1296
0.3
2014-04-28
Челябинский металлургический комбинат
Челябинский металлургический комбинат — крупнейшее в России предприятие полного металлургического цикла по выпуску высококачественных сталей. Это одно из немногих предприятий страны, которому дано право присваивать продукции собственный индекс — ЧС (Челябинская Сталь). В данном посте вы увидите как суровые мужики производят знаменитую челябинскую сталь.
Осторожно! Под катом очень жарко.
Когда-то железо получали на кострах в глиняных горшках или ямах без каких-либо специальных приспособлений. После долгого процесса обработки железа древние люди могли сделать себе наконечники для стрел или украшения для женщин. В современном мире потребности людей мало ушли от тех времён — им так же необходим металл. Но сегодня, после почти четырёхтысячелетней истории развития технологии производства металла, вместо костров на металлургических заводах используются доменные печи — агрегаты, самые крупные из которых могут выдавать до 12 тысяч тонн расплавленного чугуна в сутки.
Доменная печь — совершенное металлургическое устройство, которое работает безостановочно. Лишь иногда, один раз в 10—20 лет, когда многие элементы её конструкции износились от многолетней эксплуатации, печь останавливают для проведения капитального ремонта. Основное назначение домны — получение первого жидкого металла из железной руды.
Почти весь объём печи, высота которой может достигать нескольких десятков этажей, занимает шихта — составленная в определённых пропорциях смесь. Она состоит из обогащённой руды, кокса в качестве топлива и флюса — вещества, которое во время плавки образует шлак, помогая отделить пустую породу и золу от металла. Это исходное сырьё через сложную конструкцию засыпного аппарата непрерывно загружается в доменную печь сверху и в процессе нагревания постепенно опускается вниз. Навстречу твёрдым материалам снизу под большим давлением подаётся обогащённый кислородом воздух, нагретый до температуры 1100—1400 градусов Цельсия.
В таком режиме руда проходит весь путь сверху вниз за 4—6 часов и, дойдя до нижней части печи — горна, находится уже в жидком состоянии в виде расплавленных чугуна и шлака. В горне скапливается до тысячи и более тонн расплава, который постоянно заполняет эту часть печи и образует так называемый «мёртвый слой», высота которого составляет 0,6—1,7 метра. Когда в домне собирается достаточное количество чугуна и шлака, их выпускают через специальные огнеупорные отверстия — лётки, которые с этой целью каждый раз пробиваются бурильной машиной под управлением горнового.
Выпуск чугуна происходит в среднем каждые 40 минут. Получив выход из домны, расплавленный металл сильной струёй бьёт из отверстия, попадает в оборудованную систему желобов и, протекая через весь литейный цех, разливается в чугуновозы.
Горновой доменной печи — это первый, кто начинает работать с только что полученным расплавом. Он ведёт технологический процесс, наблюдая за ходом плавки визуально или по показаниям приборов, и своевременно выпускает чугун и шлак из доменной печи. Во многом от его мастерства и опыта зависят успехи или неудачи всей бригады доменного цеха.
С каждой плавки берется проба. Охлаждённый чугунный слиток отправляется в экспресс-лабораторию, где производится анализ его химического состава. На основе этих данных технологи доменного цеха могут скорректировать состав шихты, загружаемой в доменную печь, либо изменить технологические параметры доменной плавки. Также данные анализа учитываются при дальнейшей переработке чугуна в конвертерном цехе.
Кислородно-конвертерных цех. Сущность процесса переработки чугуна в сталь заключается в уменьшении содержания в чугуне ненужных примесей путём их окисления кислородом. Удаление этих элементов придаёт стали прочность и пластичность, а также делает её более податливой при обработке.
Чугуновозы поступают сюда по железнодорожным путям, которые проведены прямо в цех.
Основными материалами, загружаемыми в конвертер, являются металлический лом и чугун. Соотношение этих компонентов называется шихтой и измеряется примерно как один к четырём. Чугун поступает из доменного цеха в специальных ковшах-чугуновозах вместимостью от 150 до 600 тонн.
В качестве металлического лома обычно используются обрезки прокатных цехов и продукция Вторчермета. Металл засыпают в агрегат через специальную систему бункеров и весов-дозаторов, расположенных над конвертером. Сам конвертер представляет собой цилиндрический сосуд с суживающейся горловиной и сферическим днищем. Он закреплён в прочном несущем кольце, конструкция которого позволяет ему вращаться относительно поперечной оси на 360 градусов в любую сторону.
Чтобы перелить чугун, ковш с жидким металлом при помощи мостового крана поднимают к горловине наклонённого конвертера. Затем механизмы крана наклоняют чугуновозный ковш — и расплав переливается.
Когда основные материалы загружены, начинается продувка кислородом.
Слив шлака.
В некоторые периоды продувки слой вспененного шлака в 30—50 раз превышает толщину шлака в спокойном состоянии, а его уровень достигает 6 метров от поверхности спокойной ванны. При этом вспененный жидкий металл подходит к горловине конвертера и отдельные всплески выбрасываются через неё. Иногда сама эмульсия переливается через горловину, что происходит в случаях спонтанного увеличения объёма газа. Естественно, такие выбросы и всплески представляют серьёзную опасность для людей, поэтому находиться рядом с конвертером во время продувки запрещено.
Защитная стена с амбразурами, сквозь которые в котел можно запустить термодатчик. Через отверстия идет такой жар, что одежда сталевара начинает дымиться через считанные секунды.
Кипящая сталь.
Челябинский металлургический комбинат занимает 5-е место среди предприятий черной металлургии России по объему производства металлопроката и является крупнейшим производителем нержавеющей стали в стране.
Комбинат занимает площадь более 22 квадратных километров и является градообразующим предприятием, обеспечивающим рабочими местами более 17 тысяч человек.
За семь десятилетий комбинат выпустил 175 миллионов тонн кокса, 120 миллионов тонн агломерата, 200 миллионов тонн чугуна, 270 миллионов тонн стали и отгрузил 225 миллионов тонн металлопродукции.
Разливка стали — завершающая стадия сталеплавильного процесса, во время которой сталь из жидкого состояния переходит в твёрдое и приобретает определённые форму, размер и массу. До недавнего времени единственным способом, применяемым на заводах, была разливка в изложницы. В этом случае выплавленная в конвертере сталь разливается в специальные формы разных размеров и оставляется для постепенного остывания. Затем готовые слитки извлекают из изложниц, обрезают излишки и направляют на дальнейшую обработку. Однако такой способ очень трудоёмок, требует большого количества изложниц и их периодической замены, а также расходует значительный объём огнеупорных материалов.
Более экономичным способом разливки стали, позволяющим получать стальную заготовку квадратного или прямоугольного сечения непосредственно из жидкого металла, является способ непрерывной разливки стали. Принцип непрерывности машины заключается в том, что до конца разливки стали из одного ковша следующий подаётся заблаговременно. Смена ковшей производится без остановки процесса литья за счёт использования части металла в промежуточной ёмкости. Металлурги такой метод называют «плавка на плавку».
Жидкий металл распределяется на шесть потоков. За каждым «ручьем» присматривает сталевар.
Нужно постоянно следить, чтобы не забивалась горловина кристаллизаторов, в которых сталь остывает и твердеет.
Бесконечные металлические слитки плавно вытекают из кристаллизатора и разрезаются газовой кислородной горелкой на мерные длины.
Готовые стальные слябы, требующие постепенного остывания, направляются в отдельный цех, где при помощи мостового крана в определённом порядке штабелируются на покрытом песком полу.
. Это уже другой цех комбината — универсальный рельсобалочный стан, на котором производятся рельсы длиной до 100 метров с применением новейших технологий прокатки, закалки, правки, отделки и контроля качества. Именно такие рельсы используются при строительстве высокоскоростных железнодорожных путей.
По закону подлости в день нашего приезда, стан находился на перевалке. У уже не раз бывал в других рельсобалочных станах, но такого масштабного производства еще не видел.
Для строительства нового стана изготовлено 15 500 тонн металлоконструкций — это равняется двум Эйфелевым башням. Площадь рельсобалочного производства составляет более 180 000 квадратных метров. На этой площади легко поместятся 26 полей олимпийского стадиона в Лужниках.
На устройство фундамента затрачено 144 500 кубических метров бетона. По объему это 35 больших плавательных бассейнов.
Длина рельсовой заготовки составляет всего 8,1 метров, вес – около тонны. Рельс или балка получается путем раската стальной заготовки, которую предварительно разогревают в нагревательной печи. Время производства одного 100-метрового рельса составляет чуть более 2 минут.
Нам удалось посмотреть лишь малую часть комбината. Чтобы оценить весь масштаб предприятия, нужно приезжать на пару недель с палатками…
Источник: chistoprudov.livejournal.com
Осторожно! Под катом очень жарко.
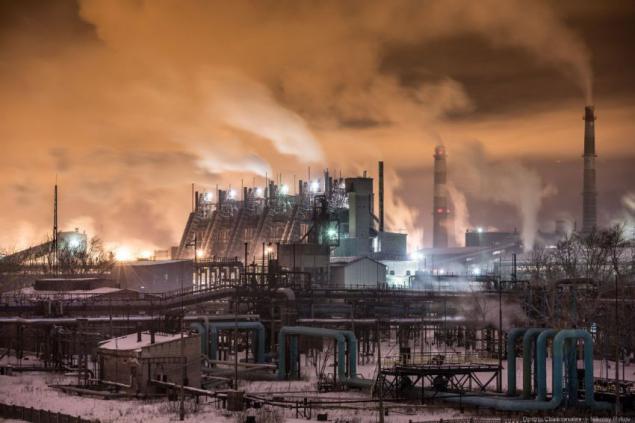
Когда-то железо получали на кострах в глиняных горшках или ямах без каких-либо специальных приспособлений. После долгого процесса обработки железа древние люди могли сделать себе наконечники для стрел или украшения для женщин. В современном мире потребности людей мало ушли от тех времён — им так же необходим металл. Но сегодня, после почти четырёхтысячелетней истории развития технологии производства металла, вместо костров на металлургических заводах используются доменные печи — агрегаты, самые крупные из которых могут выдавать до 12 тысяч тонн расплавленного чугуна в сутки.
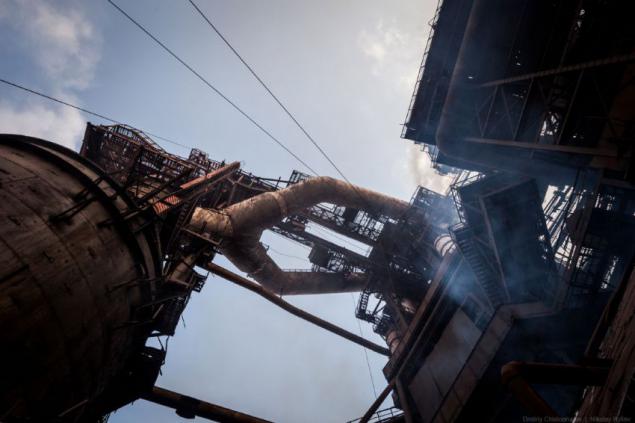
Доменная печь — совершенное металлургическое устройство, которое работает безостановочно. Лишь иногда, один раз в 10—20 лет, когда многие элементы её конструкции износились от многолетней эксплуатации, печь останавливают для проведения капитального ремонта. Основное назначение домны — получение первого жидкого металла из железной руды.
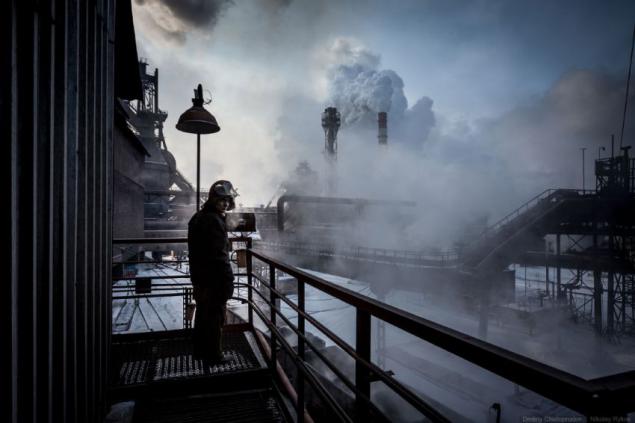
Почти весь объём печи, высота которой может достигать нескольких десятков этажей, занимает шихта — составленная в определённых пропорциях смесь. Она состоит из обогащённой руды, кокса в качестве топлива и флюса — вещества, которое во время плавки образует шлак, помогая отделить пустую породу и золу от металла. Это исходное сырьё через сложную конструкцию засыпного аппарата непрерывно загружается в доменную печь сверху и в процессе нагревания постепенно опускается вниз. Навстречу твёрдым материалам снизу под большим давлением подаётся обогащённый кислородом воздух, нагретый до температуры 1100—1400 градусов Цельсия.
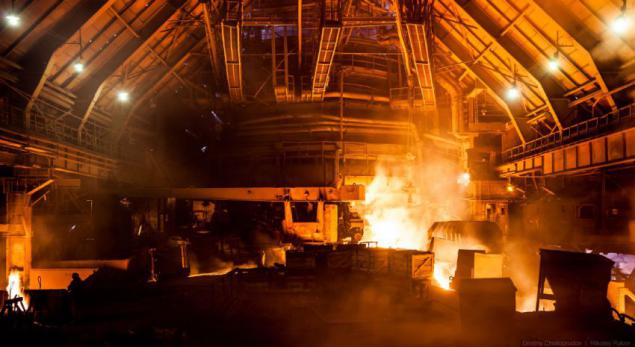
В таком режиме руда проходит весь путь сверху вниз за 4—6 часов и, дойдя до нижней части печи — горна, находится уже в жидком состоянии в виде расплавленных чугуна и шлака. В горне скапливается до тысячи и более тонн расплава, который постоянно заполняет эту часть печи и образует так называемый «мёртвый слой», высота которого составляет 0,6—1,7 метра. Когда в домне собирается достаточное количество чугуна и шлака, их выпускают через специальные огнеупорные отверстия — лётки, которые с этой целью каждый раз пробиваются бурильной машиной под управлением горнового.
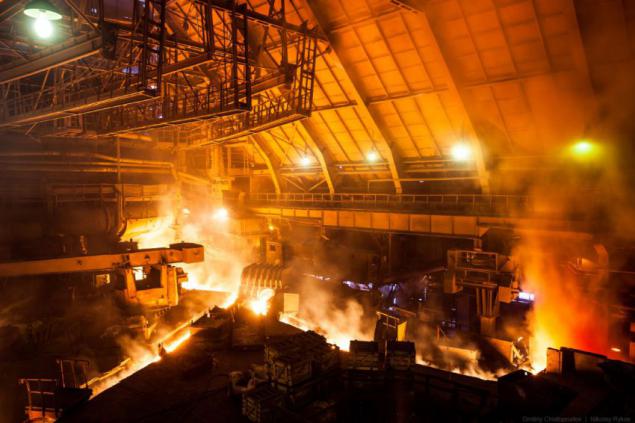
Выпуск чугуна происходит в среднем каждые 40 минут. Получив выход из домны, расплавленный металл сильной струёй бьёт из отверстия, попадает в оборудованную систему желобов и, протекая через весь литейный цех, разливается в чугуновозы.
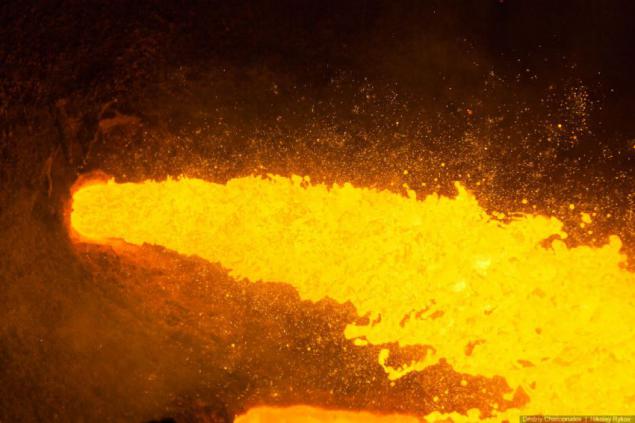
Горновой доменной печи — это первый, кто начинает работать с только что полученным расплавом. Он ведёт технологический процесс, наблюдая за ходом плавки визуально или по показаниям приборов, и своевременно выпускает чугун и шлак из доменной печи. Во многом от его мастерства и опыта зависят успехи или неудачи всей бригады доменного цеха.
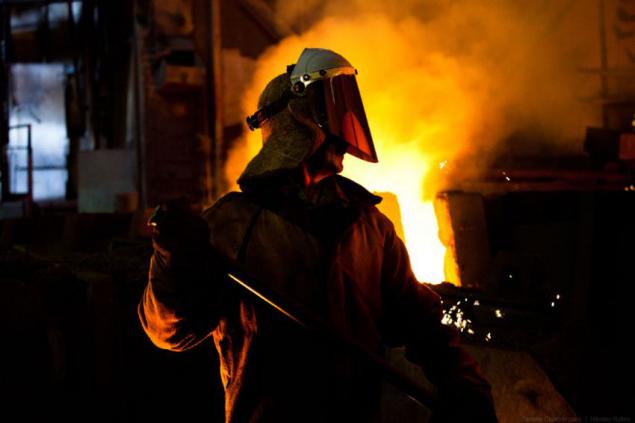
С каждой плавки берется проба. Охлаждённый чугунный слиток отправляется в экспресс-лабораторию, где производится анализ его химического состава. На основе этих данных технологи доменного цеха могут скорректировать состав шихты, загружаемой в доменную печь, либо изменить технологические параметры доменной плавки. Также данные анализа учитываются при дальнейшей переработке чугуна в конвертерном цехе.
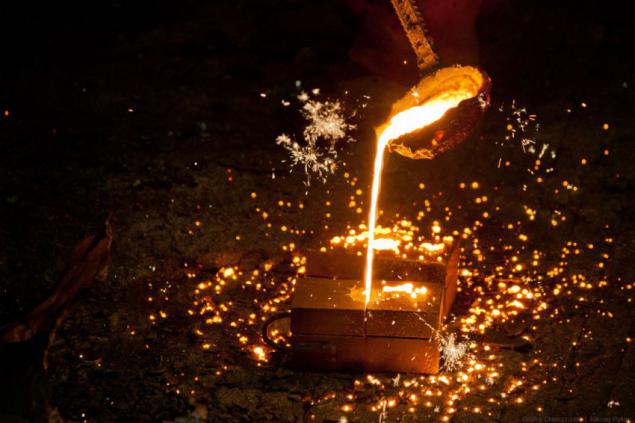
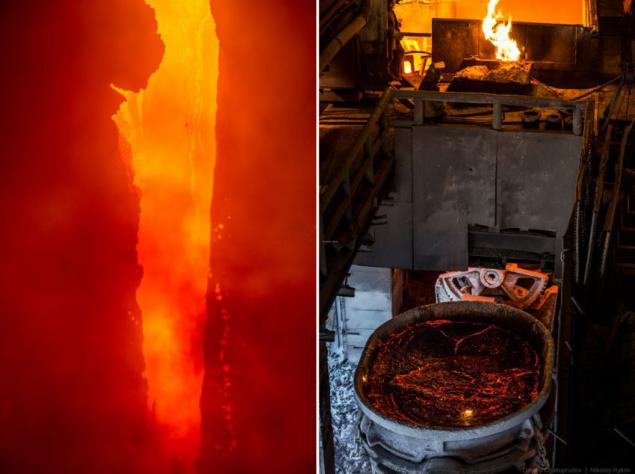
Кислородно-конвертерных цех. Сущность процесса переработки чугуна в сталь заключается в уменьшении содержания в чугуне ненужных примесей путём их окисления кислородом. Удаление этих элементов придаёт стали прочность и пластичность, а также делает её более податливой при обработке.
Чугуновозы поступают сюда по железнодорожным путям, которые проведены прямо в цех.
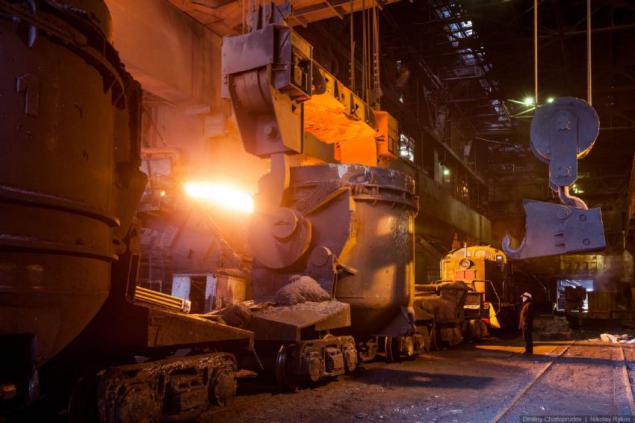
Основными материалами, загружаемыми в конвертер, являются металлический лом и чугун. Соотношение этих компонентов называется шихтой и измеряется примерно как один к четырём. Чугун поступает из доменного цеха в специальных ковшах-чугуновозах вместимостью от 150 до 600 тонн.
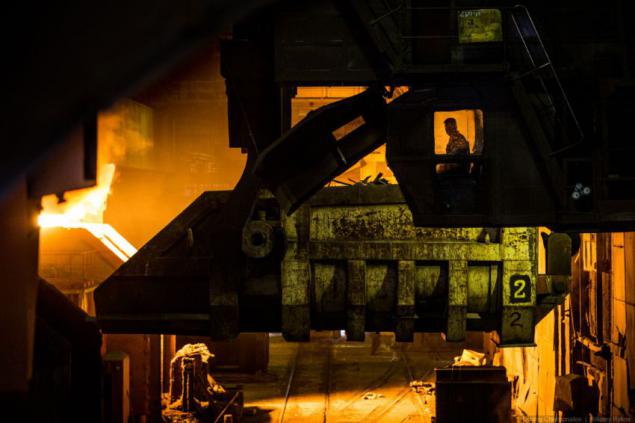
В качестве металлического лома обычно используются обрезки прокатных цехов и продукция Вторчермета. Металл засыпают в агрегат через специальную систему бункеров и весов-дозаторов, расположенных над конвертером. Сам конвертер представляет собой цилиндрический сосуд с суживающейся горловиной и сферическим днищем. Он закреплён в прочном несущем кольце, конструкция которого позволяет ему вращаться относительно поперечной оси на 360 градусов в любую сторону.
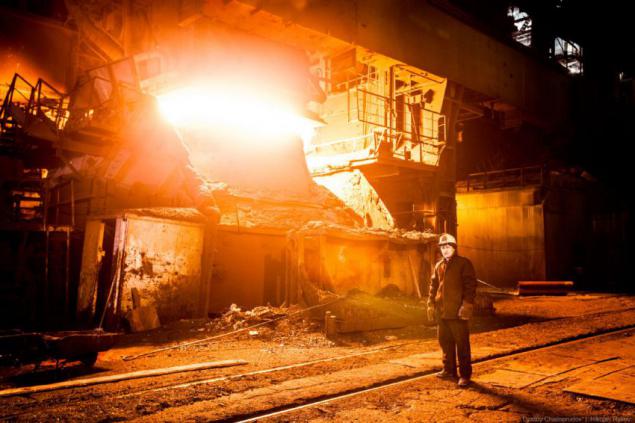
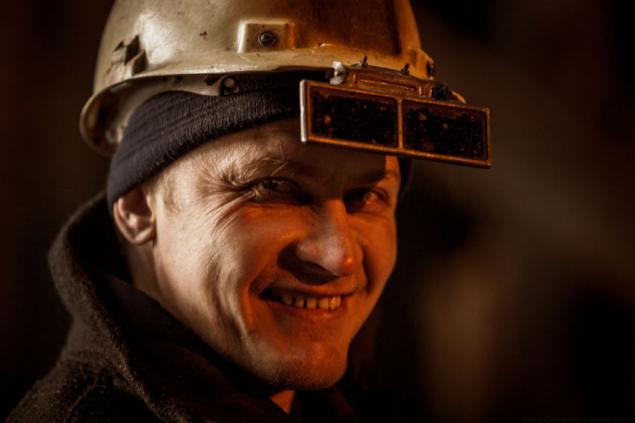
Чтобы перелить чугун, ковш с жидким металлом при помощи мостового крана поднимают к горловине наклонённого конвертера. Затем механизмы крана наклоняют чугуновозный ковш — и расплав переливается.
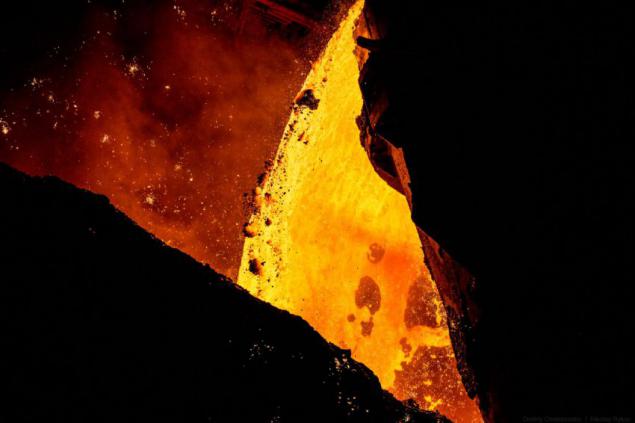
Когда основные материалы загружены, начинается продувка кислородом.
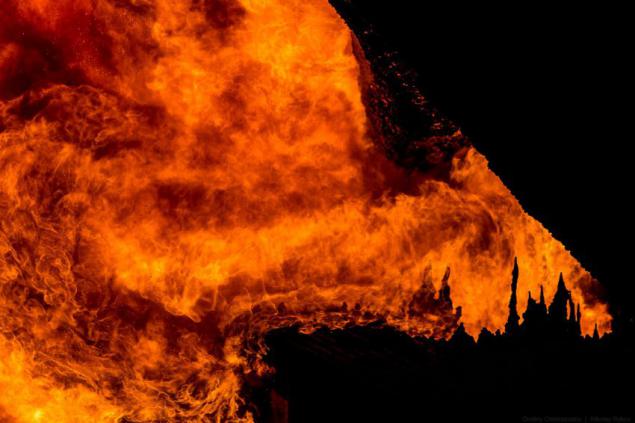
Слив шлака.
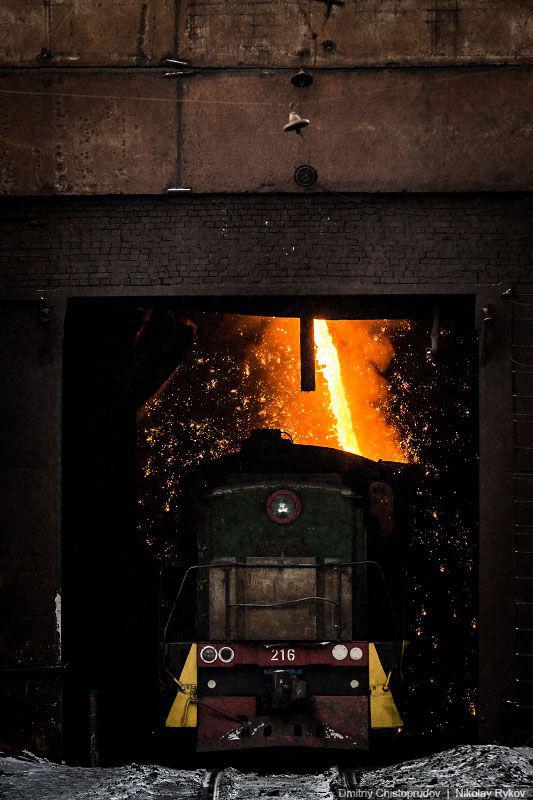
В некоторые периоды продувки слой вспененного шлака в 30—50 раз превышает толщину шлака в спокойном состоянии, а его уровень достигает 6 метров от поверхности спокойной ванны. При этом вспененный жидкий металл подходит к горловине конвертера и отдельные всплески выбрасываются через неё. Иногда сама эмульсия переливается через горловину, что происходит в случаях спонтанного увеличения объёма газа. Естественно, такие выбросы и всплески представляют серьёзную опасность для людей, поэтому находиться рядом с конвертером во время продувки запрещено.
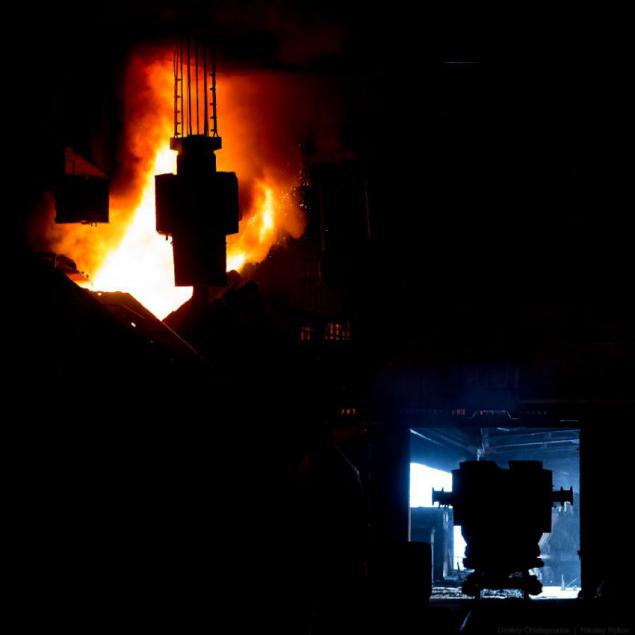
Защитная стена с амбразурами, сквозь которые в котел можно запустить термодатчик. Через отверстия идет такой жар, что одежда сталевара начинает дымиться через считанные секунды.
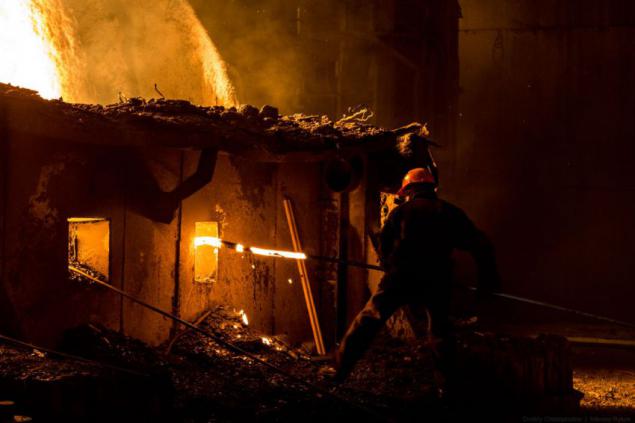
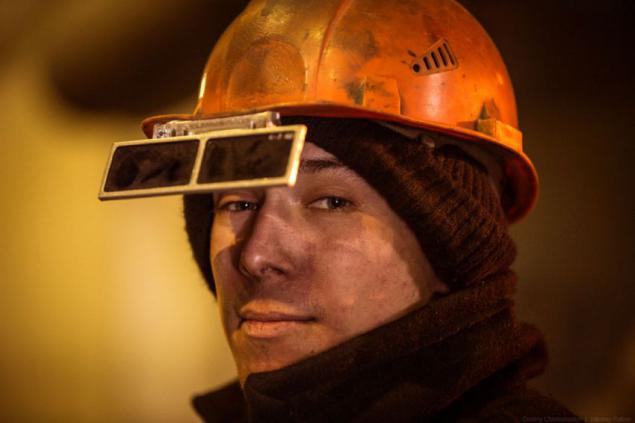
Кипящая сталь.
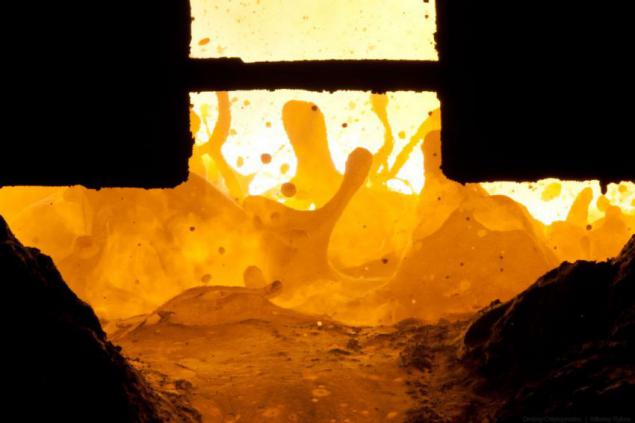
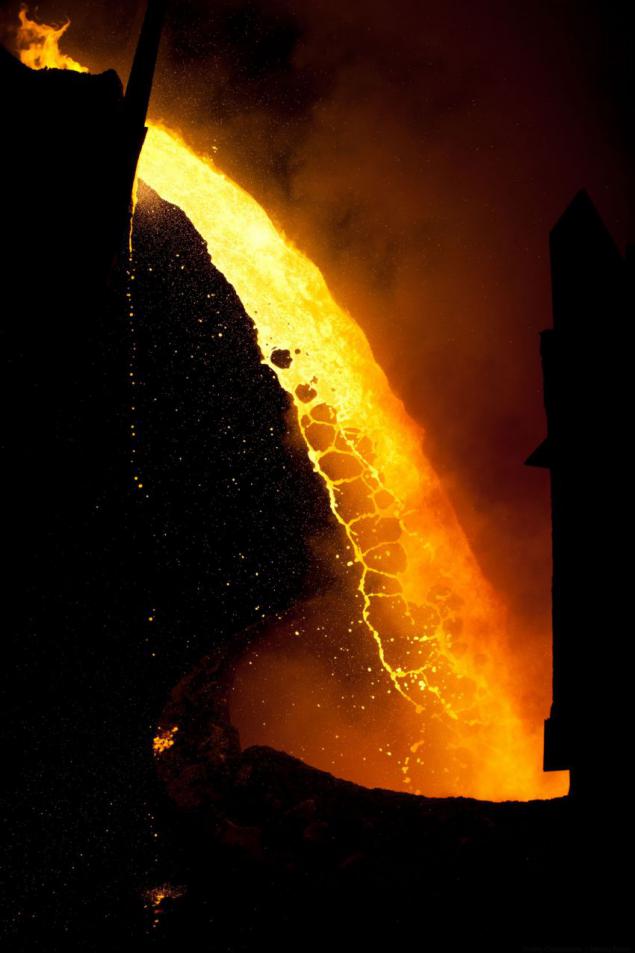
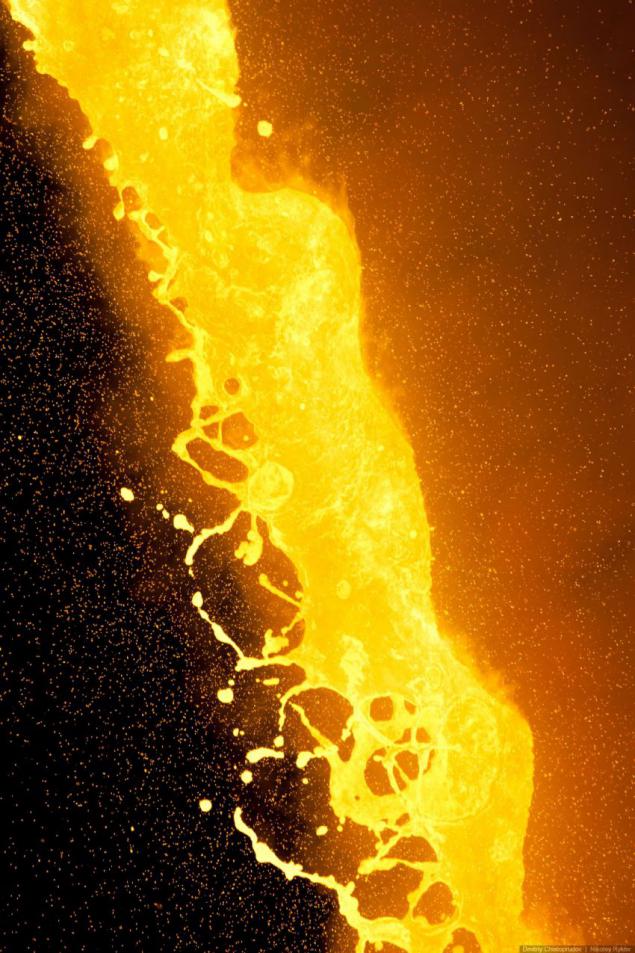
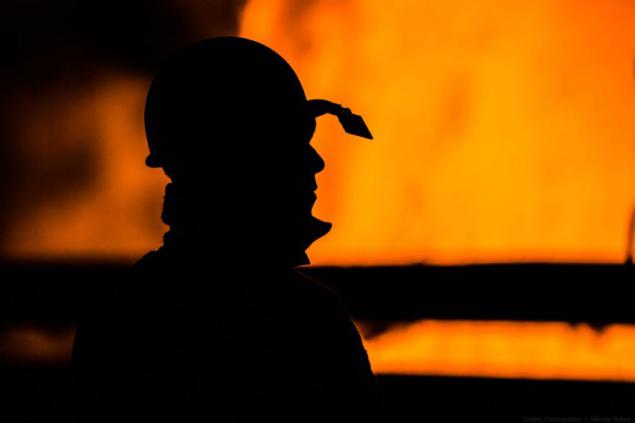
Челябинский металлургический комбинат занимает 5-е место среди предприятий черной металлургии России по объему производства металлопроката и является крупнейшим производителем нержавеющей стали в стране.
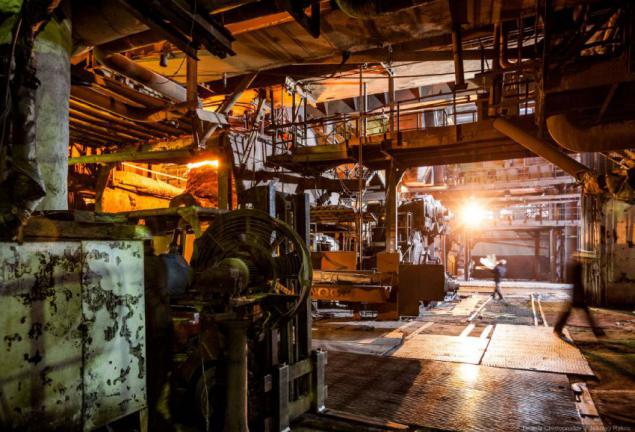
Комбинат занимает площадь более 22 квадратных километров и является градообразующим предприятием, обеспечивающим рабочими местами более 17 тысяч человек.
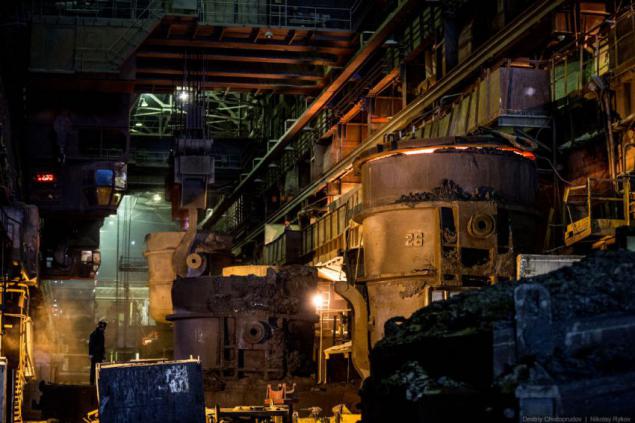
За семь десятилетий комбинат выпустил 175 миллионов тонн кокса, 120 миллионов тонн агломерата, 200 миллионов тонн чугуна, 270 миллионов тонн стали и отгрузил 225 миллионов тонн металлопродукции.
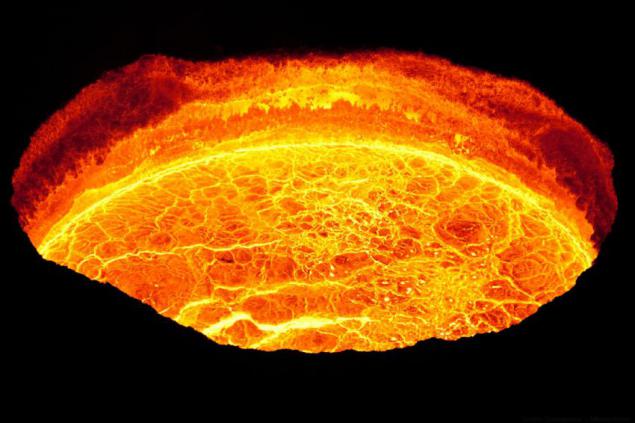
Разливка стали — завершающая стадия сталеплавильного процесса, во время которой сталь из жидкого состояния переходит в твёрдое и приобретает определённые форму, размер и массу. До недавнего времени единственным способом, применяемым на заводах, была разливка в изложницы. В этом случае выплавленная в конвертере сталь разливается в специальные формы разных размеров и оставляется для постепенного остывания. Затем готовые слитки извлекают из изложниц, обрезают излишки и направляют на дальнейшую обработку. Однако такой способ очень трудоёмок, требует большого количества изложниц и их периодической замены, а также расходует значительный объём огнеупорных материалов.
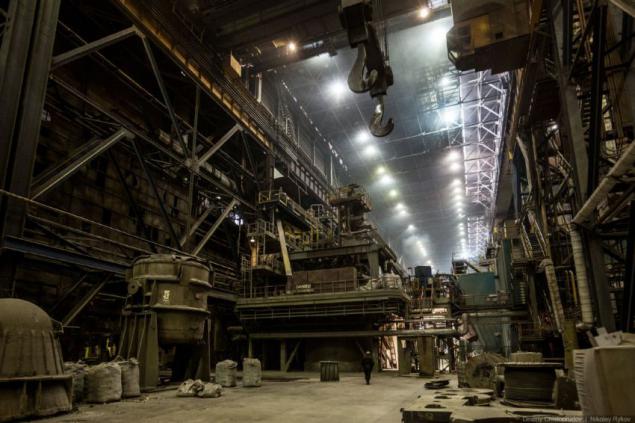
Более экономичным способом разливки стали, позволяющим получать стальную заготовку квадратного или прямоугольного сечения непосредственно из жидкого металла, является способ непрерывной разливки стали. Принцип непрерывности машины заключается в том, что до конца разливки стали из одного ковша следующий подаётся заблаговременно. Смена ковшей производится без остановки процесса литья за счёт использования части металла в промежуточной ёмкости. Металлурги такой метод называют «плавка на плавку».
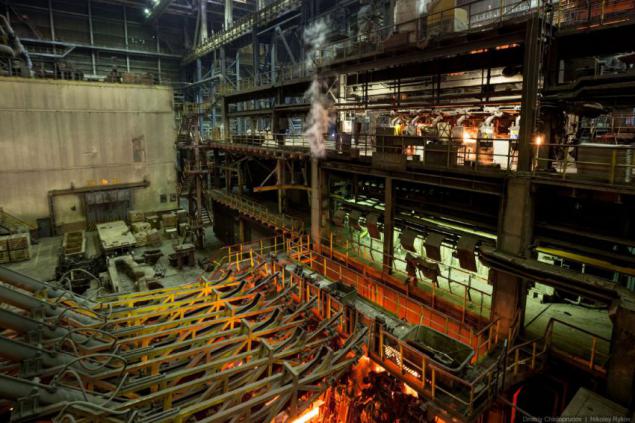
Жидкий металл распределяется на шесть потоков. За каждым «ручьем» присматривает сталевар.
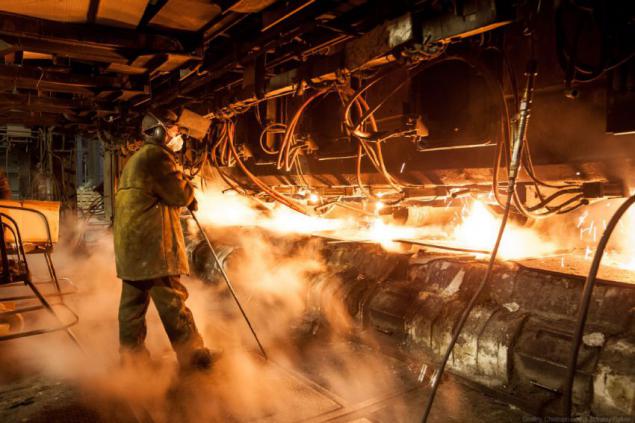
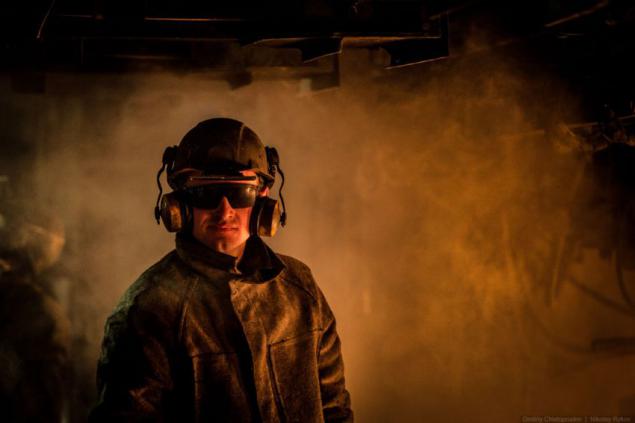
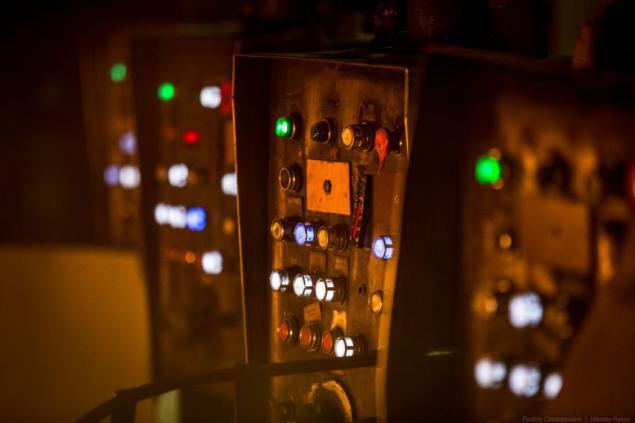
Нужно постоянно следить, чтобы не забивалась горловина кристаллизаторов, в которых сталь остывает и твердеет.
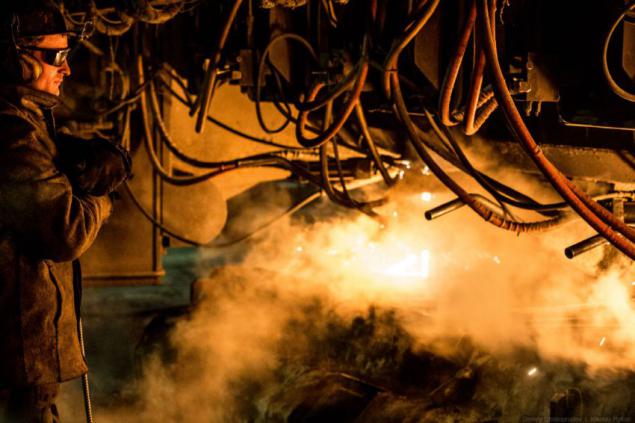
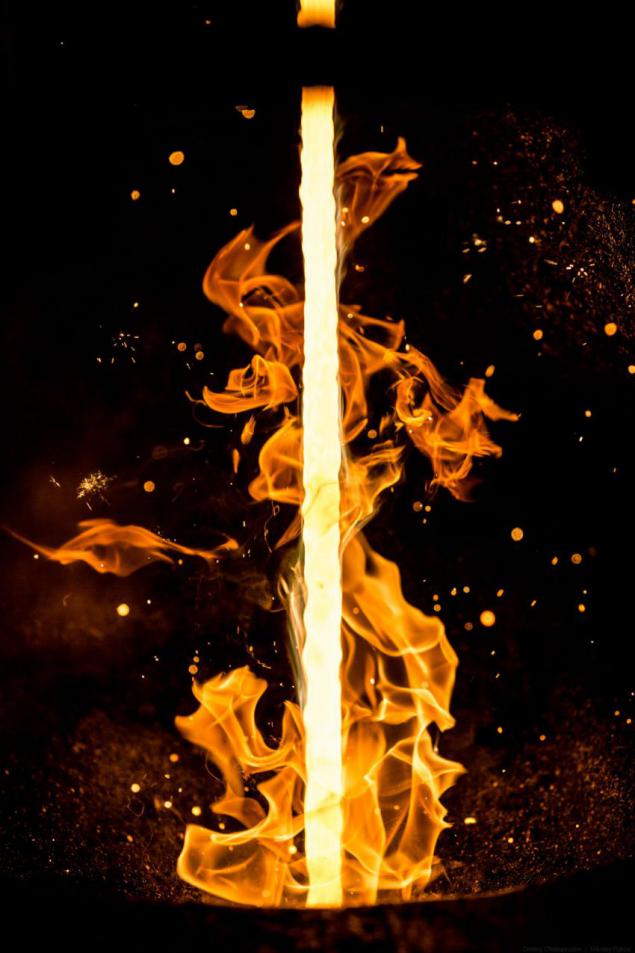
Бесконечные металлические слитки плавно вытекают из кристаллизатора и разрезаются газовой кислородной горелкой на мерные длины.
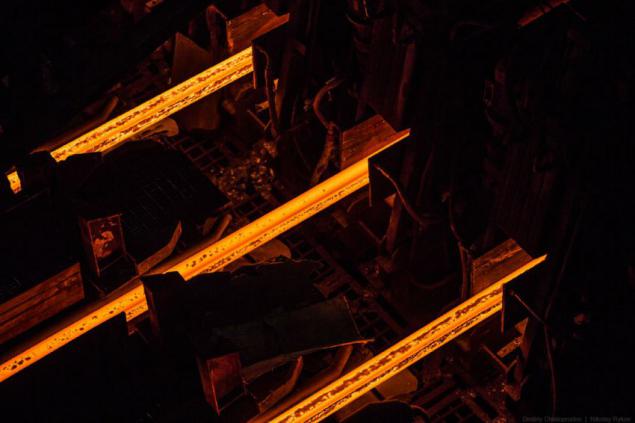
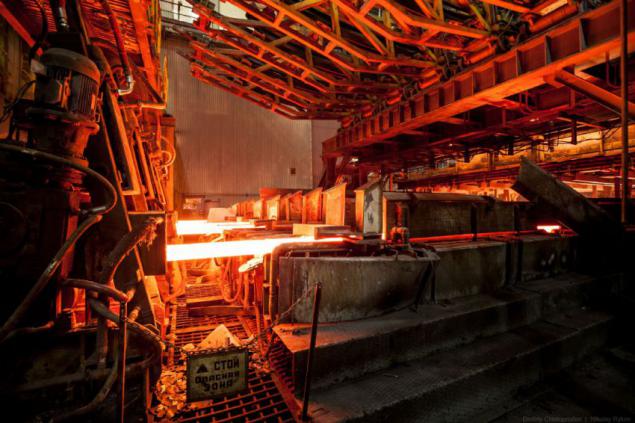
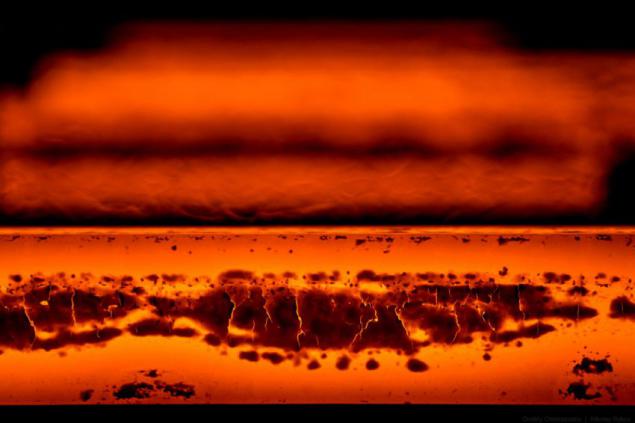
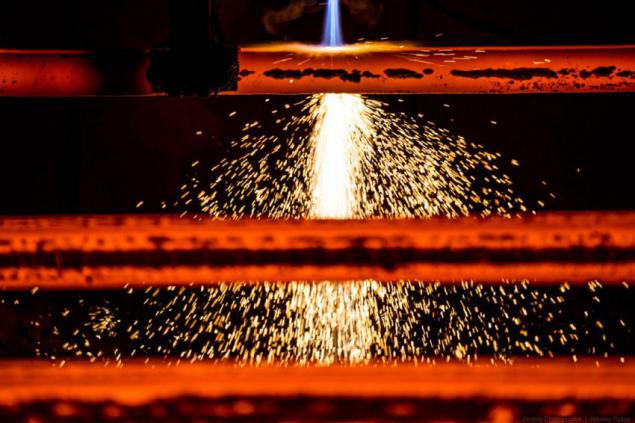
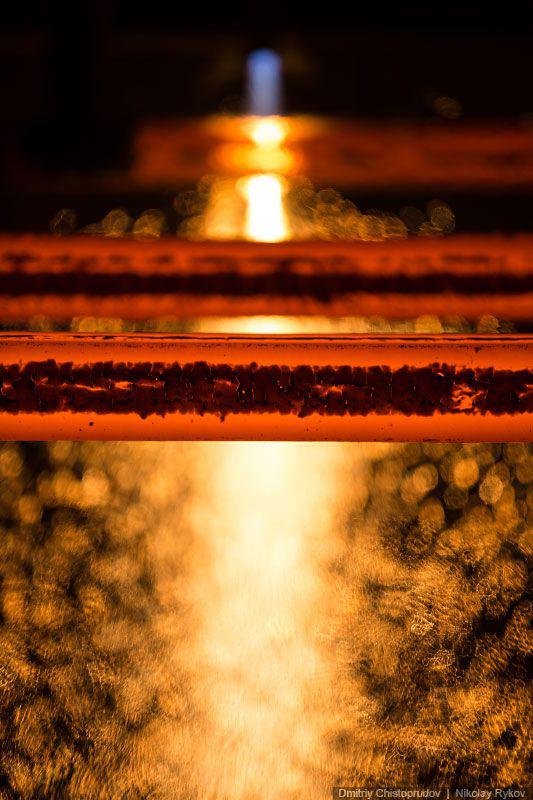
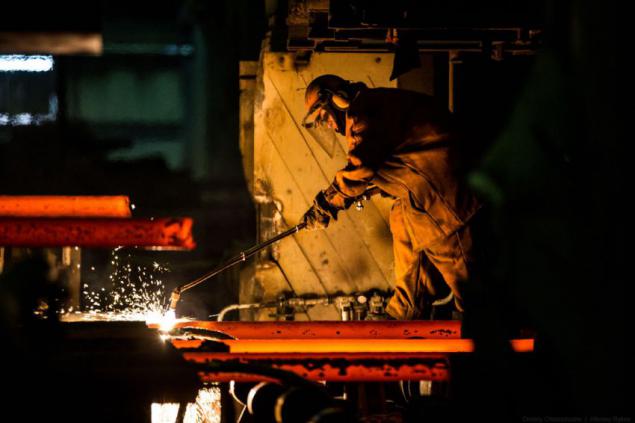
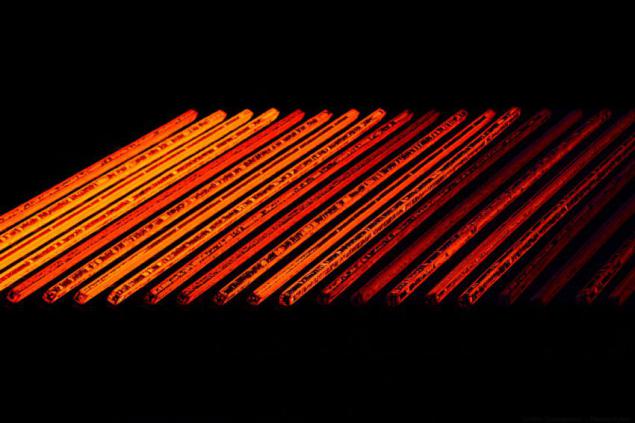
Готовые стальные слябы, требующие постепенного остывания, направляются в отдельный цех, где при помощи мостового крана в определённом порядке штабелируются на покрытом песком полу.
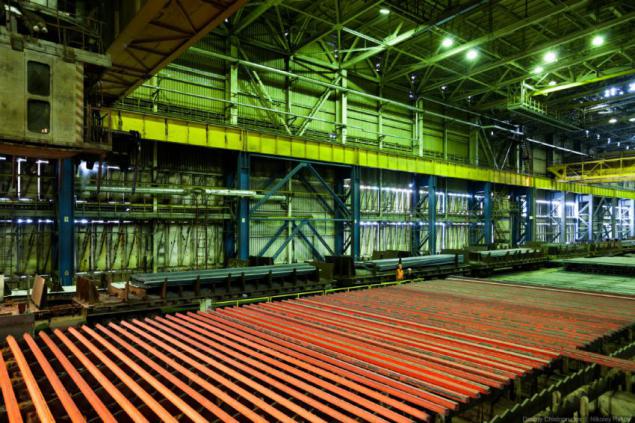
. Это уже другой цех комбината — универсальный рельсобалочный стан, на котором производятся рельсы длиной до 100 метров с применением новейших технологий прокатки, закалки, правки, отделки и контроля качества. Именно такие рельсы используются при строительстве высокоскоростных железнодорожных путей.

По закону подлости в день нашего приезда, стан находился на перевалке. У уже не раз бывал в других рельсобалочных станах, но такого масштабного производства еще не видел.
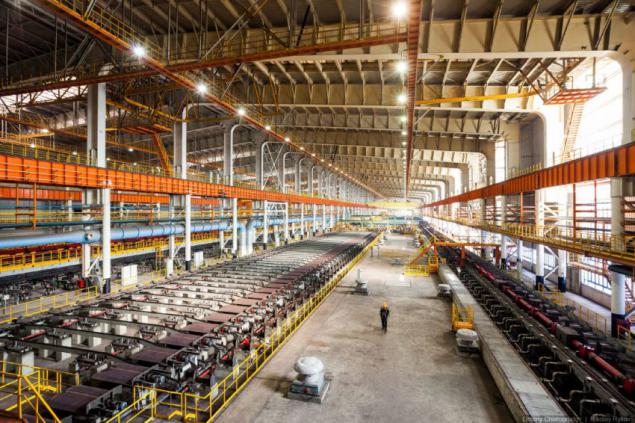
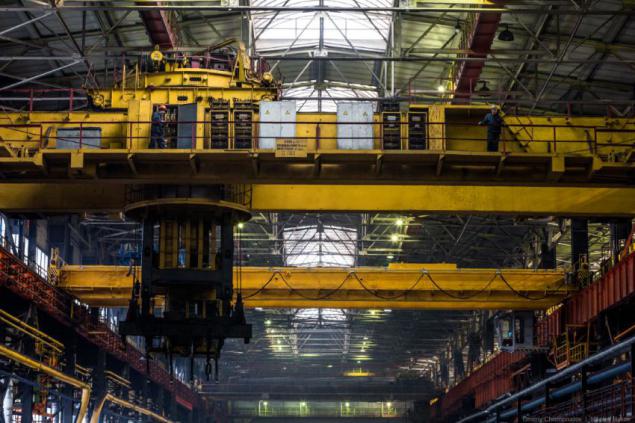
Для строительства нового стана изготовлено 15 500 тонн металлоконструкций — это равняется двум Эйфелевым башням. Площадь рельсобалочного производства составляет более 180 000 квадратных метров. На этой площади легко поместятся 26 полей олимпийского стадиона в Лужниках.
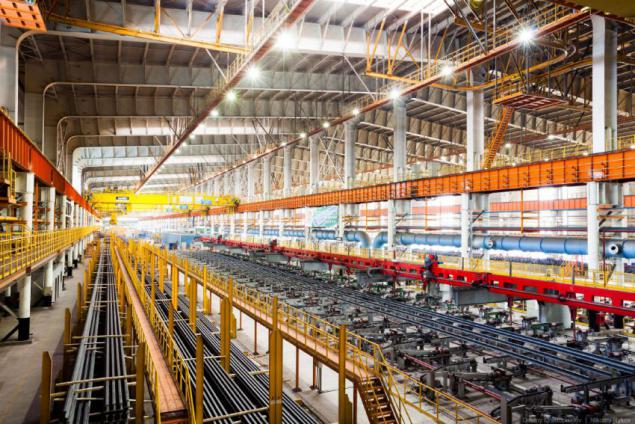
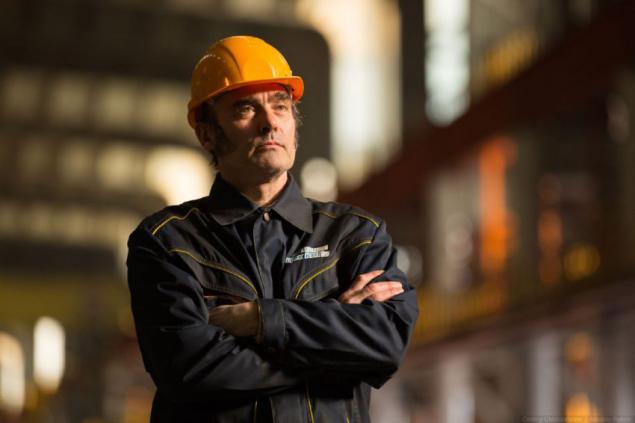
На устройство фундамента затрачено 144 500 кубических метров бетона. По объему это 35 больших плавательных бассейнов.
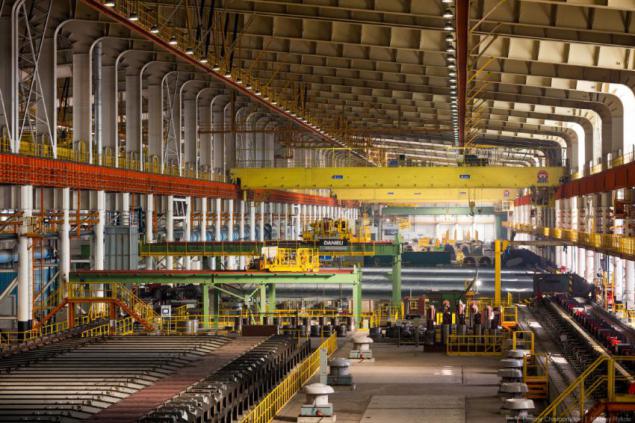
Длина рельсовой заготовки составляет всего 8,1 метров, вес – около тонны. Рельс или балка получается путем раската стальной заготовки, которую предварительно разогревают в нагревательной печи. Время производства одного 100-метрового рельса составляет чуть более 2 минут.
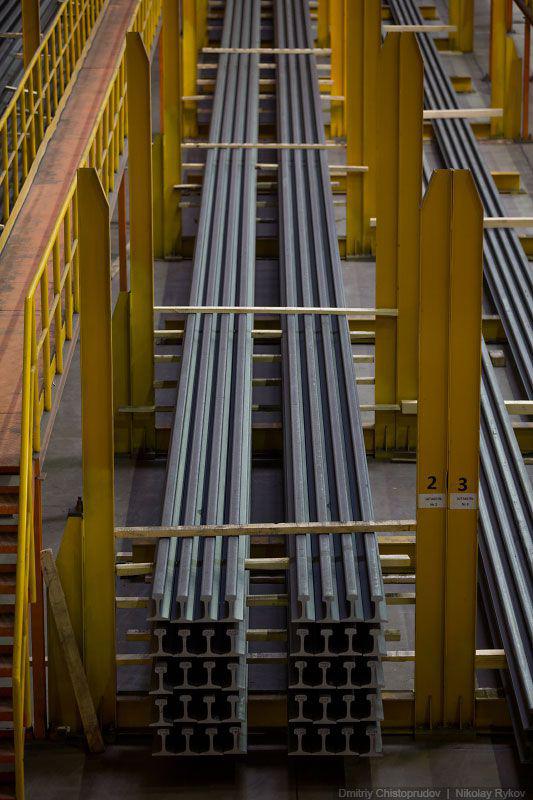
Нам удалось посмотреть лишь малую часть комбината. Чтобы оценить весь масштаб предприятия, нужно приезжать на пару недель с палатками…
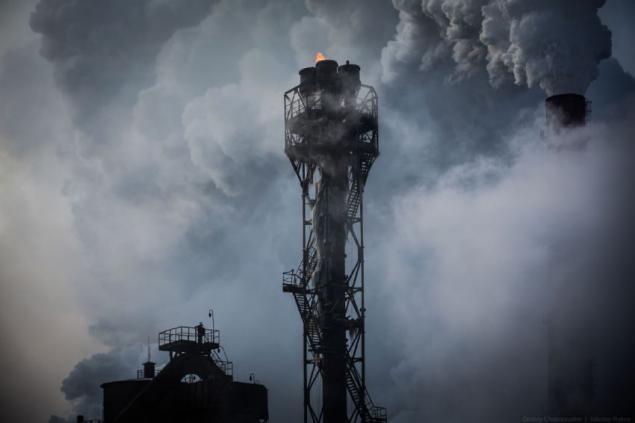
Источник: chistoprudov.livejournal.com
Портал БАШНЯ. Копирование, Перепечатка возможна при указании активной ссылки на данную страницу.