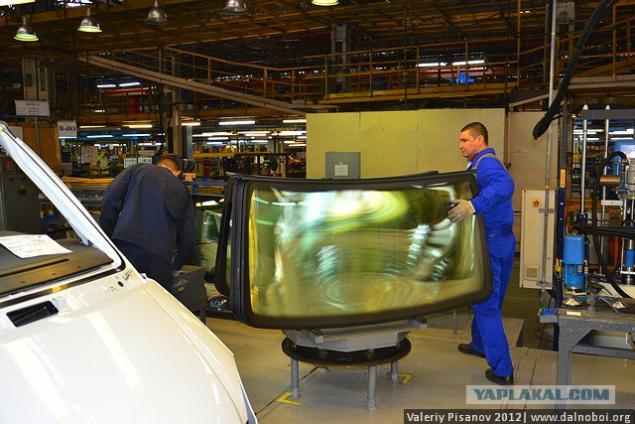
20. The operator applies adhesive to the windshield.
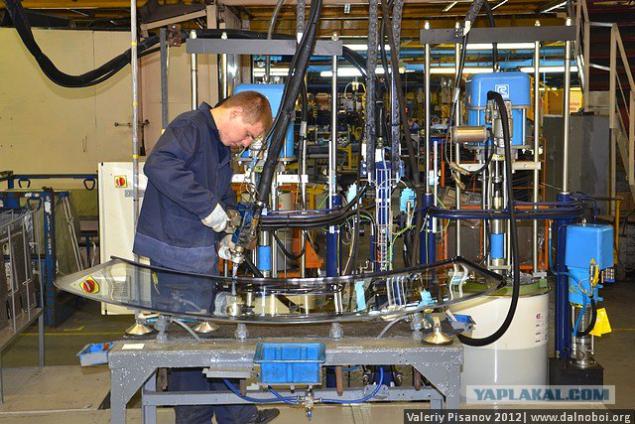
21. Do not have time to blink an eye as glass takes its original position.
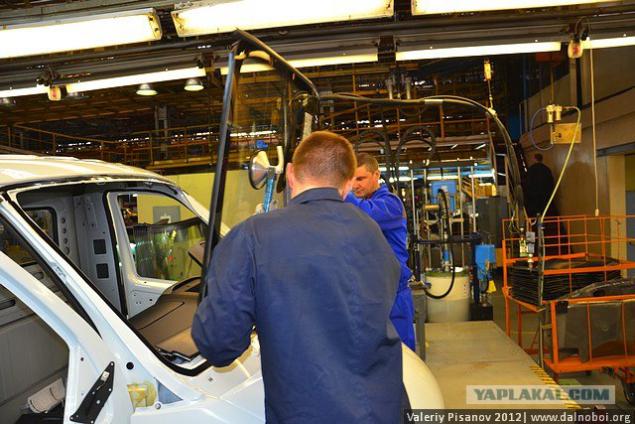
22. Krepjat wipers. By the way the former owners had a lot of complaints about the work of this unit. Gas and now take into account the wishes of all the cars set gear motors firm «BOSCH».
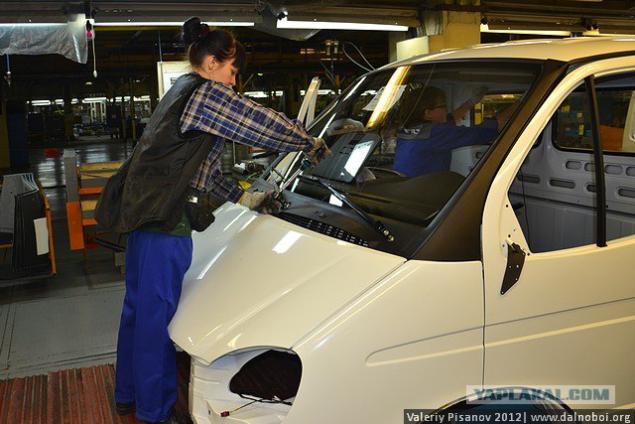
23. With the "Suite" everything else is added to ABS, branded CD MP3 audio system with control buttons on the steering wheel, powered mirrors, USB connector, air conditioning, preheater.
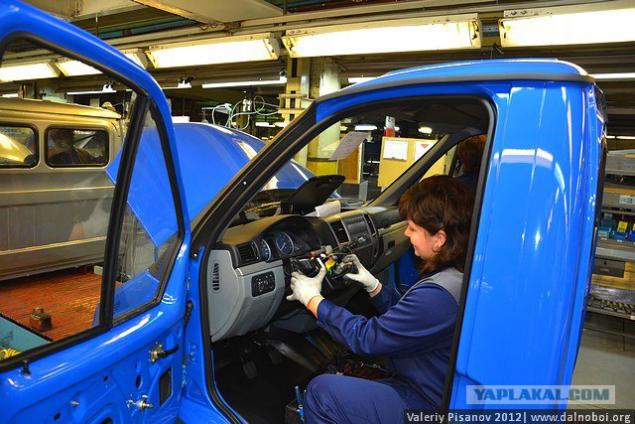
24. Immediately, near the assembly line is a section of practical training. It is worth noting that the average wage in Gaza in 2011, is about 24 thousand rubles. In the car factory employs 25 thousand people.
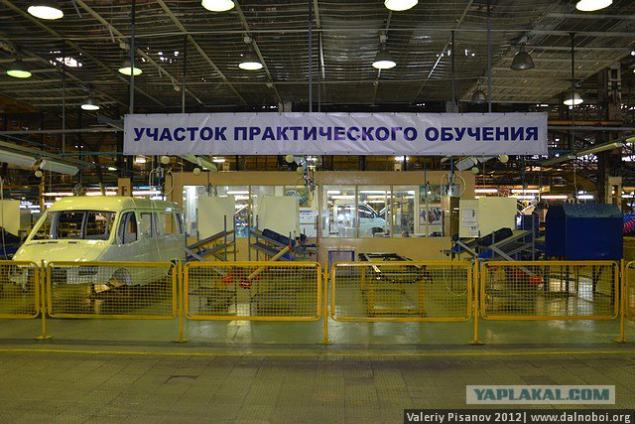
25. In the meantime, we come to the most interesting part of our trip. A branch of the conveyor on which of the components is going a whole. Today, there is a conveyor assembly of GAZ-3302 - Business Gazelle. Yet bare frame, waiting for their turn on the conveyor.
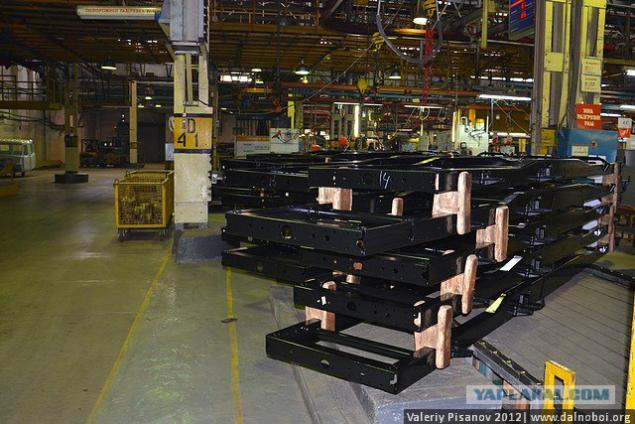
26. One of the first parts are mounted on a frame spring.
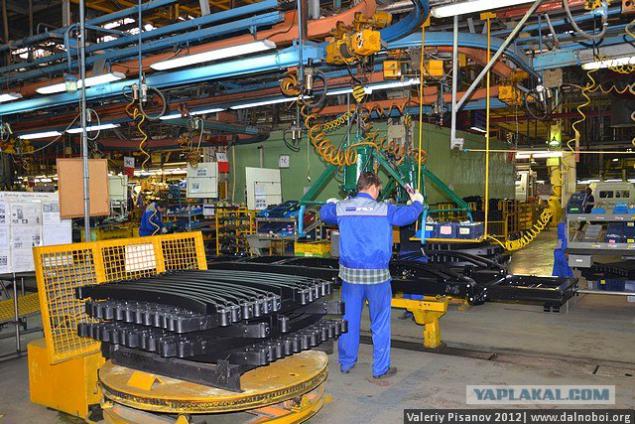
27. Two pneumatic cylinder is compressed to a size number of openings, and spring - on the basis of!
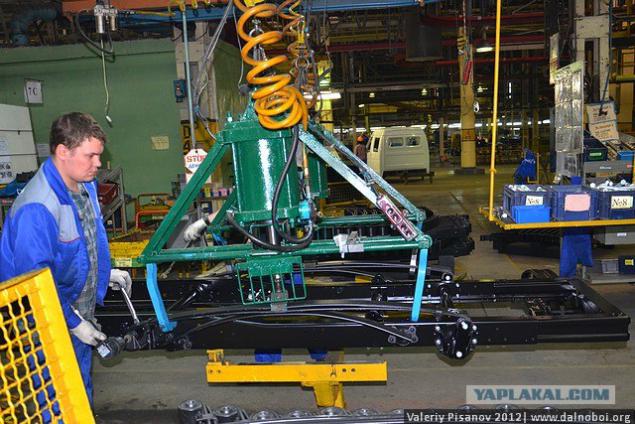
28. Most front.
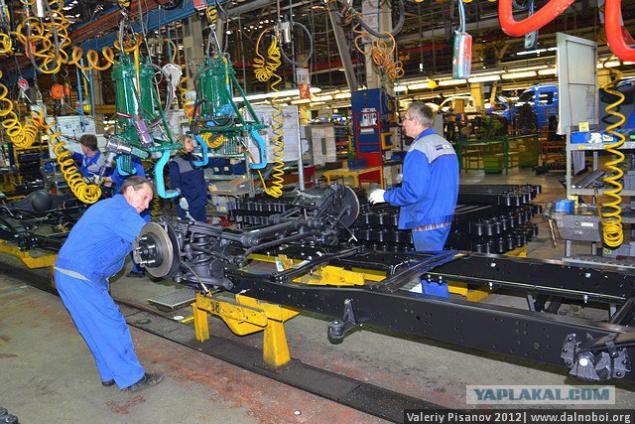
29. Rear axle.
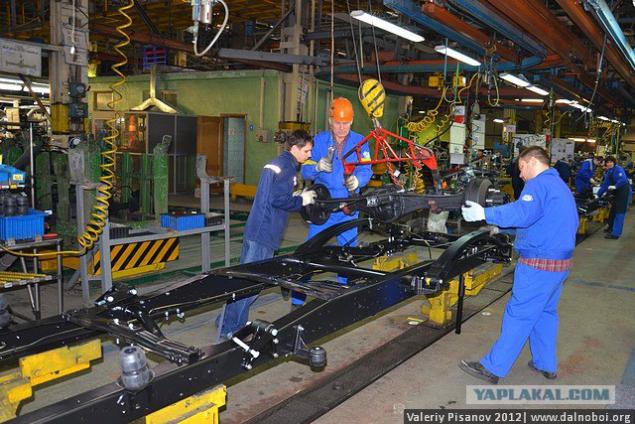
30. Ladders rear axle.
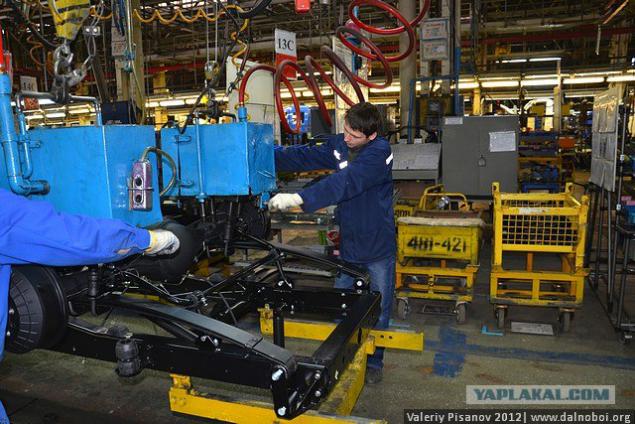
31. The stabilizer and shock absorber rear axle. Since 2011, the Gazelle put the dampers on the company «Sachs».
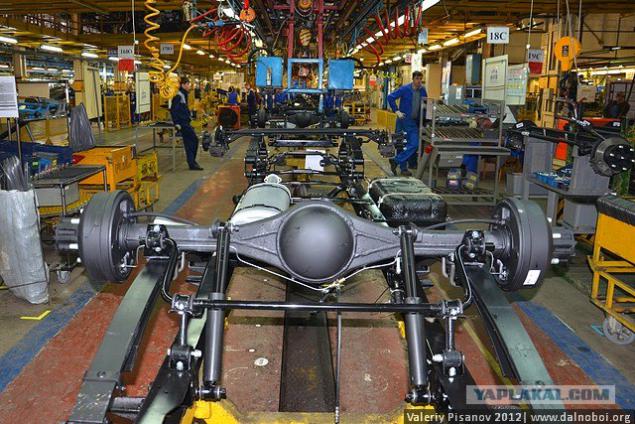
32. As from 2011, all vehicles put on the maintenance free cardan shafts, the Turkish company «Tirsan Kardan», FORD, too, puts products on their cars this company.
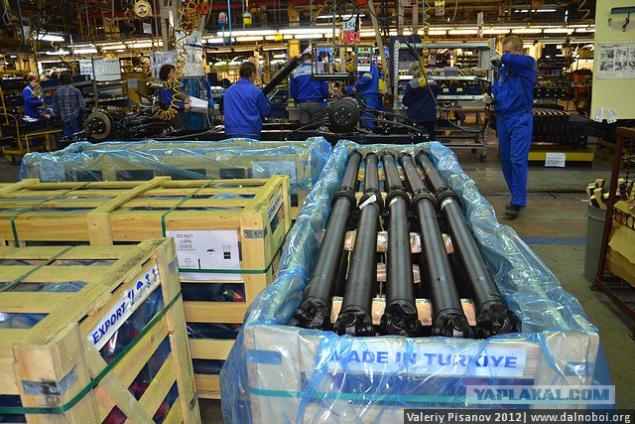
33. Up to this point on the conveyor frame is moved in the upside. After installing the muffler and fuel tank, it will make a revolution around its axis.
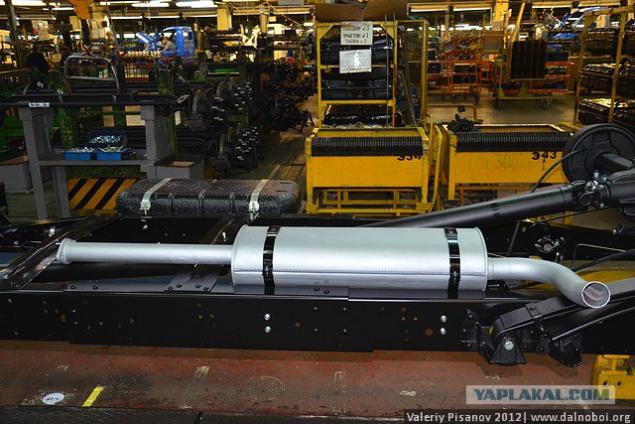
35. We also continue to follow. From above, the conveyor motors swim.
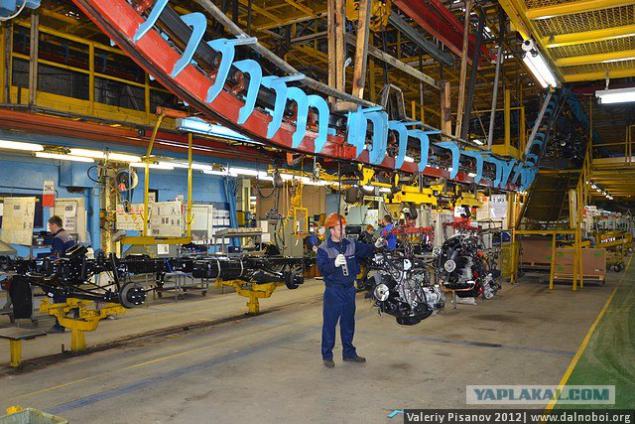
36. Who set the Gazelle, gasoline: UMP - 4216-40 and diesel: MMZ D-245 and Cummins ISF (pictured).
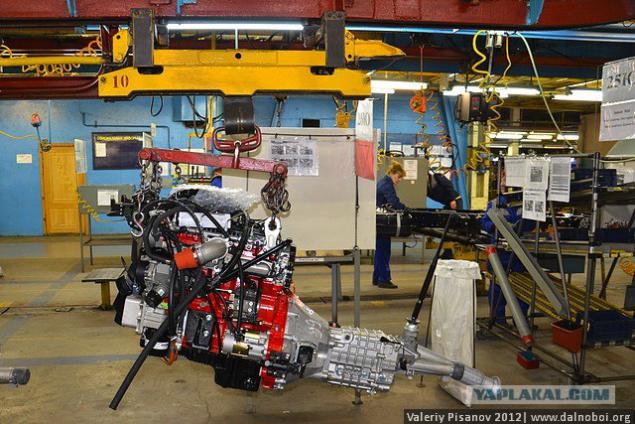
37. Every two and a half minutes coming off the assembly line brand new Gazelle. Thus, it is difficult to calculate how long it takes each transaction.
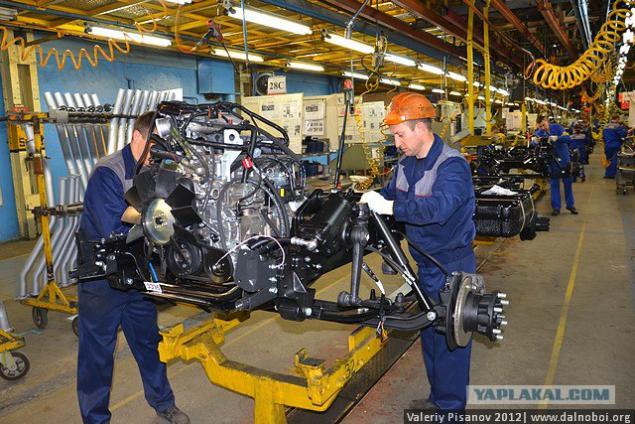
39. Perhaps our colleagues reproach me for lack of portrait photos, but by God, the rhythm of conveyor gas will not let me even for a moment distract workers from their case.
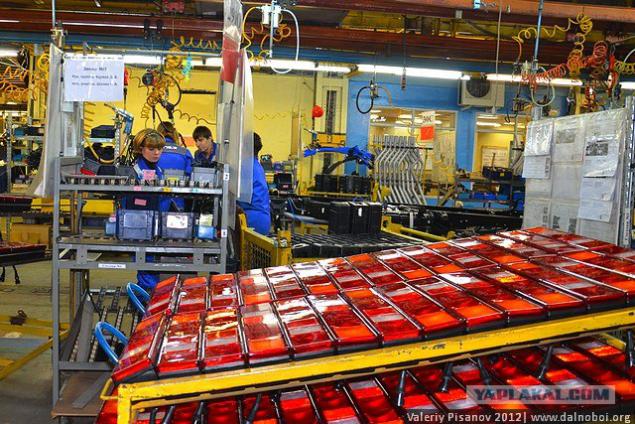
40. Who is on the line, is fitted as standard automotive gas equipment company «OMVL» (Italy).
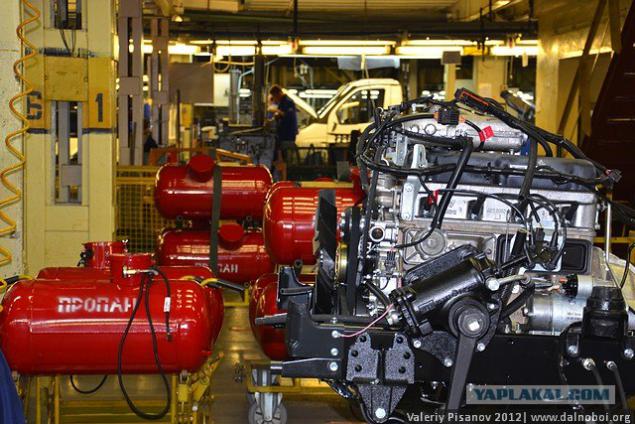
41. Just to Verkhoturov sailing cabin.
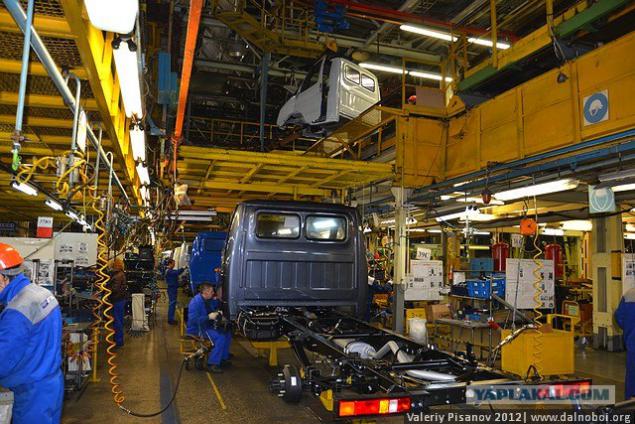
42. Two minutes and the cabin standing on the frame.
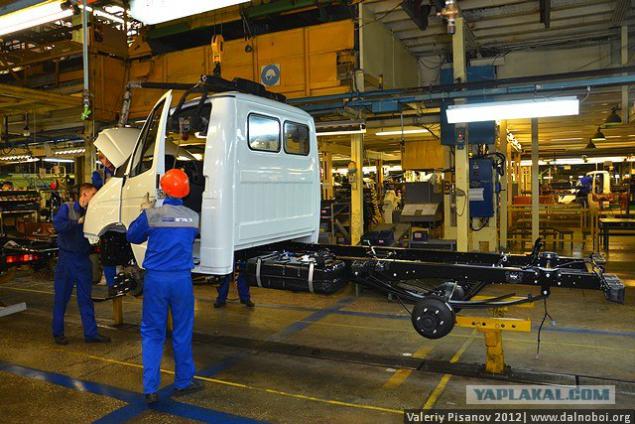
43. The rhythm of the assembly line is so high that sometimes I just do not have time to monitor workers. But it was clear that with every movement on the car there were new details.
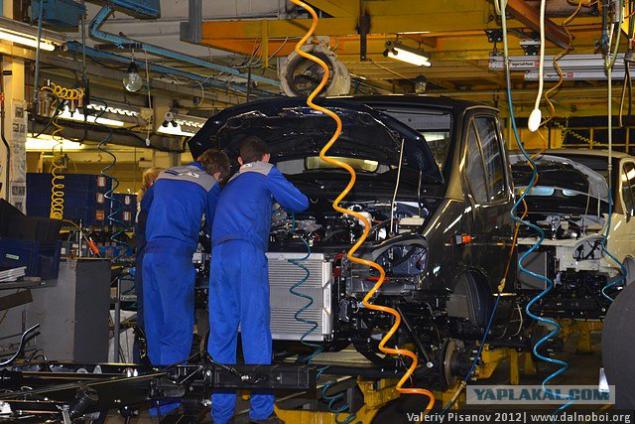
44. There are already a radiator and headlights
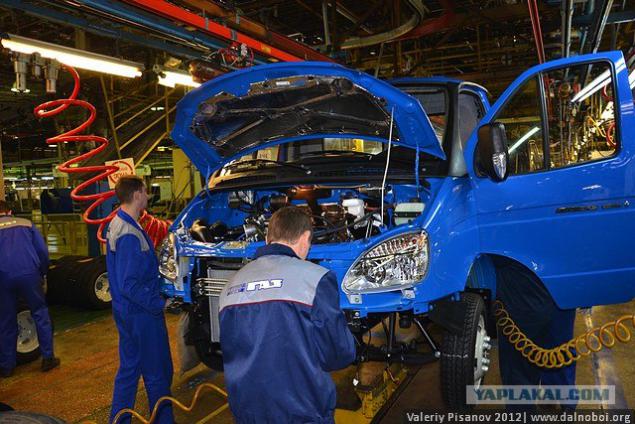
45. Second floor assembly plant used solely for the purpose of transportation of components and assemblies to the assembly point. Top with an accuracy of a second hand wheel down.
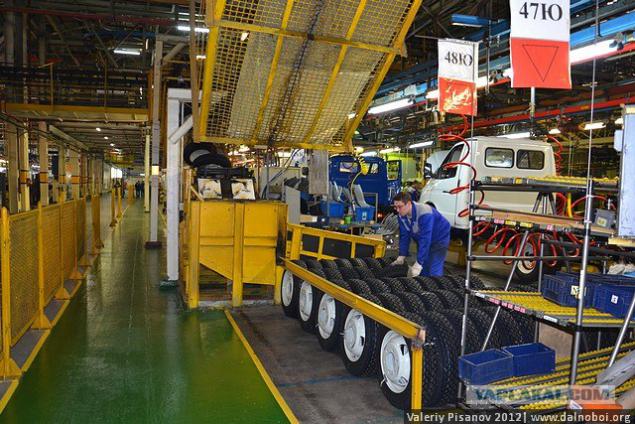
46. More time, and the wheels are already on the vehicle.
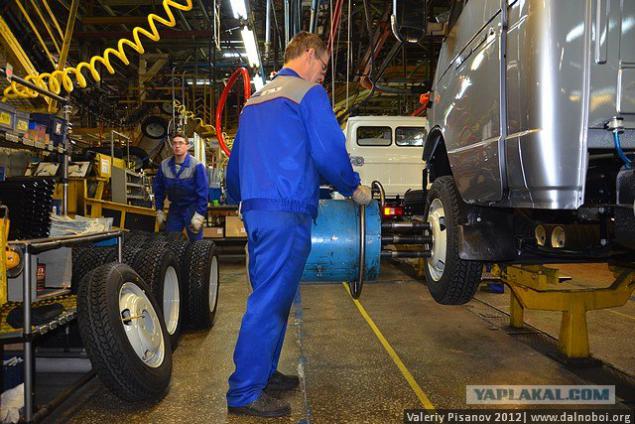
47. The local gas station.
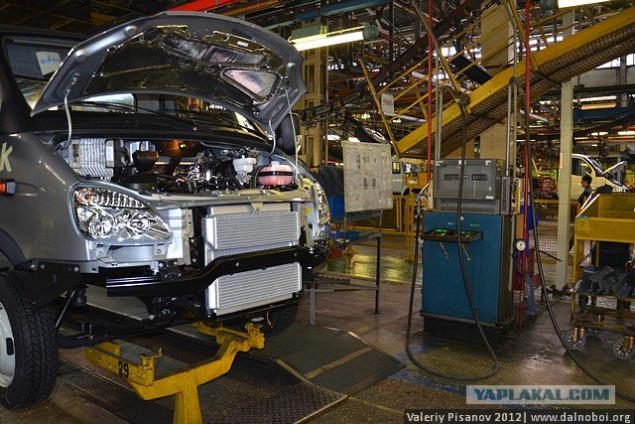
48. Each brand new car, gets ten gallons of fuel.
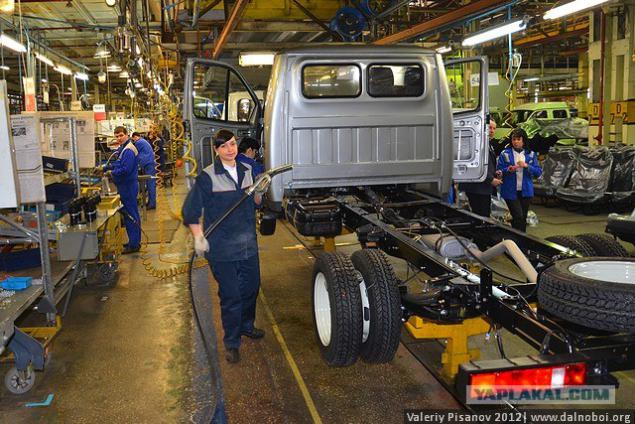
49. bagels.
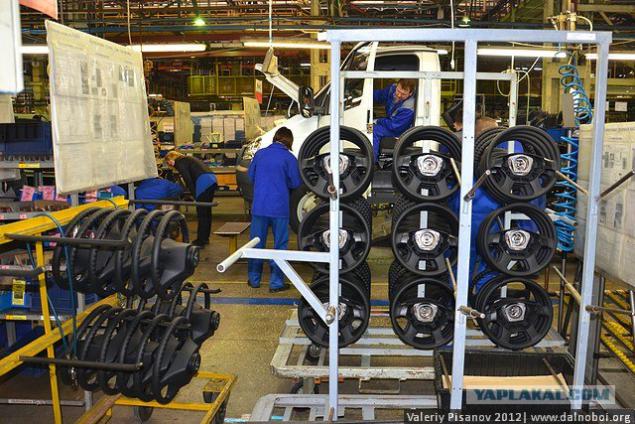
50. Install the bumper. Perhaps the most noticeable difference Business Gazelle series, from its predecessor. With his appearance had improved visual perception of the car, and significantly reduce the technological gap.
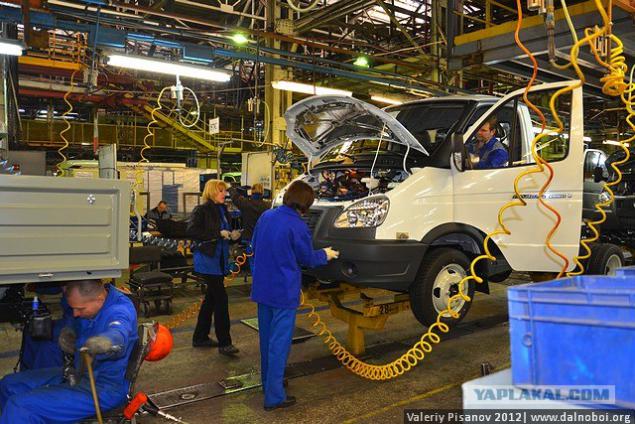
51. Body. Since 2011, the body held a 100% priming sides and base platform by cathodic electrodeposition.
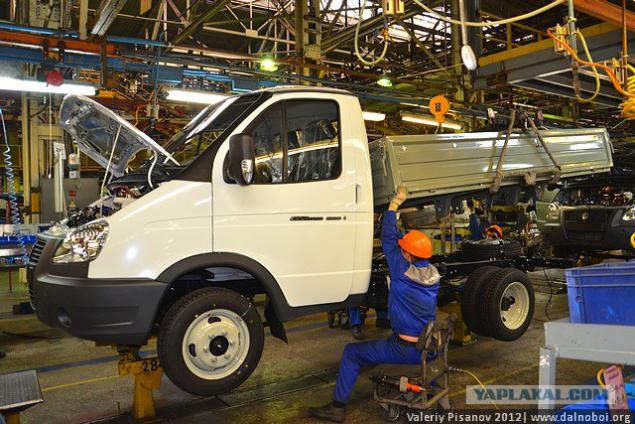
52. The metal sleeve, with its help, in the braking system of the car creates a vacuum at the same time served the brake fluid.
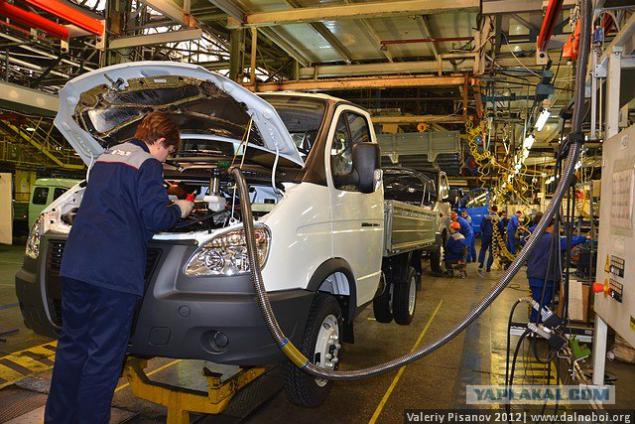
53. The car is on wheels. Who will be the first start the engine, then the car is already moving under its own power.
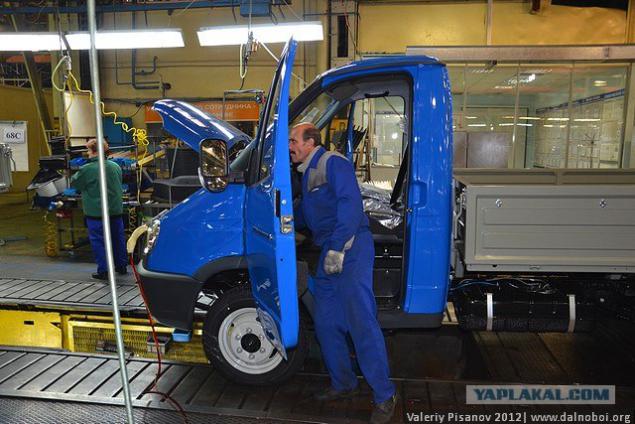
54. In the enclosed space passes running - three-kilometer run.
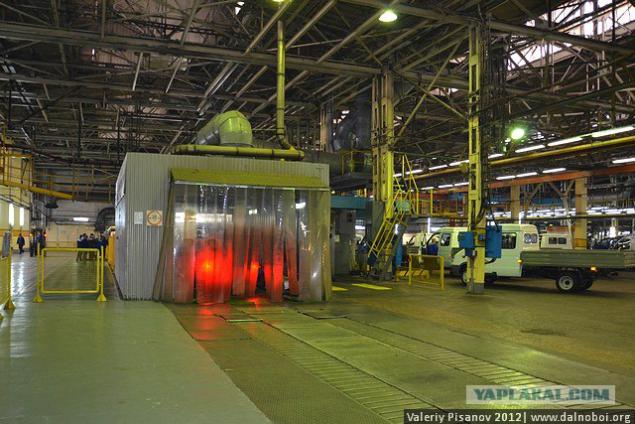
55. Freshly car arrived at the point of acceptance of the quality department.
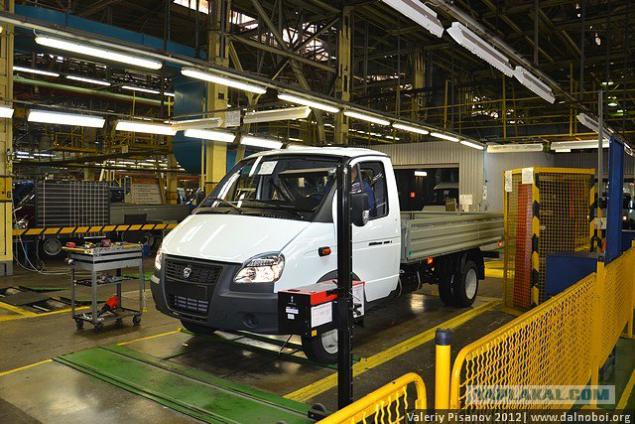
56. Specialist conducts a final inspection, but that's not all.
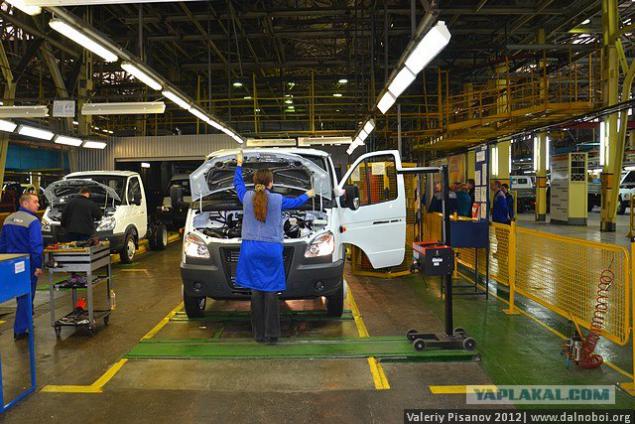
57. In conclusion, the car gets into the camera body to check for leaks.
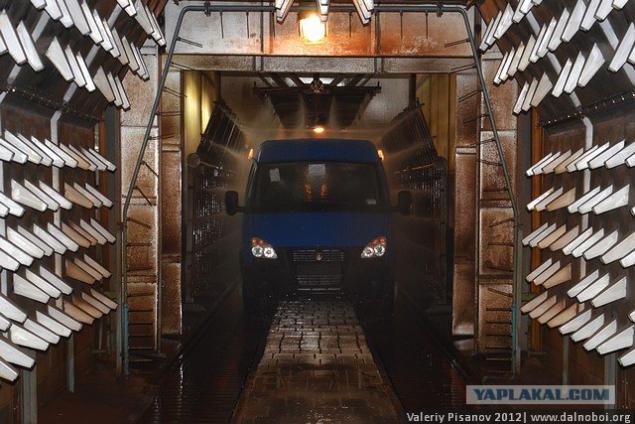
58. Ready to ship cars to buyers waiting for transporters.
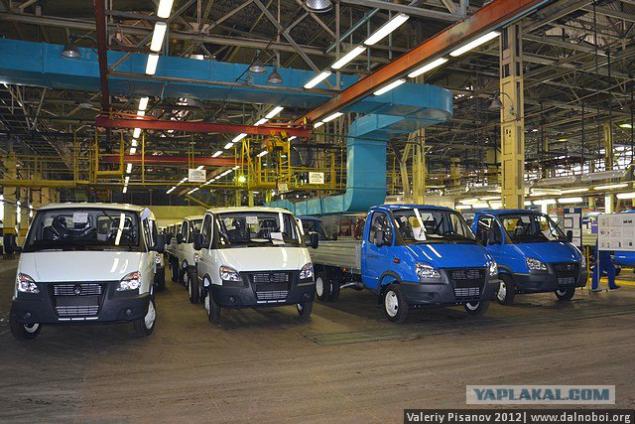
59. For the promotion and conduct of tours "Blog trucker" expresses deep gratitude to the press secretary of the Gorky Automobile Plant Erasova Paul.
© «Blog trucker» 08.04.2012
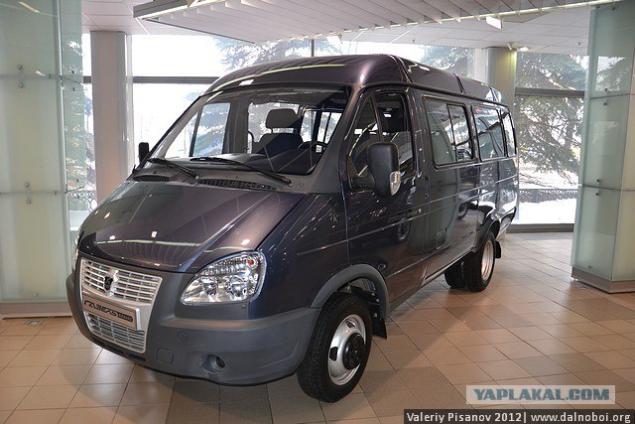
Source: