820
How to make DVD-drives ...
Photographer Andrew Manuilov was sure that the information on any drive is always recorded. As it turns out, no. Once on a single plant in Kazakhstan for production of optical media LaserMaster, he learned that the information on the disc is literally imprinted. But see for yourself.
31 photo, via
2. Production of CD - process is fully automated, but watching him chief engineer.
3. Optical discs are made of polycarbonate, which is supplied to the factory in huge sacks
4. Here it is - the future drives!
5. From the first bags of pellets go into the dryer ...
6. then sent through the pipes to the injection molding machine, where it is heated to a liquid state ...
7. ... and injected under pressure into a mold in which is located stamper
8. Stamper - a metal plate with the exact image information. Here in this thing, and is a film that later transferred to the disk. We stamper has another name - matrix. By the way, no one would have allowed you so simply take the matrix in the hands - I think that it immediately end
9. At a temperature of 250 degrees is heated to liquid state polycarbonate, takes the form of a disc. And the information applied to the matrix is imprinted on it
10. The first 30 pieces each draw automatically reject to ensure the stability of subsequent casting
11. The blanks with the information received in the cooling unit where their temperature falls to room
12.
13.
14. Then they are covered with a reflective surface (metallization) so that later laser beam in your player can read the information on the disk. Without this coating laser simply pass through
15. Then the blank stick together transparent glue that is unwound over the surface of the centrifuge for uniform gluing. DVD-wheels consist of two layers, a CD - one
16. While this is a semi-products
17. The test is performed by laser disc surface. Of the 40 drives the car has rejected one. Minimum party of one of the film - 500 discs. Manufacturing period of 14 days, the capacity of the plant is 300,000 discs per month
18. After the printed one batch of films, it is sent to the painting. At this time, you can run another batch of films
19. During this process, the operator monitors the printer, whose mission - to achieve an exact match of the customer received the label layout
20. Ready drives come in a temporary warehouse, where all are in alphabetical order.
21. The accounting manager, prepares a complete set with the task - and printing discs for subsequent assembly
22.
23. Each disc is accompanied by a hologram
24. First, a DVD-box printing is inserted, then the disk. Girls do it with incredible speed
25. Assembled wheels fall on the machine where packed in cellophane film
26. And only then collected in boxes and sent to the distribution center
27. From there, the goods of daily expenses on shops all over Kazakhstan
28. Now the boxes are shipped to the store "Meloman Grand", located on Gogol Street Almaty
29. At all stages, made a careful control over the safety of all intellectual property from possible leaks
30. Finally, the finished product on the shelves waiting for its customers
31.
Source:
31 photo, via
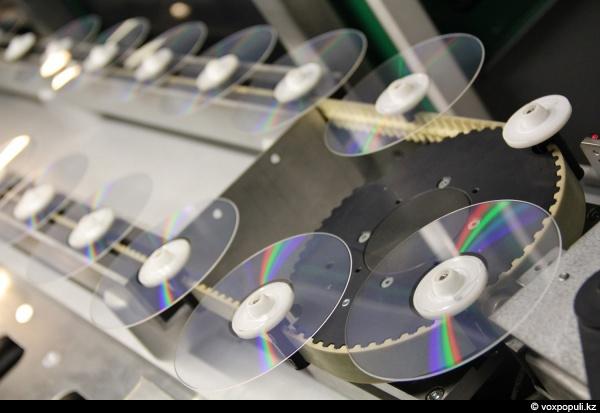
2. Production of CD - process is fully automated, but watching him chief engineer.
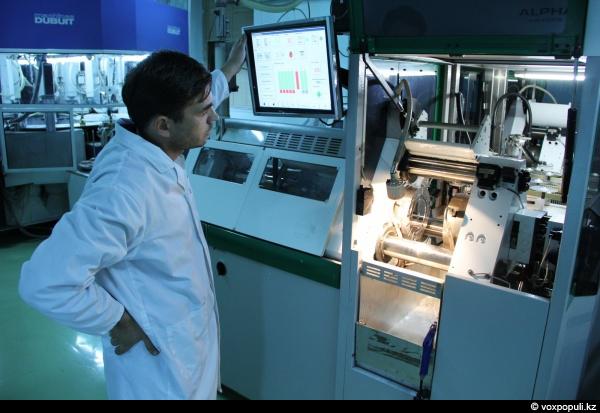
3. Optical discs are made of polycarbonate, which is supplied to the factory in huge sacks
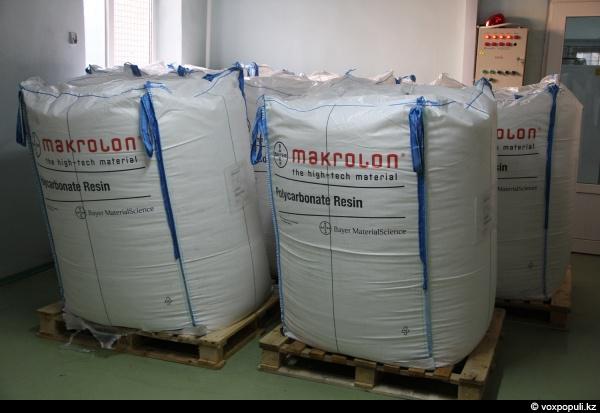
4. Here it is - the future drives!
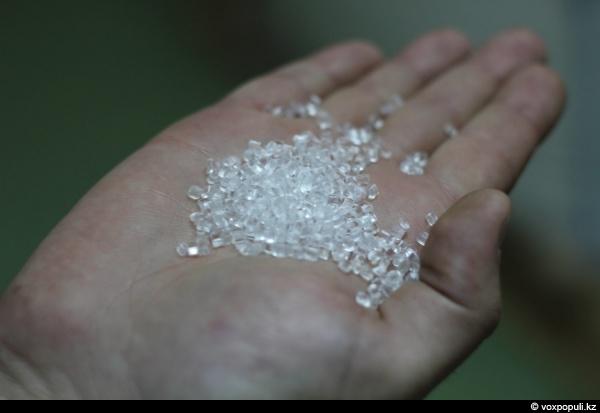
5. From the first bags of pellets go into the dryer ...
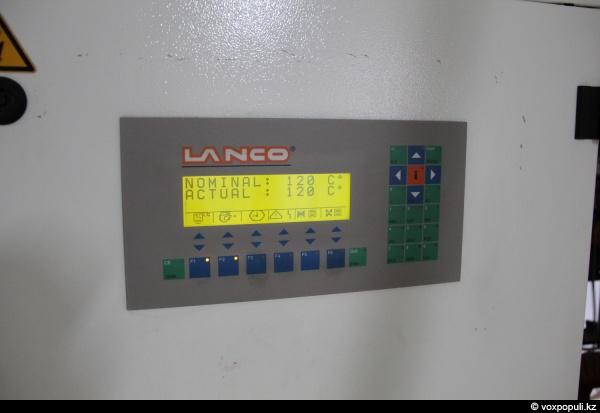
6. then sent through the pipes to the injection molding machine, where it is heated to a liquid state ...
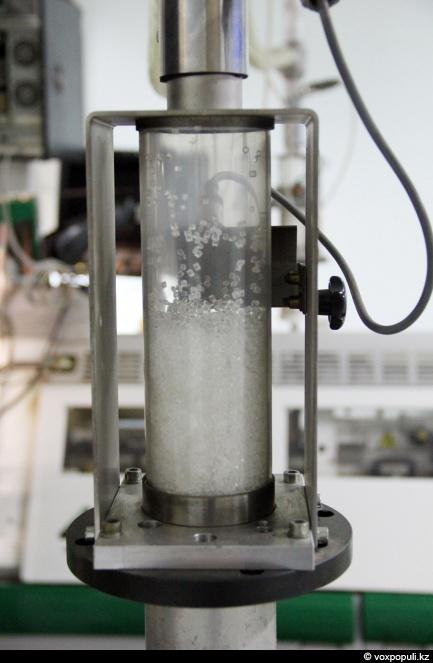
7. ... and injected under pressure into a mold in which is located stamper
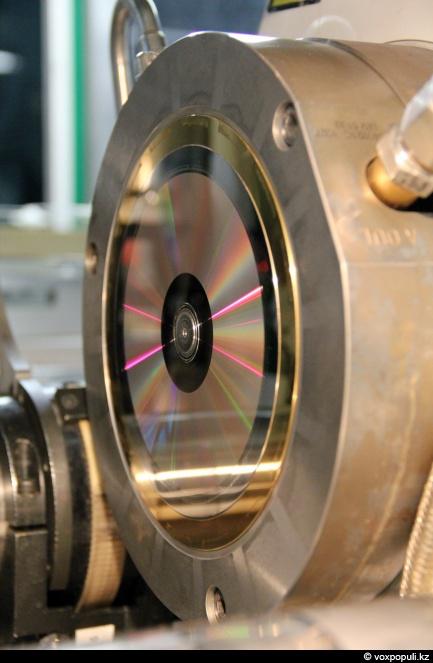
8. Stamper - a metal plate with the exact image information. Here in this thing, and is a film that later transferred to the disk. We stamper has another name - matrix. By the way, no one would have allowed you so simply take the matrix in the hands - I think that it immediately end
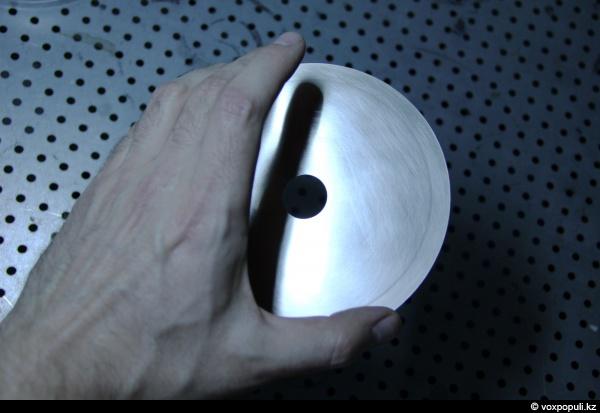
9. At a temperature of 250 degrees is heated to liquid state polycarbonate, takes the form of a disc. And the information applied to the matrix is imprinted on it
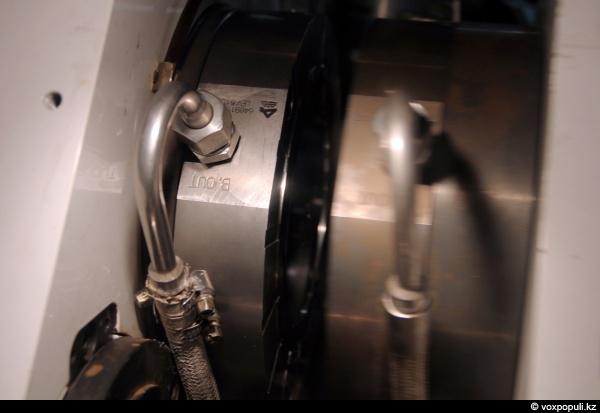
10. The first 30 pieces each draw automatically reject to ensure the stability of subsequent casting
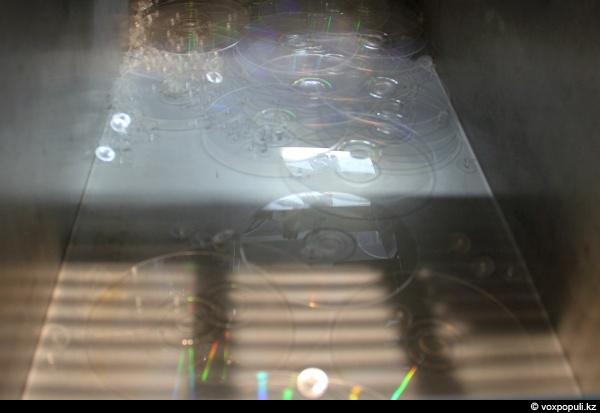
11. The blanks with the information received in the cooling unit where their temperature falls to room
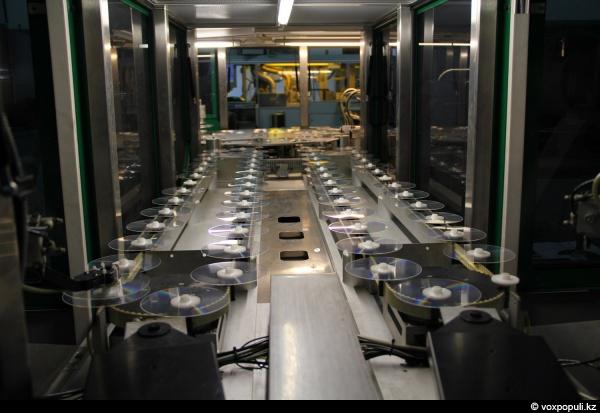
12.
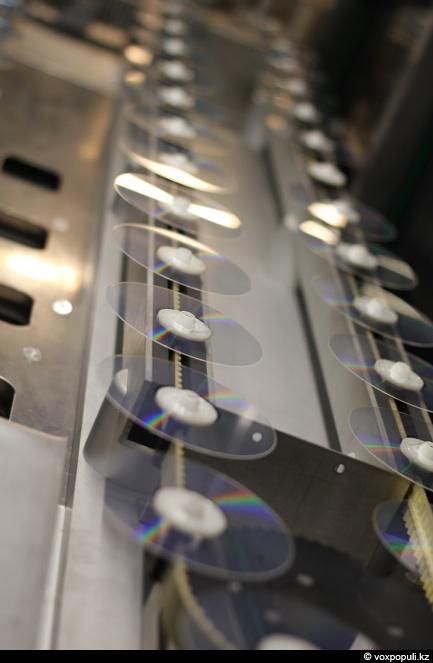
13.
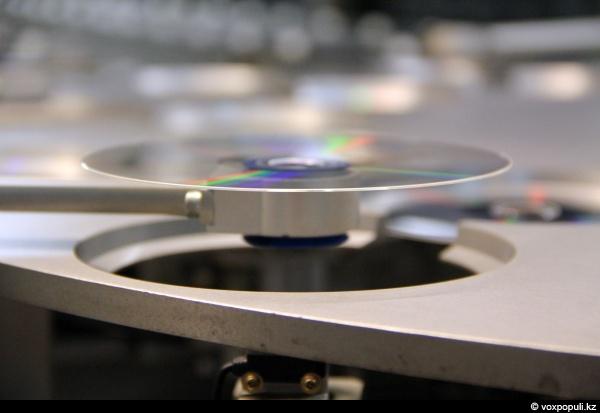
14. Then they are covered with a reflective surface (metallization) so that later laser beam in your player can read the information on the disk. Without this coating laser simply pass through
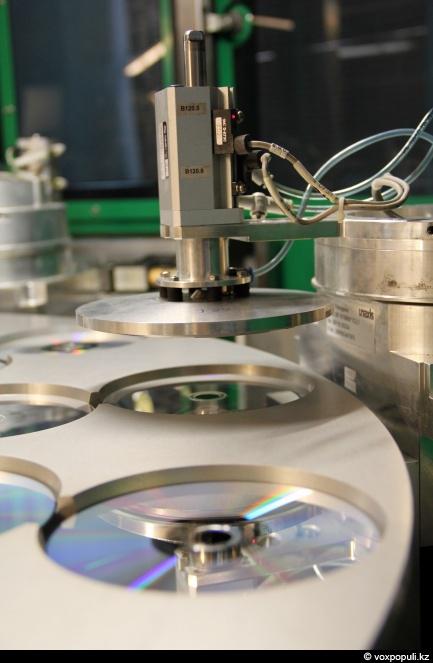
15. Then the blank stick together transparent glue that is unwound over the surface of the centrifuge for uniform gluing. DVD-wheels consist of two layers, a CD - one
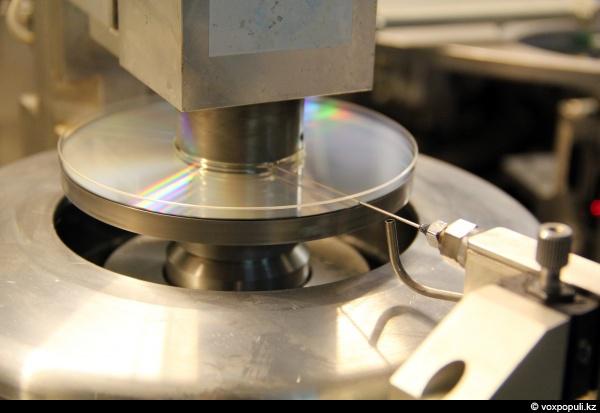
16. While this is a semi-products
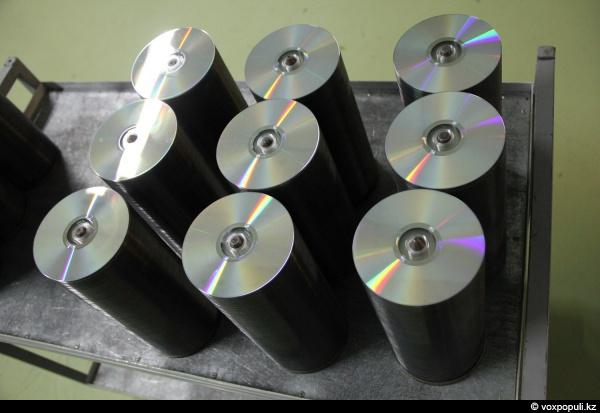
17. The test is performed by laser disc surface. Of the 40 drives the car has rejected one. Minimum party of one of the film - 500 discs. Manufacturing period of 14 days, the capacity of the plant is 300,000 discs per month
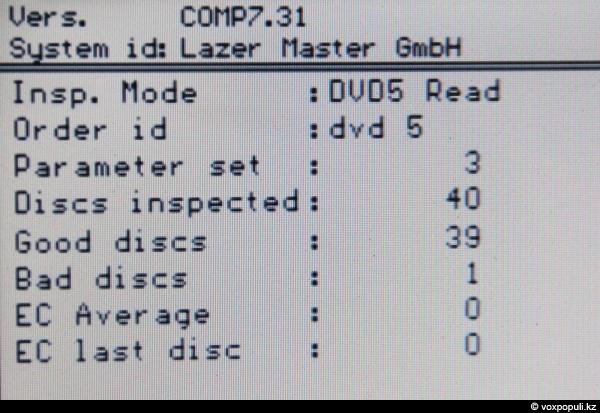
18. After the printed one batch of films, it is sent to the painting. At this time, you can run another batch of films
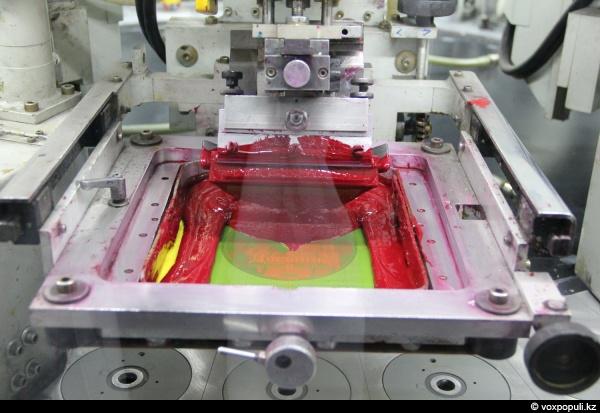
19. During this process, the operator monitors the printer, whose mission - to achieve an exact match of the customer received the label layout
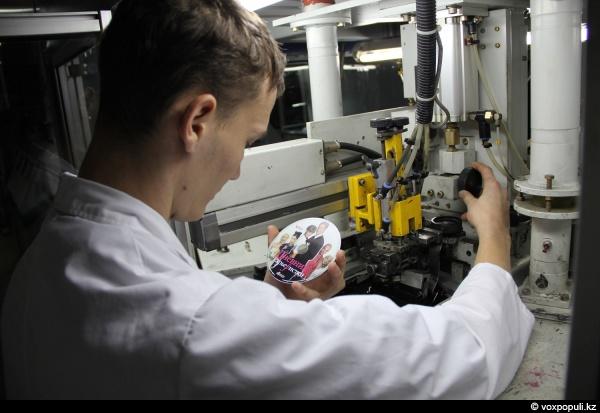
20. Ready drives come in a temporary warehouse, where all are in alphabetical order.
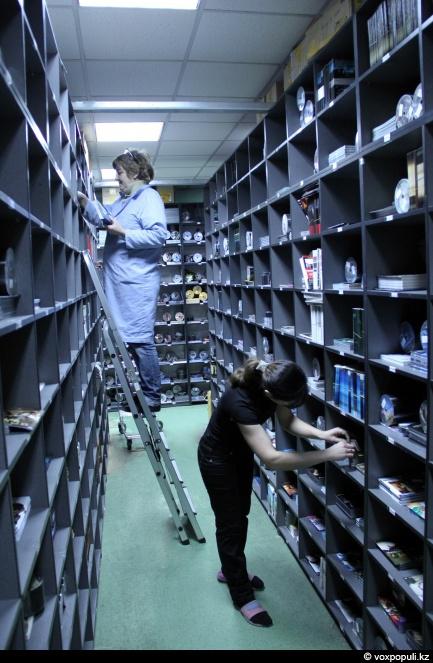
21. The accounting manager, prepares a complete set with the task - and printing discs for subsequent assembly
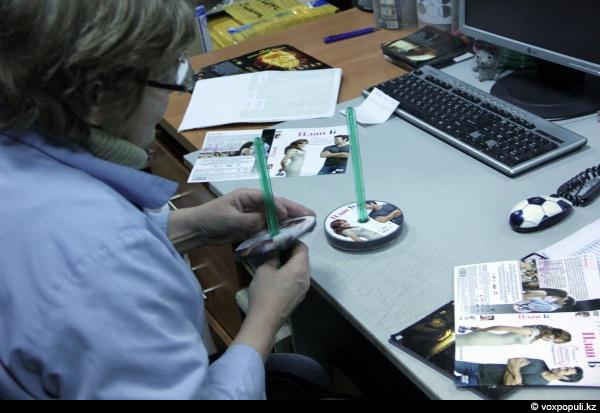
22.
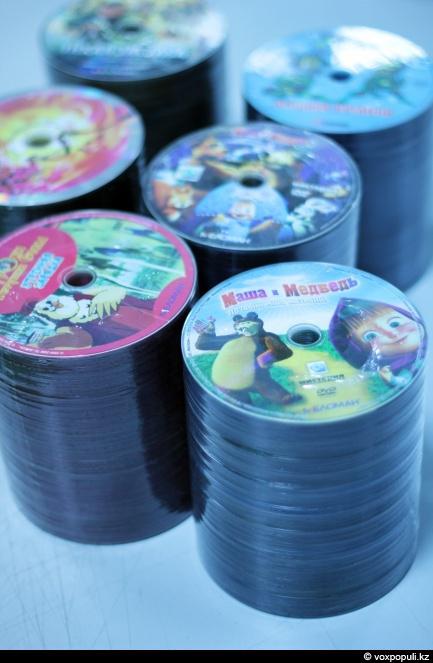
23. Each disc is accompanied by a hologram
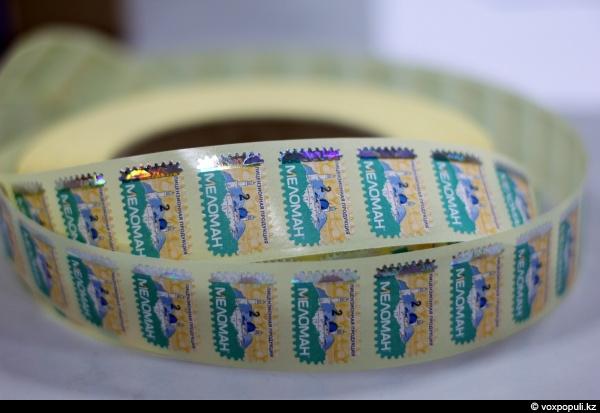
24. First, a DVD-box printing is inserted, then the disk. Girls do it with incredible speed
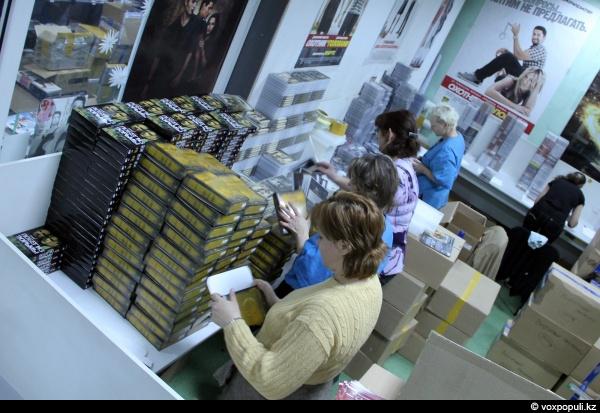
25. Assembled wheels fall on the machine where packed in cellophane film

26. And only then collected in boxes and sent to the distribution center
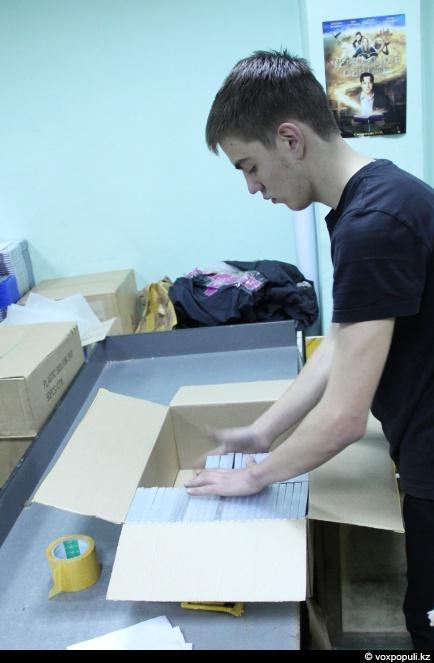
27. From there, the goods of daily expenses on shops all over Kazakhstan
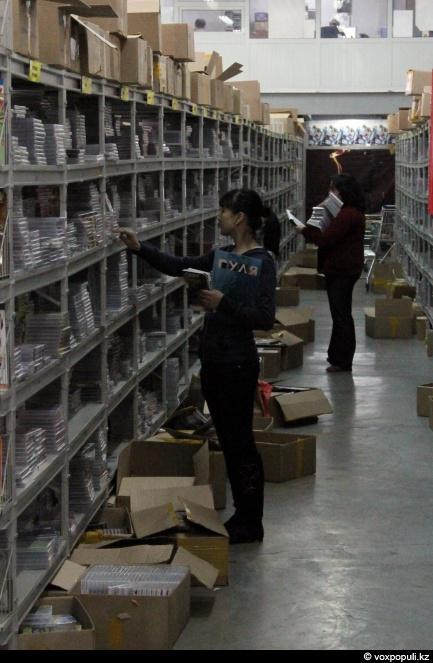
28. Now the boxes are shipped to the store "Meloman Grand", located on Gogol Street Almaty
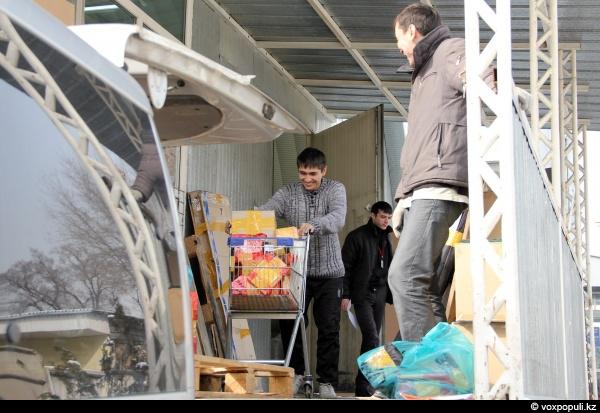
29. At all stages, made a careful control over the safety of all intellectual property from possible leaks
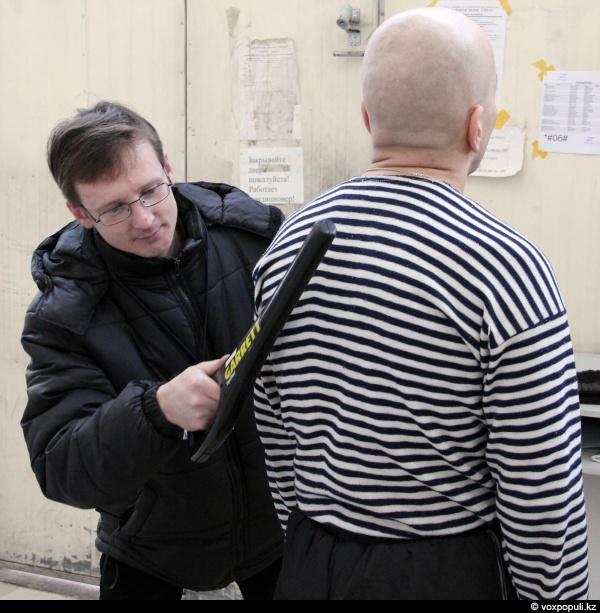
30. Finally, the finished product on the shelves waiting for its customers
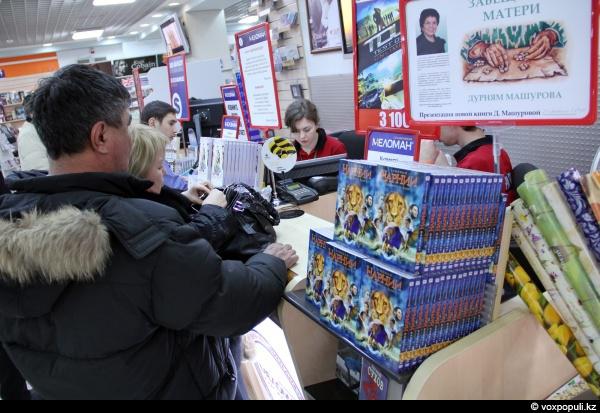
31.
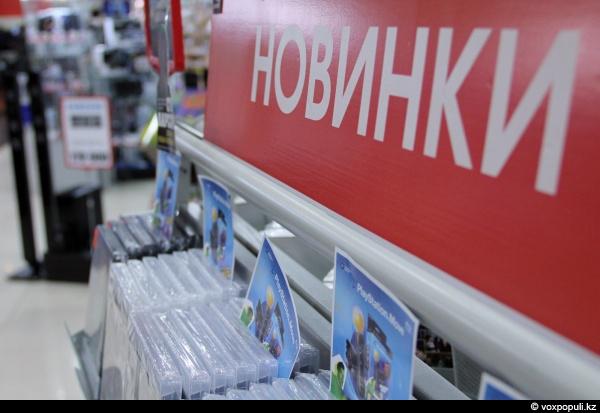
Source: