841
As a facet of the diamond
As many probably know, diamond, for all its other merits of a technical nature only becomes «the girl's best friend», when transformed into a diamond. On what path it will go while our present photo story. It begins with a hanger ... guess. The visitors to break the post production processing of solid materials (as officially called faceting), offer to put on a dressing gown, hand over hand luggage, sew and attach the pockets of at least two attendants: shop worker performing the role of a guide and employee department of economic security. Trust, as they say, but verify.
Now we're ready to get acquainted with the shop. The first item on the itinerary - pantry raw materials.
It arrives here raw materials - rough diamonds. Here they oprihoduyut: recalculate, weigh, check compliance with shipping documents, ENTERED every stone in an electronic database of records and discharged on each stone kind of road map. In this roadmap, folded in an envelope, diamond, and will travel to sites.
From the pantry diamond falls on UZTTS - section closed technological cycle. Here technology will sort and mark stones.
This is done by means of a computer markup. Installation of Diamond scans and creates a three-dimensional digital model. Using this model technician decides how many diamonds come out of the concrete stone and what form they will have. The focus is put the principle of combining the cost of future diamond and waste minimization. The program not only allows you to visualize the hidden diamonds in the diamond, but also give them the approximate cost. The classical form of cut KR-57 typically has a maximum value. Unfortunately, not every natural stone allows for precisely this form of making maximum use of raw materials.
The cost of the diamond placers 3560 dollars.
This stone will one diamond, but little more. Its cost will be a little less than three thousand dollars.
And this - two, but smaller and therefore more modest pocket.
Before leaving the site, the stones are glued to the special mandrel for subsequent processing. This small stands in an oven heated to glue firmly grabbed the diamonds.
With UZTTS stones fall on the cutting and stripping section. In the old days sawing stone performed mechanically by means of a bronze disk with a diamond-coated.
Today, the bulk of laser cutting is performed. The plant operator has the ability to visually monitor the process.
Laser cutting, firstly, the faster. Process according to sawing stone sizes can vary from five minutes to an hour. Secondly, the thickness of the laser cut is only 2 microns, which saves rough.
However, some of the stones having a high internal stress, laser cutting dangerous. Then the cutting is carried out in the old way - the bronze disk.
After the cutting of diamonds, each of which is packaged in a separate sheet, an envelope with a bar code, a list of all operations carried out with a stone, naming names of each of the workers, whose hands touch the stone, and other information is sent to the cutting and polishing sector. It is here that the diamond turns into a diamond.
The cut of the diamond is held on a rotating cast iron disc with a diamond coating. From scientific point of view, this process chemistry greater than physics. The surface of the diamond to graphite is oxidized and then formed oxidized film wears.
The diamond is fixed in the seat of a special hand tools - pliers.
With adjusting screws cutter changes the position of the stone in the collet, so that the diamond lay on the drive to the desired angle. So shapeless stone gains ground, facets and wedges.
It also happens that the stone falls out of the collet attachment. The rotary drive can send it to the "journey" on the site. Then he hears the command "loss" and an unlucky cutter goes in search of the diamond flown away. Despite the fact that each seat is equipped with a special cutter catchers stones, it happened that the search takes a very long time.
Generally, when the signal "loss" of all production into a "submarine", which, as we know, not going anywhere. Going beyond the area terminated at the time of the search of the lost stone. In the history of the work was considered definitively lost only one diamond. But he was found. Started out with a disc cutter stone "glued" to the wall, where he was discovered only a few years later.
After cutting and is not rinsing diamonds but diamonds portion fed to evaluation. Here, specially trained and certified professionals will appreciate the quality of the cut - color and defects of stone.
In assessing the cut stones are compared with these standards.
Color and defective stone - perhaps the decisive factors in its price. Price stones of similar weight and cut, but different colors may be different at times.
On site assessment of the diamond through another pantry, sent to distant lands - in Smolensk Gemological Centre. In Smolensk Diamonds receive a certificate and become a commodity. It may be legal to sell, donate, bequeath or simply "wither away" over it as Pushkin Koschey over with gold.
The cost of the diamonds - about one and a half million rubles.
All movements of the stones outside the shop carried convoys special communication. Inside the plant control the movement of the stones provides the security service department of economic security of the enterprise. Accounting stones arranged in such a way that even after many years, you can completely restore the history of each of them. Where was produced, how and by whom was bought for processing, when and who touched this stone, which manipulate them made where at a particular time the stone was during his stay at the plant.
Number of diamonds may find themselves. And each with its recorded history in detail.
Some polished to "Zvezdochka" diamonds are sent to Gokhran, adding gold and storage of the country. Others become luxuries. The last decrease in the jewelry production sites are located here in the shop.
Jewelry production technology is closely linked to the cut. Gold, silver, rings, earrings, rings, pendants ... Yes, yes. They also have with us.
Manufacturing production of jewelry begins with a stencil.
The special rubber molds of wax forms Worker "prototypes" for future rings or earrings details. From these pieces of wax is going to form the casting. Here it is called "Christmas Tree". On wax rod to one another as branches on a tree, glued blanks. Christmas tree wax collected is sent to the foundry sector. Here it is pour molding a mixture consisting essentially of plaster with special additives, and put a few hours into the oven. The mold - flask - hardens, the wax is melted out of it, leaving a blank space desired shape.
Forms for a piece of jewelry "custom" or new models are manufactured on a special milling machine. Here machine carves them out of wax on the busiest three-dimensional models. The customer has the ability to "feel" the product before it is executed in metal.
The next stage will be filled with plaster form of gold alloys. This alloy. The gold 999-carat dopants are introduced, leading him to a "commodity" 585-th sample.
This casting furnace everything happens.
Ship steel to the plant comes in sheets and gold jewelry - in kilogram ingots. In appearance - pure chocolate bar.
Cast - practical form for storage and transportation of gold bullion but to work with inconvenient. On this machine coming in gold jewelry manufacturing rolled strips in gold foil.
Later, when issuing the foil from the warehouse by weight with scissors cuts naveschik, in accordance with specific tasks on the production of jewelry.
The resulting cast - also "Tree", only this time the gold.
With this "Tree" bites the workpiece future jewelry.
Finished castings are monitored for integrity of casting, the presence of voids and defects. After this test phase fitters to clean and assemble blanks into finished products. Here on the decoration will consolidate diamonds.
Fitters working on the pallet. Gold dust, crumbs and scraps - they are called "saw cut" -sobirayutsya in special containers, separated by the color of the metal - white, yellow, red.
Once a month fitters melted the saw cut and after examination they come back into production.
So look transfused saw cut.
The examination is carried out here by means of cunning device «X-MET 7500". For professionals - a portable X-ray fluorescence energy dispersive spectrometry. The principle of its operation, we did not dare to find out, but the curious reader can easily naguglit necessary information. In the popular interpretation - this analyzer chemical composition of metal.
The device determines the purity of the gold composition of impurities in the metal. In this case, the transfused spilite contained gold and master alloy - copper, nickel, silver, zinc and tin.
Device, in spite of its compactness, very costly. It should be even more expensive than the above-mentioned diamond. At the root of the golden "Christmas tree", it is called "penny" or "heel", the fate of another. This is going to the bottom of the casting weight of impurities and dirt. Purification of the gold will be engaged already in the refinery.
On site assembly of the jewelry to fall Polisher.
Here they give the final gloss and sent to the warehouse. From there to the store.
Like diamonds, each diamond gold jewelry "travels" on the processing chain in a single package provided with a label with a bar code for tracing the entire history of a particular ring, tie clips or some other expensive trinkets.
This concludes the narrative. We hope you have been interesting. Thank deputy shop Olga Borovkov Alexey Kozhin and for the kindness with which we were received, and a fascinating story.
--img45--
Source: zvezdochka-ru.livejournal.com
Now we're ready to get acquainted with the shop. The first item on the itinerary - pantry raw materials.
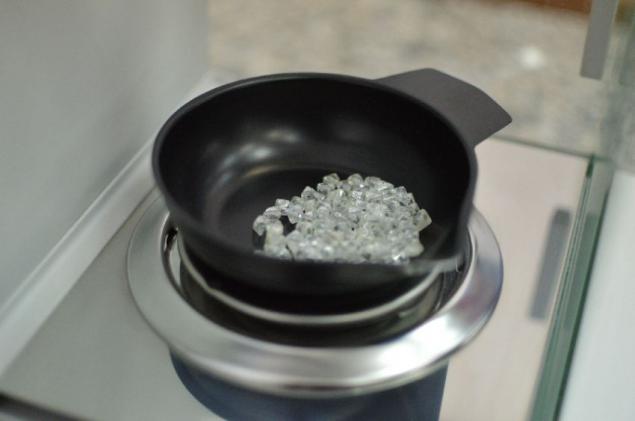
It arrives here raw materials - rough diamonds. Here they oprihoduyut: recalculate, weigh, check compliance with shipping documents, ENTERED every stone in an electronic database of records and discharged on each stone kind of road map. In this roadmap, folded in an envelope, diamond, and will travel to sites.

From the pantry diamond falls on UZTTS - section closed technological cycle. Here technology will sort and mark stones.
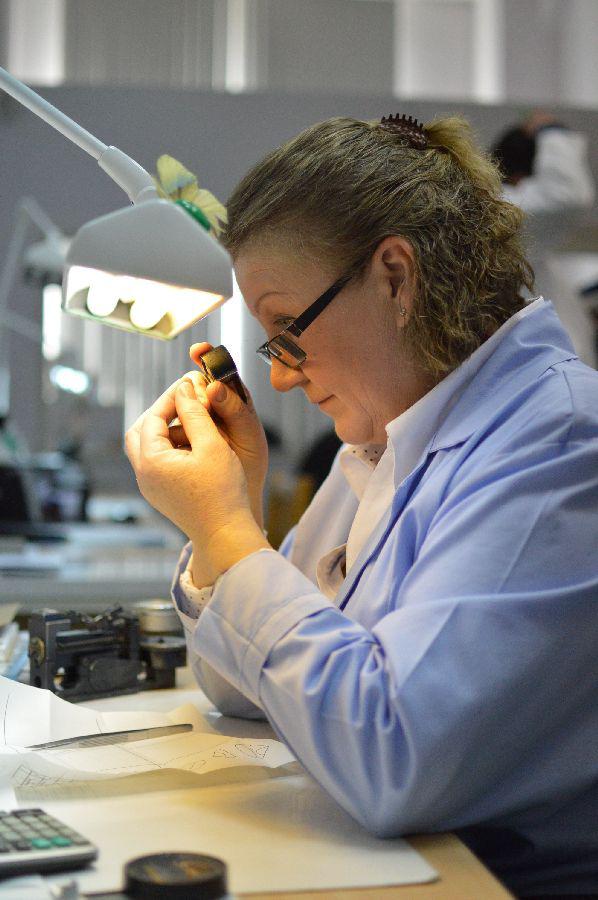
This is done by means of a computer markup. Installation of Diamond scans and creates a three-dimensional digital model. Using this model technician decides how many diamonds come out of the concrete stone and what form they will have. The focus is put the principle of combining the cost of future diamond and waste minimization. The program not only allows you to visualize the hidden diamonds in the diamond, but also give them the approximate cost. The classical form of cut KR-57 typically has a maximum value. Unfortunately, not every natural stone allows for precisely this form of making maximum use of raw materials.
The cost of the diamond placers 3560 dollars.
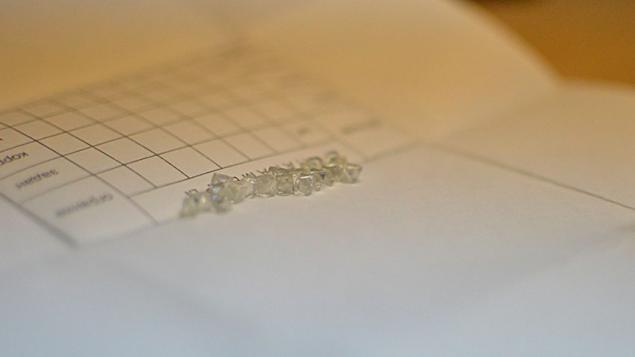
This stone will one diamond, but little more. Its cost will be a little less than three thousand dollars.
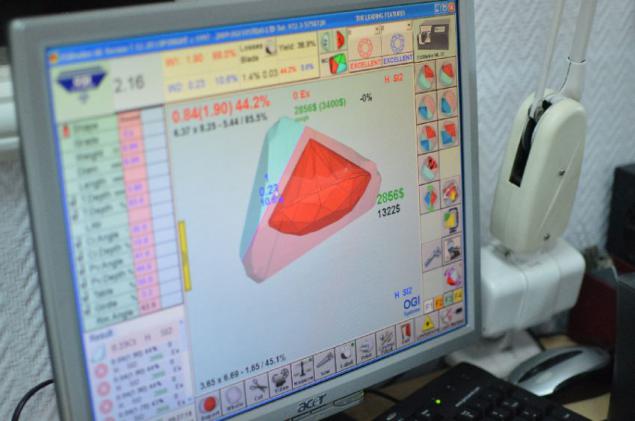
And this - two, but smaller and therefore more modest pocket.
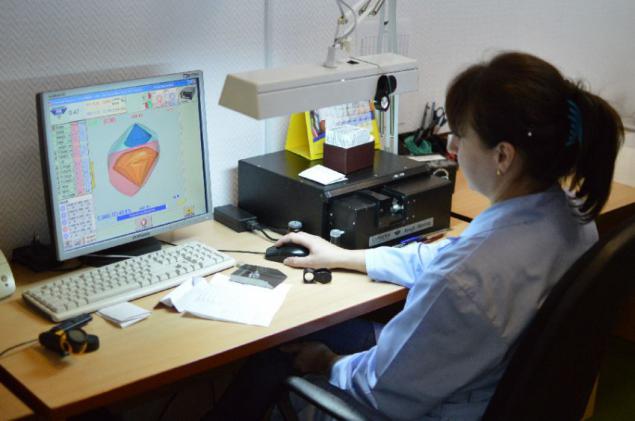
Before leaving the site, the stones are glued to the special mandrel for subsequent processing. This small stands in an oven heated to glue firmly grabbed the diamonds.
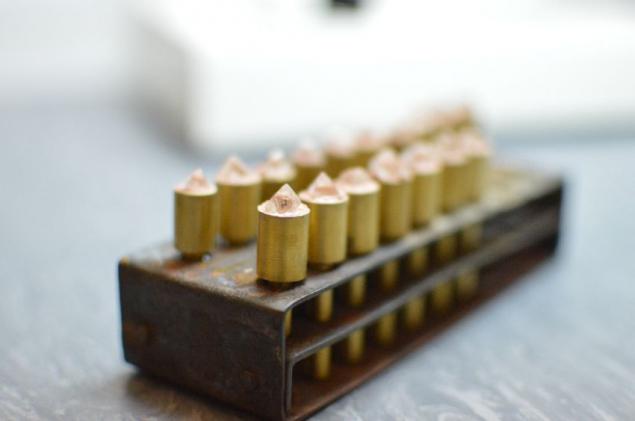
With UZTTS stones fall on the cutting and stripping section. In the old days sawing stone performed mechanically by means of a bronze disk with a diamond-coated.
Today, the bulk of laser cutting is performed. The plant operator has the ability to visually monitor the process.
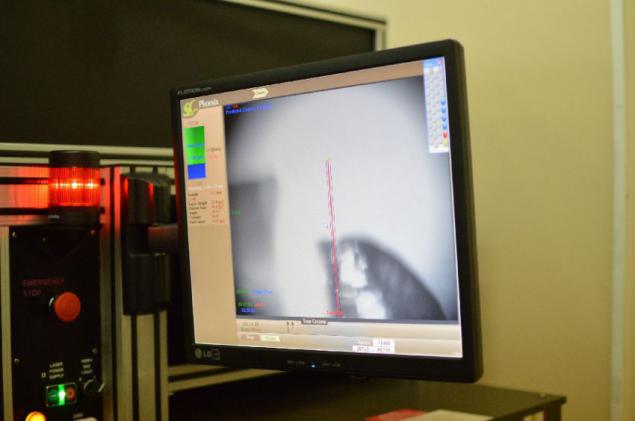
Laser cutting, firstly, the faster. Process according to sawing stone sizes can vary from five minutes to an hour. Secondly, the thickness of the laser cut is only 2 microns, which saves rough.
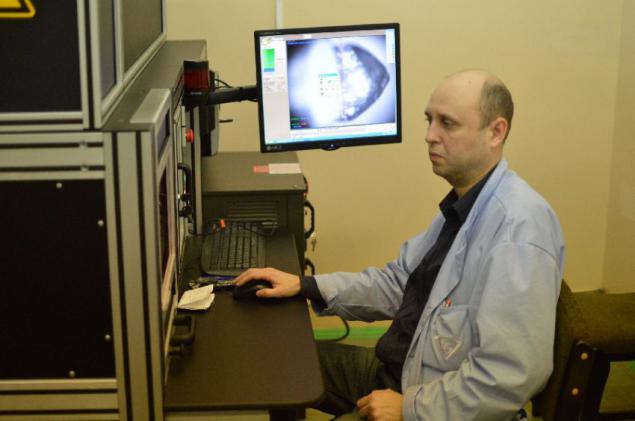
However, some of the stones having a high internal stress, laser cutting dangerous. Then the cutting is carried out in the old way - the bronze disk.
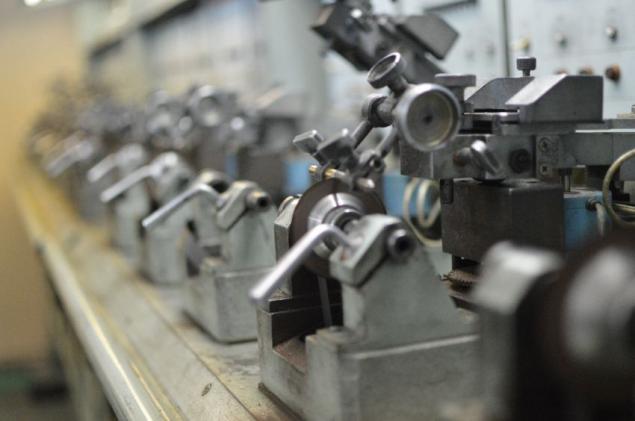
After the cutting of diamonds, each of which is packaged in a separate sheet, an envelope with a bar code, a list of all operations carried out with a stone, naming names of each of the workers, whose hands touch the stone, and other information is sent to the cutting and polishing sector. It is here that the diamond turns into a diamond.
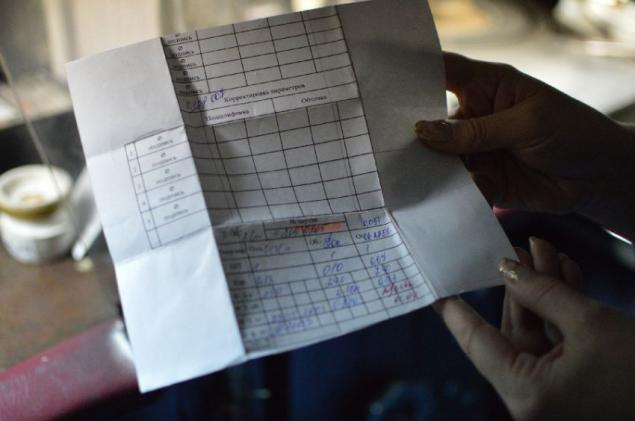
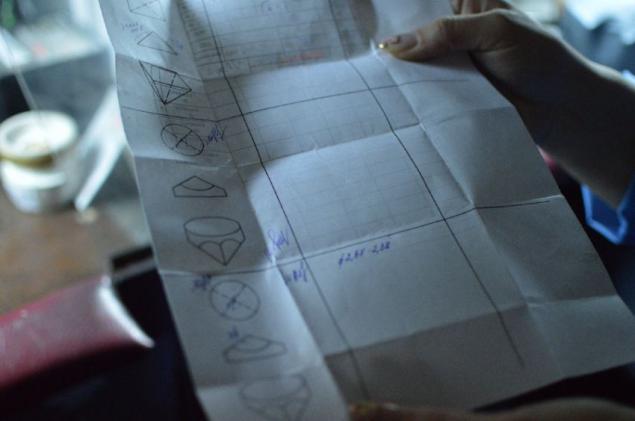
The cut of the diamond is held on a rotating cast iron disc with a diamond coating. From scientific point of view, this process chemistry greater than physics. The surface of the diamond to graphite is oxidized and then formed oxidized film wears.
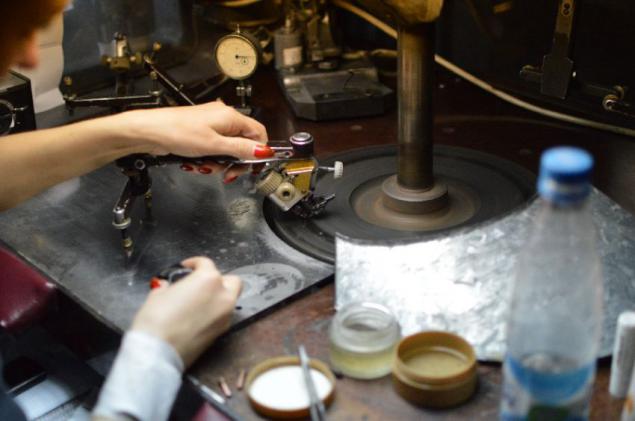
The diamond is fixed in the seat of a special hand tools - pliers.
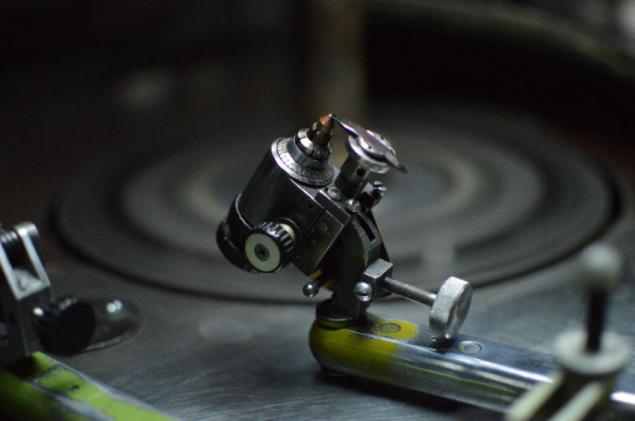
With adjusting screws cutter changes the position of the stone in the collet, so that the diamond lay on the drive to the desired angle. So shapeless stone gains ground, facets and wedges.
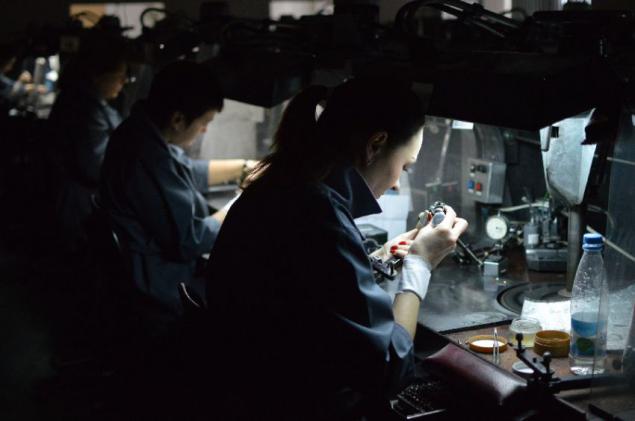
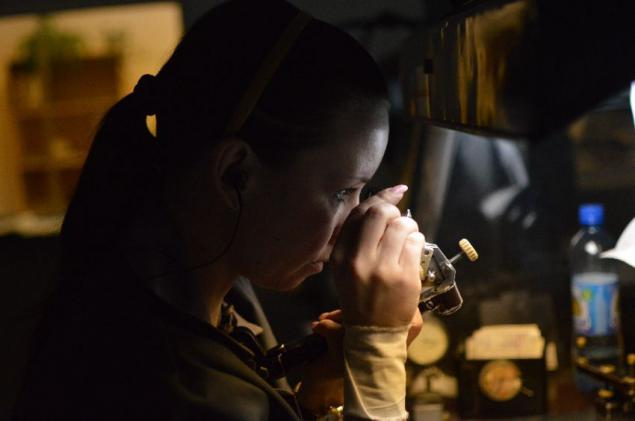
It also happens that the stone falls out of the collet attachment. The rotary drive can send it to the "journey" on the site. Then he hears the command "loss" and an unlucky cutter goes in search of the diamond flown away. Despite the fact that each seat is equipped with a special cutter catchers stones, it happened that the search takes a very long time.
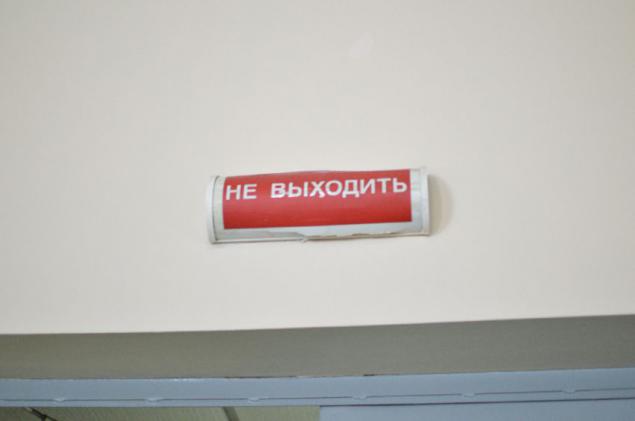
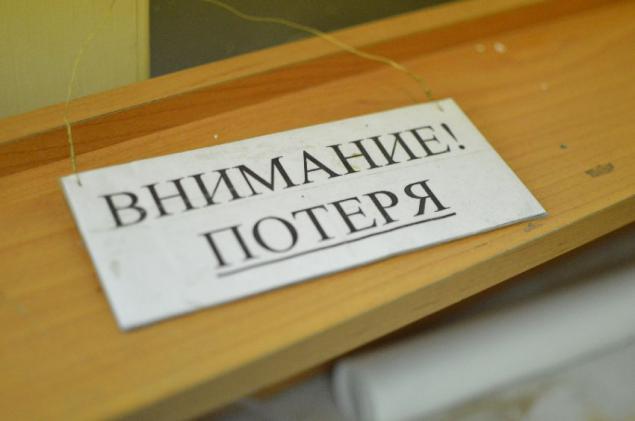
Generally, when the signal "loss" of all production into a "submarine", which, as we know, not going anywhere. Going beyond the area terminated at the time of the search of the lost stone. In the history of the work was considered definitively lost only one diamond. But he was found. Started out with a disc cutter stone "glued" to the wall, where he was discovered only a few years later.
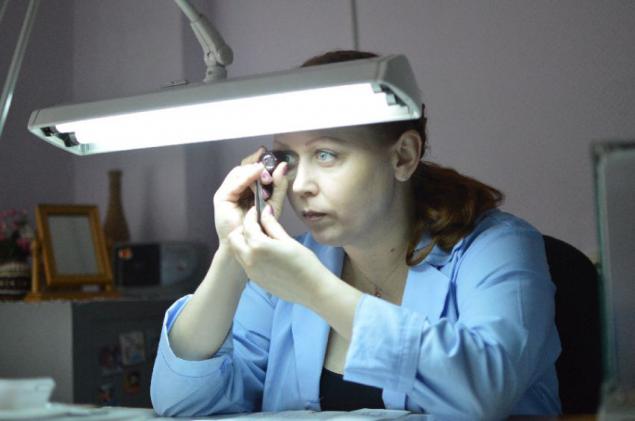
After cutting and is not rinsing diamonds but diamonds portion fed to evaluation. Here, specially trained and certified professionals will appreciate the quality of the cut - color and defects of stone.
In assessing the cut stones are compared with these standards.
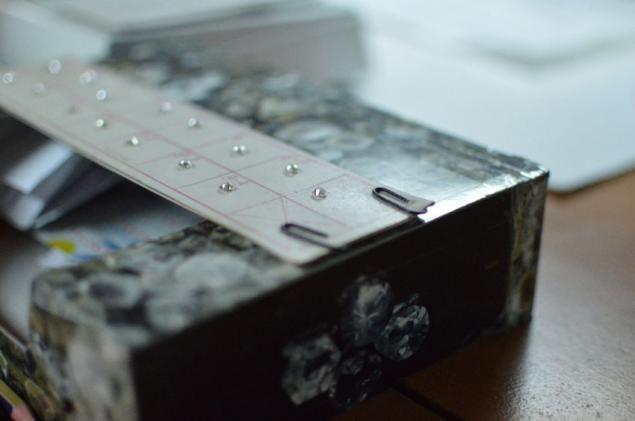
Color and defective stone - perhaps the decisive factors in its price. Price stones of similar weight and cut, but different colors may be different at times.
On site assessment of the diamond through another pantry, sent to distant lands - in Smolensk Gemological Centre. In Smolensk Diamonds receive a certificate and become a commodity. It may be legal to sell, donate, bequeath or simply "wither away" over it as Pushkin Koschey over with gold.
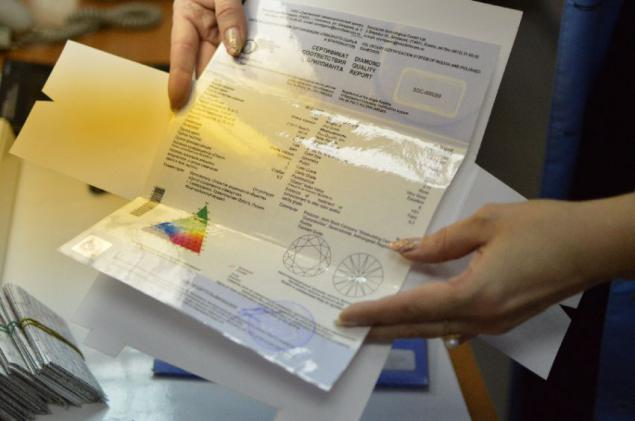
The cost of the diamonds - about one and a half million rubles.
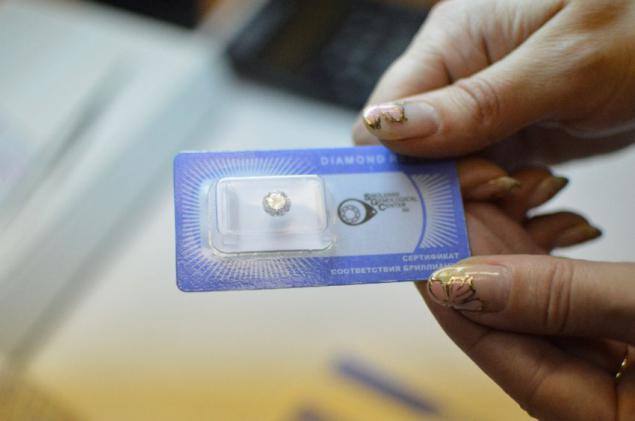
All movements of the stones outside the shop carried convoys special communication. Inside the plant control the movement of the stones provides the security service department of economic security of the enterprise. Accounting stones arranged in such a way that even after many years, you can completely restore the history of each of them. Where was produced, how and by whom was bought for processing, when and who touched this stone, which manipulate them made where at a particular time the stone was during his stay at the plant.
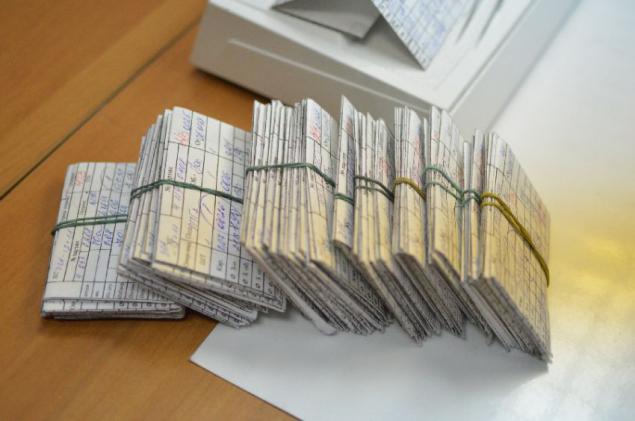
Number of diamonds may find themselves. And each with its recorded history in detail.
Some polished to "Zvezdochka" diamonds are sent to Gokhran, adding gold and storage of the country. Others become luxuries. The last decrease in the jewelry production sites are located here in the shop.
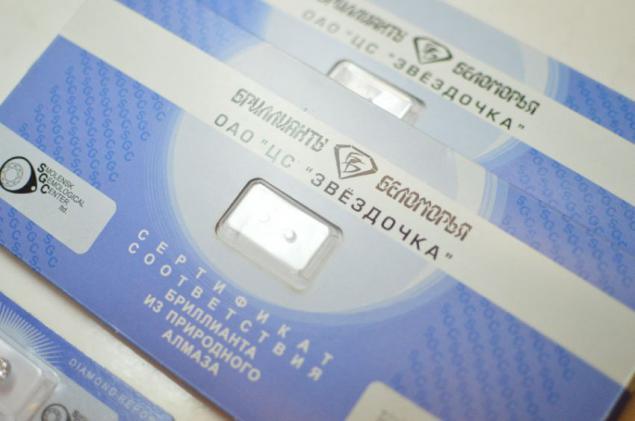
Jewelry production technology is closely linked to the cut. Gold, silver, rings, earrings, rings, pendants ... Yes, yes. They also have with us.
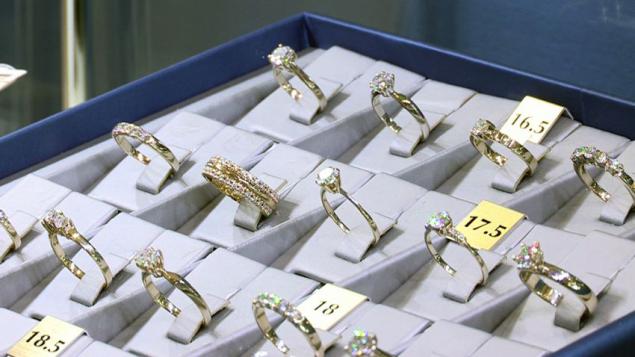
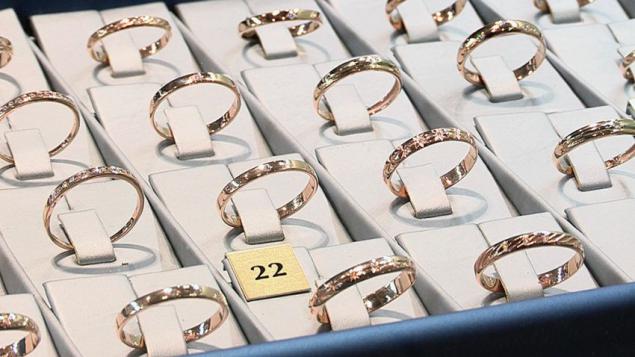
Manufacturing production of jewelry begins with a stencil.
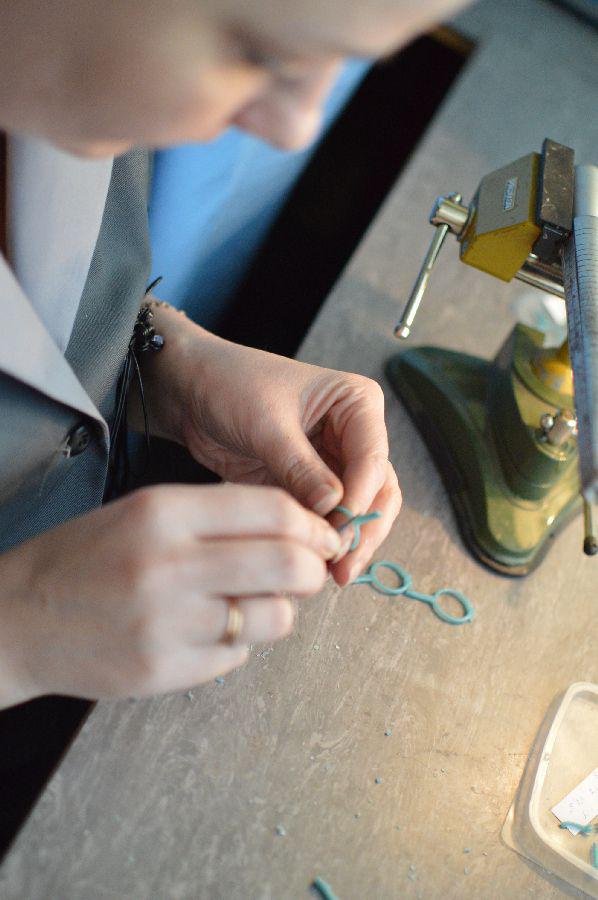
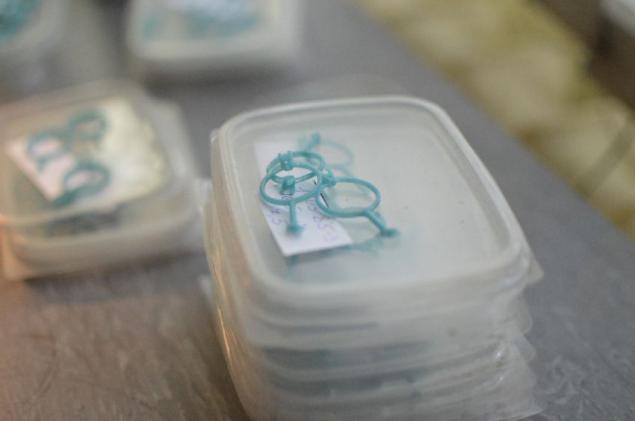
The special rubber molds of wax forms Worker "prototypes" for future rings or earrings details. From these pieces of wax is going to form the casting. Here it is called "Christmas Tree". On wax rod to one another as branches on a tree, glued blanks. Christmas tree wax collected is sent to the foundry sector. Here it is pour molding a mixture consisting essentially of plaster with special additives, and put a few hours into the oven. The mold - flask - hardens, the wax is melted out of it, leaving a blank space desired shape.
Forms for a piece of jewelry "custom" or new models are manufactured on a special milling machine. Here machine carves them out of wax on the busiest three-dimensional models. The customer has the ability to "feel" the product before it is executed in metal.
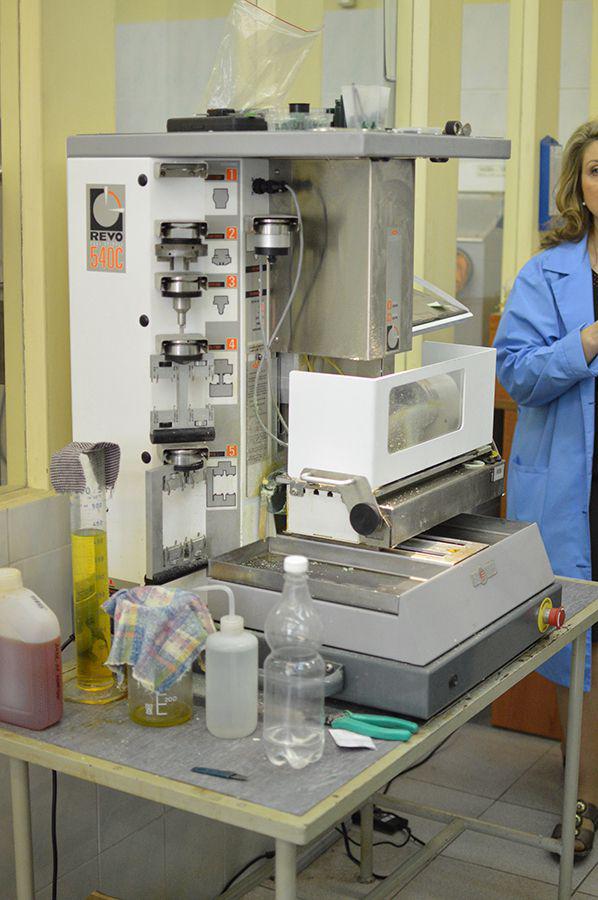
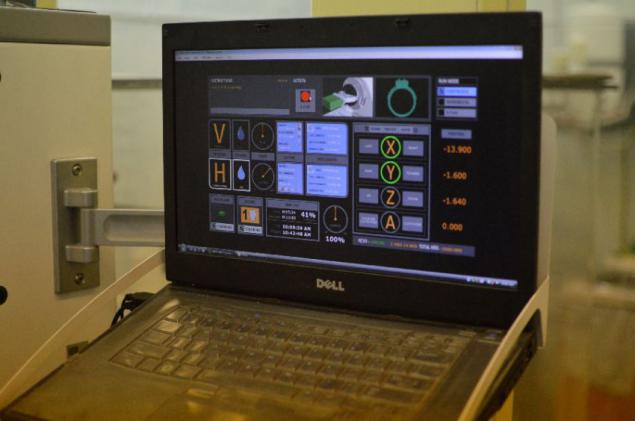
The next stage will be filled with plaster form of gold alloys. This alloy. The gold 999-carat dopants are introduced, leading him to a "commodity" 585-th sample.
This casting furnace everything happens.
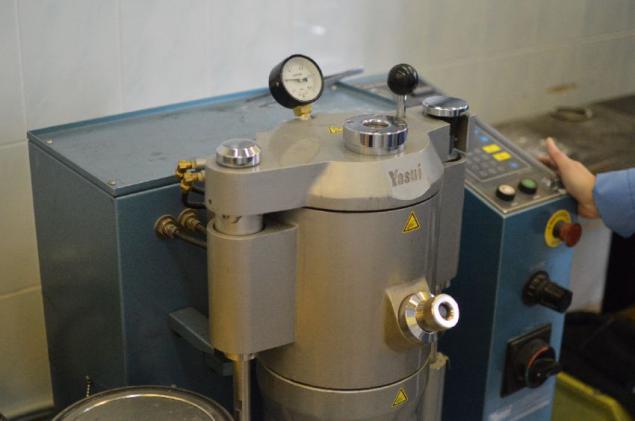
Ship steel to the plant comes in sheets and gold jewelry - in kilogram ingots. In appearance - pure chocolate bar.
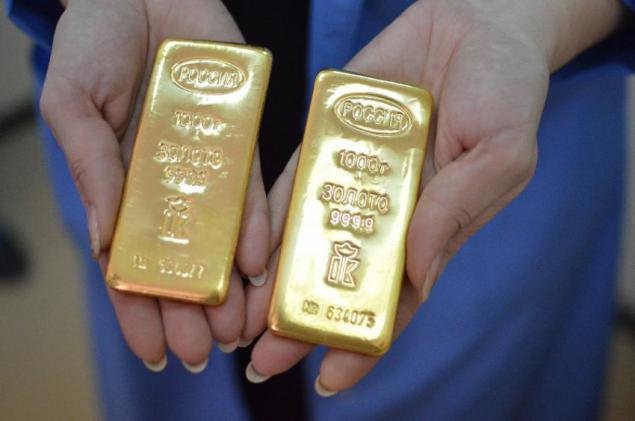
Cast - practical form for storage and transportation of gold bullion but to work with inconvenient. On this machine coming in gold jewelry manufacturing rolled strips in gold foil.
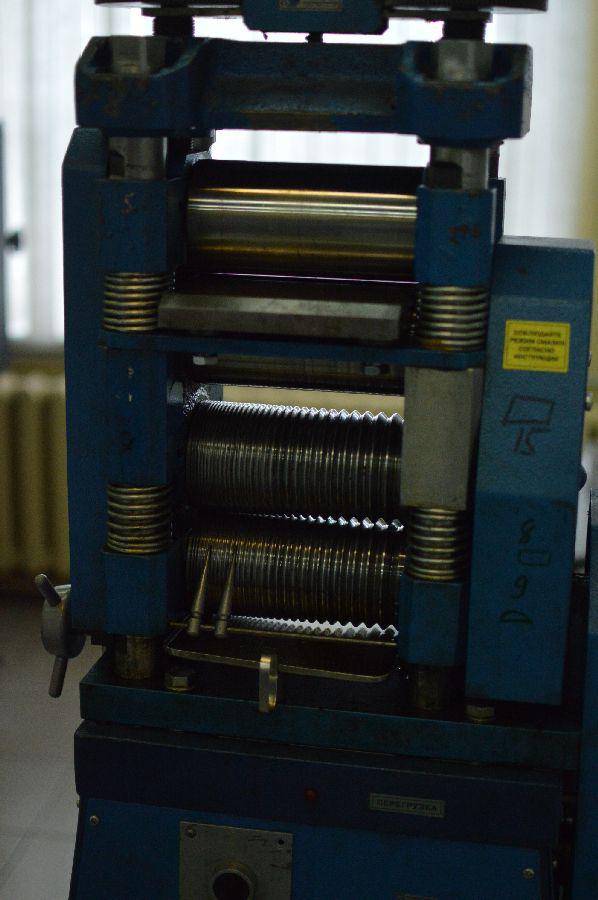
Later, when issuing the foil from the warehouse by weight with scissors cuts naveschik, in accordance with specific tasks on the production of jewelry.
The resulting cast - also "Tree", only this time the gold.
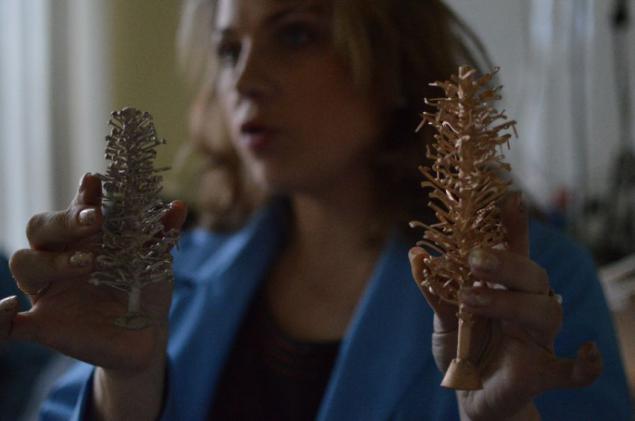
With this "Tree" bites the workpiece future jewelry.
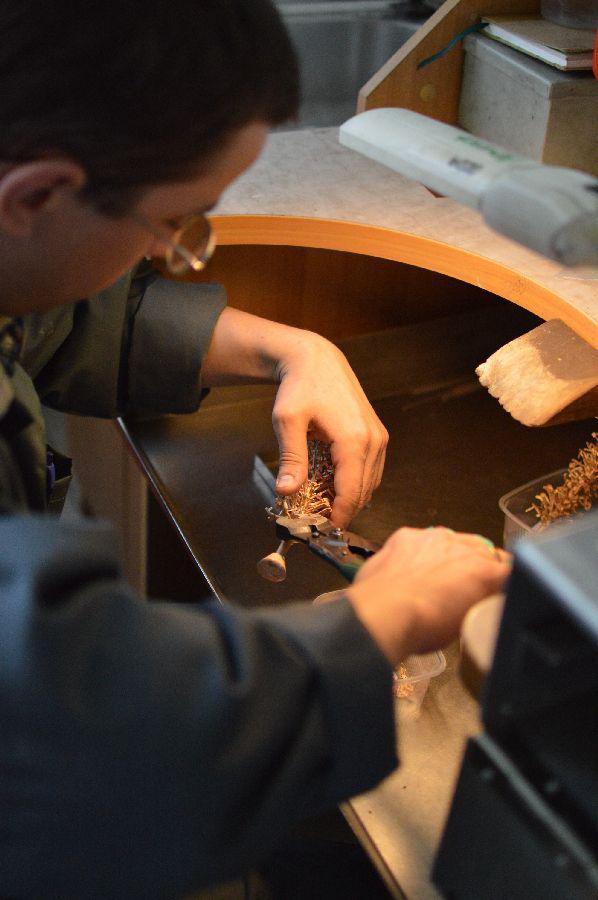
Finished castings are monitored for integrity of casting, the presence of voids and defects. After this test phase fitters to clean and assemble blanks into finished products. Here on the decoration will consolidate diamonds.
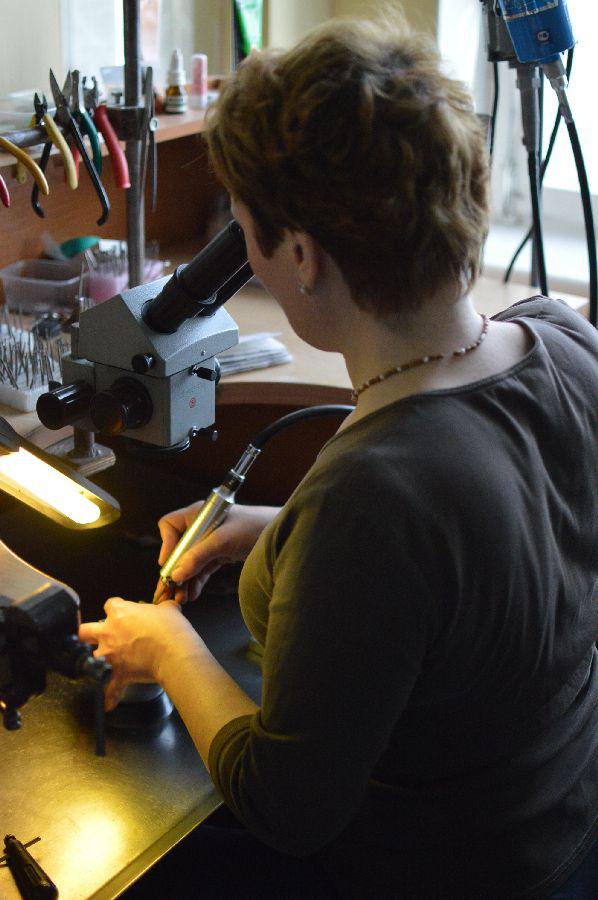
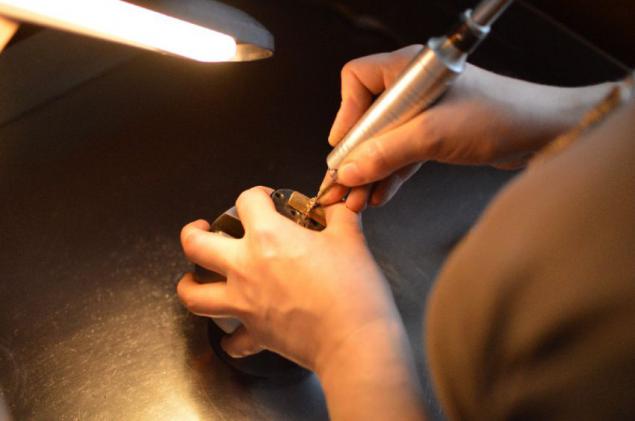
Fitters working on the pallet. Gold dust, crumbs and scraps - they are called "saw cut" -sobirayutsya in special containers, separated by the color of the metal - white, yellow, red.
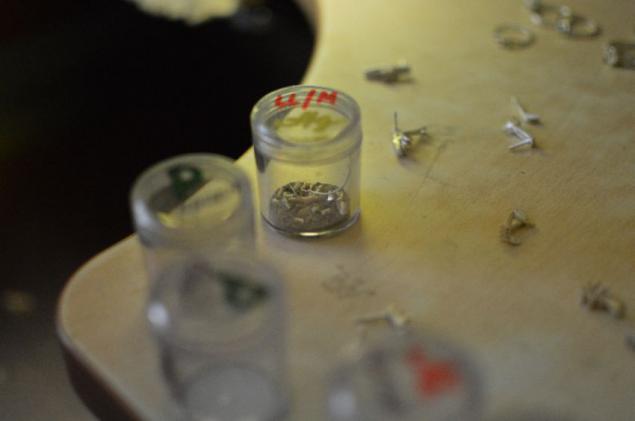
Once a month fitters melted the saw cut and after examination they come back into production.
So look transfused saw cut.
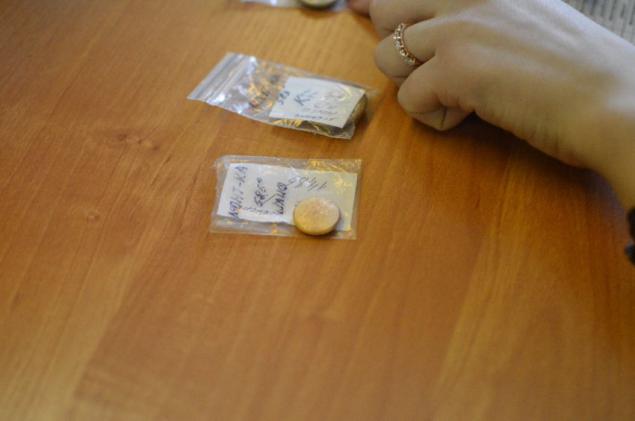
The examination is carried out here by means of cunning device «X-MET 7500". For professionals - a portable X-ray fluorescence energy dispersive spectrometry. The principle of its operation, we did not dare to find out, but the curious reader can easily naguglit necessary information. In the popular interpretation - this analyzer chemical composition of metal.
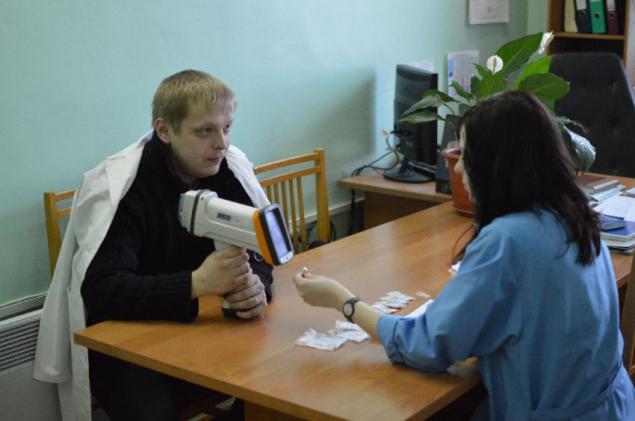
The device determines the purity of the gold composition of impurities in the metal. In this case, the transfused spilite contained gold and master alloy - copper, nickel, silver, zinc and tin.
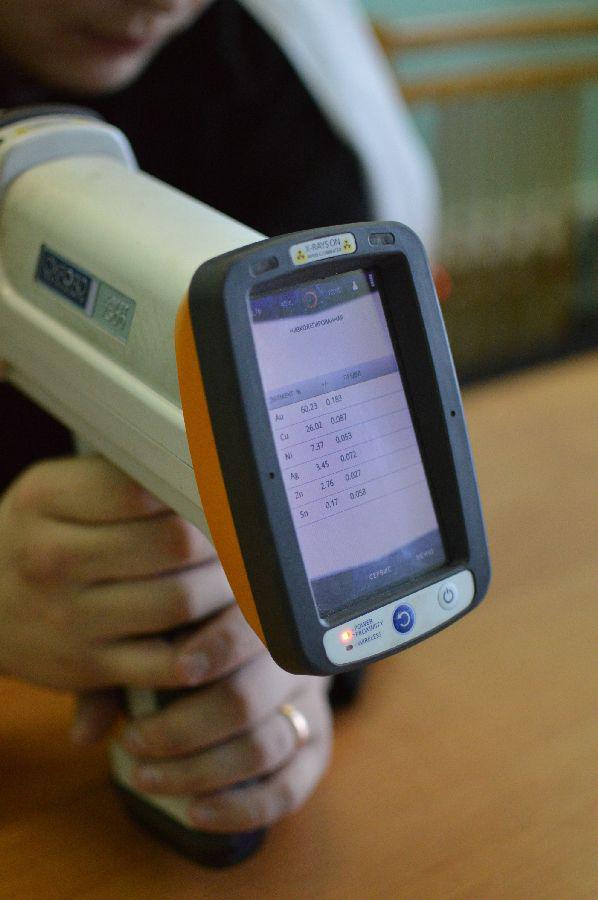
Device, in spite of its compactness, very costly. It should be even more expensive than the above-mentioned diamond. At the root of the golden "Christmas tree", it is called "penny" or "heel", the fate of another. This is going to the bottom of the casting weight of impurities and dirt. Purification of the gold will be engaged already in the refinery.
On site assembly of the jewelry to fall Polisher.
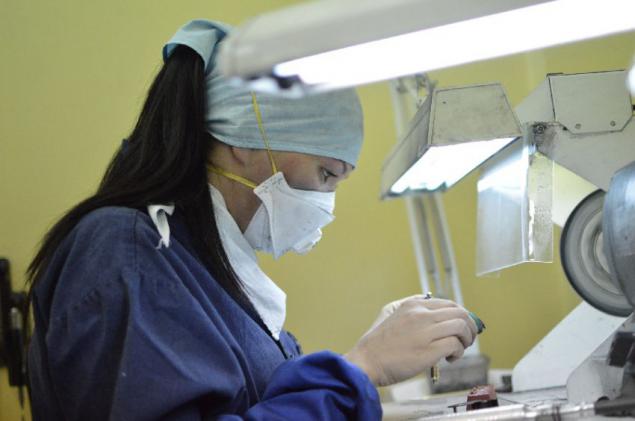
Here they give the final gloss and sent to the warehouse. From there to the store.
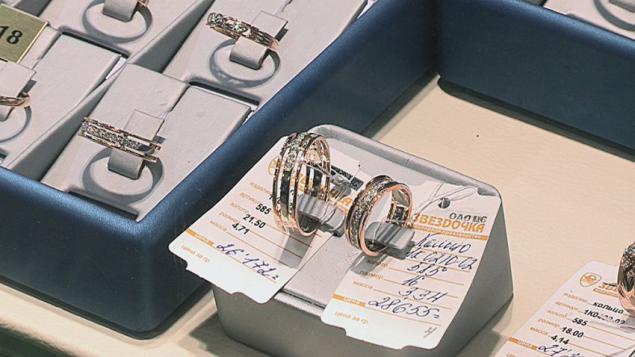
Like diamonds, each diamond gold jewelry "travels" on the processing chain in a single package provided with a label with a bar code for tracing the entire history of a particular ring, tie clips or some other expensive trinkets.
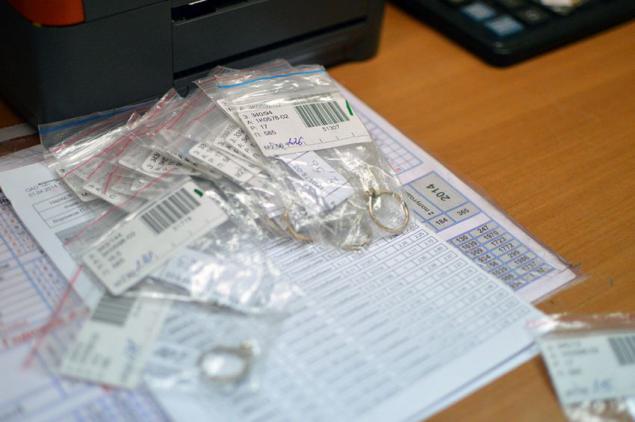
This concludes the narrative. We hope you have been interesting. Thank deputy shop Olga Borovkov Alexey Kozhin and for the kindness with which we were received, and a fascinating story.
--img45--
Source: zvezdochka-ru.livejournal.com