2090
South Africa. "De Beers" Diamonds
Diamonds - it is for the very rich. For persons of royal blood and wives multimillionaires. For movie stars, top models and lo & s-era symbols, for which the gentlemen who prefer blondes, ready to throw down the drain any money. For large diamonds, as a rule, it lasts a long trail of blood. Robbers prey on them with such passion that women, even in special occasions, prefer to wear their decorations up, and keep the originals in a safe. But the diamond - is nothing more than a cut diamond. A diamond - the stone is not rare. For the year in the world is produced as many as 10 tons of diamonds. However, only a fifth of them can be turned into diamonds. But still we are talking about tons. So people with trepidation are not this stone for its uniqueness, and not even an amazing shine. As one of the founders of the company "De Beers" Gary Oppenheimer: "The demand for diamonds is based primarily on the vanity."
Kimberly. The central point of South Africa. In the middle of the XIX century in a radius of several hundred kilometers, there was nothing but the bare steppes, which loomed farm. On one of them in 1871 first discovered diamonds. In fact, in the valleys of the rivers Orange and Vaal diamonds found before but this abundance of rocks on land belonging to the farmers de Biram, miners do not have to meet. A real diamond rush. Thousands of adventurers flocked to South Africa, hoping to earn millions. Sami brothers de Bira chose not to tempt fate - they sold their farm for a round sum miners and left those troubled places. But the name of their history preserved. It appears in the title of the world diamond monopoly - the company "De Beers".
The new field was named Kimberly, in honor of the then British Minister for the Colonies. It was a series of tubes extending deep into an area of several hundred square meters each. They were filled with diamond-blue rock, called kimberlite. There are many theories of such tubes, one thing is certain - they are all of volcanic origin. To convert conventional carbon - the very thing of which the furnace black - in a diamond requires very high temperatures and pressures. In nature, these conditions exist only in the upper part of the mantle at about 160 km. There's some carbon and crystallized in the precious mineral. Up he endured during mikroizverzheny when hot gases broke through robe and rushed liquid channel formed volcanic mass.
While kimberlite pipes - the only suppliers in the world of diamonds, these gems are not only there. In Namibia, Botswana and other countries of South-West Africa, the richest deposits found, lying on the beds of rivers and their confluence in the areas of the ocean. The fact that the kimberlite, which is shed during the eruptions of the tubes, frozen in the form of a large hill, which over time under the influence of winds and rains destroyed. Rivers carried the rock, and with it the diamonds, downstream to the ocean. Today, diamond mining in some places is conducted from ships. Practiced as causeways, in order to win back the sea diamondiferous coastal strip. But back to the Kimberly miners. Within a few years, some armed with picks and shovels, they dug tunnels so that the land around the town began to look like Swiss cheese. Landslides and floods have become commonplace at the mine. Conduct further development could only centrally, using modern methods. Previously other is realized Cecil Rhodes. It began as an ordinary miner, but the energy and university education did their job - to the end of the 80-ies of the XIX century, the syndicate "De Beers", which was led by Rhodes, was the owner of all mines around Kimberley and provides 90% of world diamond production, which is about 3 million carats a year.
Carat - is 0, 2 grams. Special unit for diamonds was necessary because most of the mined stones weigh less than a carat, and to use such a large unit as gram, jewelers just uncomfortable. Scotty Ross: "Carob Latin - ceratonia siliqua. Hence the word "carat". The seeds of this tree the size of the dry pea. They are distinguished by a constancy of weight - two-tenths of a gram. Therefore, from time immemorial they were used as the unit of measurement in jewelry. When injected standard system for precious stones, did not change anything. The unit left carats, that is, the weight of one carob seed. "
The largest ever found diamonds weighing 160 carats and 3 was the size of a human fist. These large stones in jewelry is not used. They either deposited in collections, or are split into several parts. Operation is extremely responsible. Diamond inject only the so-called cleavage direction. If it is wrong, the stone shatters into small pieces. In fact, to split one of the world's largest diamonds, "Jonker" weighing 726 carats, cutter spent a whole year. Large parts get after splitting, cut by a rapidly rotating thin as paper, bronze disc. From "Jonker" was thus obtained as many as 13 different jewels. Many do not even too large diamonds have cut because they have an irregular shape or defects are present within them. Experienced master leaves the defect on the surface of one of the parts and then easily remove it during the cut.
Kimberly today - not the main place of extraction of diamonds, but in the words of one expert: "The city of diamonds for the same symbol, like Saudi Arabia for oil or Austria for classical music." In its vicinity are still working, and quite legally, a lot of miners. "De Beers" and other major producers are interested in diamond deposits containing not less than 0, 3 carats per cubic meter of rock. Prospectors are ready to be content with less. Especially since almost all of them live in hope one day to find a great stone, and in one fell swoop to get rich.
Until World War I work in Kimberley were open way. Breed blasted with dynamite, loaded with an excavator giant dump trucks and transported to the processing plant. In memory of that time was huge, water-filled pit with a diameter of one and a half kilometers and a depth of nearly two hundred meters. But most of the tubes go into the depths of many kilometers, and the main production has to be carried underground.
Diamond Mine - Cyclopean construction. For its construction it takes five to six years. It's a whole underground city, with lots of levels, ventilation and drainage galleries, kilometers of roads and interchanges. Shaft is laid along the kimberlite pipe. From it to the place of development are the galleries. As it reaches the mined material into the shaft and further to the surface. The descent into the mine takes the strength of two minutes. First level - above us 600 meters of rock. To get to the last section, which is located at a depth of 880 meters, still have to go down a few levels. You can do it your own legs, having spent more than an hour on the road, but it is better to use the miners' public transport. " Move the miners underground at SUVs. Any person immediately the question arises: how such a machine could be at a depth of more than seven hundred meters. And it turned out to be very simple: it hitched hook. We put "on the ass." They fit in the lift and lowered into the ground. Elevators in the mines is so broad that a pair of truck breaks loose.
Extraction of kimberlite from the bottom upwards. First select the lowermost portion, and then falls by the explosion, which is higher, and so on to the ground surface. Underground mining differs little from the land. Those trinitrotoluene block, which lay in a pre-drilled boreholes. After the explosion, the pieces of ore shovel special bucket - by mining language is called "scraper", and taken through the tunnels leading to tapered shafts. According to him kimberlite cleared away down to the main haulage horizon. The lowest level of the mine 880 meters underground. At this level, there is an apparatus which the miners called crusher. In fact, it is a huge jaw. Blasted rock is delivered and assembled here on the locomotive and unloaded inside the machine, and then carefully milled as if masticated. Within seconds of the giant stones obtained stones the size of a fist.
Further ore crushing and refining already produced on the surface. This process allowed a limited number of people to avoid theft. After all, a small stone hidden in clothing or just put it on the cheek does not cost anything. Of course, the administration of mines take in this regard its actions, but human ingenuity knows no bounds. A case where a worker who has been in place in one eye prosthesis, take it out, hiding the diamonds in an empty eye socket, then insert the prosthesis in place.
Pipelining mined rock is transported from the mine, which is hidden behind piles, to the territory of the mining combine De Beers. The total length of the conveyor - 5 km. Every hour on it to the territory of the plant delivered 1,400 tons of rock. She gets in the disintegrator - a huge drum, where it is a secondary crushing. Then the ore is sifted through a mechanical sieve. Relatively large pieces again fall into the drum. The bulk is sent for further processing. Marius Sueynpoel engineer: "There is a section where the ground ore is mixed with a special ferro-silicone fluid having a very high density. The device essentially is a conventional separator, the mixture is separated into heavy and light fractions. The light sent to the blade, and a heavy - it is, in fact, have rough and minerals having a density close to that of diamond, - a recovery section ".
If you think you have produced in this way from rocks similar to those diamond sparkling crystals that are expropriated from numerous James Bond villains, you are deeply mistaken. On the face of the stone it is not much different from the usual run-of gravel or glass bottle. It helps to recognize the X-ray machine because diamonds have the ability to fluoresce under the influence of X-rays. Lessons diamonds placed for several hours in a special cleaning solution, then they are similar to themselves, that is, on the gems. In the plant only the primary sorting. Separates the largest samples and those that clearly suitable only for technical purposes. They are, incidentally, make up the majority - some 80% of production. With revenue industrial diamonds provide up to five times smaller than the jewelry. The final sorting and evaluation carried out by experts in special centers. This procedure requires a very high qualification. Besides weight diamonds are divided into four classes according to the form and purity five seven classes on color. Price for jewelry stones of the same weight can vary by several dozen times. No matter how experienced the sorter, the last word still for a cutter. Only he can say how much and what quality of work because of a polished diamond.
Brent Lunt, diamond expert: "It all depends on the size of the diamond, its shape, weight, purity. For example, diamond cutting, say, four carats from a professional takes at least three days. But it may fall a stone, which he will tinker week. In the light do not exist two identical diamonds. Each is unique, and therefore each have a cutter approach. " Brent Lunt in the jewelry business for over thirty years. In Kimberley, it contains a small workshop in diamond cutting. Stone buys from miners and wholesalers. In his lifetime he has seen a lot of things. But remember, more anecdotal stories: "Once one of my cutters, loose diamonds directly behind lapidary machine. Stone just slipped out of his hands. A few hours of all workers engaged in the workshop of his quest, but in vain. I really thought that intervened in the case evil spirits, but he found the diamond. And where do you think? The hair at the cutter. The guy was such a lush head of hair, he did not even feel like a rock landed on his crown. "
Diamond cutting and polishing - it's the final stages of processing. But first he has to make a geometrically correct shape: round, oval or pear-shaped. This is done on a device remotely resembling a lathe, which also serves as a diamond cutter - any other material will not leave a stone on a scratch treated. Once a diamond has found the correct shape, it faces on a rapidly rotating cast iron disc, on which a diamond paste. When turning and cutting grinds off about half a stone, but it becomes a diamond, which is able to shine fascinate any woman.
Strictly necessary number of facets on the diamond applied does not exist. But the most common and widely recognized is the so-called brilliant cut with 58 facets. It is used for stones of all shapes and sizes. Here art is that faces were at a certain angle to each other. Ideally, the light penetrating into the diamond through a flat top platform and repeatedly reflected from all sides, have to go back through it is a bright multi-color rainbow. The first faceting gems mastered in India seven centuries before Christ. Judging by the extant examples of ancient masters are not well versed in the laws of light reflection. And so many of the old stones in these days has to process all over again.
Before you decorate someone's collection, diamonds are the windows of jewelry stores. Some come here leave fortunes. The most expensive item of jewelry store Kimberley diamond ring three and a half carats. Thirty thousand dollars a mineral that has done a very long journey.
Source: http: //
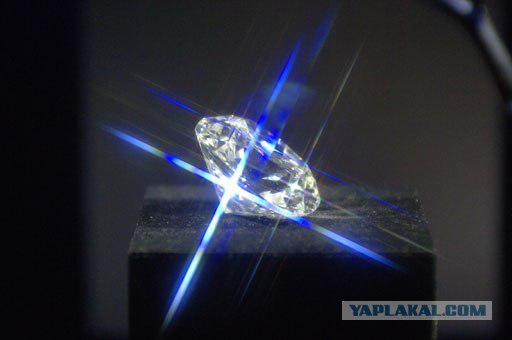
Kimberly. The central point of South Africa. In the middle of the XIX century in a radius of several hundred kilometers, there was nothing but the bare steppes, which loomed farm. On one of them in 1871 first discovered diamonds. In fact, in the valleys of the rivers Orange and Vaal diamonds found before but this abundance of rocks on land belonging to the farmers de Biram, miners do not have to meet. A real diamond rush. Thousands of adventurers flocked to South Africa, hoping to earn millions. Sami brothers de Bira chose not to tempt fate - they sold their farm for a round sum miners and left those troubled places. But the name of their history preserved. It appears in the title of the world diamond monopoly - the company "De Beers".
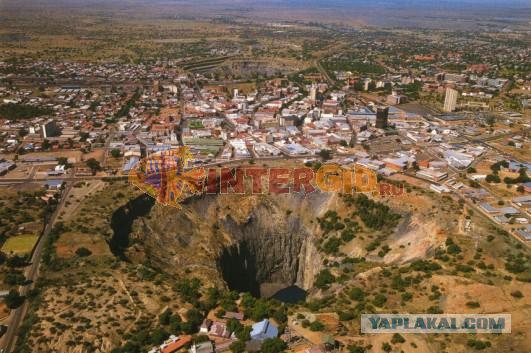
The new field was named Kimberly, in honor of the then British Minister for the Colonies. It was a series of tubes extending deep into an area of several hundred square meters each. They were filled with diamond-blue rock, called kimberlite. There are many theories of such tubes, one thing is certain - they are all of volcanic origin. To convert conventional carbon - the very thing of which the furnace black - in a diamond requires very high temperatures and pressures. In nature, these conditions exist only in the upper part of the mantle at about 160 km. There's some carbon and crystallized in the precious mineral. Up he endured during mikroizverzheny when hot gases broke through robe and rushed liquid channel formed volcanic mass.
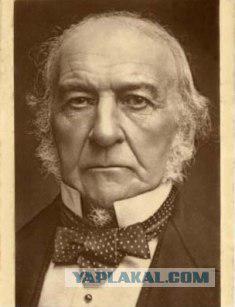
While kimberlite pipes - the only suppliers in the world of diamonds, these gems are not only there. In Namibia, Botswana and other countries of South-West Africa, the richest deposits found, lying on the beds of rivers and their confluence in the areas of the ocean. The fact that the kimberlite, which is shed during the eruptions of the tubes, frozen in the form of a large hill, which over time under the influence of winds and rains destroyed. Rivers carried the rock, and with it the diamonds, downstream to the ocean. Today, diamond mining in some places is conducted from ships. Practiced as causeways, in order to win back the sea diamondiferous coastal strip. But back to the Kimberly miners. Within a few years, some armed with picks and shovels, they dug tunnels so that the land around the town began to look like Swiss cheese. Landslides and floods have become commonplace at the mine. Conduct further development could only centrally, using modern methods. Previously other is realized Cecil Rhodes. It began as an ordinary miner, but the energy and university education did their job - to the end of the 80-ies of the XIX century, the syndicate "De Beers", which was led by Rhodes, was the owner of all mines around Kimberley and provides 90% of world diamond production, which is about 3 million carats a year.
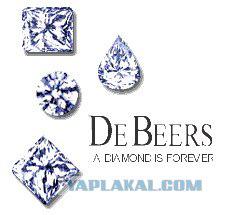
Carat - is 0, 2 grams. Special unit for diamonds was necessary because most of the mined stones weigh less than a carat, and to use such a large unit as gram, jewelers just uncomfortable. Scotty Ross: "Carob Latin - ceratonia siliqua. Hence the word "carat". The seeds of this tree the size of the dry pea. They are distinguished by a constancy of weight - two-tenths of a gram. Therefore, from time immemorial they were used as the unit of measurement in jewelry. When injected standard system for precious stones, did not change anything. The unit left carats, that is, the weight of one carob seed. "
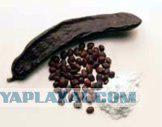
The largest ever found diamonds weighing 160 carats and 3 was the size of a human fist. These large stones in jewelry is not used. They either deposited in collections, or are split into several parts. Operation is extremely responsible. Diamond inject only the so-called cleavage direction. If it is wrong, the stone shatters into small pieces. In fact, to split one of the world's largest diamonds, "Jonker" weighing 726 carats, cutter spent a whole year. Large parts get after splitting, cut by a rapidly rotating thin as paper, bronze disc. From "Jonker" was thus obtained as many as 13 different jewels. Many do not even too large diamonds have cut because they have an irregular shape or defects are present within them. Experienced master leaves the defect on the surface of one of the parts and then easily remove it during the cut.
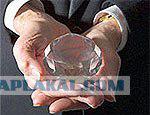
Kimberly today - not the main place of extraction of diamonds, but in the words of one expert: "The city of diamonds for the same symbol, like Saudi Arabia for oil or Austria for classical music." In its vicinity are still working, and quite legally, a lot of miners. "De Beers" and other major producers are interested in diamond deposits containing not less than 0, 3 carats per cubic meter of rock. Prospectors are ready to be content with less. Especially since almost all of them live in hope one day to find a great stone, and in one fell swoop to get rich.
Until World War I work in Kimberley were open way. Breed blasted with dynamite, loaded with an excavator giant dump trucks and transported to the processing plant. In memory of that time was huge, water-filled pit with a diameter of one and a half kilometers and a depth of nearly two hundred meters. But most of the tubes go into the depths of many kilometers, and the main production has to be carried underground.
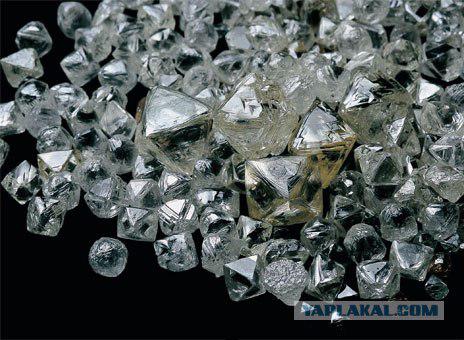
Diamond Mine - Cyclopean construction. For its construction it takes five to six years. It's a whole underground city, with lots of levels, ventilation and drainage galleries, kilometers of roads and interchanges. Shaft is laid along the kimberlite pipe. From it to the place of development are the galleries. As it reaches the mined material into the shaft and further to the surface. The descent into the mine takes the strength of two minutes. First level - above us 600 meters of rock. To get to the last section, which is located at a depth of 880 meters, still have to go down a few levels. You can do it your own legs, having spent more than an hour on the road, but it is better to use the miners' public transport. " Move the miners underground at SUVs. Any person immediately the question arises: how such a machine could be at a depth of more than seven hundred meters. And it turned out to be very simple: it hitched hook. We put "on the ass." They fit in the lift and lowered into the ground. Elevators in the mines is so broad that a pair of truck breaks loose.
Extraction of kimberlite from the bottom upwards. First select the lowermost portion, and then falls by the explosion, which is higher, and so on to the ground surface. Underground mining differs little from the land. Those trinitrotoluene block, which lay in a pre-drilled boreholes. After the explosion, the pieces of ore shovel special bucket - by mining language is called "scraper", and taken through the tunnels leading to tapered shafts. According to him kimberlite cleared away down to the main haulage horizon. The lowest level of the mine 880 meters underground. At this level, there is an apparatus which the miners called crusher. In fact, it is a huge jaw. Blasted rock is delivered and assembled here on the locomotive and unloaded inside the machine, and then carefully milled as if masticated. Within seconds of the giant stones obtained stones the size of a fist.
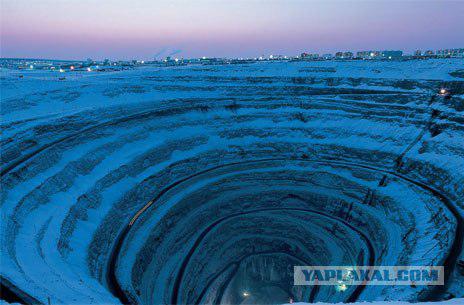
Further ore crushing and refining already produced on the surface. This process allowed a limited number of people to avoid theft. After all, a small stone hidden in clothing or just put it on the cheek does not cost anything. Of course, the administration of mines take in this regard its actions, but human ingenuity knows no bounds. A case where a worker who has been in place in one eye prosthesis, take it out, hiding the diamonds in an empty eye socket, then insert the prosthesis in place.
Pipelining mined rock is transported from the mine, which is hidden behind piles, to the territory of the mining combine De Beers. The total length of the conveyor - 5 km. Every hour on it to the territory of the plant delivered 1,400 tons of rock. She gets in the disintegrator - a huge drum, where it is a secondary crushing. Then the ore is sifted through a mechanical sieve. Relatively large pieces again fall into the drum. The bulk is sent for further processing. Marius Sueynpoel engineer: "There is a section where the ground ore is mixed with a special ferro-silicone fluid having a very high density. The device essentially is a conventional separator, the mixture is separated into heavy and light fractions. The light sent to the blade, and a heavy - it is, in fact, have rough and minerals having a density close to that of diamond, - a recovery section ".
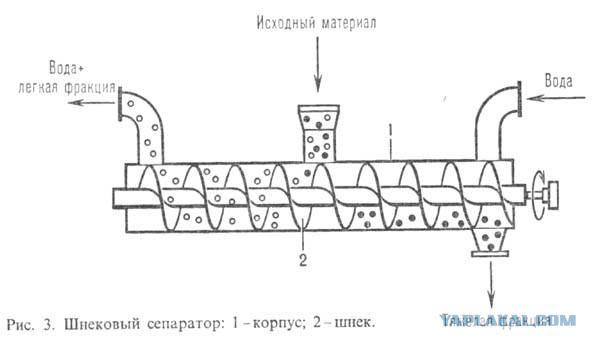
If you think you have produced in this way from rocks similar to those diamond sparkling crystals that are expropriated from numerous James Bond villains, you are deeply mistaken. On the face of the stone it is not much different from the usual run-of gravel or glass bottle. It helps to recognize the X-ray machine because diamonds have the ability to fluoresce under the influence of X-rays. Lessons diamonds placed for several hours in a special cleaning solution, then they are similar to themselves, that is, on the gems. In the plant only the primary sorting. Separates the largest samples and those that clearly suitable only for technical purposes. They are, incidentally, make up the majority - some 80% of production. With revenue industrial diamonds provide up to five times smaller than the jewelry. The final sorting and evaluation carried out by experts in special centers. This procedure requires a very high qualification. Besides weight diamonds are divided into four classes according to the form and purity five seven classes on color. Price for jewelry stones of the same weight can vary by several dozen times. No matter how experienced the sorter, the last word still for a cutter. Only he can say how much and what quality of work because of a polished diamond.
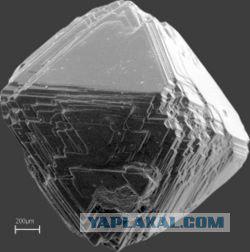
Brent Lunt, diamond expert: "It all depends on the size of the diamond, its shape, weight, purity. For example, diamond cutting, say, four carats from a professional takes at least three days. But it may fall a stone, which he will tinker week. In the light do not exist two identical diamonds. Each is unique, and therefore each have a cutter approach. " Brent Lunt in the jewelry business for over thirty years. In Kimberley, it contains a small workshop in diamond cutting. Stone buys from miners and wholesalers. In his lifetime he has seen a lot of things. But remember, more anecdotal stories: "Once one of my cutters, loose diamonds directly behind lapidary machine. Stone just slipped out of his hands. A few hours of all workers engaged in the workshop of his quest, but in vain. I really thought that intervened in the case evil spirits, but he found the diamond. And where do you think? The hair at the cutter. The guy was such a lush head of hair, he did not even feel like a rock landed on his crown. "
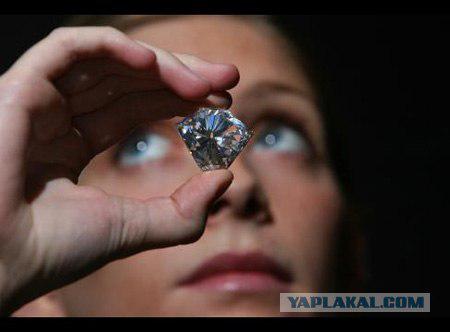
Diamond cutting and polishing - it's the final stages of processing. But first he has to make a geometrically correct shape: round, oval or pear-shaped. This is done on a device remotely resembling a lathe, which also serves as a diamond cutter - any other material will not leave a stone on a scratch treated. Once a diamond has found the correct shape, it faces on a rapidly rotating cast iron disc, on which a diamond paste. When turning and cutting grinds off about half a stone, but it becomes a diamond, which is able to shine fascinate any woman.
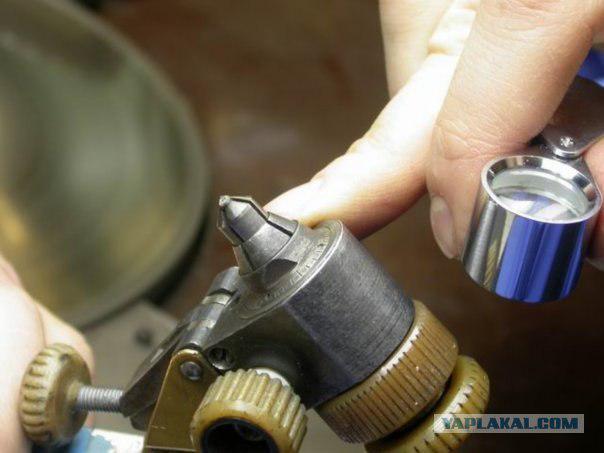
Strictly necessary number of facets on the diamond applied does not exist. But the most common and widely recognized is the so-called brilliant cut with 58 facets. It is used for stones of all shapes and sizes. Here art is that faces were at a certain angle to each other. Ideally, the light penetrating into the diamond through a flat top platform and repeatedly reflected from all sides, have to go back through it is a bright multi-color rainbow. The first faceting gems mastered in India seven centuries before Christ. Judging by the extant examples of ancient masters are not well versed in the laws of light reflection. And so many of the old stones in these days has to process all over again.
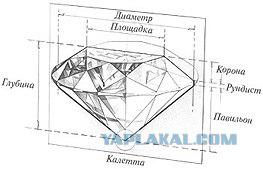
Before you decorate someone's collection, diamonds are the windows of jewelry stores. Some come here leave fortunes. The most expensive item of jewelry store Kimberley diamond ring three and a half carats. Thirty thousand dollars a mineral that has done a very long journey.
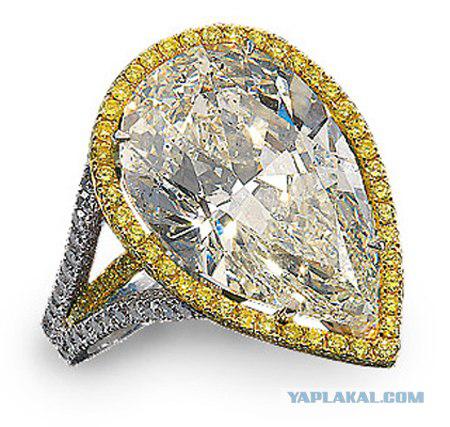
Source: http: //