420
At MIT have created artificial muscle fibres from nylon
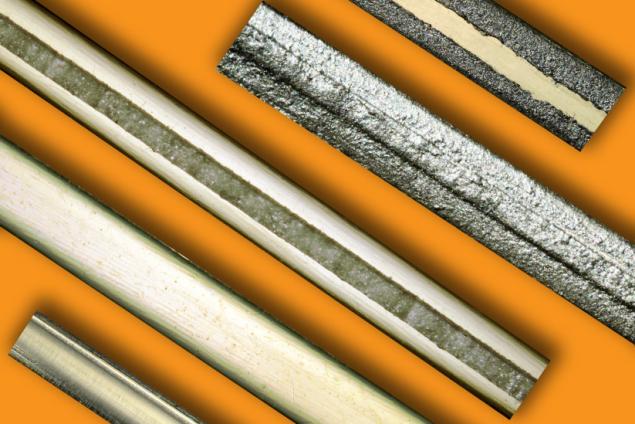
Artificial muscles – materials that can shrink and contract like muscle fibers. They can be used in many fields: from robotics components to the automotive and aviation industry. Researchers from mit have said that it has developed the simplest and cheapest system to create these "muscles".
A key component of which scientists at MIT made fiber artificial muscle – an inexpensive and widespread nylon fiber. A new approach to the use of this material is in formation and heating of the fibers in a certain way.
Previously, researchers have developed the principle of using swirling spirals of nylon fibers to simulate the progressive muscle. They showed that in particular the size and weight of such devices could expand and contract, storing and releasing more energy than natural muscles. But to repeat the bending movement of the fingers and limbs of a man – a more complex task. According to researchers at MIT, still nobody has been able to solve this problem simply and cheaply.
There are materials that can be used for the reproduction of the curving movements in biomedical devices or tactile displays. But most often these materials are "exotic" and expensive, they are difficult to produce. For example, yarns of carbon nanotubes – a durable material that can withstand over one million cycles of compression, but still too expensive for widespread use. Alloys with shape memory effect provide a strong tension, but can withstand only 1000 cycles.
In the new system, using cheap material and simple manufacturing process. Nylon can withstand a sufficient number of cycles is due to the method of formation of the nylon fibers. Some of the material of the polymer fibers, including nylon, have an unusual property: when heated, they shrink in length but expand in diameter. Some scientists have used this property to create a device of the linear actuator. But to transform a linear translational motion in the bends, the necessary devices like a mechanical block, or the winding drum. It adds complexity and increases costs. Team MIT was going to use directly the strength of the movement without additional mechanical parts.
Linear actuators made of polymer materials, there is one drawback: to cause reduction of the material to be cooled. The rate of cooling may be the limiting factor. However, scientists have realized that this disadvantage can become an advantage. Selective heating of one side of the fiber causes it to shrink faster than the heat comes to the opposite side. Thus, the thread may deviate to the side. As noted by the PhD candidate Seyed Miracoli, lead author of the study, it was necessary to combine the two properties: high voltage (tension reduction) and low thermal conductivity.
To make this system work effectively as a artificial muscle, a section of the fiber needs to be processed carefully. To change cross section from round to rectangular or square, the team would "flatten" them. The researchers then heated one side, forcing the fiber to bend. The change of direction of heating led to the fact that fiber played a more complex movement. In laboratory tests, the team used this method of heating to cause the fibers to perform a circular movement and "eight". According to scientists, the fibers can move forward with more complex trajectories.
As a heat source suitable electrical resistance heater, a chemical reaction or a laser beam that is emitted on the thread. In some experiments, the researchers put on a special fiber, conductive paint and kept in one place with binder resins. Energized heated only part of the fibers coated with paint. Heated on the one hand, the fiber could be deflected. If you heat it with the opposite, the thread returns to its original position.
Studies have shown that the material can withstand at least 100 thousand cycles of bending and is able to contract and relax up to 17 times per second. According to Ian hunter, one of the authors of the study, such fibers suitable for the production of clothing, which will shrink to adapt to the contours of the human body. Then the producers could cut size line, increasing comfort and ease of fit. From bendable fibers to make shoes that will fit exactly on the leg and its stiffness and shape will be with every step adjustable.
The system can be used for the production of a self-tuning catheters and other biomedical devices. In the long term, you can create a mechanical system, such as external panels for automobiles. Panels of fiber will adjust aerodynamic shape to adapt to changes in speed and wind. Or they can be used as an automatic “tracking systems” for solar panels. They would use the excess heat to control the orientation of the panels towards the Sun.
Scientific work published in the journal Advanced Materials 23 Nov 2016
DOI: 10.1002/adma.201604734
Source: geektimes.ru/post/282982/