1541
Excellence mask. About magic "Merlin" Say a Word
«No engine - and the most perfect design any rocket with all her stuffed dead» i> Glushko
In recent years, a private space company Space X, headed by Elon Musk, never ceases to amaze the world with its fantastic success. The main highlight of space transportation systems of the company are considered RN series Falcon, and in particular the Merlin engine 1, already dubbed "the most efficient in the world».
It creates the false impression that Space X in a relatively short time was able to create the engine, eclipsed developments in this area of such giants as « ENERGOMASH » and « Rocketdyne ». Under the cut in a popular form, we get acquainted with the modern world of rocket engines and try to understand this is not an unambiguous characterization as their effectiveness.
In 2012, the company Space X, spent the last test firing at the moment engine modifications Merlin 1 - D. During these tests, the engine thrust-weight ratio was increased to 150 units, which allowed him to name Space X «самым effective in history ».
In the field of engine, thrust-weight ratio is called the ratio of engine thrust (CU) to its dry weight. In the case of missile LRE usually this ratio is engine thrust in vacuum (in TC) divided by its dry weight (in tonnes).
Merlin 1D is capable of thrust from the earth in the 67t and 82T in vacuum (Melin 1D Vacuum), with a mass of about 600kg. At pH 1.1 using the Falcon 9 9 overall thrust of these engines in 600ts. The engine does not have its own system of thrust vector control (SWT), and stage of the launch control is effected by varying thrust on opposite axes, as well as at pH 1 H (throttling to reduce thrust and / or afterburner to increase the rated thrust).
Merlin 1D engines on the Falcon 9 rocket 1.1 i>
The difference between the engine thrust in the ground and in a vacuum is typical, and is connected with the deterioration of motor performance in the dense layers of the atmosphere of the planet. Atmospheric drag aerodynamics of the engine is increased in proportion to the size of the exhaust nozzle of the engine (the combined resistance of the atmospheric pressure only increases with the square of jet exhaust). It would seem that only need to minimize the size of the nozzle and improve engine performance. However, with increasing altitude atmospheric drag is reduced, and with it the characteristics of the engine on the contrary increases with the size of the nozzle.
The key here is not the absolute size of the nozzle, and expansion ratio - the ratio of the greatest cross sectional area of the cone of the nozzle to its smallest cross-sectional area. The higher the value, the higher the efficiency of the engine in a given environment. Therefore, the nozzle size the vast majority of engines a first stage launch vehicles represent a compromise for optimal engine performance, both in the atmosphere and in vacuum.
Thrust indirectly depends on the fuel used, and in contrast to the characteristics such as thrust and specific impulse, is not applicable to all types of engines - solid rocket systems are themselves engines.
The most high thrust-weight ratio differ LRE runs on a mixture of heptyl and dinitrogen tetroxide. So RD 275M ("Energomash") carrier rocket Proton M have the highest thrust-weight ratio in the world - more than 170 (187t thrust in vacuum, the mass of the engine 1, 1t). Their "big" brother RD 270 , developed in time for the summer is not ur RN 700, had a thrust-200 units! All the more surprising that it is a closed-cycle engines (see. Below). These characteristics are achieved because of the hypergolic fuel by which greatly simplified the design (and weight) of rocket engines. At the same time these motors have a pretty high parameters of specific impulse (285s for RD 275M).
RD 275M, Russian modification of the base of the Soviet RD 253 for RN series Proton (payload mass is increased to 750kg) i>
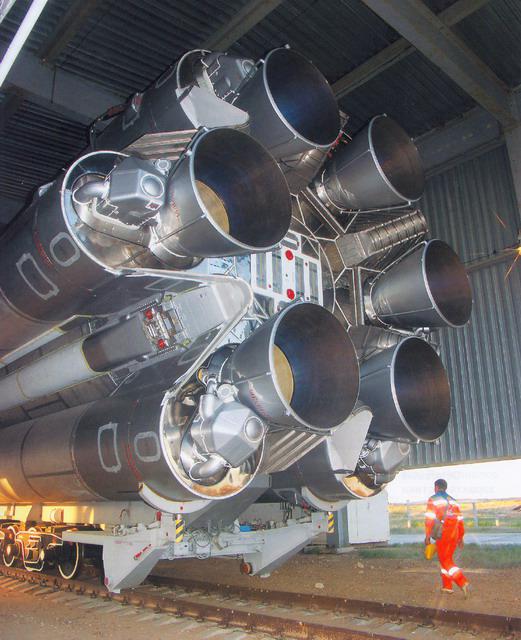
Specific impulse (sometimes referred to as specific thrust) expresses the time during which the engine develops thrust in one newton (1N = 1kgs / 0, 102), using 1 kg of fuel. The higher the UI the lower the engine requires fuel message payload certain amount of movement. In contrast, Thrust, this value and engineers often taken as an index of efficiency of the engine.