1283
Bodyguards Japanese sword
Turn on the work of this master painted in the months ahead among the kings, emirs and just museums. To then they had the opportunity to say: "This is the work of Fujiwara katana Kanefusa XXV». Hold this sword in hand - you soprikosnёtes with eternity, because manufacturing technology samurai sword there, at least in the form in which we know it, about a thousand years.
Master and keeper of the tradition of the famous Japanese arms no less famous in Japan than, say, a member of the imperial family, gave an exclusive interview.
The generic name is Fujiwara Kanefusa Kazuo Kato, a Japanese master blacksmith in the 25th generation. Born in 1957, the 32-year Showa era. He graduated from high school and enrolled as an apprentice to the legendary master Hassan Sadaiti. Since 1983, he learned the art of forging and engraving under the guidance of his father. It takes a year and Cato opened his own studio in the very spot where once stood the shop of his grandfather, was destroyed by the typhoon. On the opening day of the new studio and lighting Kato favorite tools inherited his grandfather and name: Fujiwara Kanefusa XXV. The first blade is created in the new studio newfound Fujiwara Kanefusa, he won first prize at an exhibition of contemporary swords. This was followed by Kaoruyama Award, a prize for excellence and other awards. Among the blades, made master of the swords to the Meiji Shrine and Atsuta, weapons for heroes yokozuna. Blacksmiths Association has chosen the city of Seki Fujiwara Kanefusu Chairman of the Board.
I knew almost certainly that get an audience with the man whose family from month to month, from year to year - and so 700 years in a row! - Defended at the forge, of making the legendary samurai swords - yes another case just will not!
We met as agreed at the exhibition in Gostiny Dvor. Handshake master was dense and powerful, like a blacksmith. Stocky, broad-shouldered and stout figure in a gray kimono. Butch, deep and at the same time tenacious gaze of dark eyes. Something similar to vangogovskogo Dr. Ray, a graduate school of Sumo.
I give him a selection of special editions "Authors cold steel»:
- I know your magazine - with a nod and a faint half-smile eastern, hidden in the folds of a large person responsible master.
I remember with emotion the words of gratitude in the language of the interviewee - Arigoto! And with emotion, the Japanese style, put his hands clasped to his chest.
In preparation for the interview, I looked at the photo and video files: pictures of studio Fujiwara, depicting the scene of forging. How few, but significant, each in its place, the participants of this action .. Apprentice fanned furs yellow fire in the hearth, metal apprentice tripped to the searing flames, and the master, with the tool at the ready, met crimson glow of the workpiece at the anvil. Much more than a mise en scene "forging swords in the forge of the Japanese," I was struck by the interior of a smithy and its furniture. And yet - white garments inspired blacksmiths and their expressions.
WARRIORS white robes
... I am well aware of Russian Interior forge. Gloomy twilight in which lurk the dark corners. Zakopchёnnye wall fumes in the air and chipping iron under my feet. Sweaty, soiled with soot persons artisan in the wet T-shirts that put stiff, long-lost color and texture, leather or canvas aprons.
- Master Fujiwara - I ask - how did you manage to iron must be forged to the forge, and the wall, and he horn rend reason gold, without smoke and soot flames - all shining white surgical?
A master and his disciples, dressed like angels in white kimono with wide sleeves, moving as if they Actors from the theater Kobuk? ..
- For the Japanese sword - is not just a piece of iron, it is holy. To touch the skating, it is necessary that around and everything was clean. - A voice like Fujiwara-san answers I probably recite the mantra.
- But white clothes so easy to dirty! Why are you elected is white? - I try to find out.
- Do not we have elected. It's an old tradition ... This was the clothing of ancient warriors since Muromachi, - Master says gravely. Apparel masters were cut free, with long, as at kintos, sleeves. Blacksmiths work with open fire and hot metal without gloves! No mechanization, everything by hand. Nothing should separate the blacksmith and his creation - the blade.
Japanese smiths Dynasty originated in the Middle Ages. Demand for their work - two-handed edged slightly bent swords with removable handle and hilt, braided cord, was, as ever, high. Some clans disappeared in the crucible of time, but others managed to save, passing from father to son, ancestral traditions for centuries.
- Who was the first to forge your glorified dynasty?
Tempering line
- Fujiwara Kanefusa - he was the first. It is at the junction of his red-hot and soft zones turned out, has long been valued as experts, special boundary hardening the blade (ham) that bears his same name, "Fujiwara tedzi" or "Clover Fujiwara." This plant, and at the same time, the dynamic pattern of the quenching line remarkably conveys movement, development ... Sometimes the wavy line, which experts called "the soul of the blade" more resembles the outlines of hills or mountains, lost in the blue haze of the horizon ... It is this distinctive - crony - sign Fujiwara Kanefusa swords and handed down from one generation to another, and reached our days
- Is only pattern, even tenderly cultivated clan, capable of defeating time? .. Or is there something more important in the Japanese sword?
- The blade itself, its pattern, line hardening ham and sharpness - meets the master. - Of course, an important and very significant and complex Garda sword - tsuba and the ring adjacent to it - and others - author - finishing elements "kosirae" (frame sword). But just exactly how to forge as hardened as polished blade - that are laid all the fighting and aesthetic properties of the sword.
- That's when the line of ham can be difficult to look away ...
- Today, in Japan, there are several major clans of smiths, gunsmiths, supporting the main "Blade" canons. Legends like the Japanese masters carefully keep their secrets of manufacturing swords. It features hand-forged and different in composition and structure of composite steel and secrets hardening zone along the blade and tricks hand-polishing stones, reveals moire patterns "Hud" and tempering line "jamon". Could you, Fujiwara-san, tell us, at least briefly, as, for example, from steel syrodutnoy tamahagane obtained patterned blade?
- I can not - briefly replied the master.
- From the conversation it is very difficult to properly understand how and what to do. Even my disciples did not understand everything, and yet they look as I do.
- How many combat swords have made you and your generation?
- During the whole race - it's hard to say something, without falling into error ... As for me, in the last ten years, I forge 250 different blades and short and long. Of these, one hundred - well, and ten - very good. I note only that the main purpose of katana is not a fight, but to protect.
- Can I see your products in Russia?
- A good half of my top ten Katan bought Russian collectors.
When considering the close, the line turns into a group of ham-crystal grains, changing the intensity, sometimes disappears. Patterns are changing in the direction of the blade and the blade to the Obukhov
LOCATION, OPERATION
namolennye - You are making swords different "grades"? What katana fall under the definition of "good"?
- In these swords is an important feature - they are made in a special pace, with a special spirit ... the inner attitude of the master and his team ... They are investing in blade not only his skill, ability, talent, they leave Catania piece of his soul and even his fate or , speaking in the eastern, karma.
- You said, "special rate". How much time spent on production of one unit of arms in the middle?
- No matter how many times it took a good job. Do a good job in the mood, there's pace, and it goes fast! I can, without looking at the anvil, only hearing to determine how to argue things are going in the studio. You know, how different can sound under the hammer metal? Do you know what it says? If you like this (knocking on the table): top-Kahn ... Tinn - means that something has gone wrong! But when I hear a clatter: Tinn top-ton! - Then, the pace and punch right. In the final hammer blow must issue a resounding "tonnes" and in any case not raskvashennoe "Cannes"! Our work is important not rulers and thermometers. Important direct conversation with the material and fire. The fire - he can tell a lot about metal. Share and, if necessary, supporting master. Fire - God is the master. And his friend. He tells color. The color is red flame - too early to start. Yellow flames - signal the Ready! Golden fire - while forging.
- Getting Started, what more do you look first?
- It is important to choose the right place for a forge. In Japanese, it sounds like: a place Dojo! This master and students come every day. Here, from morning to night noise horn and pounding hammers. It is necessary to result in severe and, in general, monotonous work, eventually born inspired work of art and technology. You know, when that happens? When the space size reduction operation. The work of generations.
- The sword ready. Collected Futi - oval, thin-walled metal coupling at the mouth of the handle, Kathir - chashkoobraznoe oval pommel handle other copyrights elements ... How to test the fighting qualities of the unique works of art and technology?
- I want to stress once more. Japanese sword is not created as a weapon of struggle. This is primarily defense weapon. He became one of the most advanced in the world kinds of bladed weapons, because checking the centuries of practical fencing.
- Japan - a recognized trendsetter in the field of high technologies. Does this impact on the modern manufacturing technique of the sword? Specifically: how to achieve high-tech are applied at the current master of the katana?
- I'm afraid I have to disappoint: no, no. Not found. I do not know of such examples. Innovation, departures from the canon and tradition of our ancient craft contraindicated. Here, in the course of other criteria.
- I wonder what is it?
- Say, verified technology works with metal. From the perspective of a blacksmith, gunsmith, technologically advanced nation, not least determined by the achievements in the field of metal processing. The Japanese have mastered the work with metal a thousand years ago, about the same age, and Japanese sword. The ancient culture of work with iron - this is a true symbol of the country.
Fujiwara Kanefusa XXV, tanto, March 2009 Sheath matt varnish with a picture of leaves made of gold colored matt lacquer, mother of pearl. The length of the sword in the scabbard 42 cm, weight 445 g
- With rolled into battle not go. Although the Battle of the samurai without swords, as a rule, can not do. The deep meaning in the fact that these weapons are intended primarily for protection. Instead of attacking. Katana, first of all, is revered as a work of art as a symbol of strength, protection, talisman, not a weapon for aggression. However, the defense implies warfare. Of course, modern swords - works of art - do not cut (or do so rarely on the above reasons), protecting expensive (literally and figuratively) swords.
- And the last question, Fujiwara-san. What is the situation you have with the succession of generations? Do you have in mind, who will extend into the future line of "Fujiwara tendzi"?
- My son, Fujiwara XXVI. His latest work has received international prizes and has just been bought by a collector ...
- From Russia?
- Yes. Do you love and appreciate Japanese weapons. Therefore, I plan to make a film, a kind of master class on making katana. His presentation, together with the "Kasumi Group", will spend the autumn exhibition at the "Gostiny Dvor". There we invite all fans of author's cold steel.
- Thanks for the interview and see you on the master class, Fujiwara-san!
HERE
Photo for memory
Source:
Master and keeper of the tradition of the famous Japanese arms no less famous in Japan than, say, a member of the imperial family, gave an exclusive interview.
The generic name is Fujiwara Kanefusa Kazuo Kato, a Japanese master blacksmith in the 25th generation. Born in 1957, the 32-year Showa era. He graduated from high school and enrolled as an apprentice to the legendary master Hassan Sadaiti. Since 1983, he learned the art of forging and engraving under the guidance of his father. It takes a year and Cato opened his own studio in the very spot where once stood the shop of his grandfather, was destroyed by the typhoon. On the opening day of the new studio and lighting Kato favorite tools inherited his grandfather and name: Fujiwara Kanefusa XXV. The first blade is created in the new studio newfound Fujiwara Kanefusa, he won first prize at an exhibition of contemporary swords. This was followed by Kaoruyama Award, a prize for excellence and other awards. Among the blades, made master of the swords to the Meiji Shrine and Atsuta, weapons for heroes yokozuna. Blacksmiths Association has chosen the city of Seki Fujiwara Kanefusu Chairman of the Board.
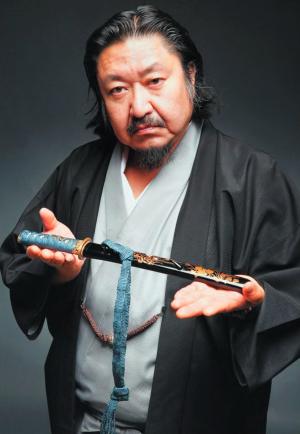
I knew almost certainly that get an audience with the man whose family from month to month, from year to year - and so 700 years in a row! - Defended at the forge, of making the legendary samurai swords - yes another case just will not!
We met as agreed at the exhibition in Gostiny Dvor. Handshake master was dense and powerful, like a blacksmith. Stocky, broad-shouldered and stout figure in a gray kimono. Butch, deep and at the same time tenacious gaze of dark eyes. Something similar to vangogovskogo Dr. Ray, a graduate school of Sumo.
I give him a selection of special editions "Authors cold steel»:
- I know your magazine - with a nod and a faint half-smile eastern, hidden in the folds of a large person responsible master.
I remember with emotion the words of gratitude in the language of the interviewee - Arigoto! And with emotion, the Japanese style, put his hands clasped to his chest.
In preparation for the interview, I looked at the photo and video files: pictures of studio Fujiwara, depicting the scene of forging. How few, but significant, each in its place, the participants of this action .. Apprentice fanned furs yellow fire in the hearth, metal apprentice tripped to the searing flames, and the master, with the tool at the ready, met crimson glow of the workpiece at the anvil. Much more than a mise en scene "forging swords in the forge of the Japanese," I was struck by the interior of a smithy and its furniture. And yet - white garments inspired blacksmiths and their expressions.
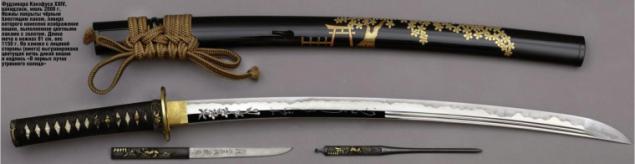
WARRIORS white robes
... I am well aware of Russian Interior forge. Gloomy twilight in which lurk the dark corners. Zakopchёnnye wall fumes in the air and chipping iron under my feet. Sweaty, soiled with soot persons artisan in the wet T-shirts that put stiff, long-lost color and texture, leather or canvas aprons.
- Master Fujiwara - I ask - how did you manage to iron must be forged to the forge, and the wall, and he horn rend reason gold, without smoke and soot flames - all shining white surgical?
A master and his disciples, dressed like angels in white kimono with wide sleeves, moving as if they Actors from the theater Kobuk? ..
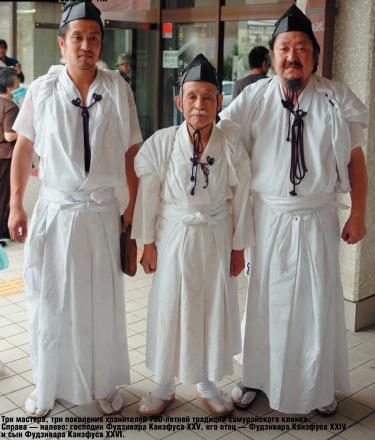
- For the Japanese sword - is not just a piece of iron, it is holy. To touch the skating, it is necessary that around and everything was clean. - A voice like Fujiwara-san answers I probably recite the mantra.
- But white clothes so easy to dirty! Why are you elected is white? - I try to find out.
- Do not we have elected. It's an old tradition ... This was the clothing of ancient warriors since Muromachi, - Master says gravely. Apparel masters were cut free, with long, as at kintos, sleeves. Blacksmiths work with open fire and hot metal without gloves! No mechanization, everything by hand. Nothing should separate the blacksmith and his creation - the blade.
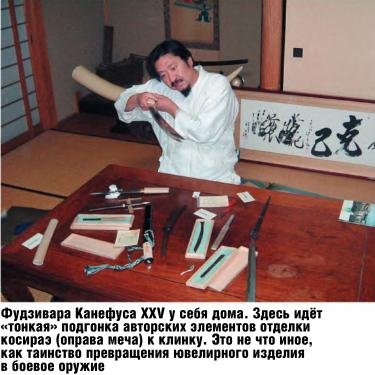
Japanese smiths Dynasty originated in the Middle Ages. Demand for their work - two-handed edged slightly bent swords with removable handle and hilt, braided cord, was, as ever, high. Some clans disappeared in the crucible of time, but others managed to save, passing from father to son, ancestral traditions for centuries.
- Who was the first to forge your glorified dynasty?
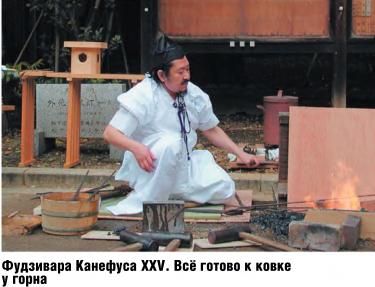
Tempering line
- Fujiwara Kanefusa - he was the first. It is at the junction of his red-hot and soft zones turned out, has long been valued as experts, special boundary hardening the blade (ham) that bears his same name, "Fujiwara tedzi" or "Clover Fujiwara." This plant, and at the same time, the dynamic pattern of the quenching line remarkably conveys movement, development ... Sometimes the wavy line, which experts called "the soul of the blade" more resembles the outlines of hills or mountains, lost in the blue haze of the horizon ... It is this distinctive - crony - sign Fujiwara Kanefusa swords and handed down from one generation to another, and reached our days
- Is only pattern, even tenderly cultivated clan, capable of defeating time? .. Or is there something more important in the Japanese sword?
- The blade itself, its pattern, line hardening ham and sharpness - meets the master. - Of course, an important and very significant and complex Garda sword - tsuba and the ring adjacent to it - and others - author - finishing elements "kosirae" (frame sword). But just exactly how to forge as hardened as polished blade - that are laid all the fighting and aesthetic properties of the sword.
- That's when the line of ham can be difficult to look away ...
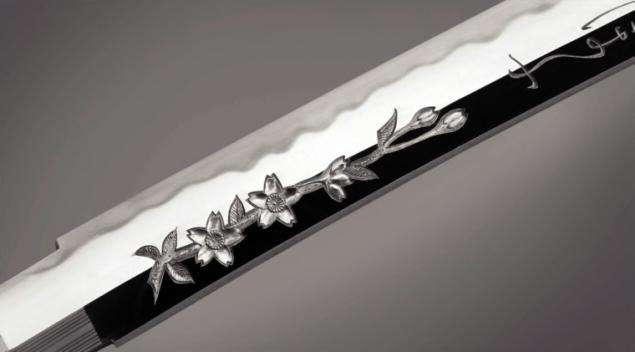
- Today, in Japan, there are several major clans of smiths, gunsmiths, supporting the main "Blade" canons. Legends like the Japanese masters carefully keep their secrets of manufacturing swords. It features hand-forged and different in composition and structure of composite steel and secrets hardening zone along the blade and tricks hand-polishing stones, reveals moire patterns "Hud" and tempering line "jamon". Could you, Fujiwara-san, tell us, at least briefly, as, for example, from steel syrodutnoy tamahagane obtained patterned blade?
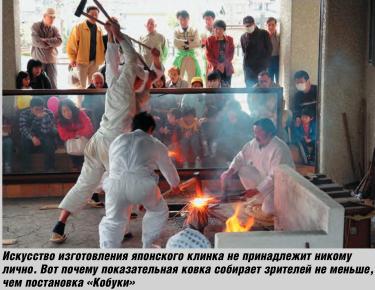
- I can not - briefly replied the master.
- From the conversation it is very difficult to properly understand how and what to do. Even my disciples did not understand everything, and yet they look as I do.
- How many combat swords have made you and your generation?
- During the whole race - it's hard to say something, without falling into error ... As for me, in the last ten years, I forge 250 different blades and short and long. Of these, one hundred - well, and ten - very good. I note only that the main purpose of katana is not a fight, but to protect.
- Can I see your products in Russia?
- A good half of my top ten Katan bought Russian collectors.
When considering the close, the line turns into a group of ham-crystal grains, changing the intensity, sometimes disappears. Patterns are changing in the direction of the blade and the blade to the Obukhov
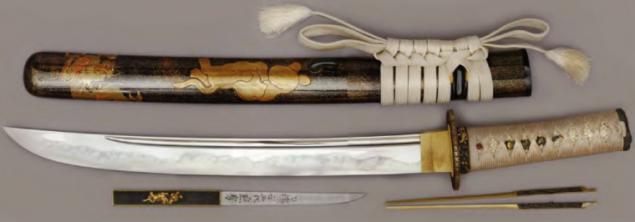
LOCATION, OPERATION
namolennye - You are making swords different "grades"? What katana fall under the definition of "good"?
- In these swords is an important feature - they are made in a special pace, with a special spirit ... the inner attitude of the master and his team ... They are investing in blade not only his skill, ability, talent, they leave Catania piece of his soul and even his fate or , speaking in the eastern, karma.
- You said, "special rate". How much time spent on production of one unit of arms in the middle?
- No matter how many times it took a good job. Do a good job in the mood, there's pace, and it goes fast! I can, without looking at the anvil, only hearing to determine how to argue things are going in the studio. You know, how different can sound under the hammer metal? Do you know what it says? If you like this (knocking on the table): top-Kahn ... Tinn - means that something has gone wrong! But when I hear a clatter: Tinn top-ton! - Then, the pace and punch right. In the final hammer blow must issue a resounding "tonnes" and in any case not raskvashennoe "Cannes"! Our work is important not rulers and thermometers. Important direct conversation with the material and fire. The fire - he can tell a lot about metal. Share and, if necessary, supporting master. Fire - God is the master. And his friend. He tells color. The color is red flame - too early to start. Yellow flames - signal the Ready! Golden fire - while forging.
- Getting Started, what more do you look first?
- It is important to choose the right place for a forge. In Japanese, it sounds like: a place Dojo! This master and students come every day. Here, from morning to night noise horn and pounding hammers. It is necessary to result in severe and, in general, monotonous work, eventually born inspired work of art and technology. You know, when that happens? When the space size reduction operation. The work of generations.
- The sword ready. Collected Futi - oval, thin-walled metal coupling at the mouth of the handle, Kathir - chashkoobraznoe oval pommel handle other copyrights elements ... How to test the fighting qualities of the unique works of art and technology?
- I want to stress once more. Japanese sword is not created as a weapon of struggle. This is primarily defense weapon. He became one of the most advanced in the world kinds of bladed weapons, because checking the centuries of practical fencing.
- Japan - a recognized trendsetter in the field of high technologies. Does this impact on the modern manufacturing technique of the sword? Specifically: how to achieve high-tech are applied at the current master of the katana?
- I'm afraid I have to disappoint: no, no. Not found. I do not know of such examples. Innovation, departures from the canon and tradition of our ancient craft contraindicated. Here, in the course of other criteria.
- I wonder what is it?
- Say, verified technology works with metal. From the perspective of a blacksmith, gunsmith, technologically advanced nation, not least determined by the achievements in the field of metal processing. The Japanese have mastered the work with metal a thousand years ago, about the same age, and Japanese sword. The ancient culture of work with iron - this is a true symbol of the country.
Fujiwara Kanefusa XXV, tanto, March 2009 Sheath matt varnish with a picture of leaves made of gold colored matt lacquer, mother of pearl. The length of the sword in the scabbard 42 cm, weight 445 g
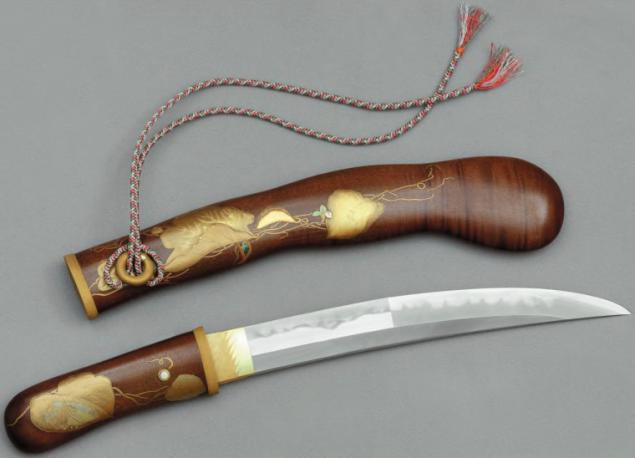
- With rolled into battle not go. Although the Battle of the samurai without swords, as a rule, can not do. The deep meaning in the fact that these weapons are intended primarily for protection. Instead of attacking. Katana, first of all, is revered as a work of art as a symbol of strength, protection, talisman, not a weapon for aggression. However, the defense implies warfare. Of course, modern swords - works of art - do not cut (or do so rarely on the above reasons), protecting expensive (literally and figuratively) swords.
- And the last question, Fujiwara-san. What is the situation you have with the succession of generations? Do you have in mind, who will extend into the future line of "Fujiwara tendzi"?
- My son, Fujiwara XXVI. His latest work has received international prizes and has just been bought by a collector ...
- From Russia?
- Yes. Do you love and appreciate Japanese weapons. Therefore, I plan to make a film, a kind of master class on making katana. His presentation, together with the "Kasumi Group", will spend the autumn exhibition at the "Gostiny Dvor". There we invite all fans of author's cold steel.
- Thanks for the interview and see you on the master class, Fujiwara-san!
HERE
Photo for memory
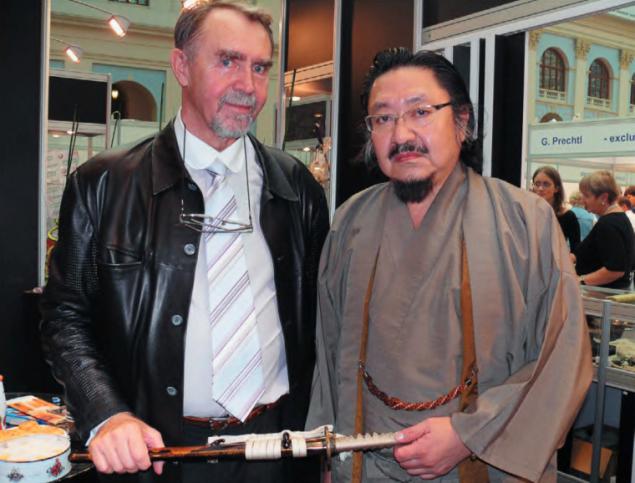
Source: