445
Plant Chicago's vertical farm and food waste treatment
The windy city turns into a greenhouse for sustainable urban farming.
Entrepreneur John Edel (John Edel) intends to turn the plant in the industrial district of Chicago, where in the 1920s they Packed the meat, in a completely new farming vertical farm running on food waste.
John has received a total of $ 1.5 million. U.S. Department of Commerce and economic opportunity Illinois (Department of Commerce and Economic Opportunity (DCEO)).
The Department has allocated two grants to support an integrated system of renewable energy, which will process up to 12,000 tonnes of food waste per year. Most of this material is brewer's grain (residue from beer wort) that comes from the brewery at the plant and from other Breweries around Chicago – material that is currently sent to landfill.
"These grants will help us create 125 new jobs with green collar workers in the economically distressed localities and test a new economic model that relies on secondary use of waste resources for production of food. In addition, we will reduce the amount of CO2 sent into the atmosphere, at 3,000 tons annually, using renewable energy," says Edel.
As John explains, the room is using the vertical spaces you can plant a much larger number of crops than in the horizontal plane.
Installation of anaerobic bioreactor
"The plant will produce its own electricity and heat on site using proven technologies. Our anaerobic bioreactor will use absolutely any food waste: crude brewer's grain, vegetable waste, fat, to process them and get the methane for systems of combined production of heat and electricity.
Installation of anaerobic bioreactor
This system will provide the building with heat and electric power. The plant will remain connected to the public power network and gas pipeline not only as a backup source, but also to sell surplus electricity back to the grid for General use".
System combined heat and power is a motor, is simultaneously connected to the turbine and the heat recovery system. The turbine produces electricity and the recovery system captures the heat produced by the engine.
Installation of anaerobic bioreactor
The heat in the system is in the form of steam at a temperature of about 430 ° C and will be delivered to the brewery that the plant, to ensure the fermentation process.
From the brewery the steam will be supplied at a temperature of 95 ° C and will be passed on to the absorption chiller, which will heat or cool the water used as needed for heating or cooling of the building.
Installing an anaerobic bioreactor system and the combined production of heat and electricity, the plant will produce about 380 kilowatts of electricity and 2.1 million British thermal units (BTU) – enough to provide the full scope of needs of object 93500 square feet (8 686 m2).
The bioreactor will allow the plant to become independent from Central power and to produce heat and electricity for their tenants at a price of one quarter to one third of the current cost. In addition to the brewery in its territory, John has plans to open a bakery and aquaponics system.
The total project cost approximately $ 3 million, half of which provide grants received, and the remaining part covers the loan company John and help other organizations.
Beginning in 2011, the construction and renovation of the building is gradually coming to the final straight. However, the plant is running and partially operational, using one floor and natural light for a small farm, being successful and independent agricultural facility in Chicago. And recently, the company received the official status of non-profit organizations and as a consequence of significant tax incentives.
Source: facepla.net
Entrepreneur John Edel (John Edel) intends to turn the plant in the industrial district of Chicago, where in the 1920s they Packed the meat, in a completely new farming vertical farm running on food waste.
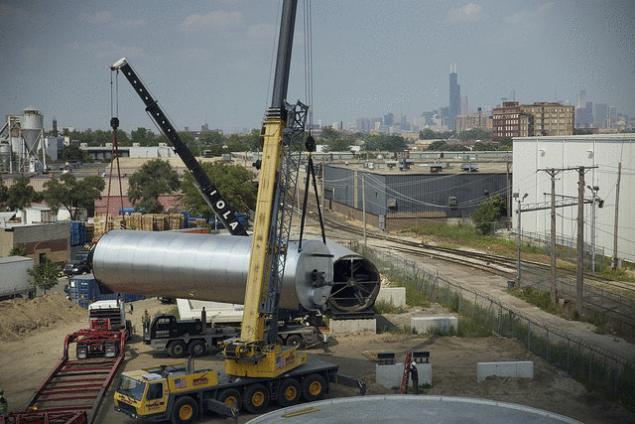
John has received a total of $ 1.5 million. U.S. Department of Commerce and economic opportunity Illinois (Department of Commerce and Economic Opportunity (DCEO)).
The Department has allocated two grants to support an integrated system of renewable energy, which will process up to 12,000 tonnes of food waste per year. Most of this material is brewer's grain (residue from beer wort) that comes from the brewery at the plant and from other Breweries around Chicago – material that is currently sent to landfill.
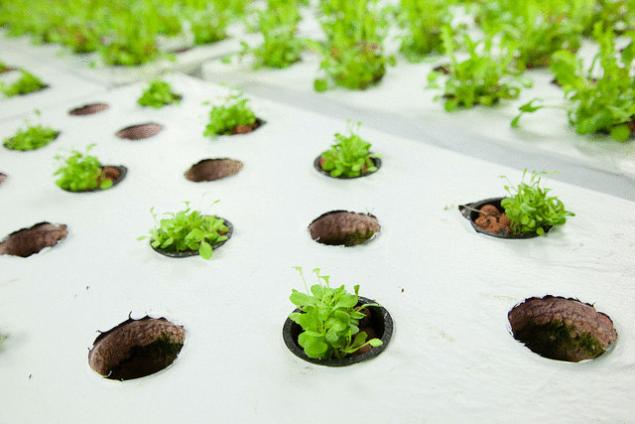
"These grants will help us create 125 new jobs with green collar workers in the economically distressed localities and test a new economic model that relies on secondary use of waste resources for production of food. In addition, we will reduce the amount of CO2 sent into the atmosphere, at 3,000 tons annually, using renewable energy," says Edel.
As John explains, the room is using the vertical spaces you can plant a much larger number of crops than in the horizontal plane.
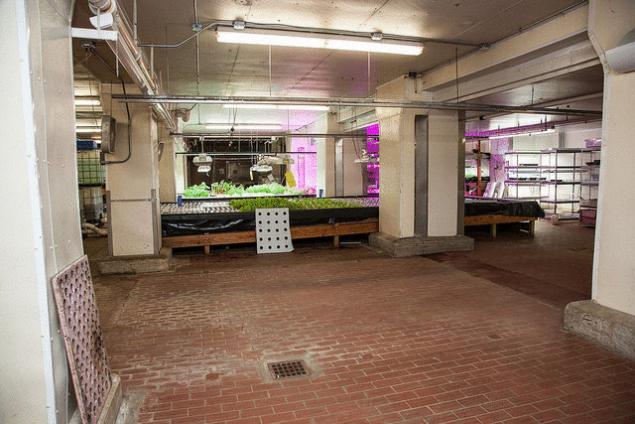
Installation of anaerobic bioreactor
"The plant will produce its own electricity and heat on site using proven technologies. Our anaerobic bioreactor will use absolutely any food waste: crude brewer's grain, vegetable waste, fat, to process them and get the methane for systems of combined production of heat and electricity.
Installation of anaerobic bioreactor
This system will provide the building with heat and electric power. The plant will remain connected to the public power network and gas pipeline not only as a backup source, but also to sell surplus electricity back to the grid for General use".
System combined heat and power is a motor, is simultaneously connected to the turbine and the heat recovery system. The turbine produces electricity and the recovery system captures the heat produced by the engine.
Installation of anaerobic bioreactor
The heat in the system is in the form of steam at a temperature of about 430 ° C and will be delivered to the brewery that the plant, to ensure the fermentation process.
From the brewery the steam will be supplied at a temperature of 95 ° C and will be passed on to the absorption chiller, which will heat or cool the water used as needed for heating or cooling of the building.
Installing an anaerobic bioreactor system and the combined production of heat and electricity, the plant will produce about 380 kilowatts of electricity and 2.1 million British thermal units (BTU) – enough to provide the full scope of needs of object 93500 square feet (8 686 m2).
The bioreactor will allow the plant to become independent from Central power and to produce heat and electricity for their tenants at a price of one quarter to one third of the current cost. In addition to the brewery in its territory, John has plans to open a bakery and aquaponics system.
The total project cost approximately $ 3 million, half of which provide grants received, and the remaining part covers the loan company John and help other organizations.
Beginning in 2011, the construction and renovation of the building is gradually coming to the final straight. However, the plant is running and partially operational, using one floor and natural light for a small farm, being successful and independent agricultural facility in Chicago. And recently, the company received the official status of non-profit organizations and as a consequence of significant tax incentives.
Source: facepla.net