1430
Production of solar panels
This photoelectric converters - semiconductor devices that convert solar energy into direct current. Simply put, these are the main elements of the device, which we call "solar panels". With the help of such batteries into orbit working satellites. Make these batteries we have in Krasnodar - the factory "Saturn".
. Enterprise in Krasnodar part of the Federal Space Agency, but has "Saturn" company "Ochakovo", which literally saved this production in the 90s. The owners of "Ochakovo" acquired a controlling stake, which had almost gone to Americans. "Ochakovo" put here a lot of money by purchasing advanced equipment, has managed to retain specialists and now "Saturn" - one of the two leaders in the Russian market for the production of solar and rechargeable batteries for the needs of the space industry - civil and military. All profits earned by the "Saturn", remains here in Krasnodar, and is on the development of the production base.
So, it all starts here - in the area of so-called vapor-phase epitaxy. In this room there is a gas reactor, in which on a substrate made of germanium for three hours the crystalline layer is grown to serve as a basis for future photocell. The cost of such a facility - about three million euros.
After that, the substrate is still a long way to go: on both sides of the photocell will cause the electrical contacts (and, on the working side of the contact will be "picture-size fits all", whose dimensions are carefully calculated to ensure maximum passage of sunlight) will appear on the substrate-coated and etc. - More than two dozen manufacturing operations at various plants before photocell will form the basis of solar cell.
For example, the installation of photolithography. Here photocell formed "drawings" electrical contacts. The machine performs all operations automatically, for a given program. Here and in the light of relevant, that does not harm the photosensitive layer photocell - as before, in the era of analog photography, we used the "red» Lamps.
In a vacuum deposition installation using an electron beam applied electrical contacts and insulators as well as antireflection coating applied (they increase the current generated by the photocell 30%).
Well, the photocell is ready and you are ready to assemble the solar cell. Are soldered to the surface of the photocell tire, then to connect them with each other and are glued to the protective glass, in which the free space under the radiation, the photocell can not withstand loads. And, although the thickness stekla only 0, 12 mm, battery with such solar cells will be a long time to work on the orbit (in high orbits for more than fifteen years).
The electrical connection between the solar cells are made of silver contacts (called busses) thickness of 0, 02 mm.
To obtain a desired voltage is generated by a solar battery, photoelectric cells connected in series. Here is the section of the series-connected solar cells (photovoltaic cells - so right).
Finally, the solar cell is assembled. Here, we show only a portion of the battery - panel format layout. Such panels on a satellite may have up to eight, depending on whether power is needed. In modern communication satellites, it reaches 10 kW. These panels will be mounted on a satellite in space they unfold like wings, and with their help we will watch satellite TV, enjoy satellite internet, navigation systems (satellites "Glonass" Krasnodar use solar panels).
When the spacecraft is illuminated by the sun, electricity generated by solar battery powers the system unit, and the excess energy is stored in the battery. When the spacecraft is in the shadow of the Earth, machine uses the energy stored in the battery. Nickel-hydrogen battery having a high energy (60 Wh / kg) and virtually inexhaustible resource, is widely used in spacecraft. The production of such batteries - another part of the plant "Saturn».
In this image, the assembly of nickel-hydrogen battery produces Chevalier Medal of the Order "For Services to the Motherland» II degree Anatoly Panin.
Assembly shop of nickel-hydrogen batteries. Filling the battery is prepared for placement in the body. Filling - a positive and negative electrodes separated by the separator paper - in them, and there is a transformation and storage of energy.
Apparatus for electron beam welding in vacuum whereby manufactured battery housing made of thin metal.
Plot shop, where the body and parts batteries are tested for effects of high blood pressure.
Due to the fact that the accumulation of energy in the battery is accompanied by the formation of hydrogen and the pressure inside the battery increases, the leak test - an integral part of the manufacturing process of the battery.
Base nickel-hydrogen battery - a very important part of the entire device, working in space. The housing is designed for the pressure of 60 kg · s / cm2, when tested rupture occurred at a pressure of 148 kg · s / cm2.
Proven strength battery is charged with electrolyte and hydrogen, and then they are ready to go.
Housing nickel-hydrogen battery is made of a special metal alloy and must be mechanically strong, lightweight and have a high thermal conductivity. Batteries are installed in the cell and not in contact with each other.
Accumulators and batteries collected are subjected to an electrical test on its own production. In space, nothing will be impossible to fix and replace, so here thoroughly test each product.
All space technology shall be tested for exposure via vibratory stands that simulate the load during injection of the spacecraft into orbit.
In general, the plant "Saturn" produced the most favorable impression. Production is well organized, the shop is clean and bright, the people running qualified to deal with such experts - a pleasure and a very interesting person, at least to some extent, the interests of our cosmos. Left with "Saturn" in a good mood - always nice to look at our place are not engaged in idle chatter and no shift of paper and make real, serious business, successfully competing with the same producers in other countries. Would be more in Russia this.
drugoi
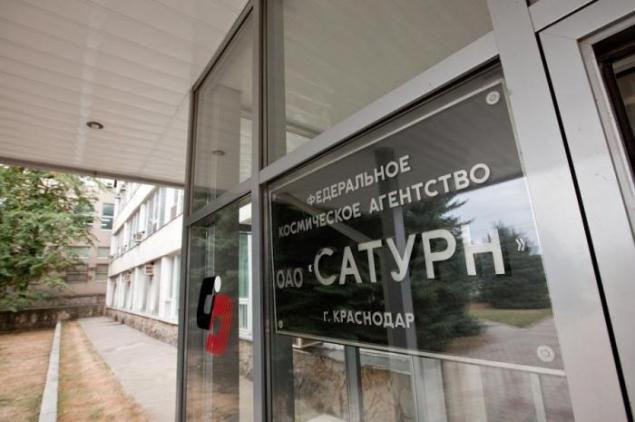
. Enterprise in Krasnodar part of the Federal Space Agency, but has "Saturn" company "Ochakovo", which literally saved this production in the 90s. The owners of "Ochakovo" acquired a controlling stake, which had almost gone to Americans. "Ochakovo" put here a lot of money by purchasing advanced equipment, has managed to retain specialists and now "Saturn" - one of the two leaders in the Russian market for the production of solar and rechargeable batteries for the needs of the space industry - civil and military. All profits earned by the "Saturn", remains here in Krasnodar, and is on the development of the production base.
So, it all starts here - in the area of so-called vapor-phase epitaxy. In this room there is a gas reactor, in which on a substrate made of germanium for three hours the crystalline layer is grown to serve as a basis for future photocell. The cost of such a facility - about three million euros.
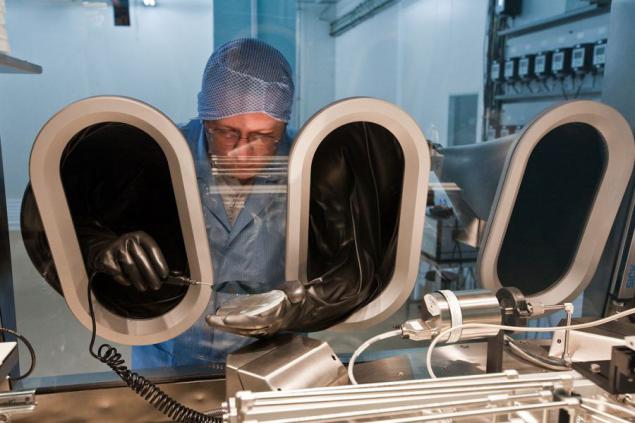
After that, the substrate is still a long way to go: on both sides of the photocell will cause the electrical contacts (and, on the working side of the contact will be "picture-size fits all", whose dimensions are carefully calculated to ensure maximum passage of sunlight) will appear on the substrate-coated and etc. - More than two dozen manufacturing operations at various plants before photocell will form the basis of solar cell.
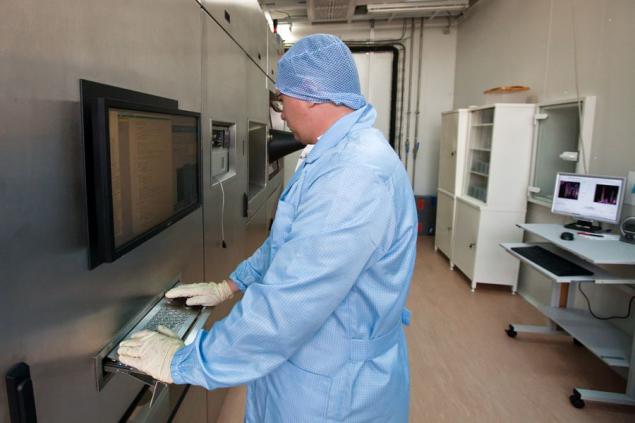
For example, the installation of photolithography. Here photocell formed "drawings" electrical contacts. The machine performs all operations automatically, for a given program. Here and in the light of relevant, that does not harm the photosensitive layer photocell - as before, in the era of analog photography, we used the "red» Lamps.
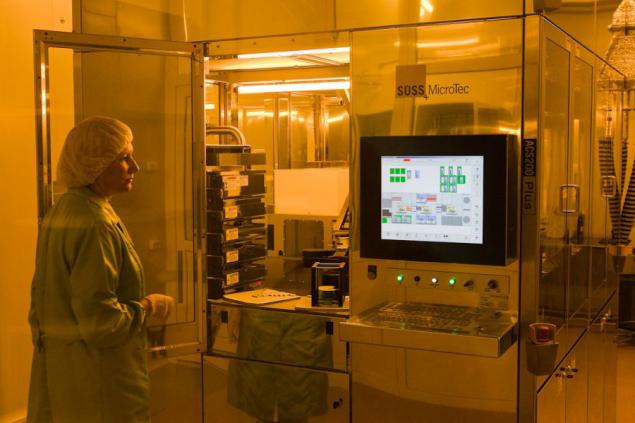
In a vacuum deposition installation using an electron beam applied electrical contacts and insulators as well as antireflection coating applied (they increase the current generated by the photocell 30%).
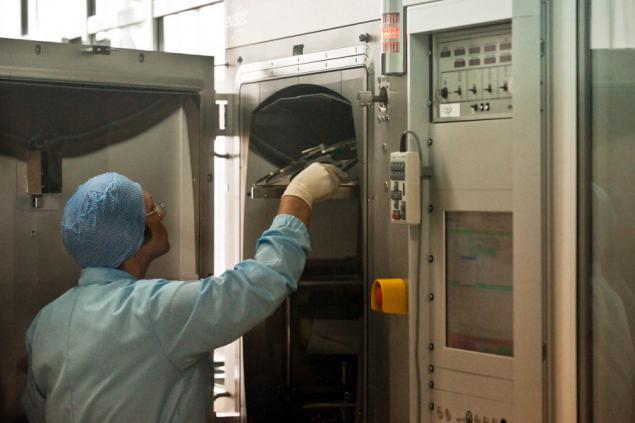
Well, the photocell is ready and you are ready to assemble the solar cell. Are soldered to the surface of the photocell tire, then to connect them with each other and are glued to the protective glass, in which the free space under the radiation, the photocell can not withstand loads. And, although the thickness stekla only 0, 12 mm, battery with such solar cells will be a long time to work on the orbit (in high orbits for more than fifteen years).
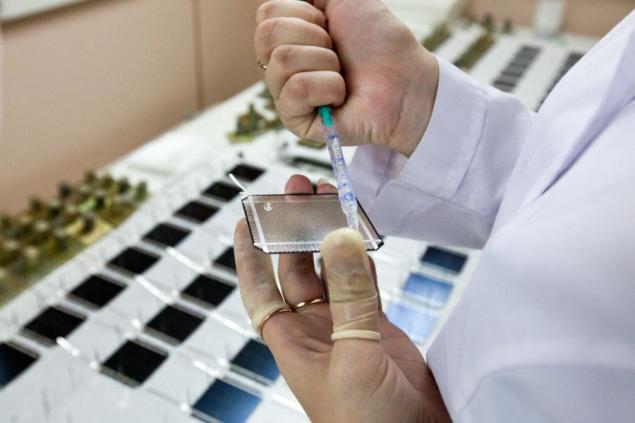
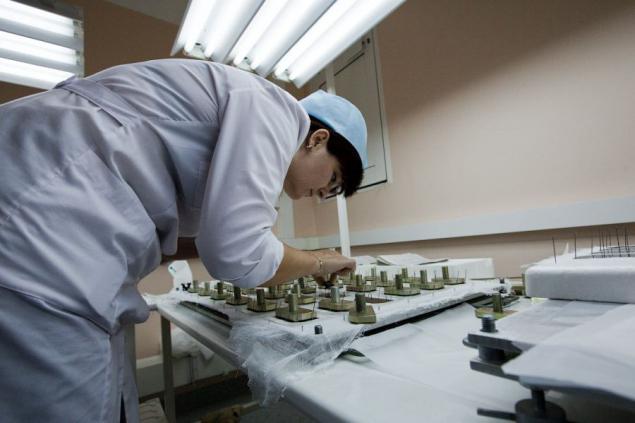
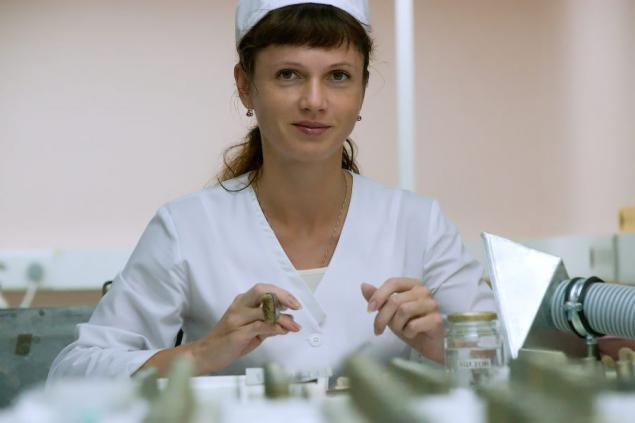
The electrical connection between the solar cells are made of silver contacts (called busses) thickness of 0, 02 mm.
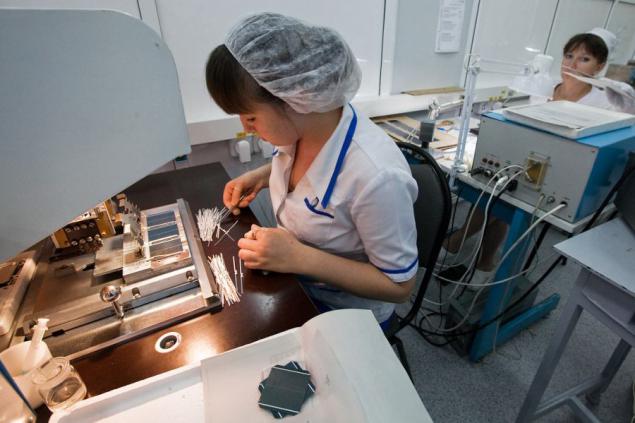
To obtain a desired voltage is generated by a solar battery, photoelectric cells connected in series. Here is the section of the series-connected solar cells (photovoltaic cells - so right).
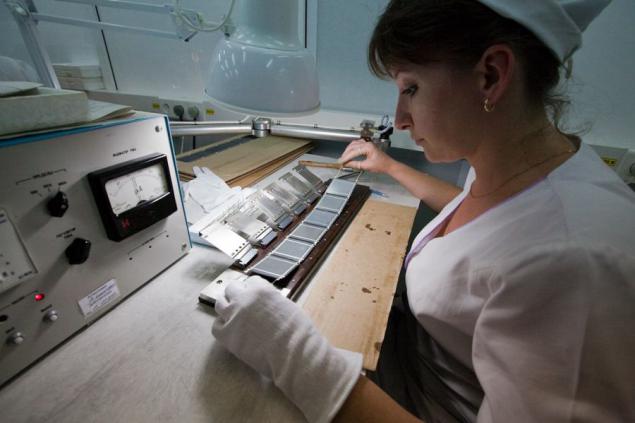
Finally, the solar cell is assembled. Here, we show only a portion of the battery - panel format layout. Such panels on a satellite may have up to eight, depending on whether power is needed. In modern communication satellites, it reaches 10 kW. These panels will be mounted on a satellite in space they unfold like wings, and with their help we will watch satellite TV, enjoy satellite internet, navigation systems (satellites "Glonass" Krasnodar use solar panels).
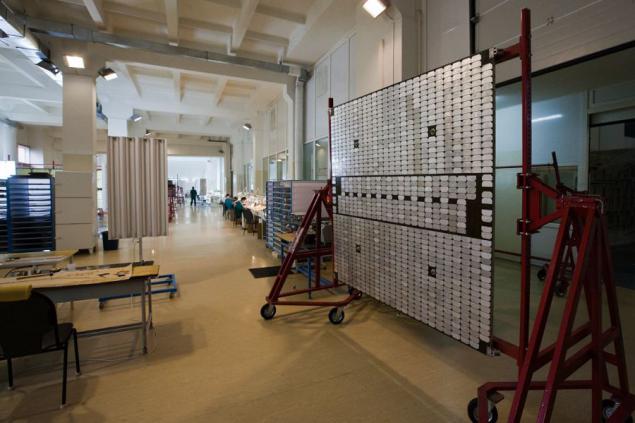
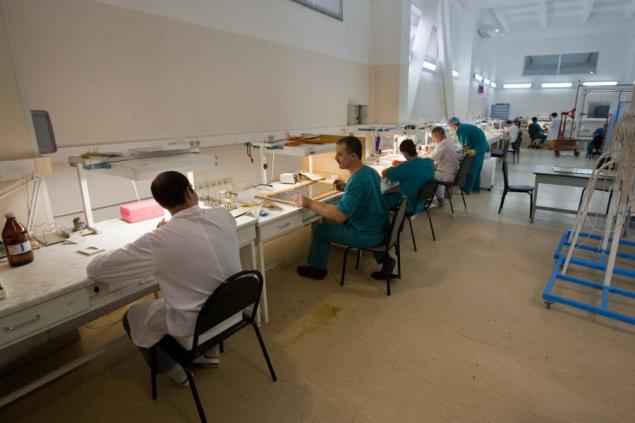
When the spacecraft is illuminated by the sun, electricity generated by solar battery powers the system unit, and the excess energy is stored in the battery. When the spacecraft is in the shadow of the Earth, machine uses the energy stored in the battery. Nickel-hydrogen battery having a high energy (60 Wh / kg) and virtually inexhaustible resource, is widely used in spacecraft. The production of such batteries - another part of the plant "Saturn».
In this image, the assembly of nickel-hydrogen battery produces Chevalier Medal of the Order "For Services to the Motherland» II degree Anatoly Panin.
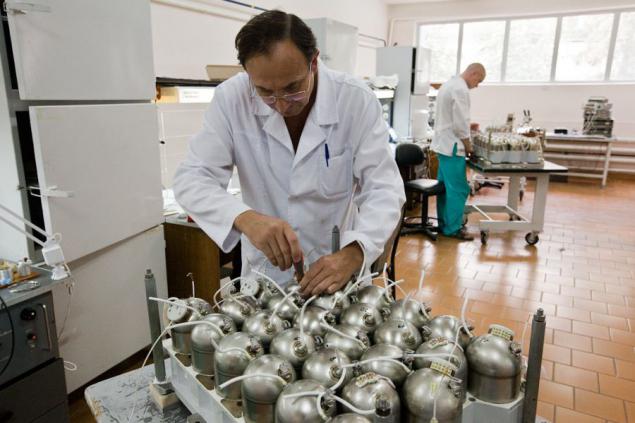
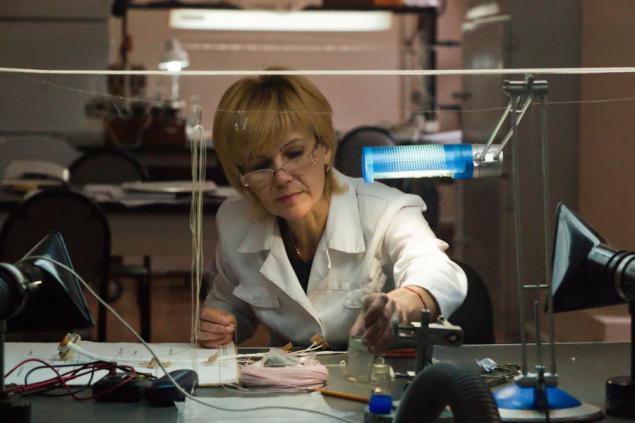
Assembly shop of nickel-hydrogen batteries. Filling the battery is prepared for placement in the body. Filling - a positive and negative electrodes separated by the separator paper - in them, and there is a transformation and storage of energy.
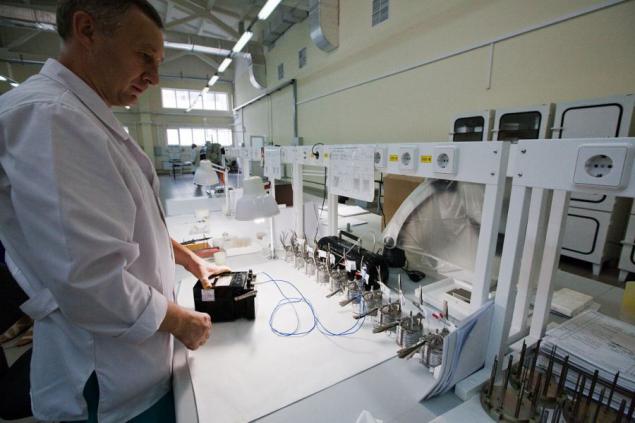
Apparatus for electron beam welding in vacuum whereby manufactured battery housing made of thin metal.
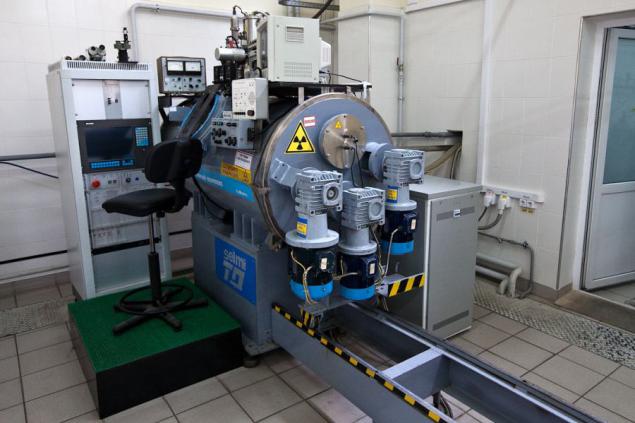
Plot shop, where the body and parts batteries are tested for effects of high blood pressure.
Due to the fact that the accumulation of energy in the battery is accompanied by the formation of hydrogen and the pressure inside the battery increases, the leak test - an integral part of the manufacturing process of the battery.
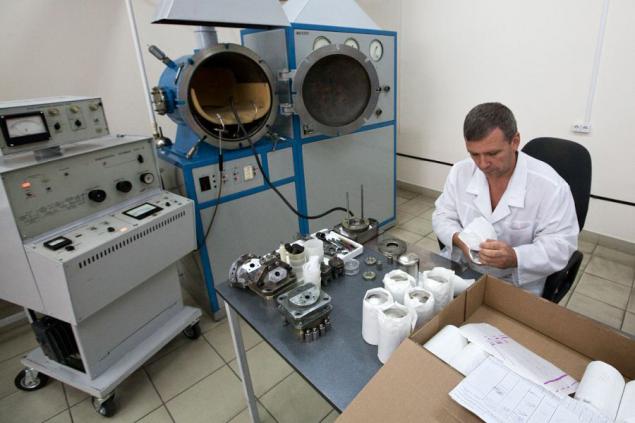
Base nickel-hydrogen battery - a very important part of the entire device, working in space. The housing is designed for the pressure of 60 kg · s / cm2, when tested rupture occurred at a pressure of 148 kg · s / cm2.
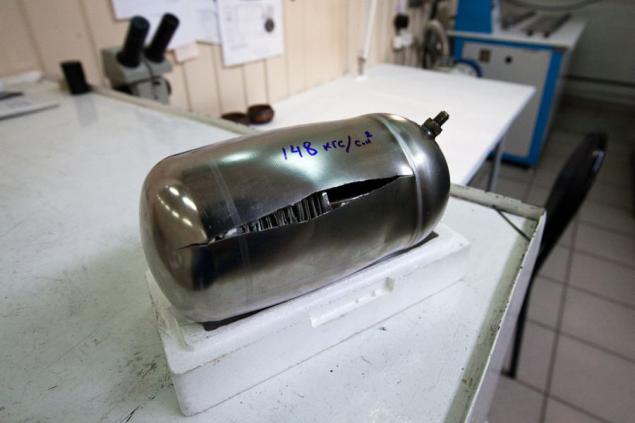
Proven strength battery is charged with electrolyte and hydrogen, and then they are ready to go.
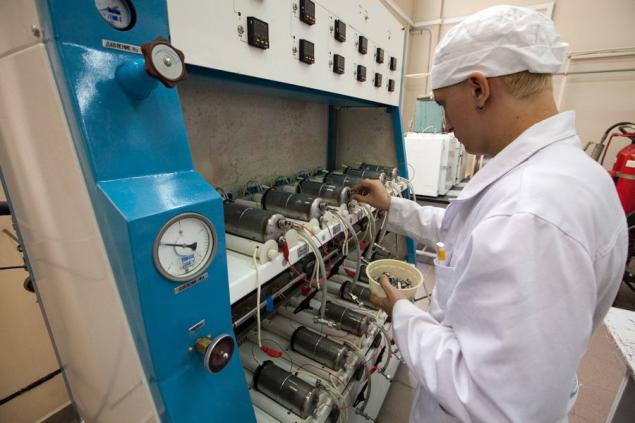
Housing nickel-hydrogen battery is made of a special metal alloy and must be mechanically strong, lightweight and have a high thermal conductivity. Batteries are installed in the cell and not in contact with each other.
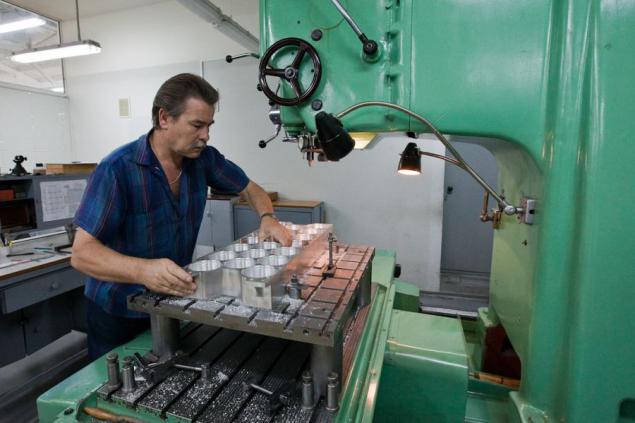
Accumulators and batteries collected are subjected to an electrical test on its own production. In space, nothing will be impossible to fix and replace, so here thoroughly test each product.
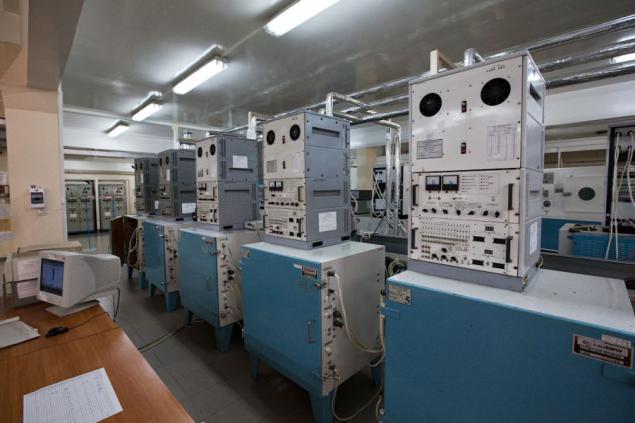
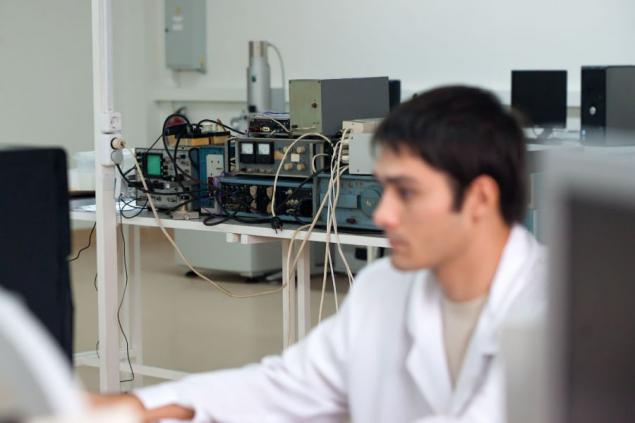
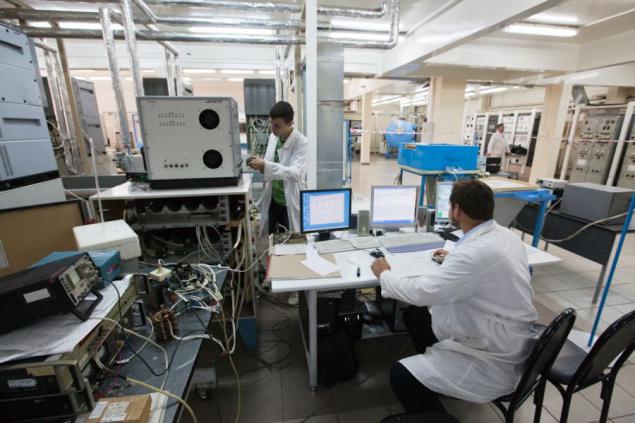
All space technology shall be tested for exposure via vibratory stands that simulate the load during injection of the spacecraft into orbit.
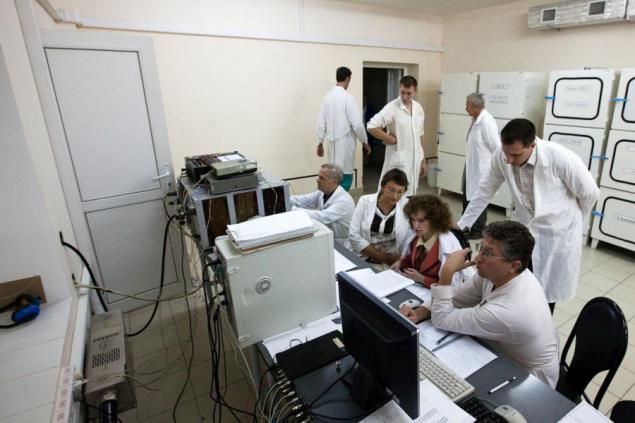
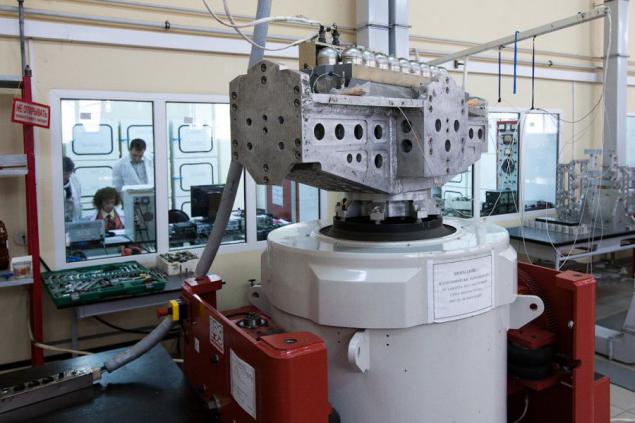
In general, the plant "Saturn" produced the most favorable impression. Production is well organized, the shop is clean and bright, the people running qualified to deal with such experts - a pleasure and a very interesting person, at least to some extent, the interests of our cosmos. Left with "Saturn" in a good mood - always nice to look at our place are not engaged in idle chatter and no shift of paper and make real, serious business, successfully competing with the same producers in other countries. Would be more in Russia this.
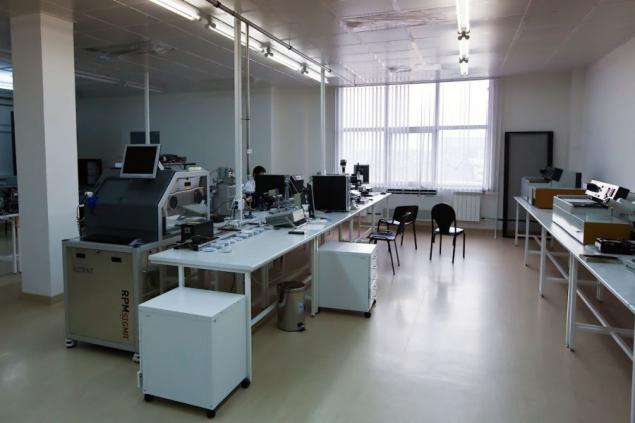
drugoi