1225
Salt of the earth
Once volumes of Aral salt reached 600 thousand tonnes annually, supplying all the 15 republics of the Soviet Union. Who produces about 250 thousand tons, and used only for the domestic market. There was a new time came, private investors, new technologies, cut jobs, and even salt has changed ...
Stocks of salt in the southern basin constitute 11 million. Tons, which is enough for about another 40 -50 years. Restoration of salt reserves of the lake occurs every 35-45 years.
Salt formed after evaporation of highly concentrated salt brine.
The thickness of the salt layer reaches 1, 5 meters. Now salt extraction from the lake takes place every two years, from May to November. Volume production for the season is 250 thousand tons.
Rubber boots six months so corroded by salt, that they have to change. On the seasonal extraction, transportation and unloading of salt attracts more than 100 workers. Furthermore they are constantly at the plant JSC "Araltuz" employs 700 people at its facilities allow to contain only 400. But the leadership of the plant is on it to give us something to take local people. But on the lake protection ensures that thieves do not pilfered abandoned equipment.
In the old days people extracted salt manually, the clock is at the concentrated salt water.
The deposit is located 10 km from the village Zhaksykylysh, which is home to about 6000 people. All of them tend to work in the factory. The average salary is 30-35 thousand tenge.
After the salt produced, it is transferred to a gondola. In the night on the hill sent 40 wagons.
After the salt is fed to unloader TR-2 (conveyor of high bugrovaniya).
The height of the salt mountain reaches 25 meters.
With the help of a bulldozer made bugrovaniya process and storage of salt on the hill.
Stockpiled salt hardens and in order to loosen it, it explodes with the help of ammonites.
Salt raw salt from the mound for processing into a hopper is supplied with bulldozers.
And there already using conveyor funds goes to grinding and enrichment plant.
Since the conveyor belt is fed to the crushing salt.
The spiral classifier salt passes the primary stage of enrichment.
For this purpose, a classifier is fed lake brine - brine.
After spiral classifier and a countercurrent separator salt is fed to a dewatering elevator.
And only after that enriched salt is fed into the drying compartment where the COP apparatus (fluidized bed) by means of hot air from the drying process occurs elektrokolarifera.
Dried salt at a temperature of 100 -140S.
And then begins the process of iodization. In the past, when there was no special equipment to enrich salt with minerals and iodine, salt was not purified, so it had a grayish tint. Now she is white.
The finished salt laid out in polypropylene bags 10, 30, 50 kg.
Prepacked salt of the feed conveyor is fed to the packaging process.
And from there to zheleznorozhnye covered wagons. Every day, the plant sends 4-5 wagon all over Kazakhstan.
Warehouse "Araltuz" accommodates 750 tons.
Several years ago, enterprising people from the south of Kazakhstan tried to counterfeit products "Araltuz", creating the same package, but fasuya unsupplemented and non-iodized salt from Suzak field. To distinguish a fake, when you buy should pay attention to marking and manufacture date of the salt.
Before sending the salt production laboratory checks every two hours finished products for the maintenance of minerals and iodine percentage.
In February next year, "Araltuz" launches Spanish factory, which will double the volume of production, but at the same time and to halve the number of employees ...
via source
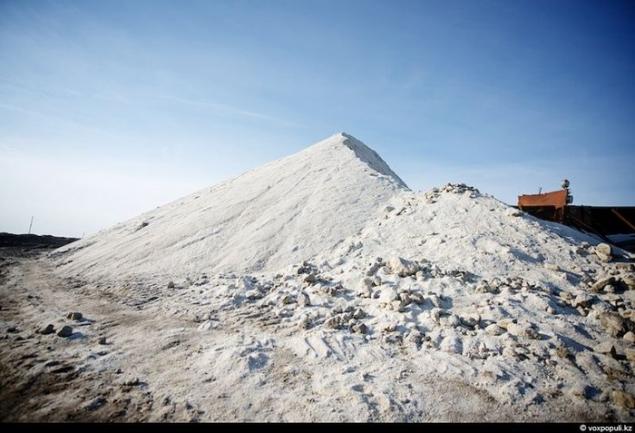
Stocks of salt in the southern basin constitute 11 million. Tons, which is enough for about another 40 -50 years. Restoration of salt reserves of the lake occurs every 35-45 years.
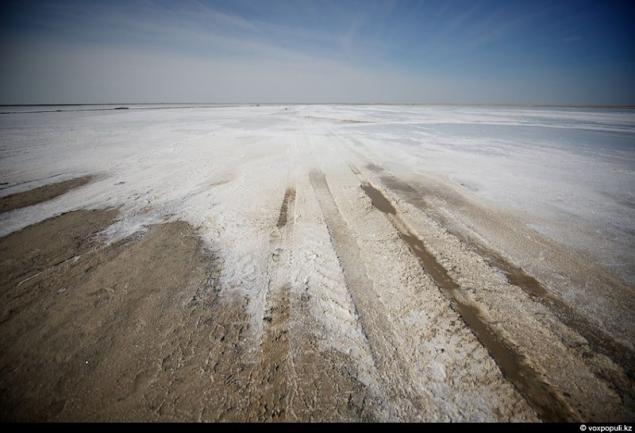
Salt formed after evaporation of highly concentrated salt brine.
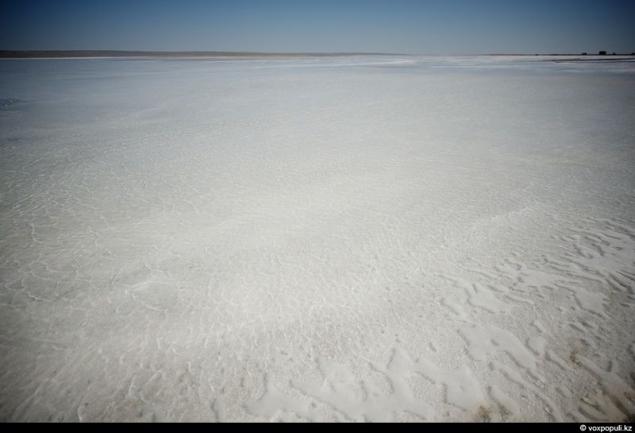
The thickness of the salt layer reaches 1, 5 meters. Now salt extraction from the lake takes place every two years, from May to November. Volume production for the season is 250 thousand tons.
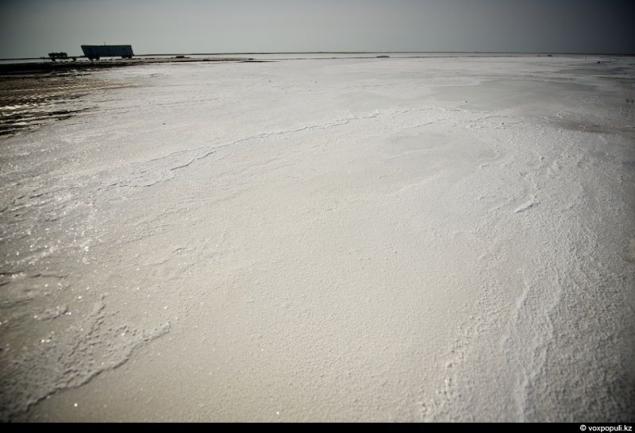
Rubber boots six months so corroded by salt, that they have to change. On the seasonal extraction, transportation and unloading of salt attracts more than 100 workers. Furthermore they are constantly at the plant JSC "Araltuz" employs 700 people at its facilities allow to contain only 400. But the leadership of the plant is on it to give us something to take local people. But on the lake protection ensures that thieves do not pilfered abandoned equipment.
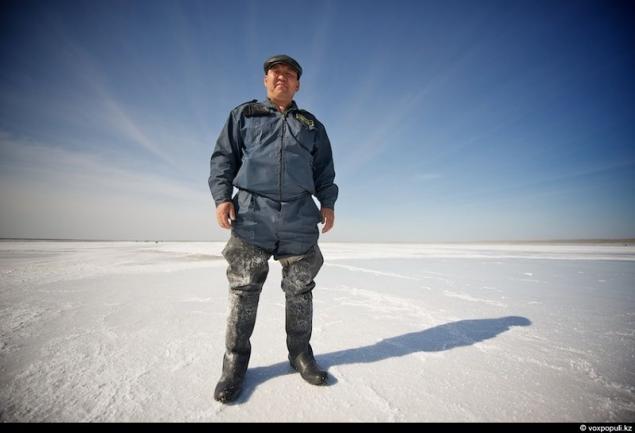
In the old days people extracted salt manually, the clock is at the concentrated salt water.
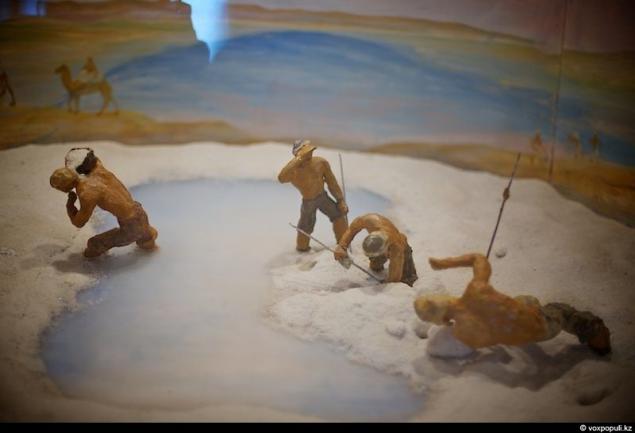
The deposit is located 10 km from the village Zhaksykylysh, which is home to about 6000 people. All of them tend to work in the factory. The average salary is 30-35 thousand tenge.
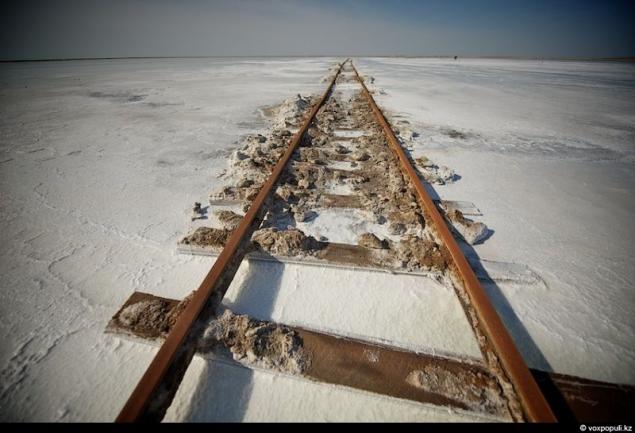
After the salt produced, it is transferred to a gondola. In the night on the hill sent 40 wagons.
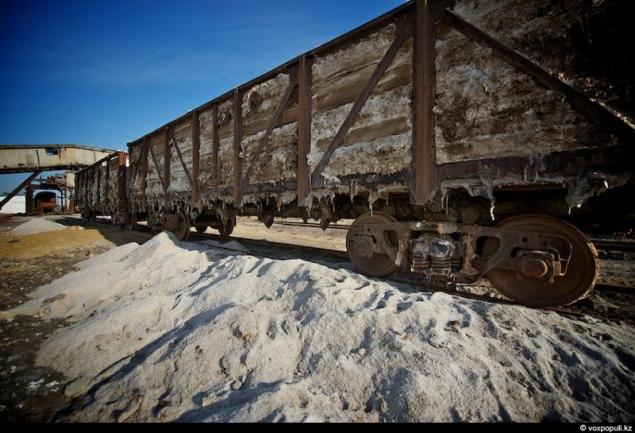
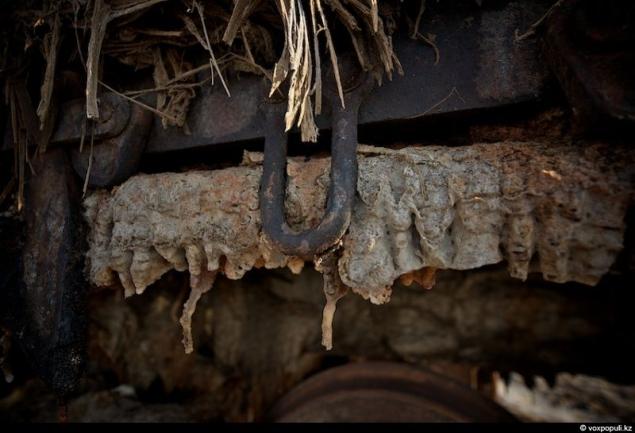
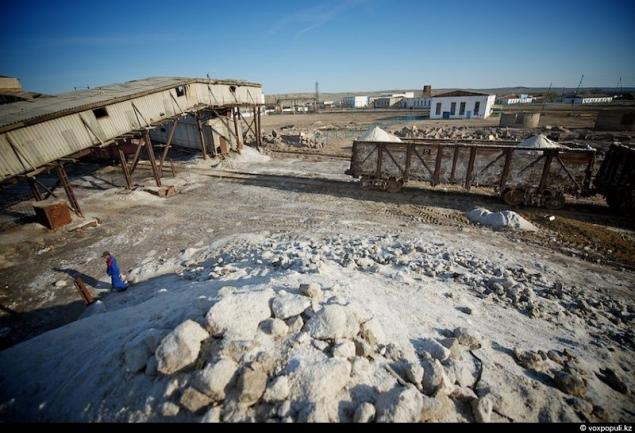
After the salt is fed to unloader TR-2 (conveyor of high bugrovaniya).

The height of the salt mountain reaches 25 meters.
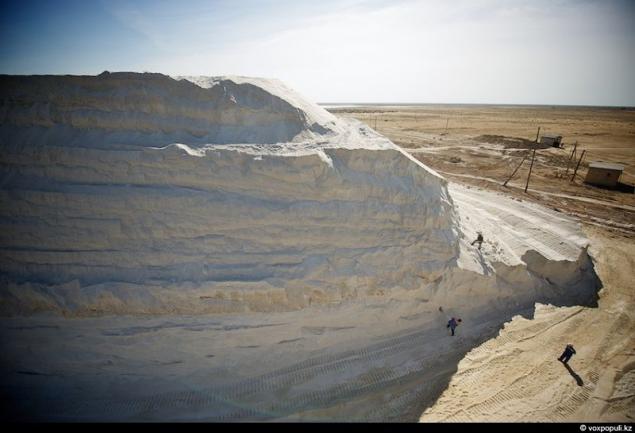
With the help of a bulldozer made bugrovaniya process and storage of salt on the hill.
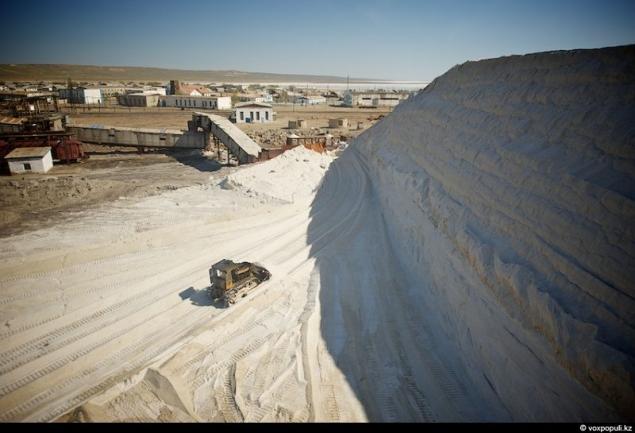
Stockpiled salt hardens and in order to loosen it, it explodes with the help of ammonites.
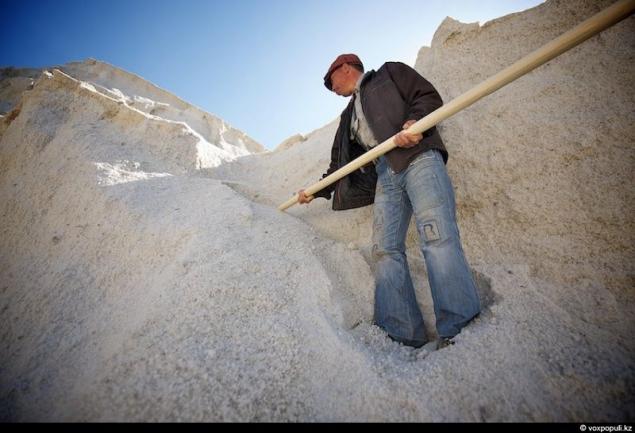
Salt raw salt from the mound for processing into a hopper is supplied with bulldozers.
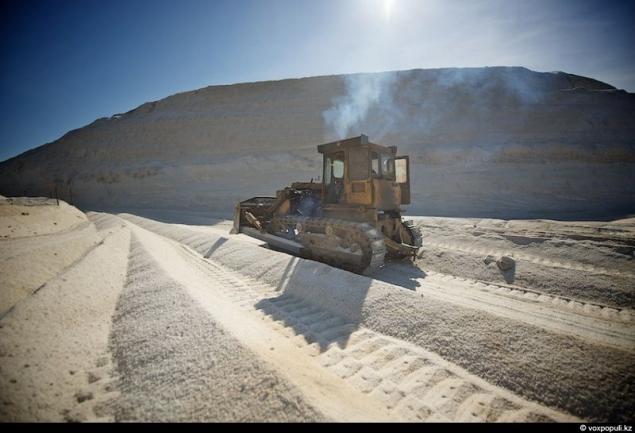
And there already using conveyor funds goes to grinding and enrichment plant.
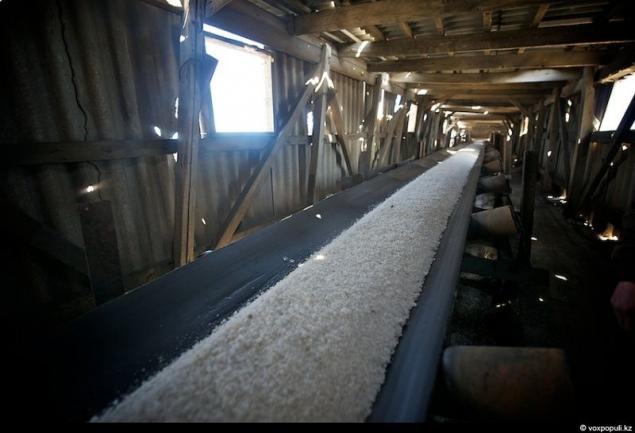
Since the conveyor belt is fed to the crushing salt.
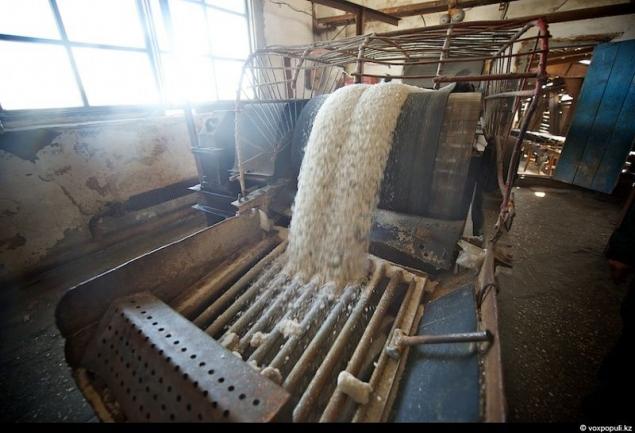
The spiral classifier salt passes the primary stage of enrichment.
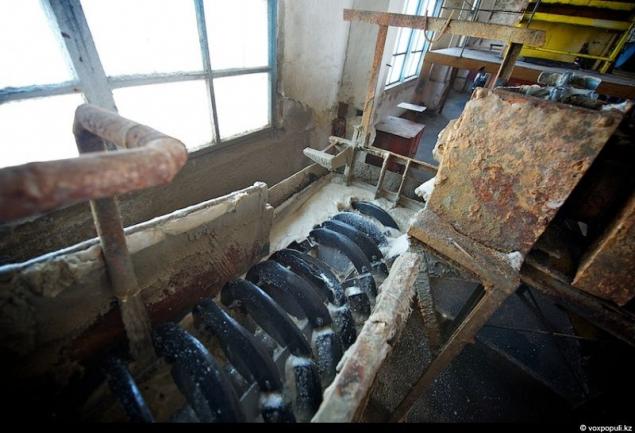
For this purpose, a classifier is fed lake brine - brine.
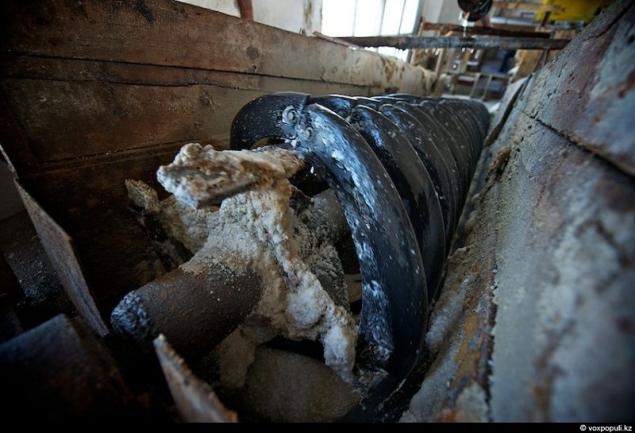
After spiral classifier and a countercurrent separator salt is fed to a dewatering elevator.
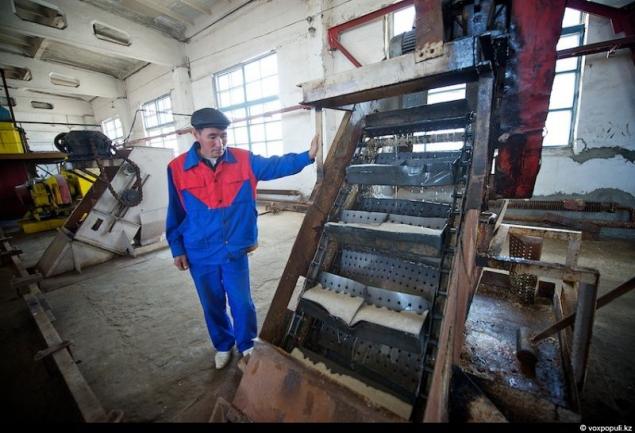
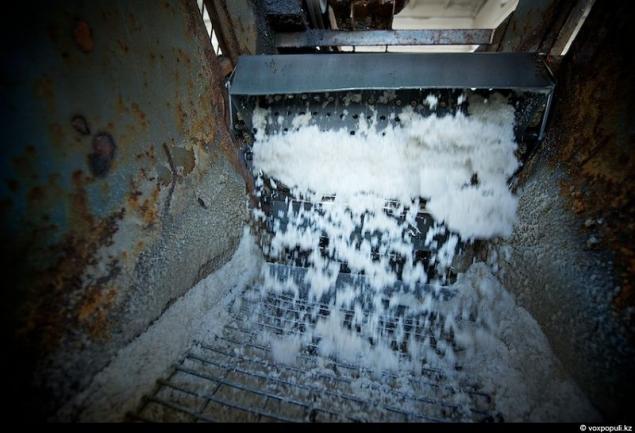
And only after that enriched salt is fed into the drying compartment where the COP apparatus (fluidized bed) by means of hot air from the drying process occurs elektrokolarifera.
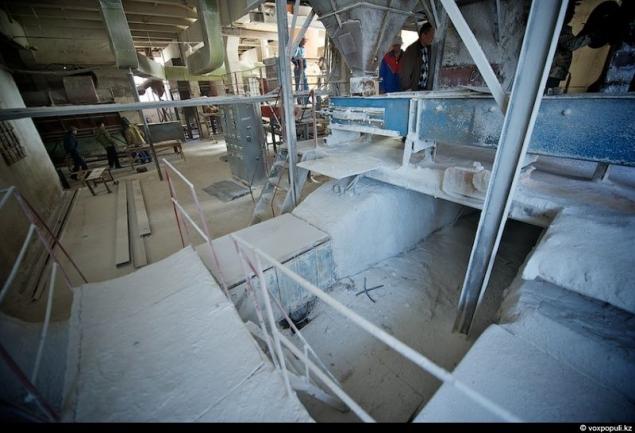
Dried salt at a temperature of 100 -140S.
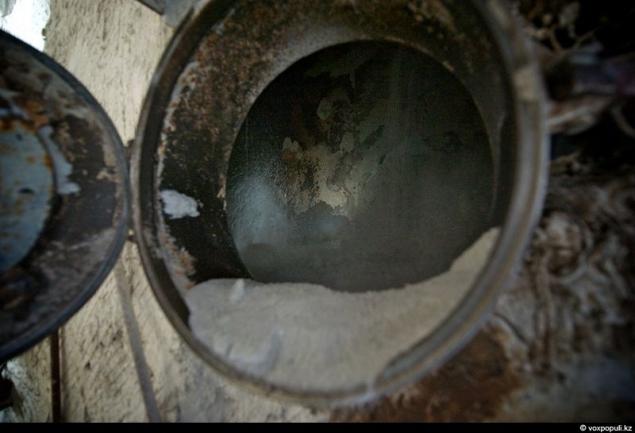
And then begins the process of iodization. In the past, when there was no special equipment to enrich salt with minerals and iodine, salt was not purified, so it had a grayish tint. Now she is white.
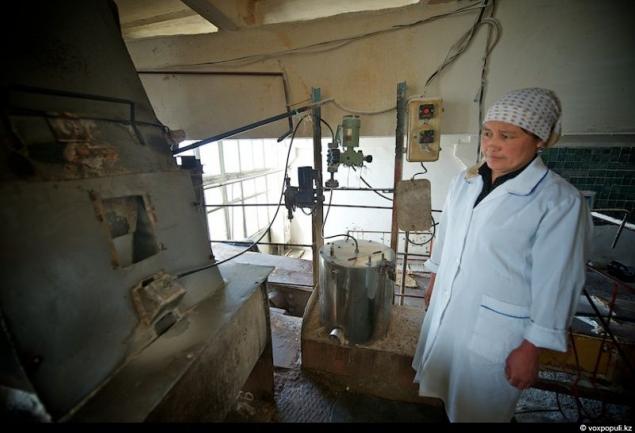
The finished salt laid out in polypropylene bags 10, 30, 50 kg.
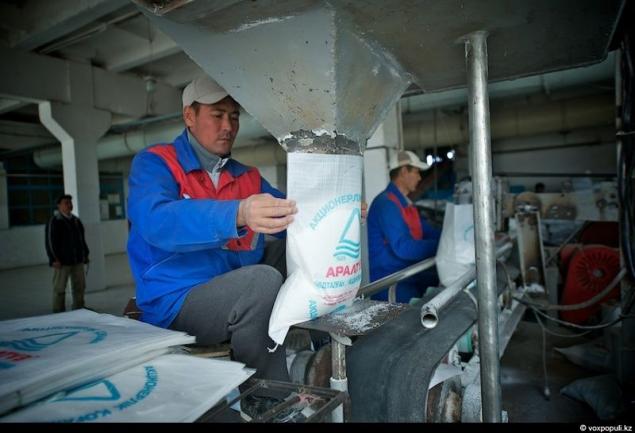
Prepacked salt of the feed conveyor is fed to the packaging process.
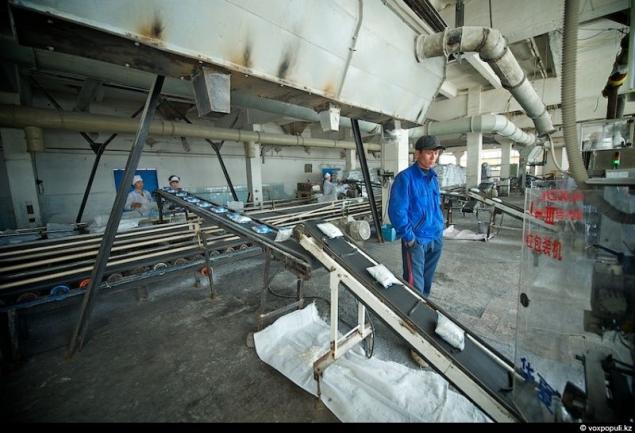
And from there to zheleznorozhnye covered wagons. Every day, the plant sends 4-5 wagon all over Kazakhstan.
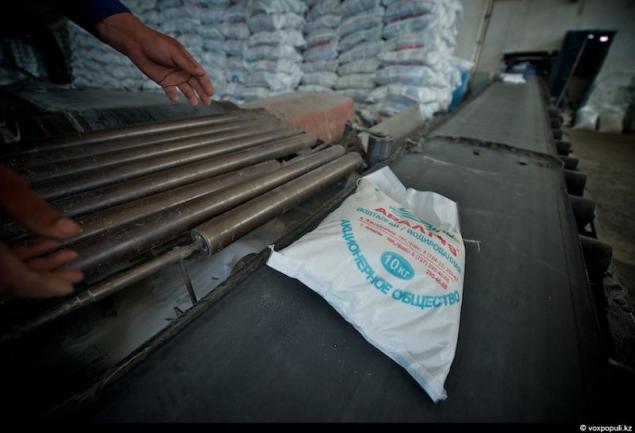
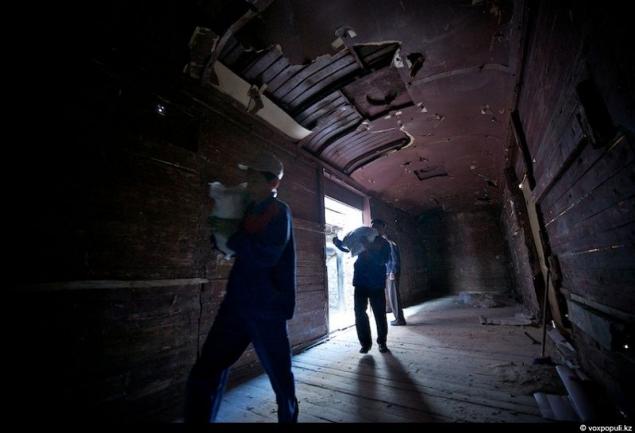
Warehouse "Araltuz" accommodates 750 tons.
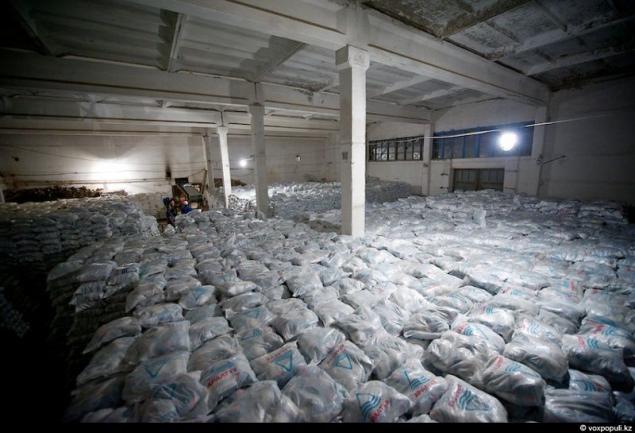
Several years ago, enterprising people from the south of Kazakhstan tried to counterfeit products "Araltuz", creating the same package, but fasuya unsupplemented and non-iodized salt from Suzak field. To distinguish a fake, when you buy should pay attention to marking and manufacture date of the salt.
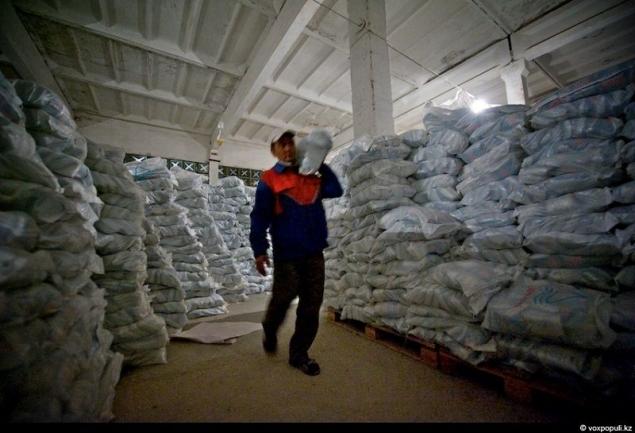
Before sending the salt production laboratory checks every two hours finished products for the maintenance of minerals and iodine percentage.
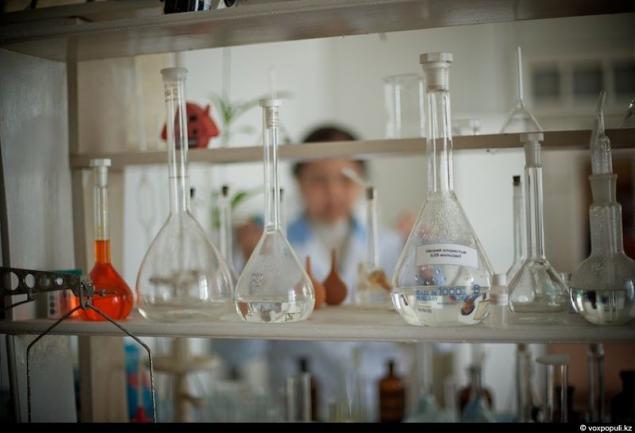
In February next year, "Araltuz" launches Spanish factory, which will double the volume of production, but at the same time and to halve the number of employees ...
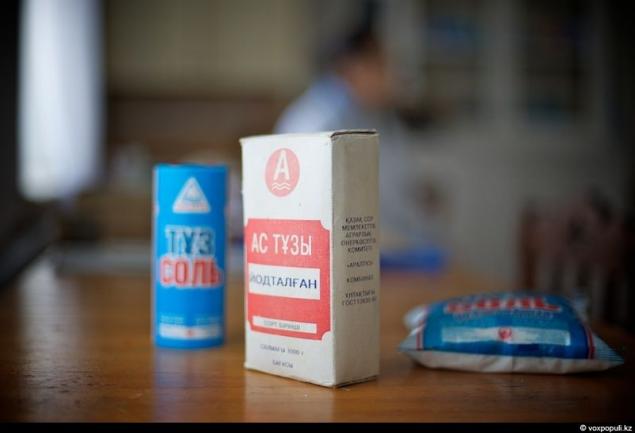
via source