1292
Chelyabinsk Planta Metalúrgica
Chelyabinsk Planta Metalúrgica - Ciclo de acero más grande de Rusia integrado para la producción de aceros de alta calidad. Esta es una de las pocas empresas en el país, que tiene derecho a ceder sus propios productos de índice - ES (Chelyabinsk Acero). En este post se puede ver cómo los chicos duros producen el famoso acero Chelyabinsk.
Precaución Bajo el corte es muy caliente.
Una vez que el hierro se produce en la hoguera en ollas de barro o pozos sin necesidad de herramientas especiales. Después de un largo proceso de tratamiento de los pueblos antiguos de hierro podría hacer unas puntas de flecha y joyas para las mujeres. En el mundo de hoy necesita personas han dejado poco de aquellos tiempos - que sólo necesita un poco de metal. Pero hoy, después de casi cuatro milenios historia del desarrollo de la tecnología de producción de metal, en lugar de los incendios en los hornos de las acerías hornos usados - unidades, la mayor de las cuales puede producir hasta 12 mil toneladas de hierro fundido por día.
Alto Horno - un dispositivo metalúrgica perfecta que funciona sin parar. Sólo a veces, una vez en 10-20 años, cuando muchos elementos de su diseño usado por muchos años de funcionamiento, el horno se apaga para una revisión. El objetivo principal del alto horno - proporcionar un primer metal líquido a partir de mineral de hierro
.
Casi todo el volumen del horno, cuya altura puede alcanzar varias decenas de plantas, se encarga de la - una mezcla de ciertas proporciones. Se compone de mineral enriquecido, coque como combustible y flujo - una sustancia que se forma durante la escoria de fundición, ayudando a separar la ganga y las cenizas desde el metal. Esta materia prima a través de un aparato de diseño relleno complicada cargado continuamente en un alto horno de la parte superior y en el proceso de calentamiento es gradualmente desciende. Hacia la parte inferior de materiales sólidos bajo aire enriquecido con oxígeno a alta presión se alimenta calienta a una temperatura de 1100-1400 grados Celsius.
En este modo, el mineral pasa todo el camino de arriba a abajo durante 4-6 horas y, antes de llegar a la parte inferior del horno - de la solera, ya está en un estado líquido en la forma de hierro fundido y la escoria. En montañosa acumulada hasta mil o más toneladas de fusión, que llena constantemente esta parte del horno y forma una llamada "capa de muertos", cuya altura es de 0, 6-1, 7 metros. Cuando va a una cantidad suficiente de hierro en lingotes de alto horno y escoria, que se liberan a través de un agujeros refractarios especiales - categoría, para ello cada vez que golpeó la máquina de perforación funcionando furnaceman
.
La liberación de hierro ocurre en promedio cada 40 minutos. Tener una manera de salir del horno alto, el metal fundido es fuerte chorro golpea fuera del agujero, entra en el sistema equipado con canaletas y fluye a través de la fundición vierte en chugunovozy.
Alto horno Hearth - el primero que comenzó a trabajar con la masa fundida recién obtenido. Lidera el proceso tecnológico, observando el progreso de fusión visualmente o por lecturas de los instrumentos, y oportuna produce hierro y escoria de alto horno. En muchos sentidos, de su éxito o fracaso habilidad y experiencia depende de la explosión tienda de horno de todo el equipo.
Con cada serie se toma la muestra. Chilled lingote de hierro fundido va a expresar el laboratorio responsable del análisis de su composición química. Sobre la base de estos datos, tecnología de explosión tienda de horno puede ajustar la composición de la carga cargado en un alto horno, o cambiar los parámetros tecnológicos de alto horno. Además, el análisis de los datos se tienen en cuenta en el proceso posterior de arrabio en la tienda del convertidor.
Tienda de BOF. RESUMEN proceso de conversión de hierro en acero es reducir el contenido de impurezas no deseadas en el hierro por oxidación del mismo con oxígeno. La eliminación de estos elementos da la fuerza y ductilidad del acero, y también hace que sea más dócil durante el procesamiento.
Chugunovozy llegado aquí en las vías del ferrocarril, que se celebran directamente en la tienda.
Los principales materiales que se cargan en el convertidor son chatarra y hierro. La relación de estos componentes se llama la carga y mide aproximadamente de uno a cuatro. Hierro viene de la tienda de los altos hornos de la capacidad especial de cubos-chugunovozah de 150 a 600 toneladas.
Como chatarra utilizado comúnmente trenes de laminación y corte productos Vtorchermet. El metal se vierte en la unidad a través de un sistema especial de bunkers y escalas de medición situados sobre el convertidor. Mismo Converter es un recipiente cilíndrico con un cuello cónico y parte inferior esférica. Se fija en un anillo de soporte robusto cuyo diseño permite que gire en relación con el eje transversal 360 grados en cualquier dirección.
Para verter hierro fundido líquido cuchara de metal por medio de una grúa para levantar el convertidor de cuello inclinado. Entonces los mecanismos de la grúa inclinada cucharas de hierro - y la masa fundida se vierte
.
Una vez que se cargan los materiales básicos, que empieza a soplar el oxígeno.
Escurrir escoria.
En algunos períodos de soplado de una capa de espuma de escoria 30-50 veces mayor que el espesor de la escoria en un estado de calma, y su nivel alcanza los 6 metros de la superficie de un baño tranquilo. Al mismo tiempo, el metal fundido de espuma se aproxima a la boca del convertidor y algunos picos lanzados a través de él. A veces ella emulsión se vierte a través del cuello, lo que sucede en los casos de aumento espontáneo en el volumen de gas. Naturalmente, este tipo de emisiones y explosiones representan un grave peligro para las personas, por lo que se quedan cerca del convertidor durante el soplado está prohibido.
Muro de protección de lagunas a través del cual se pueden ejecutar el sensor de temperatura de la caldera. A través de los agujeros son tan caliente, que la siderúrgica ropa comienza a fumar en cuestión de segundos.
Hervir el acero.
Chelyabinsk Planta Metalúrgica tiene el quinto lugar entre la industria siderúrgica de Rusia en términos de producción de acero y es el mayor productor de acero inoxidable en el país.
La planta tiene una superficie de más de 22 kilómetros cuadrados y es un gran generador de empleo, proporcionando puestos de trabajo para más de 17 mil personas.
Durante siete décadas, la planta ha producido 175 millones de toneladas de coque, 120 millones de toneladas de sinter, 200 millones de toneladas de hierro, 270 millones de toneladas de acero y se envían 225 millones de toneladas de productos de acero.
Fundición de acero - la etapa final del proceso de fabricación de acero, durante el cual el acero de un estado líquido a sólido y adquiere cierta forma, tamaño y peso. Hasta hace poco, el único método utilizado en las fábricas vertía en moldes. En este caso, fundido en el acero convertidor se vierte en moldes especiales de diferentes tamaños y se dejó para el enfriamiento gradual. Entonces lingotes listos recuperados del molde, cortar el exceso y enviados para su posterior procesamiento. Sin embargo, este método es muy intensivo en mano de obra, requiere una gran cantidad de moldes y su sustitución periódica y consume una cantidad significativa de materiales refractarios.
Un método de moldeo más económico, permite obtener un tocho de acero de sección transversal cuadrada o rectangular directamente de metal fundido, un método de colada continua de acero. Máquinas Going es que hasta el final de la fundición de un cubo sirvió el siguiente avance. Cambio de la cubeta se hace sin detener el proceso de fundición debido al uso del metal en el depósito intermedio. Los productores de acero como un método denominado "fusión en la fusión."
El metal líquido se divide en seis corrientes. Detrás de cada "arroyo" parece obrero metalúrgico.
Es necesario un seguimiento constante de no sacrificar a los moldes del cuello en el que el acero se enfría y se endurece.
Barras de metal Infinite fluyen suavemente del molde y se cortan quemador de gas de oxígeno a la longitud.
Losas de acero acabado, que requieren un enfriamiento gradual se envían en un taller independiente, donde con la ayuda de una grúa en un cierto orden se apilan en el suelo cubierto de arena.
. Este es otro complejo de plantas - planta de laminación universal, que produjo los carriles de hasta 100 metros con la última tecnología de laminado, templado, enderezar, acabado y control de calidad. Tales carriles se utilizan en la construcción de ferrocarriles de alta velocidad.
De acuerdo con la ley de la mezquindad en el día de nuestra llegada, el campamento estaba en el transbordo. Hemos estado en varias ocasiones en otro tren de laminación, pero este tipo de producción a gran escala aún no se ve.
Para la construcción de la nueva planta de producción de 15.500 toneladas de acero - esto es dos de la Torre Eiffel. Ferroviario Área y la fabricación de más de 180, 000 metros cuadrados. Esta zona es fácil de instalar 26 campos en el estadio olímpico Luzhniki.
En el dispositivo de la fundación se llevó 144.500 metros cúbicos de hormigón. Por volumen 35 es una gran piscina.
La longitud de la pieza de ferrocarril está a sólo 8, 1 m, peso - cerca de una tonelada. El carril o viga es producido por un tocho de acero peal, que se precalienta en el horno de calentamiento. El tiempo de producción de un carril de 100 metros es poco más de 2 minutos.
Nos las arreglamos para ver sólo una pequeña parte de la planta. Para apreciar la escala de la empresa, es necesario llegar a un par de semanas con tiendas de campaña ...
Fuente: chistoprudov.livejournal.com
Precaución Bajo el corte es muy caliente.
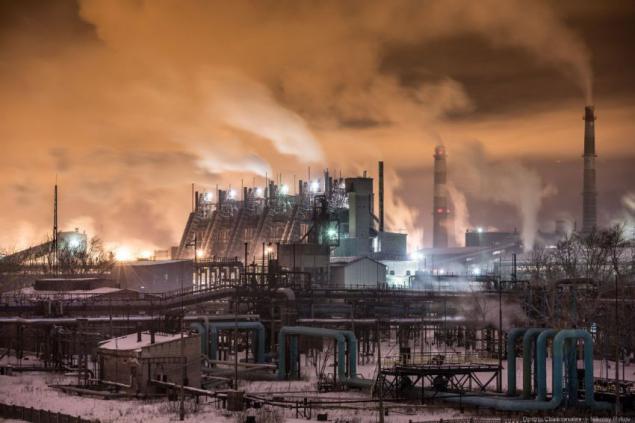
Una vez que el hierro se produce en la hoguera en ollas de barro o pozos sin necesidad de herramientas especiales. Después de un largo proceso de tratamiento de los pueblos antiguos de hierro podría hacer unas puntas de flecha y joyas para las mujeres. En el mundo de hoy necesita personas han dejado poco de aquellos tiempos - que sólo necesita un poco de metal. Pero hoy, después de casi cuatro milenios historia del desarrollo de la tecnología de producción de metal, en lugar de los incendios en los hornos de las acerías hornos usados - unidades, la mayor de las cuales puede producir hasta 12 mil toneladas de hierro fundido por día.
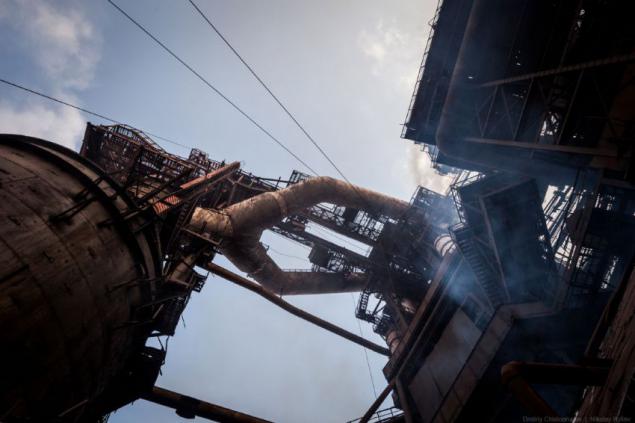
Alto Horno - un dispositivo metalúrgica perfecta que funciona sin parar. Sólo a veces, una vez en 10-20 años, cuando muchos elementos de su diseño usado por muchos años de funcionamiento, el horno se apaga para una revisión. El objetivo principal del alto horno - proporcionar un primer metal líquido a partir de mineral de hierro
.
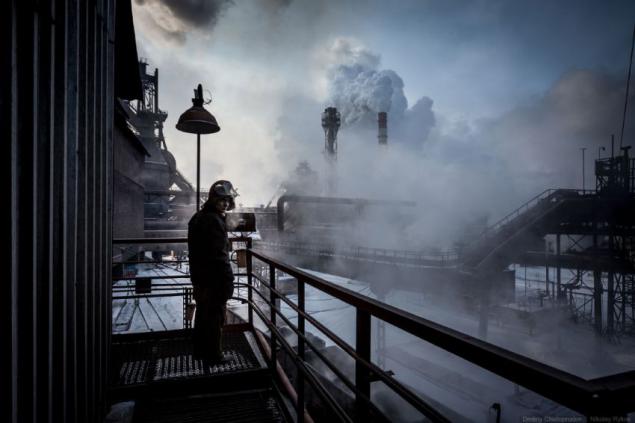
Casi todo el volumen del horno, cuya altura puede alcanzar varias decenas de plantas, se encarga de la - una mezcla de ciertas proporciones. Se compone de mineral enriquecido, coque como combustible y flujo - una sustancia que se forma durante la escoria de fundición, ayudando a separar la ganga y las cenizas desde el metal. Esta materia prima a través de un aparato de diseño relleno complicada cargado continuamente en un alto horno de la parte superior y en el proceso de calentamiento es gradualmente desciende. Hacia la parte inferior de materiales sólidos bajo aire enriquecido con oxígeno a alta presión se alimenta calienta a una temperatura de 1100-1400 grados Celsius.
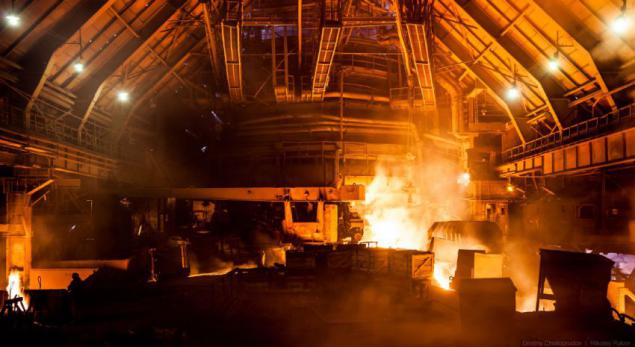
En este modo, el mineral pasa todo el camino de arriba a abajo durante 4-6 horas y, antes de llegar a la parte inferior del horno - de la solera, ya está en un estado líquido en la forma de hierro fundido y la escoria. En montañosa acumulada hasta mil o más toneladas de fusión, que llena constantemente esta parte del horno y forma una llamada "capa de muertos", cuya altura es de 0, 6-1, 7 metros. Cuando va a una cantidad suficiente de hierro en lingotes de alto horno y escoria, que se liberan a través de un agujeros refractarios especiales - categoría, para ello cada vez que golpeó la máquina de perforación funcionando furnaceman
.
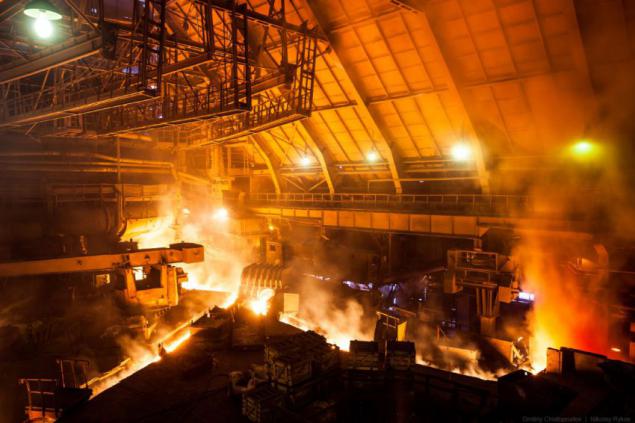
La liberación de hierro ocurre en promedio cada 40 minutos. Tener una manera de salir del horno alto, el metal fundido es fuerte chorro golpea fuera del agujero, entra en el sistema equipado con canaletas y fluye a través de la fundición vierte en chugunovozy.
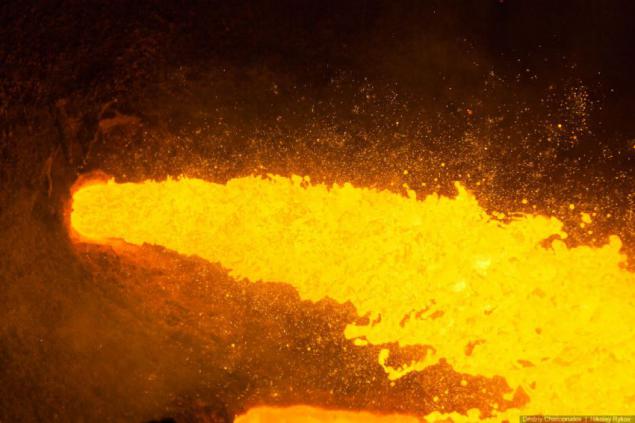
Alto horno Hearth - el primero que comenzó a trabajar con la masa fundida recién obtenido. Lidera el proceso tecnológico, observando el progreso de fusión visualmente o por lecturas de los instrumentos, y oportuna produce hierro y escoria de alto horno. En muchos sentidos, de su éxito o fracaso habilidad y experiencia depende de la explosión tienda de horno de todo el equipo.
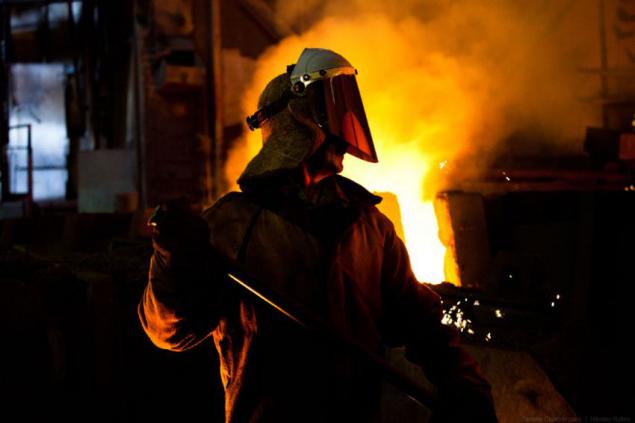
Con cada serie se toma la muestra. Chilled lingote de hierro fundido va a expresar el laboratorio responsable del análisis de su composición química. Sobre la base de estos datos, tecnología de explosión tienda de horno puede ajustar la composición de la carga cargado en un alto horno, o cambiar los parámetros tecnológicos de alto horno. Además, el análisis de los datos se tienen en cuenta en el proceso posterior de arrabio en la tienda del convertidor.
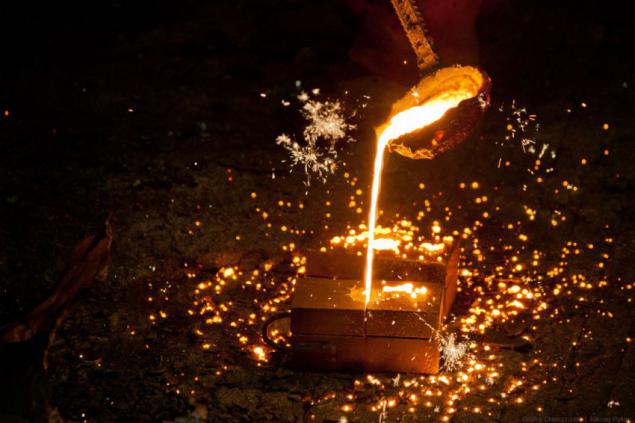
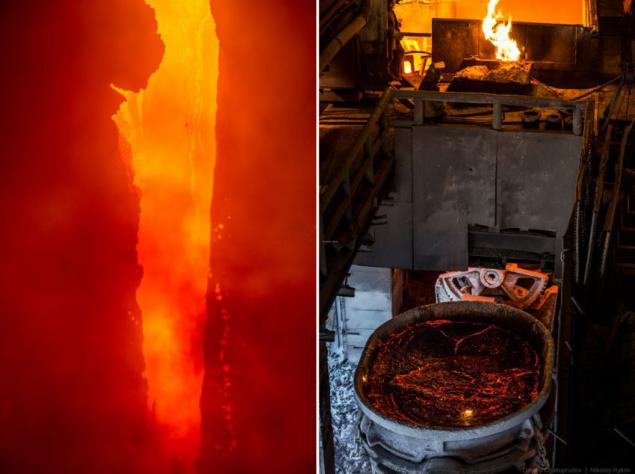
Tienda de BOF. RESUMEN proceso de conversión de hierro en acero es reducir el contenido de impurezas no deseadas en el hierro por oxidación del mismo con oxígeno. La eliminación de estos elementos da la fuerza y ductilidad del acero, y también hace que sea más dócil durante el procesamiento.
Chugunovozy llegado aquí en las vías del ferrocarril, que se celebran directamente en la tienda.
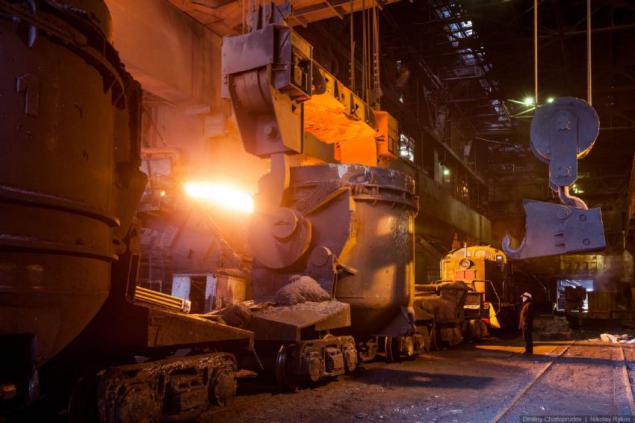
Los principales materiales que se cargan en el convertidor son chatarra y hierro. La relación de estos componentes se llama la carga y mide aproximadamente de uno a cuatro. Hierro viene de la tienda de los altos hornos de la capacidad especial de cubos-chugunovozah de 150 a 600 toneladas.
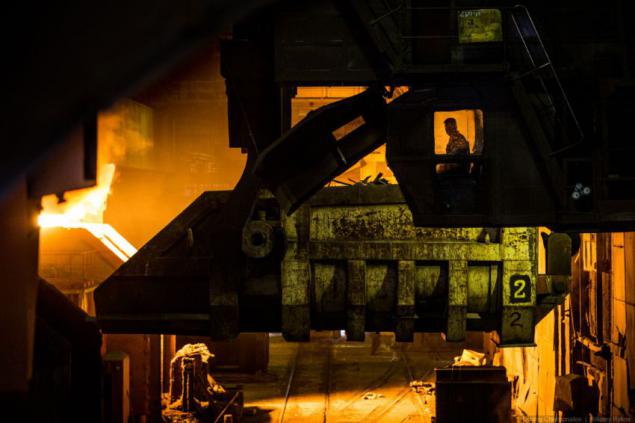
Como chatarra utilizado comúnmente trenes de laminación y corte productos Vtorchermet. El metal se vierte en la unidad a través de un sistema especial de bunkers y escalas de medición situados sobre el convertidor. Mismo Converter es un recipiente cilíndrico con un cuello cónico y parte inferior esférica. Se fija en un anillo de soporte robusto cuyo diseño permite que gire en relación con el eje transversal 360 grados en cualquier dirección.
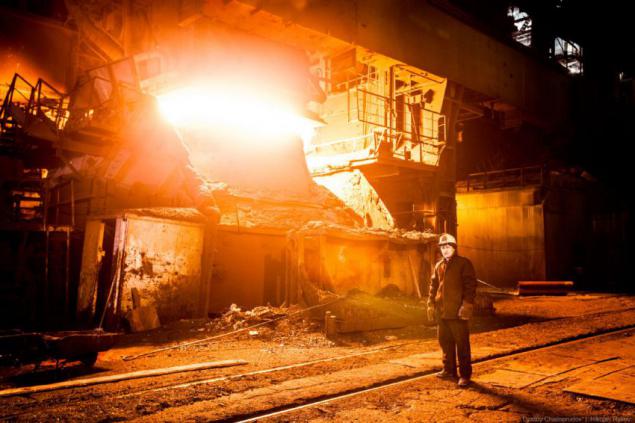
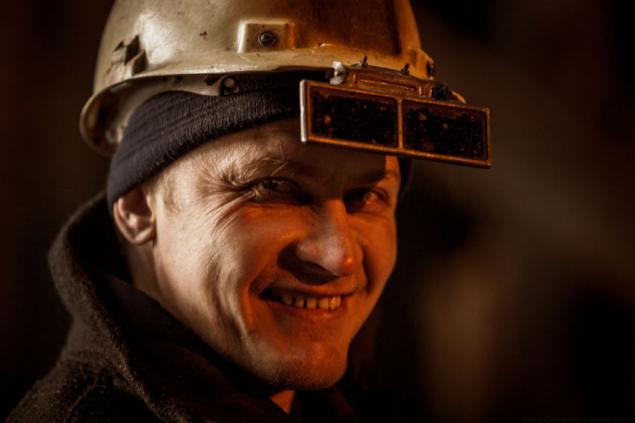
Para verter hierro fundido líquido cuchara de metal por medio de una grúa para levantar el convertidor de cuello inclinado. Entonces los mecanismos de la grúa inclinada cucharas de hierro - y la masa fundida se vierte
.
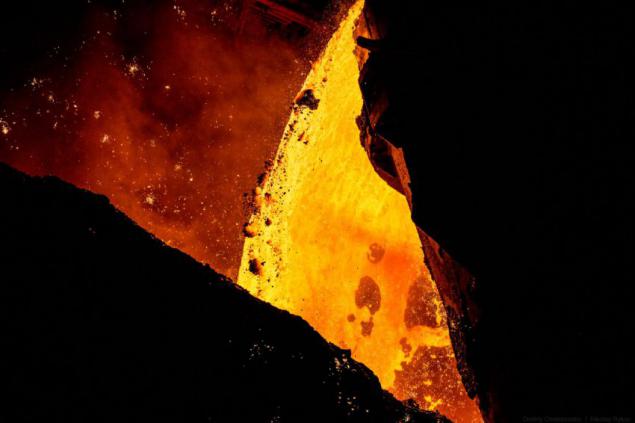
Una vez que se cargan los materiales básicos, que empieza a soplar el oxígeno.
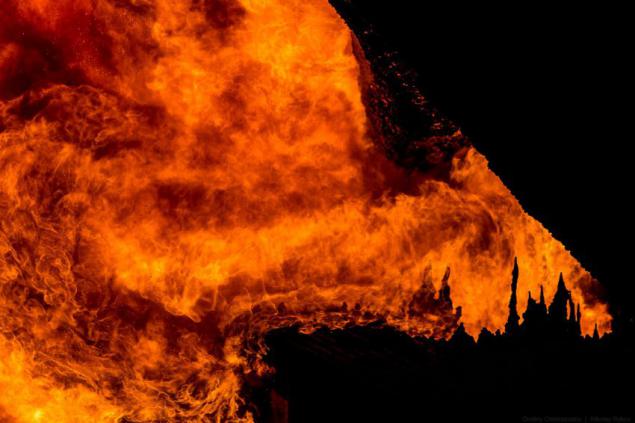
Escurrir escoria.
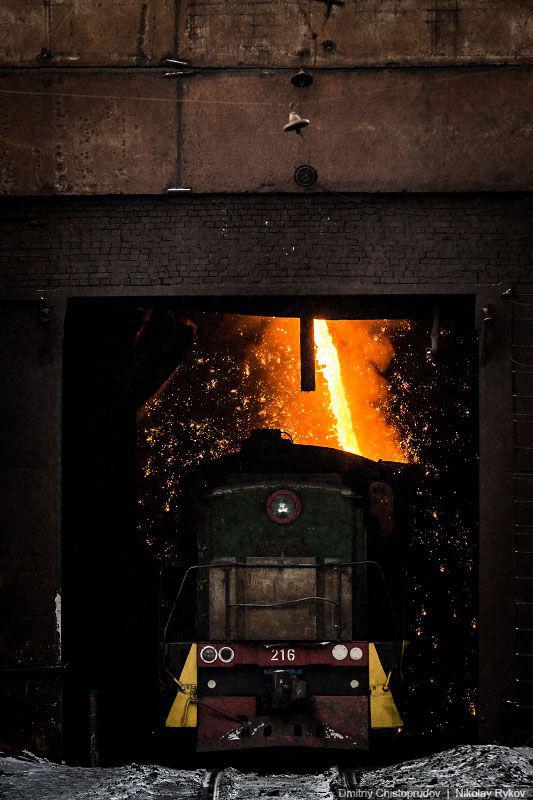
En algunos períodos de soplado de una capa de espuma de escoria 30-50 veces mayor que el espesor de la escoria en un estado de calma, y su nivel alcanza los 6 metros de la superficie de un baño tranquilo. Al mismo tiempo, el metal fundido de espuma se aproxima a la boca del convertidor y algunos picos lanzados a través de él. A veces ella emulsión se vierte a través del cuello, lo que sucede en los casos de aumento espontáneo en el volumen de gas. Naturalmente, este tipo de emisiones y explosiones representan un grave peligro para las personas, por lo que se quedan cerca del convertidor durante el soplado está prohibido.
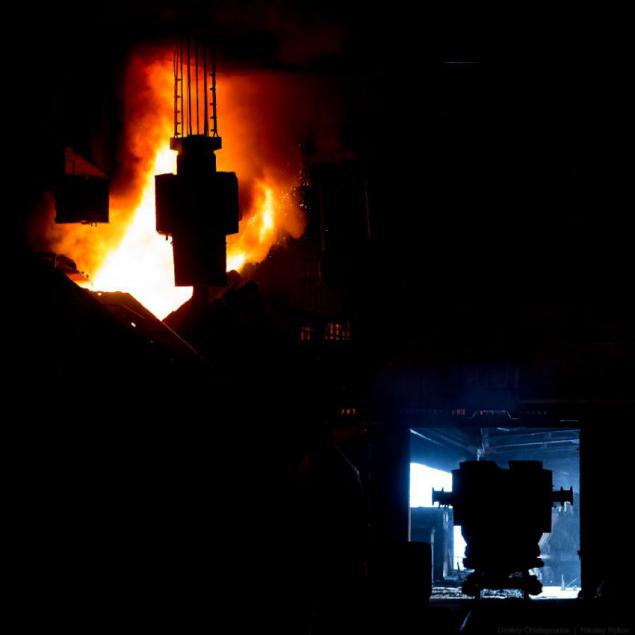
Muro de protección de lagunas a través del cual se pueden ejecutar el sensor de temperatura de la caldera. A través de los agujeros son tan caliente, que la siderúrgica ropa comienza a fumar en cuestión de segundos.
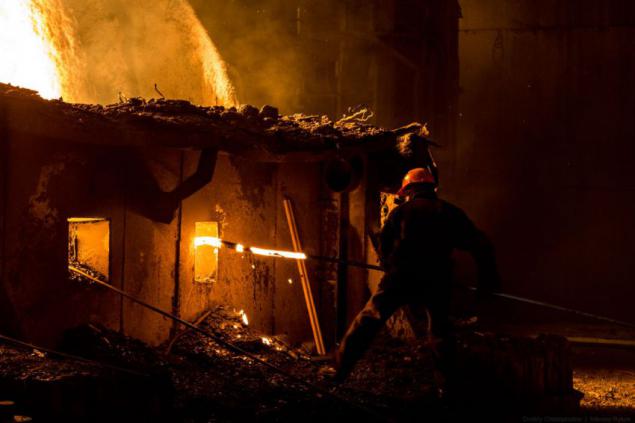
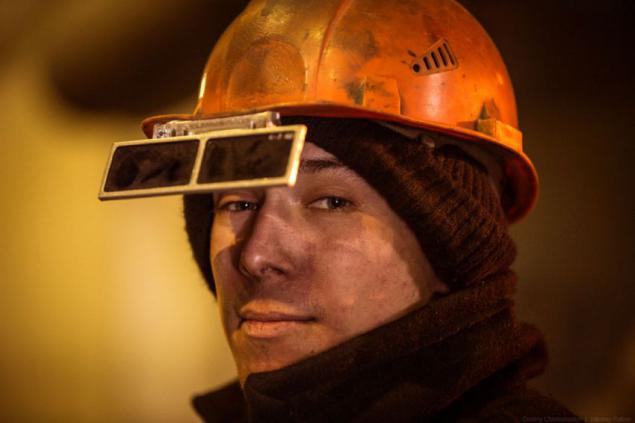
Hervir el acero.
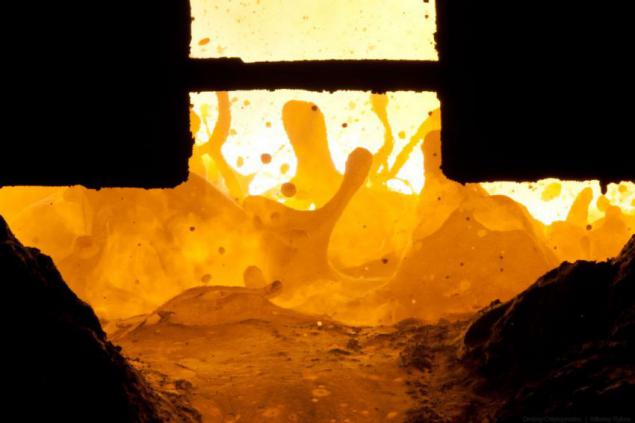
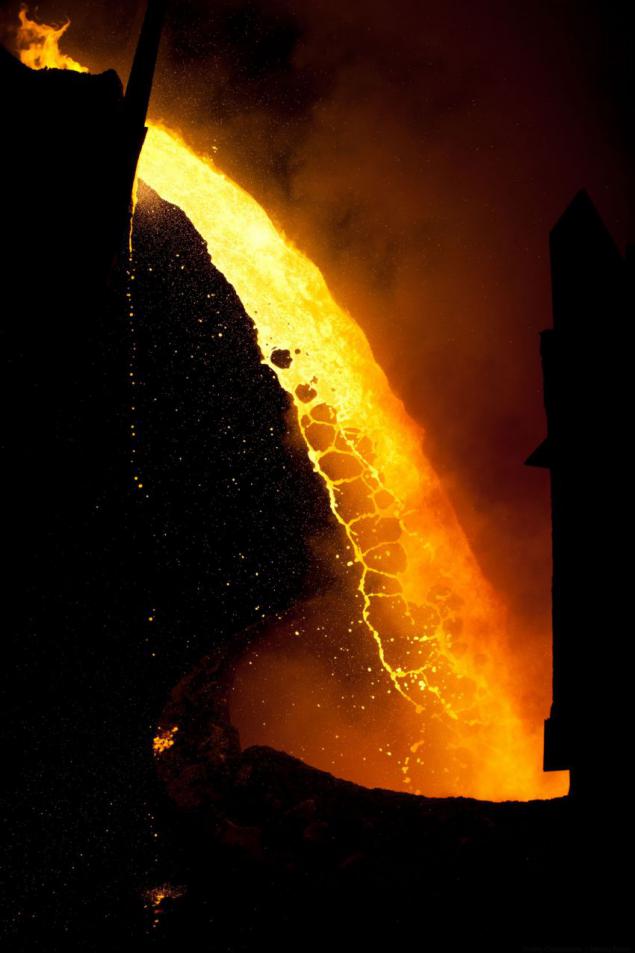
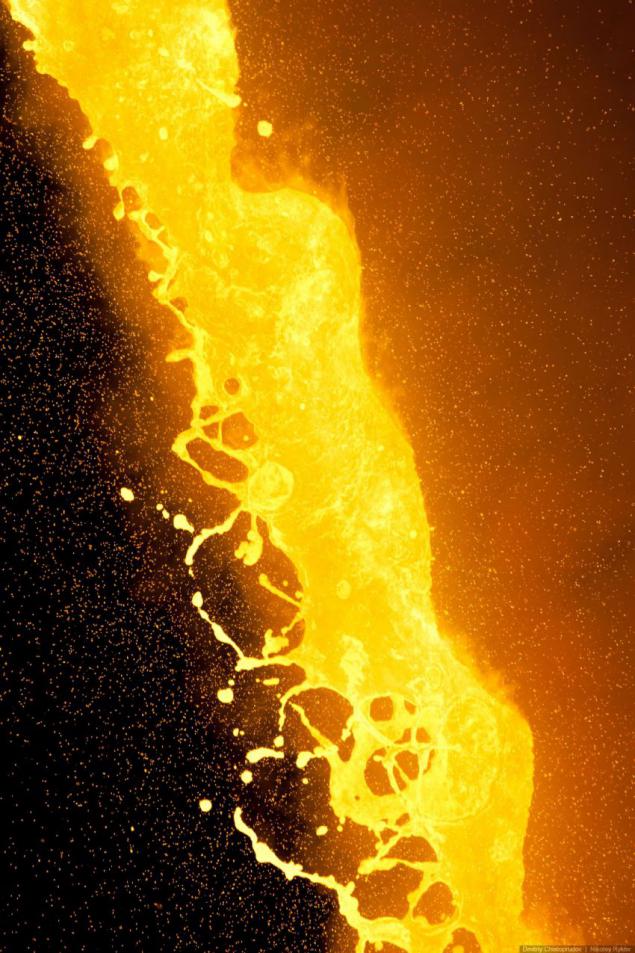
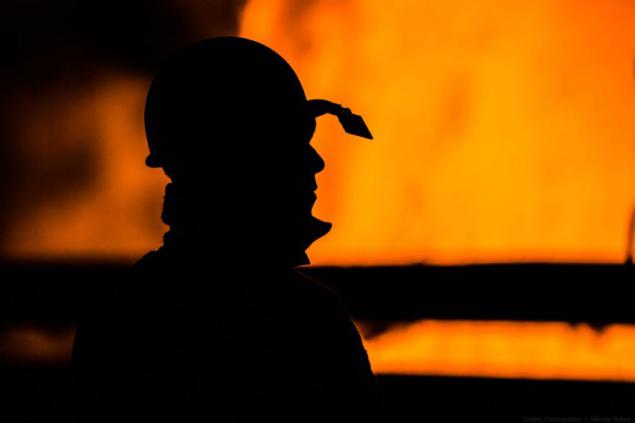
Chelyabinsk Planta Metalúrgica tiene el quinto lugar entre la industria siderúrgica de Rusia en términos de producción de acero y es el mayor productor de acero inoxidable en el país.
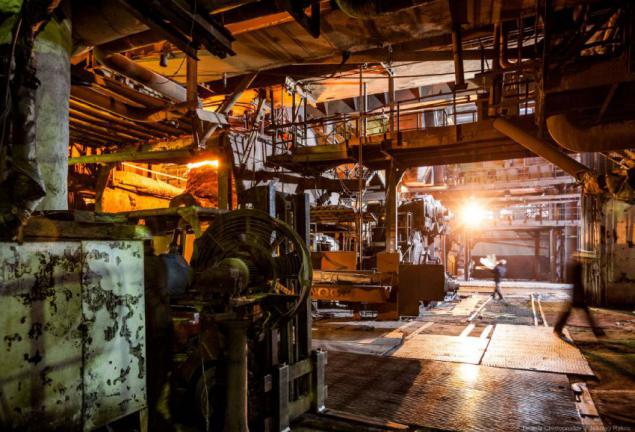
La planta tiene una superficie de más de 22 kilómetros cuadrados y es un gran generador de empleo, proporcionando puestos de trabajo para más de 17 mil personas.
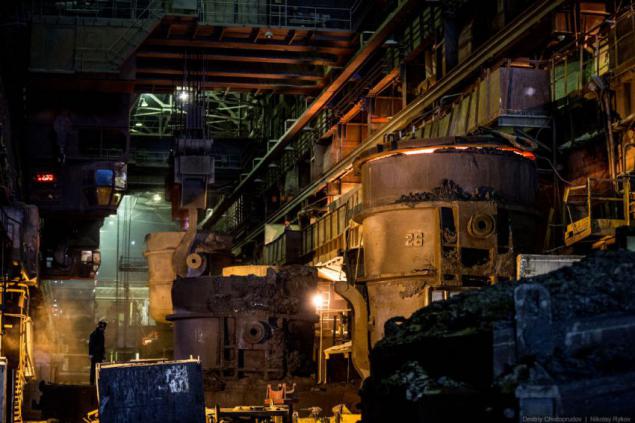
Durante siete décadas, la planta ha producido 175 millones de toneladas de coque, 120 millones de toneladas de sinter, 200 millones de toneladas de hierro, 270 millones de toneladas de acero y se envían 225 millones de toneladas de productos de acero.
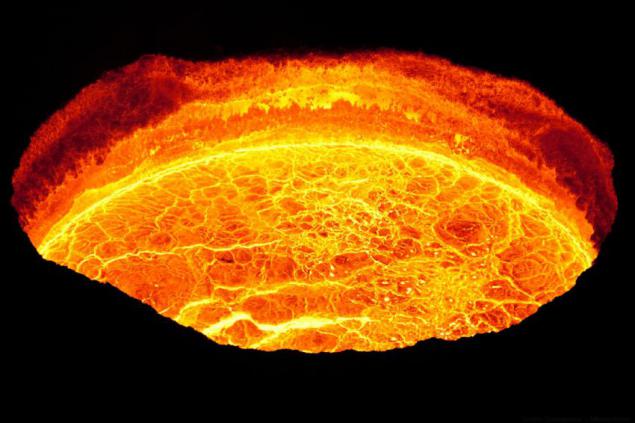
Fundición de acero - la etapa final del proceso de fabricación de acero, durante el cual el acero de un estado líquido a sólido y adquiere cierta forma, tamaño y peso. Hasta hace poco, el único método utilizado en las fábricas vertía en moldes. En este caso, fundido en el acero convertidor se vierte en moldes especiales de diferentes tamaños y se dejó para el enfriamiento gradual. Entonces lingotes listos recuperados del molde, cortar el exceso y enviados para su posterior procesamiento. Sin embargo, este método es muy intensivo en mano de obra, requiere una gran cantidad de moldes y su sustitución periódica y consume una cantidad significativa de materiales refractarios.
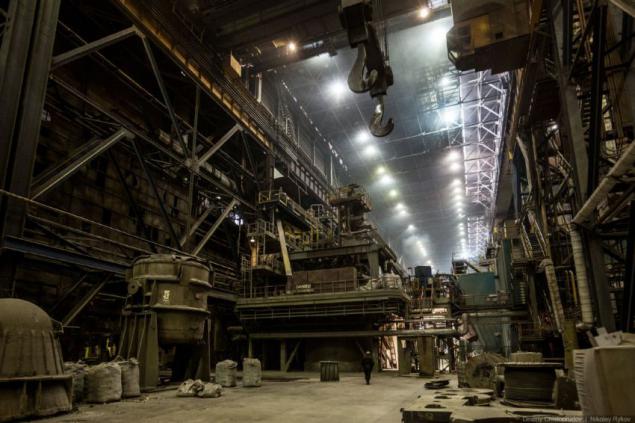
Un método de moldeo más económico, permite obtener un tocho de acero de sección transversal cuadrada o rectangular directamente de metal fundido, un método de colada continua de acero. Máquinas Going es que hasta el final de la fundición de un cubo sirvió el siguiente avance. Cambio de la cubeta se hace sin detener el proceso de fundición debido al uso del metal en el depósito intermedio. Los productores de acero como un método denominado "fusión en la fusión."
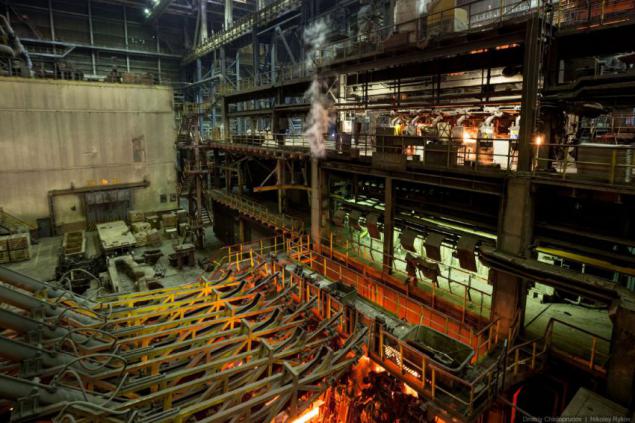
El metal líquido se divide en seis corrientes. Detrás de cada "arroyo" parece obrero metalúrgico.
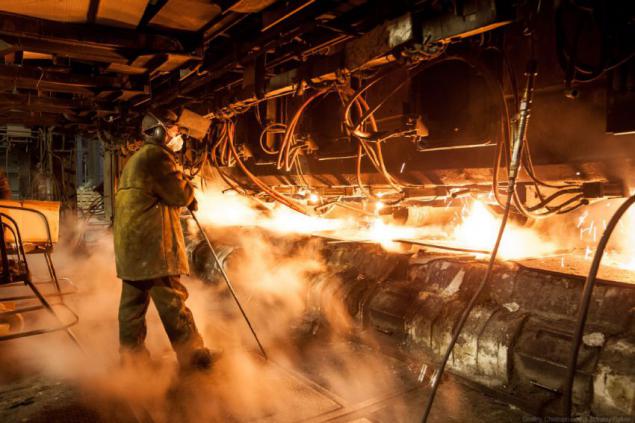
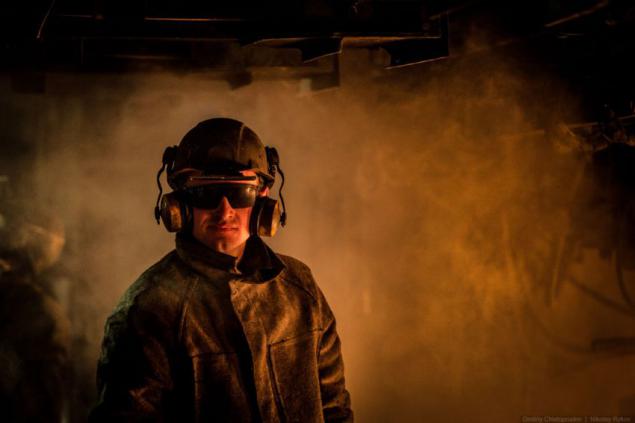
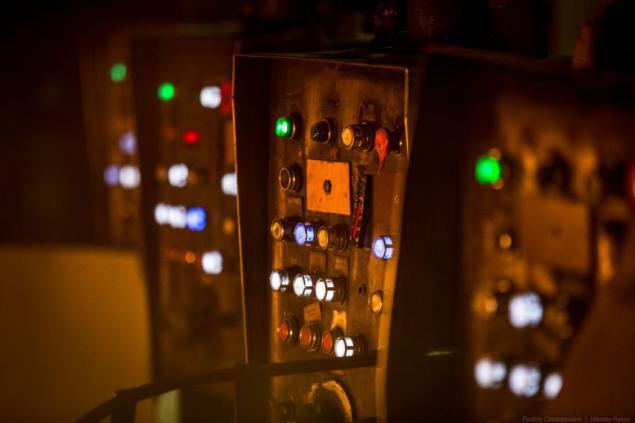
Es necesario un seguimiento constante de no sacrificar a los moldes del cuello en el que el acero se enfría y se endurece.
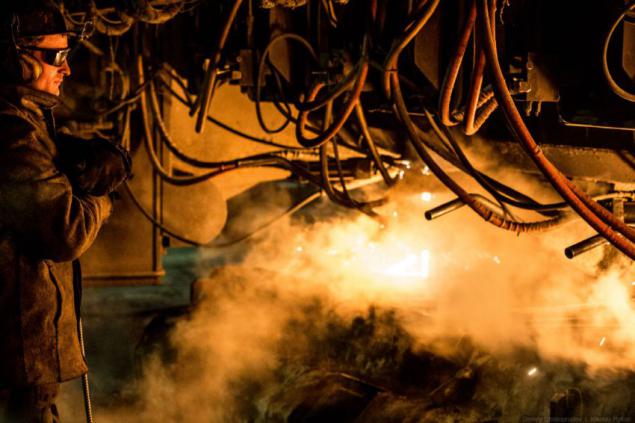
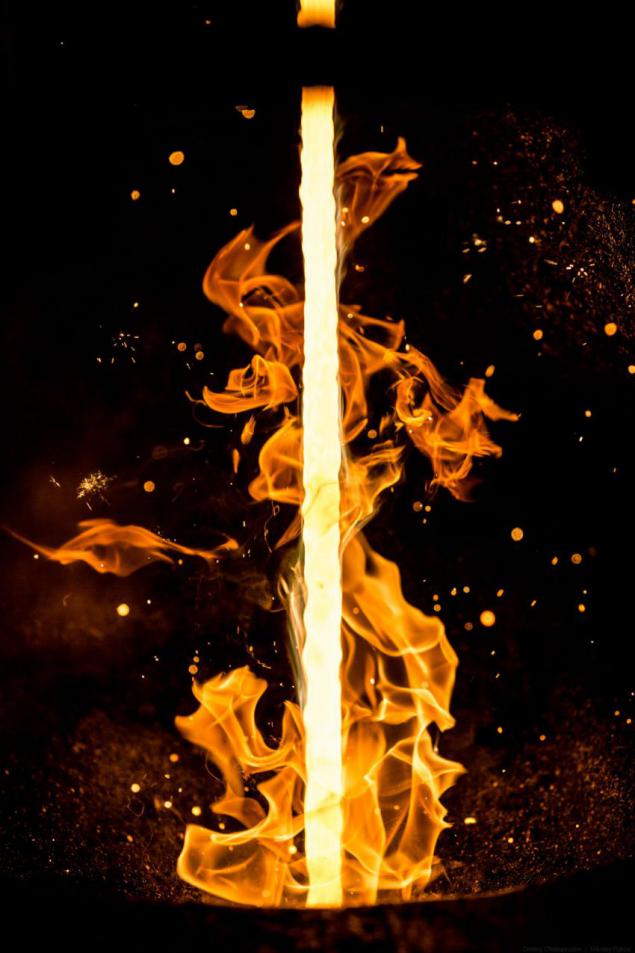
Barras de metal Infinite fluyen suavemente del molde y se cortan quemador de gas de oxígeno a la longitud.
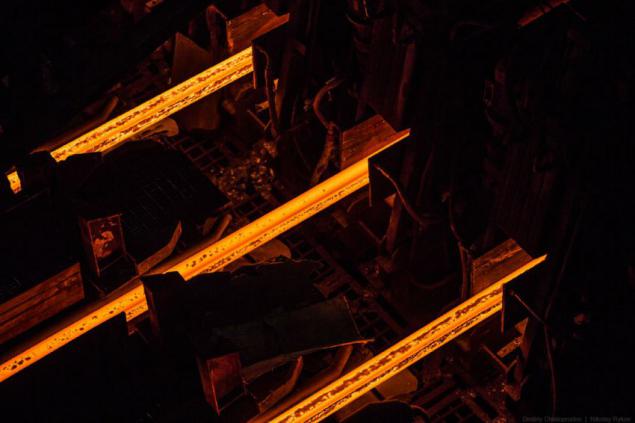
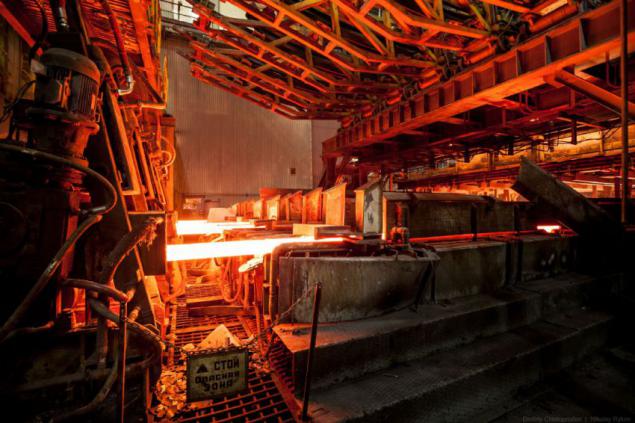
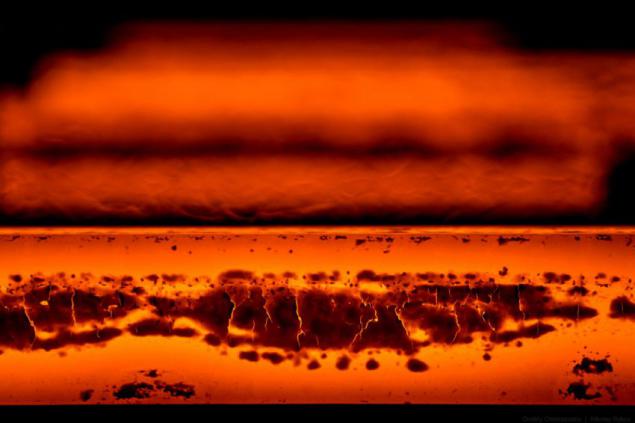
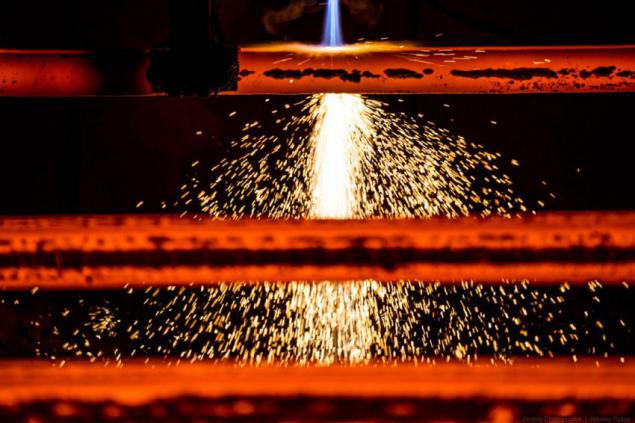
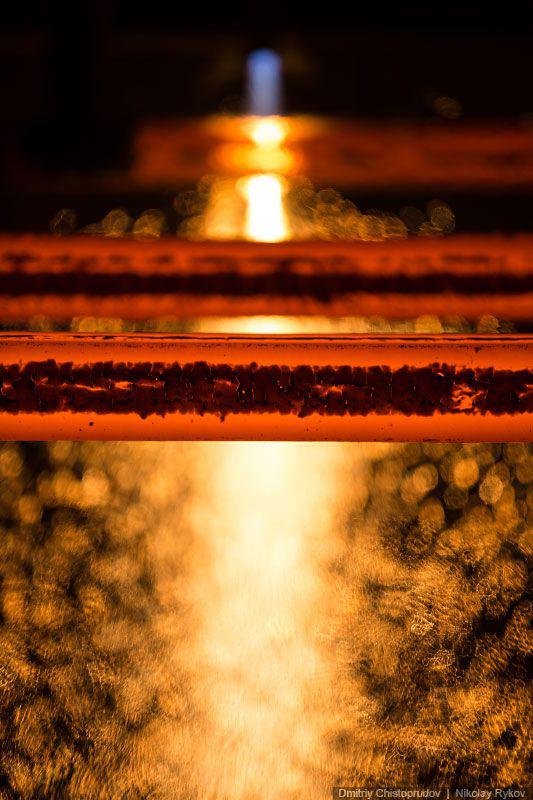
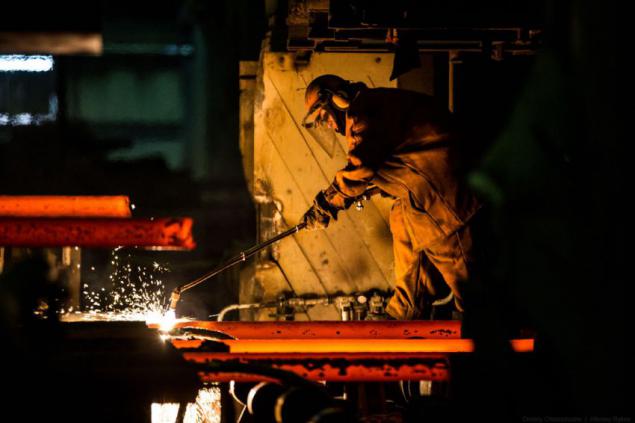
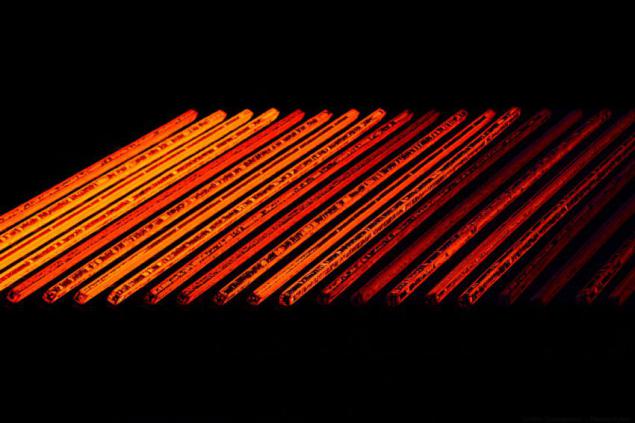
Losas de acero acabado, que requieren un enfriamiento gradual se envían en un taller independiente, donde con la ayuda de una grúa en un cierto orden se apilan en el suelo cubierto de arena.
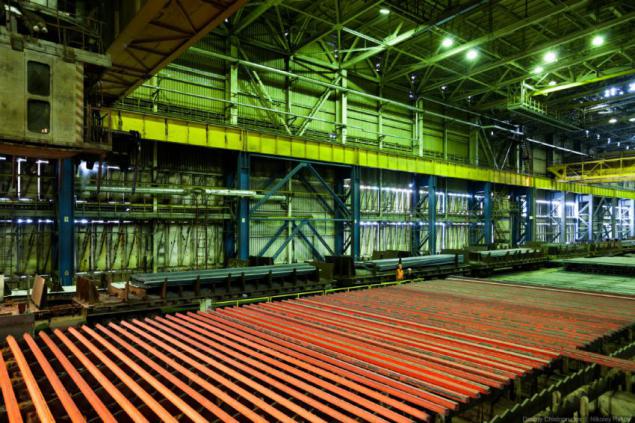
. Este es otro complejo de plantas - planta de laminación universal, que produjo los carriles de hasta 100 metros con la última tecnología de laminado, templado, enderezar, acabado y control de calidad. Tales carriles se utilizan en la construcción de ferrocarriles de alta velocidad.

De acuerdo con la ley de la mezquindad en el día de nuestra llegada, el campamento estaba en el transbordo. Hemos estado en varias ocasiones en otro tren de laminación, pero este tipo de producción a gran escala aún no se ve.
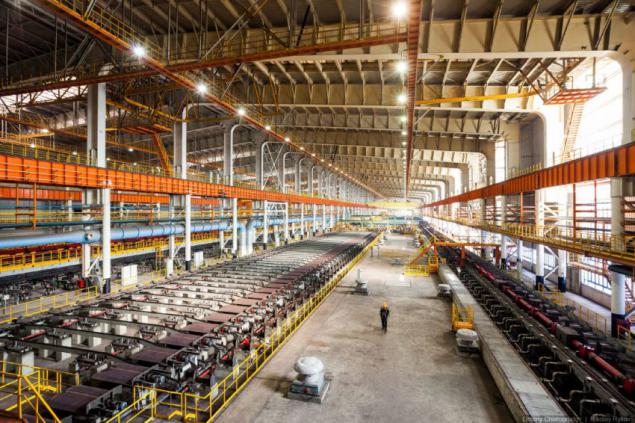
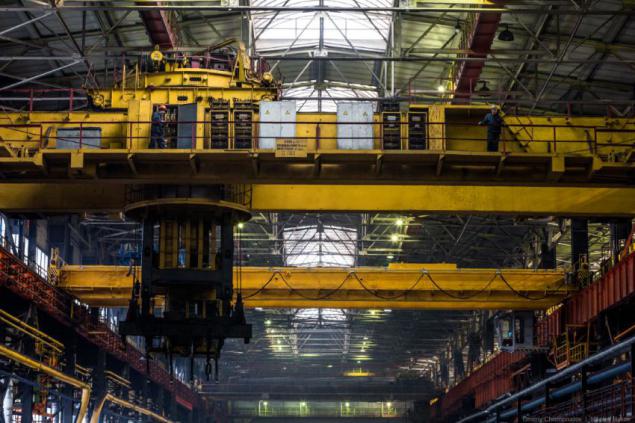
Para la construcción de la nueva planta de producción de 15.500 toneladas de acero - esto es dos de la Torre Eiffel. Ferroviario Área y la fabricación de más de 180, 000 metros cuadrados. Esta zona es fácil de instalar 26 campos en el estadio olímpico Luzhniki.
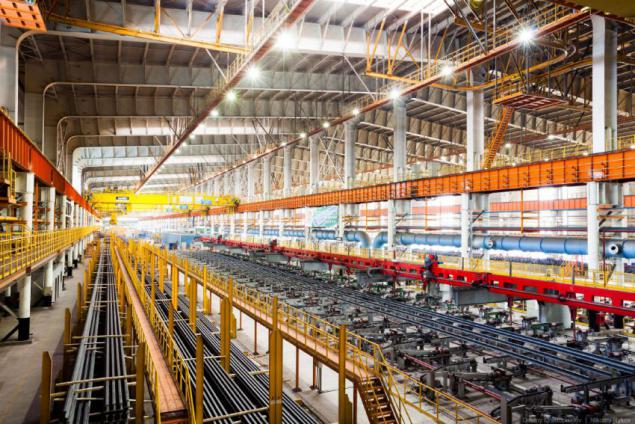
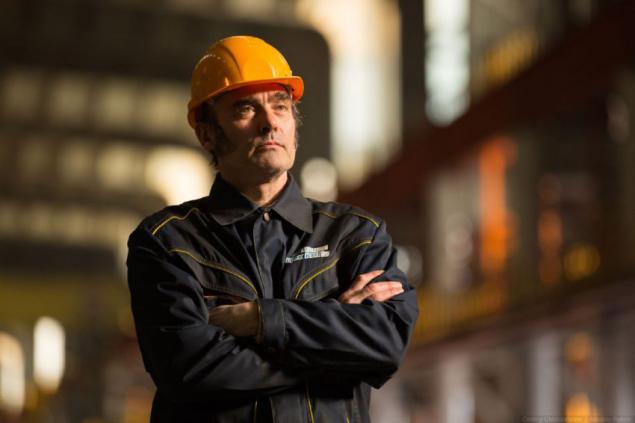
En el dispositivo de la fundación se llevó 144.500 metros cúbicos de hormigón. Por volumen 35 es una gran piscina.
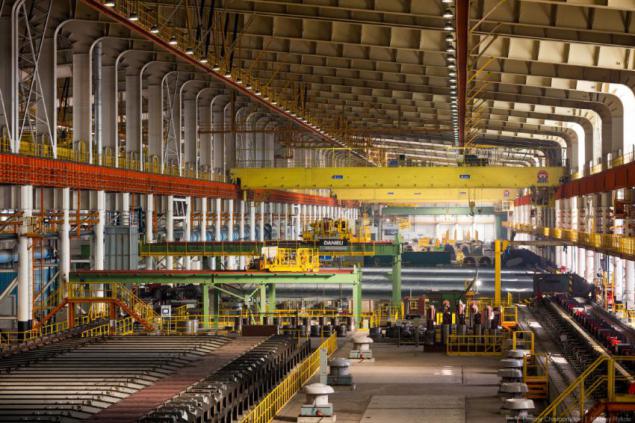
La longitud de la pieza de ferrocarril está a sólo 8, 1 m, peso - cerca de una tonelada. El carril o viga es producido por un tocho de acero peal, que se precalienta en el horno de calentamiento. El tiempo de producción de un carril de 100 metros es poco más de 2 minutos.
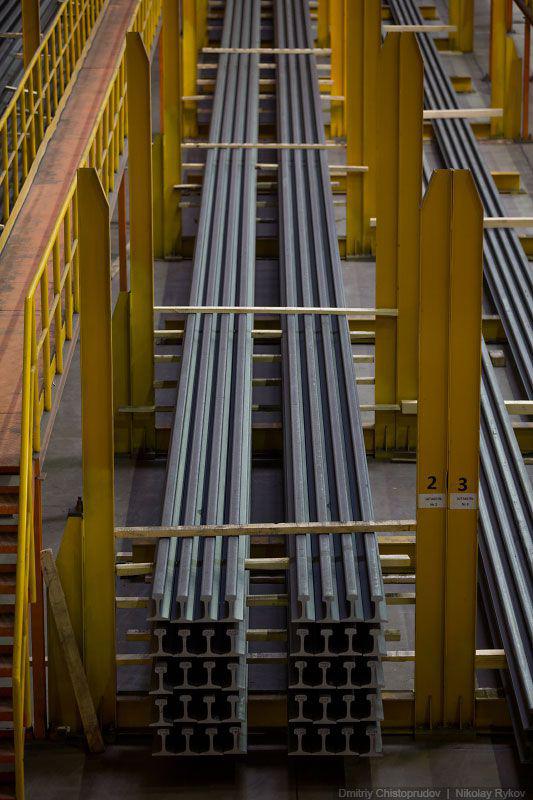
Nos las arreglamos para ver sólo una pequeña parte de la planta. Para apreciar la escala de la empresa, es necesario llegar a un par de semanas con tiendas de campaña ...
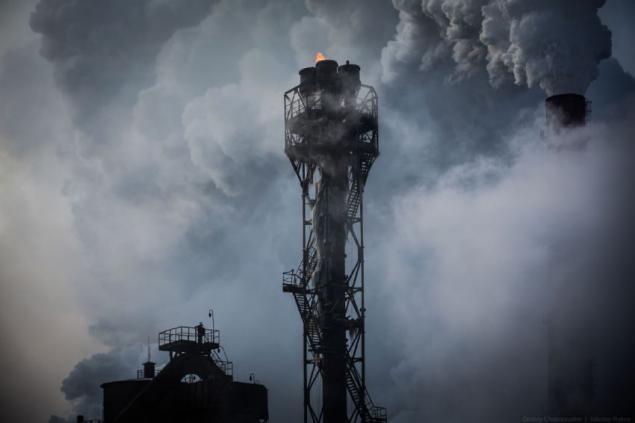
Fuente: chistoprudov.livejournal.com
Lingotes de oro de los Estados Unidos contienen tungsteno!
La primera exposición de los niños de modelado en Chelyabinsk