888
Space technologies for aviation
On the eve of the Day of Cosmonautics leading enterprise holding "PT Himkompozit" CVTs "Technology" held a press tour for media representatives to acquaint the public with the most significant completed projects for the production of composite products and glass products for the aerospace, aviation and life.
Enterprises established on the basis of two institutions: the technical branch of glass and VIAM soon celebrate 55 years since the 70s it has been developing in the space sector.
Walk on the production and see how they do it.
The main task of the holding company - the development of technology and the supply of serial designs from polymeric composite materials (PCM).
To ship "Buran" for the first time the country has made large payload bay doors of SMP with a total length of 18 meters. Until now, "Buran" is considered to be the quintessence of the latest achievements of domestic space industry.
Of the 100 tonnes of the total weight of the ship 10 tons - products produced on "Technology". Among these 10% were ultra-light heat-shielding tiles, high-strength glazed cockpit, large structures made of composite materials, and more.
2. At the entrance to the company are composite samples portions "Buran" (payload bay leaf) and the PAK FA (center section).
3. Go to the manufacturing facility for the production of composite structures.
4. It produces tooling design and tooling for composite materials.
5. The company is involved in two major projects related to the aircraft. It is the creation of our future aircraft MS21 (Obninsk responsible for the development of technology and production of integrated stringer panels caissons stabilizer fin and tail with improved load-carrying capacity) and engine to it - PD-14.
6. Processing panel of the gas generator for advanced engine PD-14 ("Perm Motors"), which will be installed on MS21.
7. Preparation for the second row of the panel of the gas generator.
Layers - Cabin, honeycomb paneling, etc.
Sheathing made from domestic materials, developed in VIAM.
8. prepregs - semi-finished composite material, carbon fiber, or on the basis of glass fiber impregnated with a special binder
9. Ready-panel prototype engine, which will go to trial.
Results will be produced about 12 experimental engines. After the test results to make decisions on the use of the serial.
Prepared casing, it is installed on a given item and the program comes machining. The surfaces of double curvature on the five-axis machines are processed.
10. Final machining sash reversing device PD-14 engine.
11.Ustanovka automated tape laying prepreg for composite structures was launched in 1985 and until last year was the only unit in Russia. The second came last year in Ulyanovsk. Two years ago, it was a complete modernization of the old installation guides remained, desks, and basic mechanical part of the portal. Mechanics, drive, software - everything is new.
12. unidirectional tape prepregs with Western products layer by layer butt puts on the table the pattern for future details.
13. For more complex components require manual layout, followed by autoclave molding.
14. The unit provides preset angles for computation products, process prikladki and seals for the given values, the complexity is reduced at times.
15. Installation spreads cladding portion made thereafter specialized stringer together snap-mounted on, and goes into the autoclave at a pressure of 7 atmospheres and a temperature of about 180 turns of finished part rise 7 meters and a weight of 50 kg.
16. One and a half weeks spent on the production of a stringer panel. After that, the details go to "Aviastar", which is a collector tail MS21, and from there everything goes to Irkutsk for the final assembly of the aircraft.
17. There is also produced parts of the wing panels for the Su-47 "Berkut" (the one with forward-swept wing). The set of 8 meters in length, the thickness at the edge of the more than 20 mm, the number of layers - about a hundred.
18. We go to other parts of the enterprise.
19. Build a three-layer honeycomb panels to heat the spacecraft takes place in a clean room in which strict requirements for temperature, humidity, dust.
20. These panels reduce energomassovye characteristics, increase the service life of up to 15 years and from proceeds of the design documentation to the manufacture of the product takes place 3 months.
21. In orbit at the moment there are about 27 satellites with elements Obninsk «Technology».
22. At the date of design carcass weight of 480 grams / square meter and in the future, this weight will be reduced. In this respect, we are not only going on a par with the leading Western firms, but even ahead of them.
23. Production of large skins for nose cones of missiles type "Proton", "Rokot", "Angara", 10-12 sets per year, we deliver to the Khrunichev Center. The manufacture of such structures - oversized cowls are engaged in a number of countries in the world.
24. Large Cabin placed on snap, rolled adhesive film is superimposed honeycomb, again adhesive film laid paneling and goes into the autoclave in the final gluing.
25. Some of the details are so complex that they require the intervention of human hands.
26. For bonding temperature of the autoclave required 175 degrees. At a certain speed mode and all assigned seven. Stitch mode lasts three hours.
27. Go to the "finished product warehouse».
28. fairing "Proton" has a total height of about 16 meters, diameter of 4350 a total weight of slightly more than a ton. Because metal is the same design would weigh more than two tons.
29. Due to the constant modernization and weight reduction fairings increased weight satellites. Simple "Proton" before brings to the transitional orbit satellites weighing 4, 5 tons. Now - more than 6 tons. For commercial launches of "Proton" ranks first in the world
30. In the project "Sea Launch» (Sea-lounch) fairing used by Boeing for missiles worth $ 9 million, our weight is not only equal, but on the contrary ahead of West and is almost two times less - about 4 million.
31. The holding producing 28 units of the wing and fuselage of the RMB to the multipurpose fighter T-50 (PAK FA), but to show them to the public can not.
32. Holding has unique experience in glass processing and producing of glass.
To protect aircrew from the harmful effects of external factors developed glazed with multifunctional nanoscale coating for new combat aircraft.
33. Vacuum unit for deposition of nanostructured multifunctional coating. Sterile room with several degrees of purity control.
Loading Zone. Preventing from pieces of organic matter (for example, has fallen off to evaporation.)
34.
35. Preparation for the installation of glass designs before placing the spray unit.
36. Although the thickness of the coating about 80-90 nm, it reduces the electromagnetic radiation is 250 times, to reduce radar visibility at 40-60%.
37. Filters, quartz glass.
38. Glazing for some trains also make and test here.
39. The results of the dynamic tests glazing impact.
40. Hall of tests launcher PU132-based anti-aircraft gun carriage was born in 1954 with a modern filling.
41. PU132 (where 132 - the inner diameter of the barrel) can throw stones, metal bars, ice balls at a rate of 100 to 1900 km / h. There are vandal-proof test, in which the fire bottle. If the speed of a small object is charged with the direction of the muzzle.
42. But the main throwing object - a bird. And it is not simple, but with a passport. Flyer comes with a special factory.
Depending on the type of glass and helicopter-type aircraft, train set speed and selected carcass weight (typically 1 kg).
From a single control room behind a thick glass special person made a shot.
43. The cabin of the helicopter Ka-62 with a trace pound bird strike.
44. The tested model aircraft cabin windows in the back yard. And about a given last week's issue, see otgadku here.
In 2013, the company made:
- More than 70 panels and thermal solar panels for carcases of 11 satellites.
- By now in Earth orbit successfully operates 27 satellites, which included a production of "CVTs" Technology ".
- Manufactured and shipped shell nose cones, transfer compartment 3rd stage gargrot 1st, 2nd and 3rd stages, local fairings Motor 3-Tier:
• 10 carrier rockets "Proton-M"
• 1st rocket "Angara 5"
• 2 carrier rockets "Angara 1.2".
At the end of 2013 was successfully launched a fundamentally new carrier rocket "Soyuz 2.1V" to the block elimination "Volga", which included applied thermal control system of the new generation created on the basis of our panels. This launch was launched into Earth orbit research satellite "Stork" ultra-light carbon-fiber panels with solar panels and satellite body, made, again in Obninsk.
Source: fotografersha.livejournal.com
Enterprises established on the basis of two institutions: the technical branch of glass and VIAM soon celebrate 55 years since the 70s it has been developing in the space sector.
Walk on the production and see how they do it.
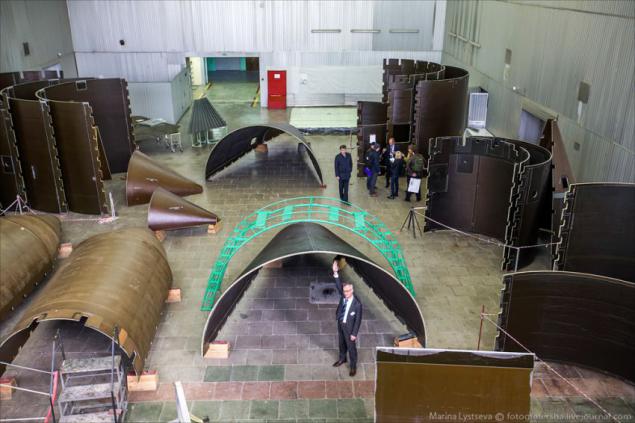
The main task of the holding company - the development of technology and the supply of serial designs from polymeric composite materials (PCM).
To ship "Buran" for the first time the country has made large payload bay doors of SMP with a total length of 18 meters. Until now, "Buran" is considered to be the quintessence of the latest achievements of domestic space industry.
Of the 100 tonnes of the total weight of the ship 10 tons - products produced on "Technology". Among these 10% were ultra-light heat-shielding tiles, high-strength glazed cockpit, large structures made of composite materials, and more.
2. At the entrance to the company are composite samples portions "Buran" (payload bay leaf) and the PAK FA (center section).
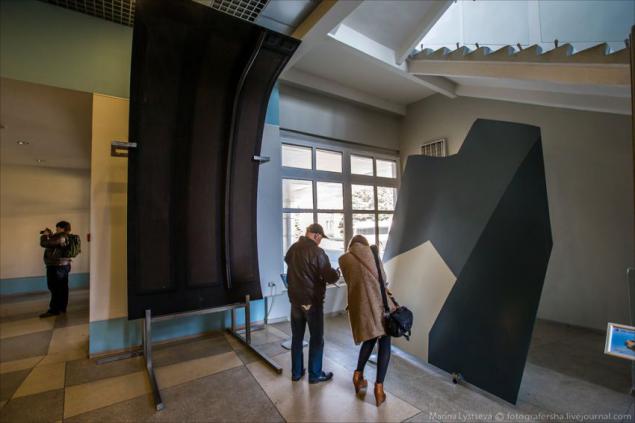
3. Go to the manufacturing facility for the production of composite structures.
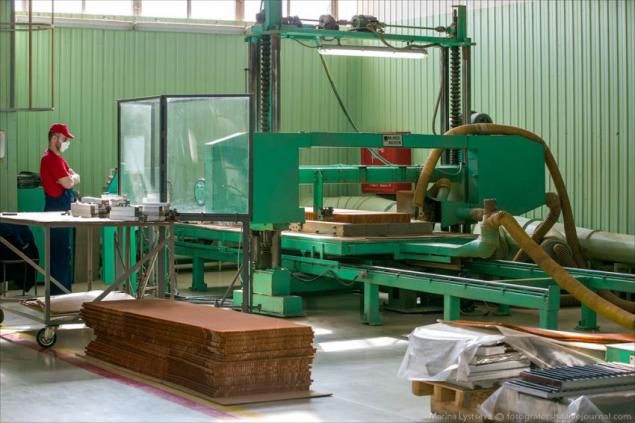
4. It produces tooling design and tooling for composite materials.
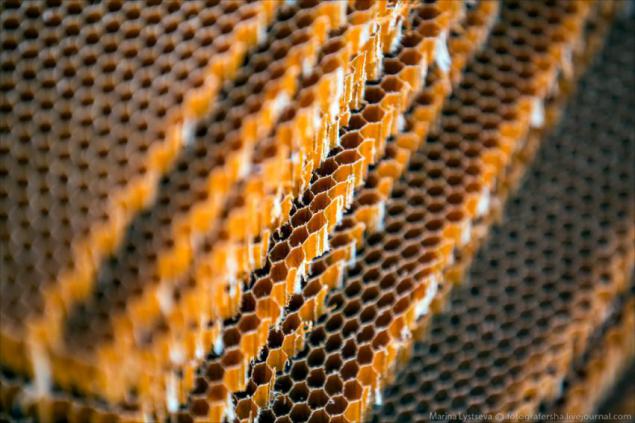
5. The company is involved in two major projects related to the aircraft. It is the creation of our future aircraft MS21 (Obninsk responsible for the development of technology and production of integrated stringer panels caissons stabilizer fin and tail with improved load-carrying capacity) and engine to it - PD-14.
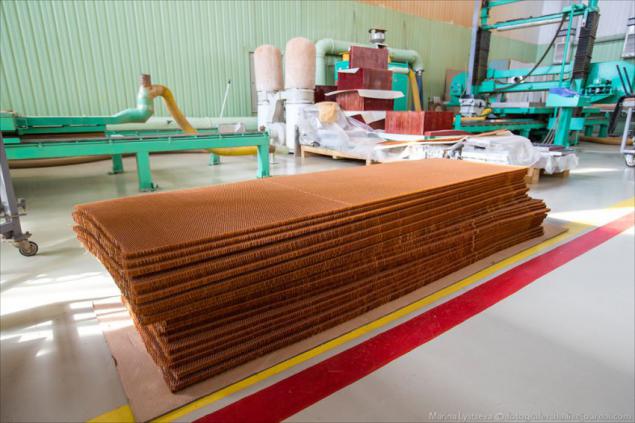
6. Processing panel of the gas generator for advanced engine PD-14 ("Perm Motors"), which will be installed on MS21.
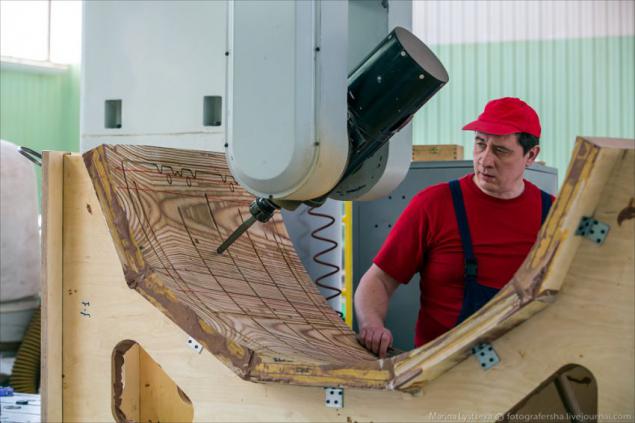
7. Preparation for the second row of the panel of the gas generator.
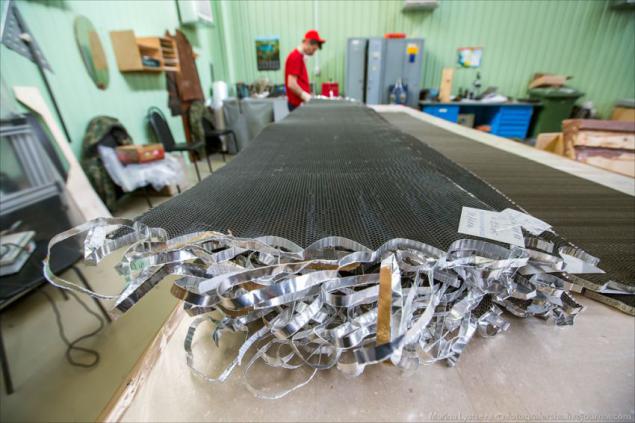
Layers - Cabin, honeycomb paneling, etc.
Sheathing made from domestic materials, developed in VIAM.
8. prepregs - semi-finished composite material, carbon fiber, or on the basis of glass fiber impregnated with a special binder
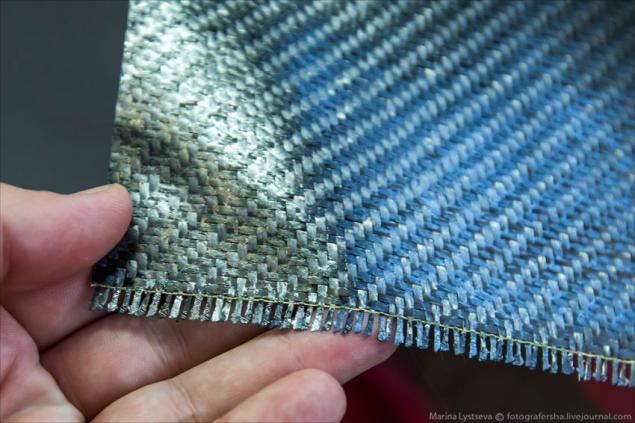
9. Ready-panel prototype engine, which will go to trial.
Results will be produced about 12 experimental engines. After the test results to make decisions on the use of the serial.
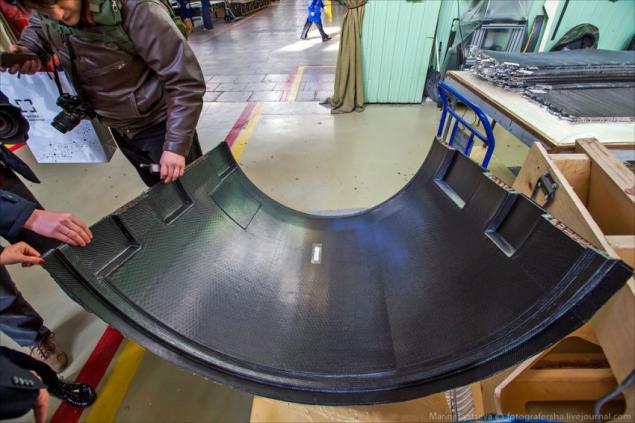
Prepared casing, it is installed on a given item and the program comes machining. The surfaces of double curvature on the five-axis machines are processed.
10. Final machining sash reversing device PD-14 engine.
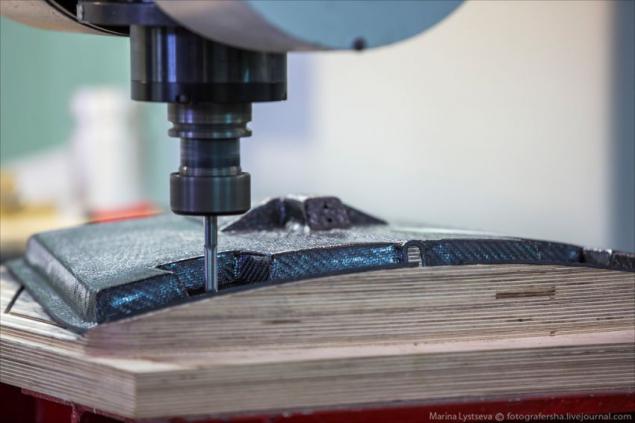
11.Ustanovka automated tape laying prepreg for composite structures was launched in 1985 and until last year was the only unit in Russia. The second came last year in Ulyanovsk. Two years ago, it was a complete modernization of the old installation guides remained, desks, and basic mechanical part of the portal. Mechanics, drive, software - everything is new.
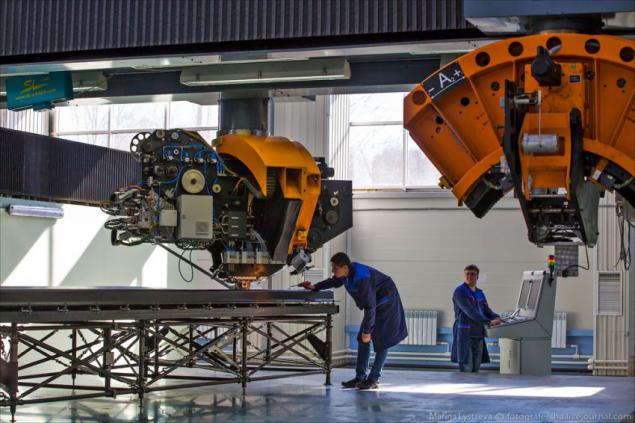
12. unidirectional tape prepregs with Western products layer by layer butt puts on the table the pattern for future details.
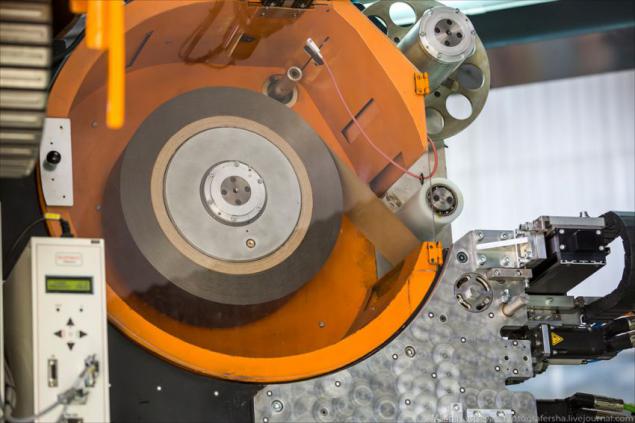
13. For more complex components require manual layout, followed by autoclave molding.
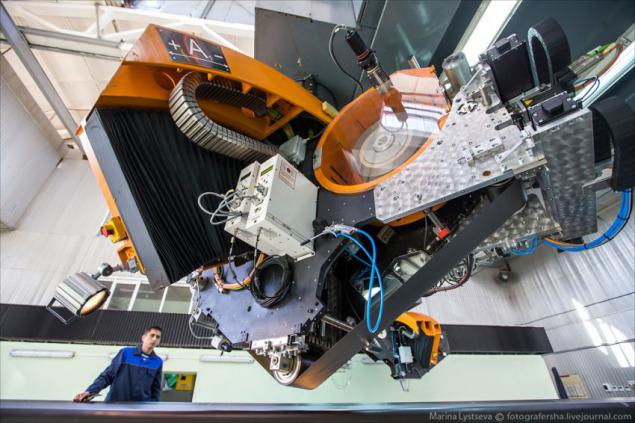
14. The unit provides preset angles for computation products, process prikladki and seals for the given values, the complexity is reduced at times.
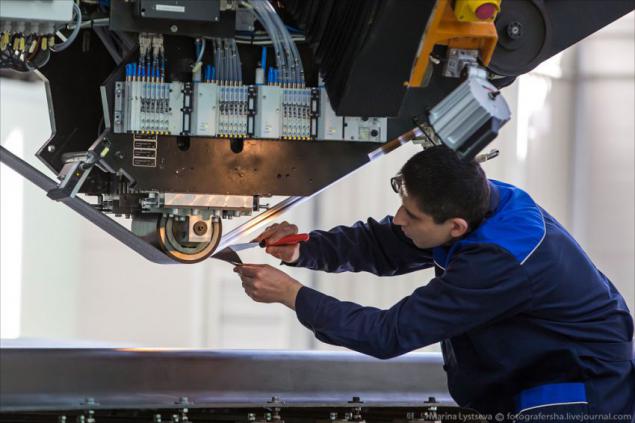
15. Installation spreads cladding portion made thereafter specialized stringer together snap-mounted on, and goes into the autoclave at a pressure of 7 atmospheres and a temperature of about 180 turns of finished part rise 7 meters and a weight of 50 kg.
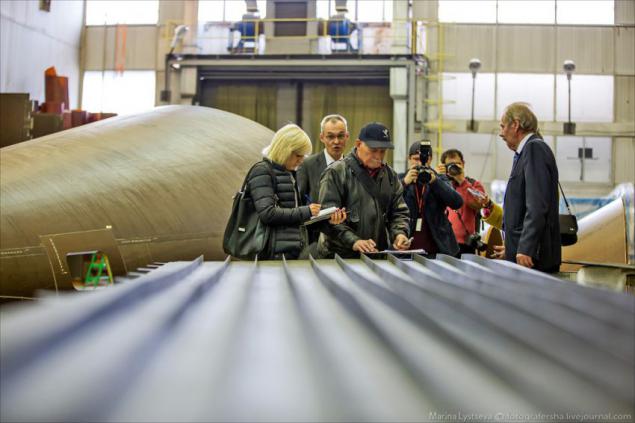
16. One and a half weeks spent on the production of a stringer panel. After that, the details go to "Aviastar", which is a collector tail MS21, and from there everything goes to Irkutsk for the final assembly of the aircraft.
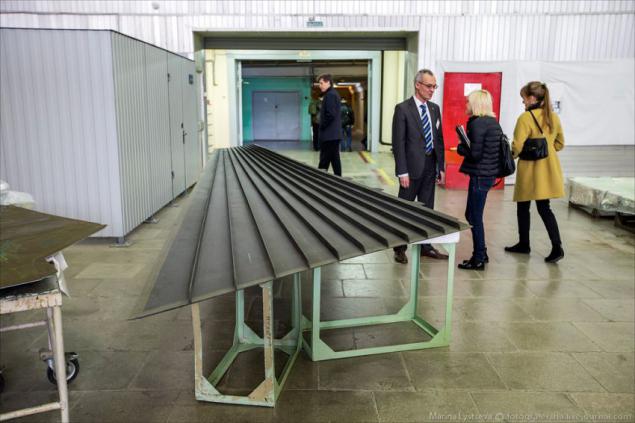
17. There is also produced parts of the wing panels for the Su-47 "Berkut" (the one with forward-swept wing). The set of 8 meters in length, the thickness at the edge of the more than 20 mm, the number of layers - about a hundred.
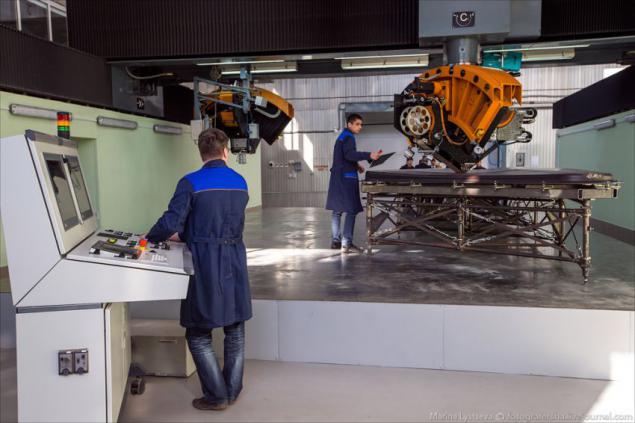
18. We go to other parts of the enterprise.
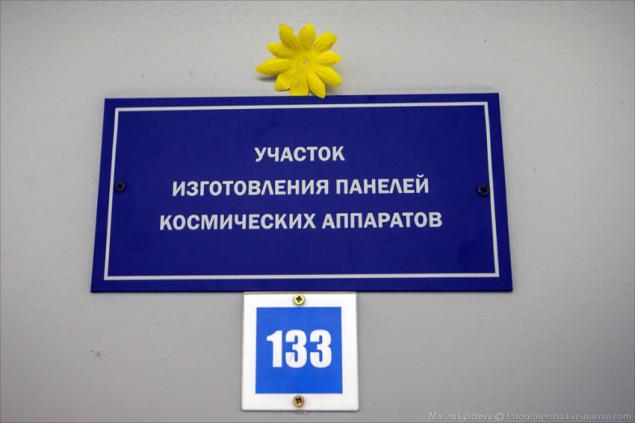
19. Build a three-layer honeycomb panels to heat the spacecraft takes place in a clean room in which strict requirements for temperature, humidity, dust.
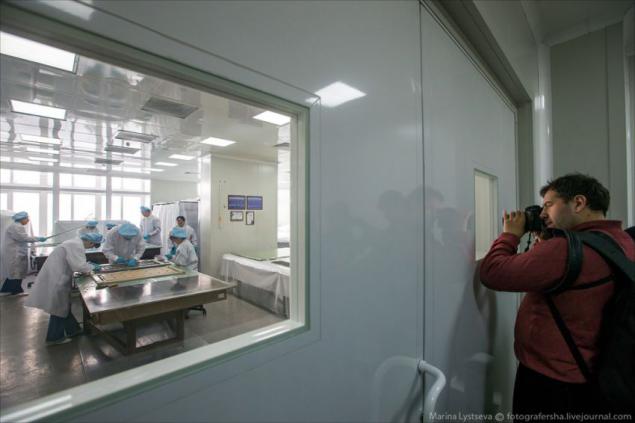
20. These panels reduce energomassovye characteristics, increase the service life of up to 15 years and from proceeds of the design documentation to the manufacture of the product takes place 3 months.
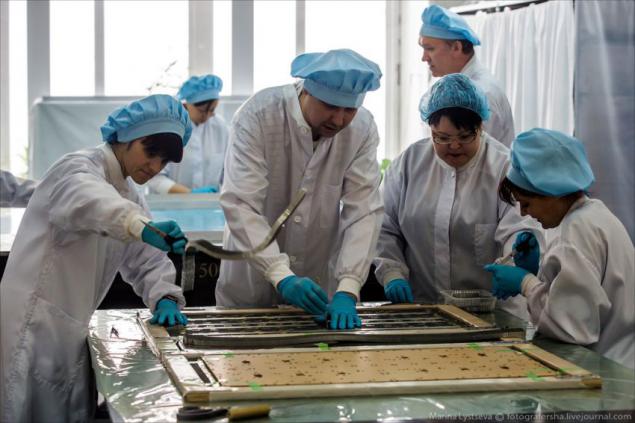
21. In orbit at the moment there are about 27 satellites with elements Obninsk «Technology».
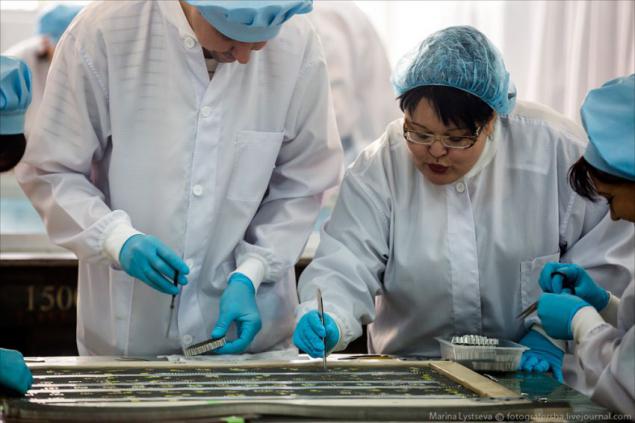
22. At the date of design carcass weight of 480 grams / square meter and in the future, this weight will be reduced. In this respect, we are not only going on a par with the leading Western firms, but even ahead of them.
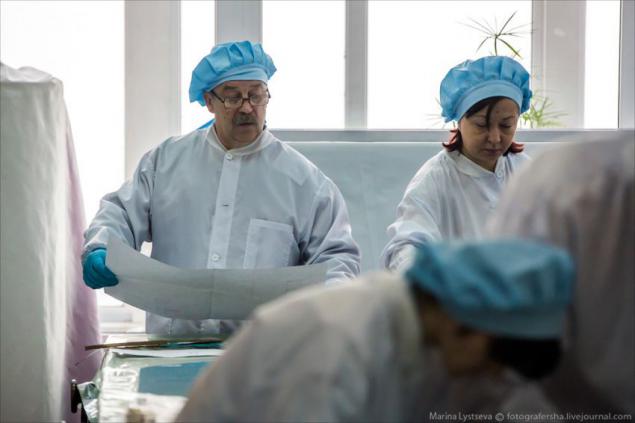
23. Production of large skins for nose cones of missiles type "Proton", "Rokot", "Angara", 10-12 sets per year, we deliver to the Khrunichev Center. The manufacture of such structures - oversized cowls are engaged in a number of countries in the world.
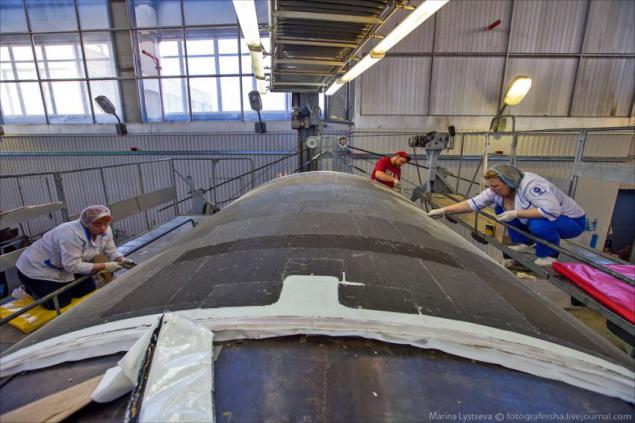
24. Large Cabin placed on snap, rolled adhesive film is superimposed honeycomb, again adhesive film laid paneling and goes into the autoclave in the final gluing.
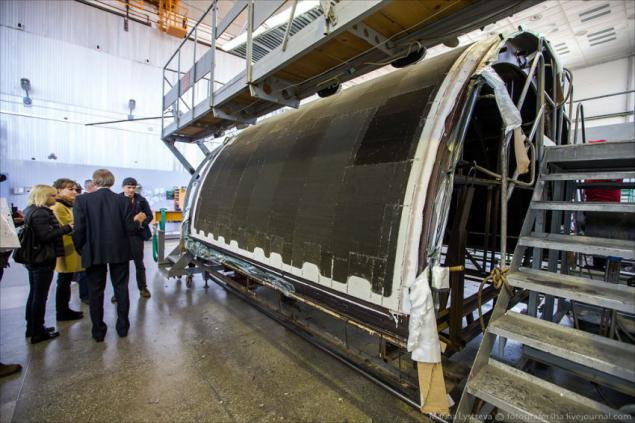
25. Some of the details are so complex that they require the intervention of human hands.
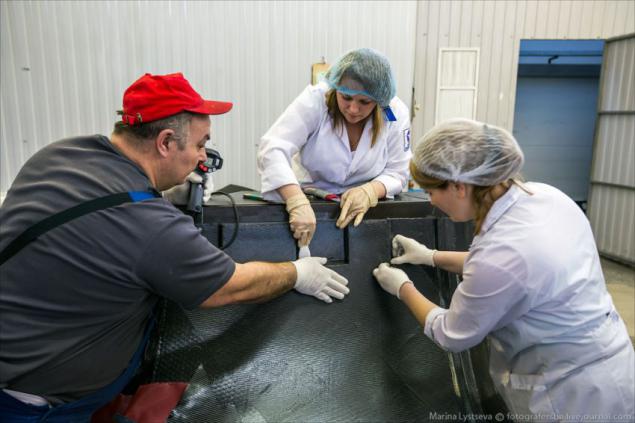
26. For bonding temperature of the autoclave required 175 degrees. At a certain speed mode and all assigned seven. Stitch mode lasts three hours.
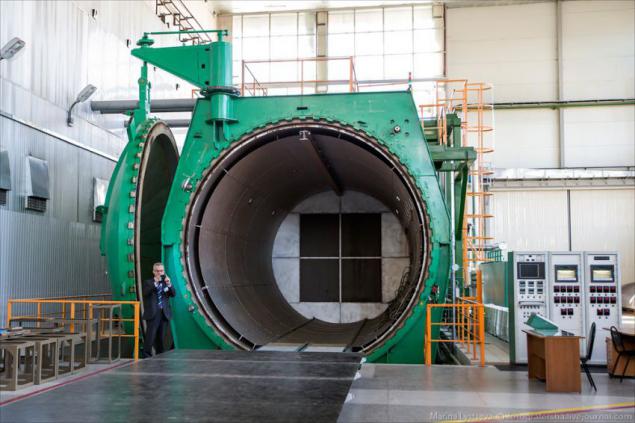
27. Go to the "finished product warehouse».
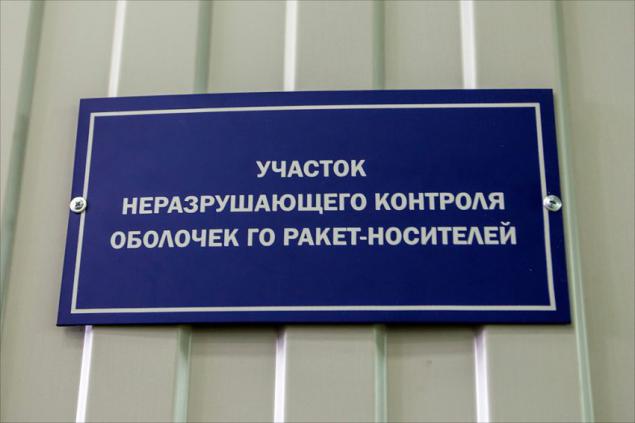
28. fairing "Proton" has a total height of about 16 meters, diameter of 4350 a total weight of slightly more than a ton. Because metal is the same design would weigh more than two tons.

29. Due to the constant modernization and weight reduction fairings increased weight satellites. Simple "Proton" before brings to the transitional orbit satellites weighing 4, 5 tons. Now - more than 6 tons. For commercial launches of "Proton" ranks first in the world
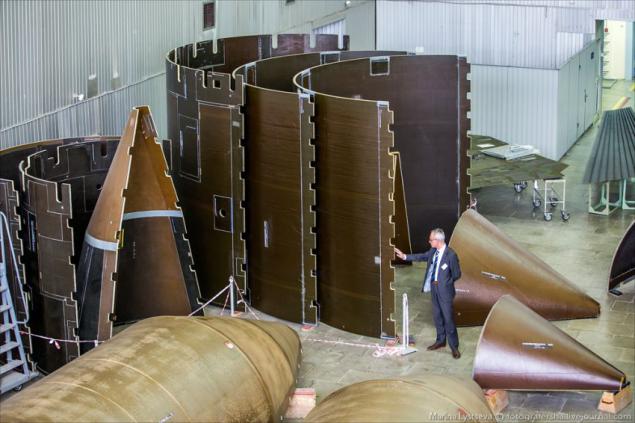
30. In the project "Sea Launch» (Sea-lounch) fairing used by Boeing for missiles worth $ 9 million, our weight is not only equal, but on the contrary ahead of West and is almost two times less - about 4 million.
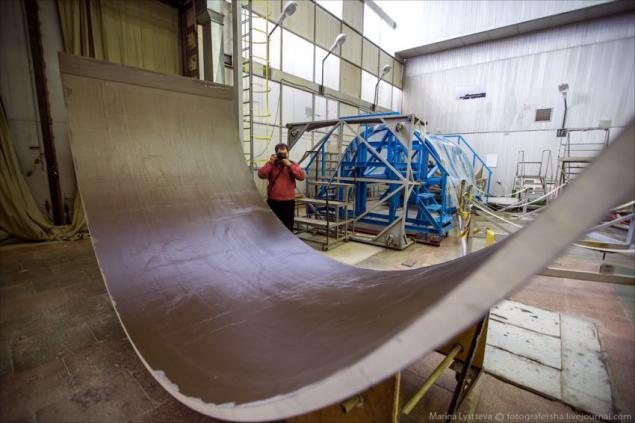
31. The holding producing 28 units of the wing and fuselage of the RMB to the multipurpose fighter T-50 (PAK FA), but to show them to the public can not.
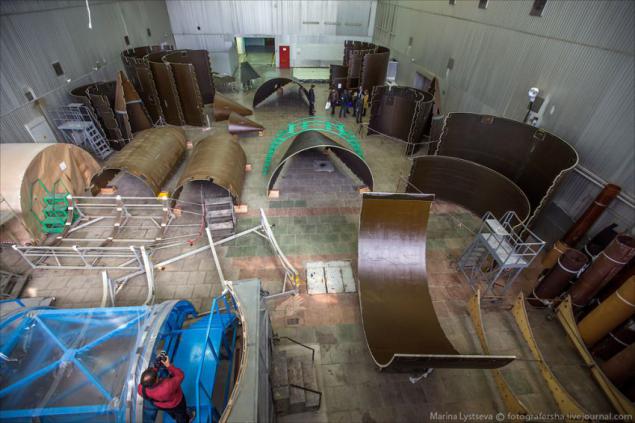
32. Holding has unique experience in glass processing and producing of glass.
To protect aircrew from the harmful effects of external factors developed glazed with multifunctional nanoscale coating for new combat aircraft.
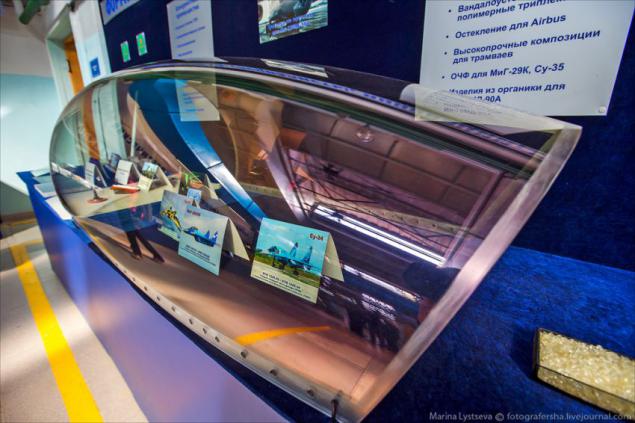
33. Vacuum unit for deposition of nanostructured multifunctional coating. Sterile room with several degrees of purity control.
Loading Zone. Preventing from pieces of organic matter (for example, has fallen off to evaporation.)
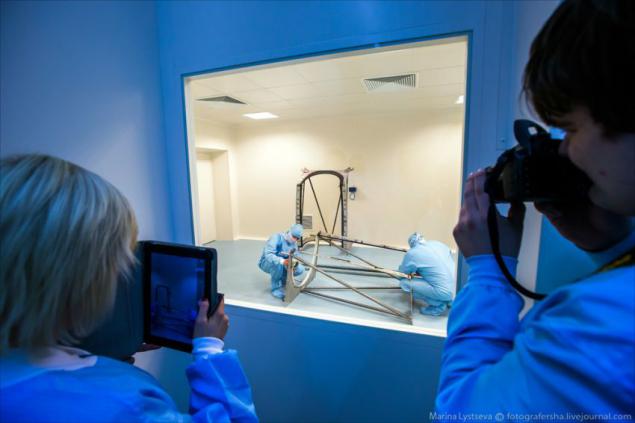
34.
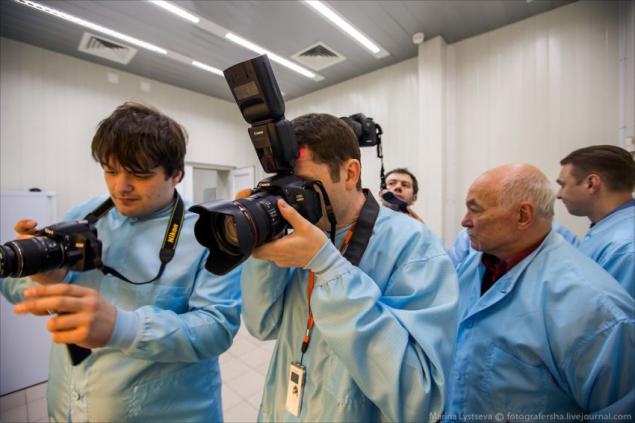
35. Preparation for the installation of glass designs before placing the spray unit.
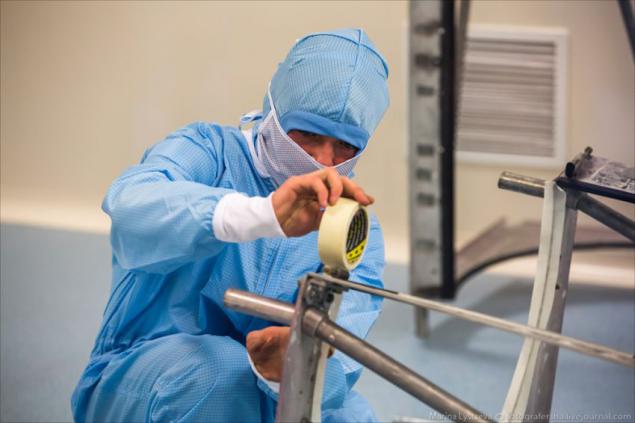
36. Although the thickness of the coating about 80-90 nm, it reduces the electromagnetic radiation is 250 times, to reduce radar visibility at 40-60%.
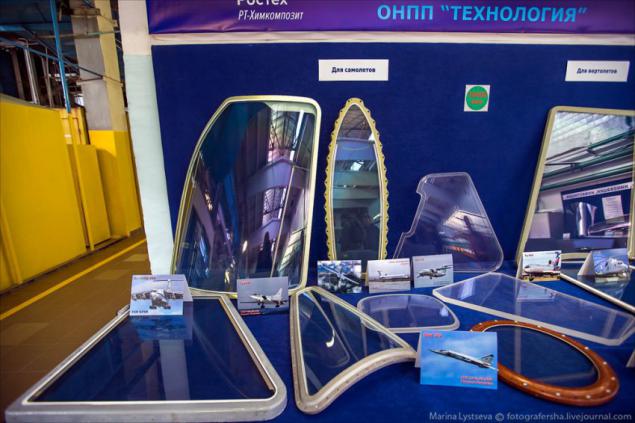
37. Filters, quartz glass.
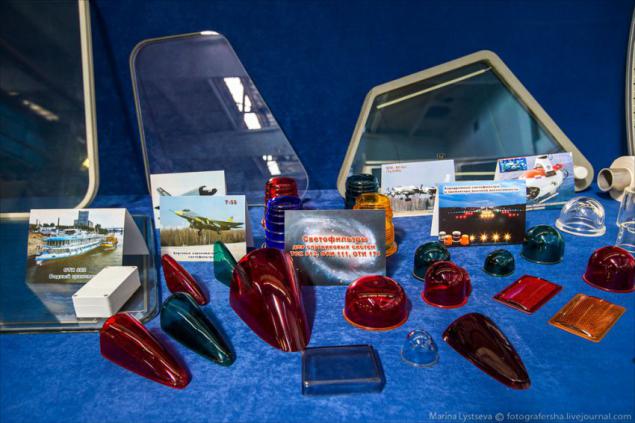
38. Glazing for some trains also make and test here.
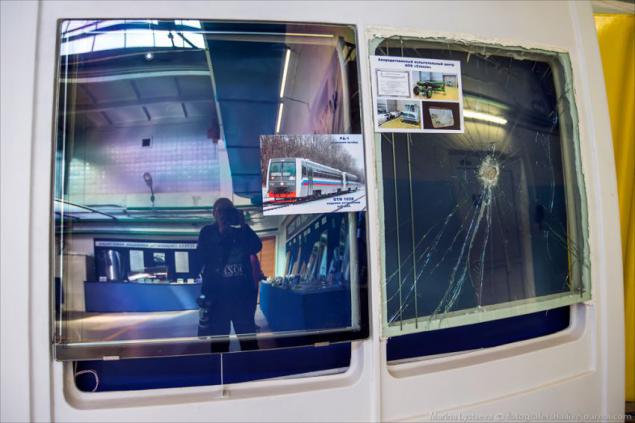
39. The results of the dynamic tests glazing impact.
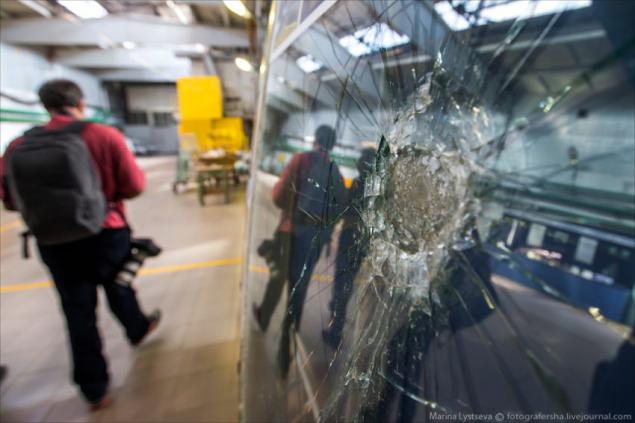
40. Hall of tests launcher PU132-based anti-aircraft gun carriage was born in 1954 with a modern filling.
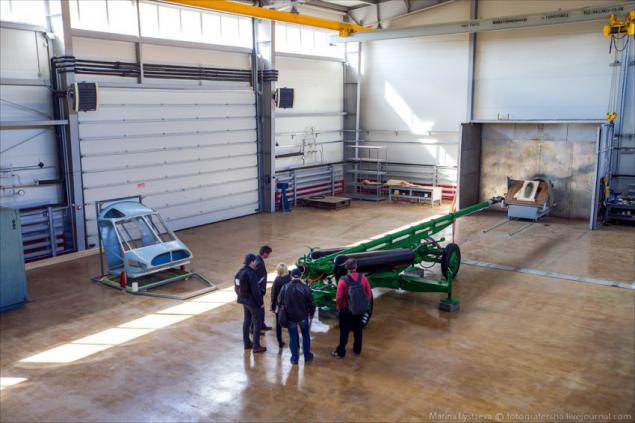
41. PU132 (where 132 - the inner diameter of the barrel) can throw stones, metal bars, ice balls at a rate of 100 to 1900 km / h. There are vandal-proof test, in which the fire bottle. If the speed of a small object is charged with the direction of the muzzle.
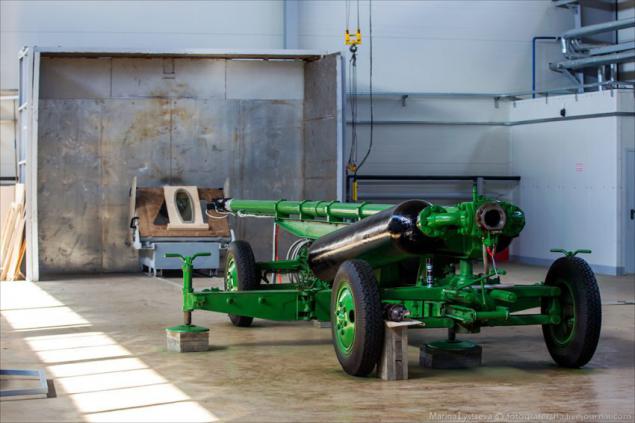
42. But the main throwing object - a bird. And it is not simple, but with a passport. Flyer comes with a special factory.
Depending on the type of glass and helicopter-type aircraft, train set speed and selected carcass weight (typically 1 kg).
From a single control room behind a thick glass special person made a shot.
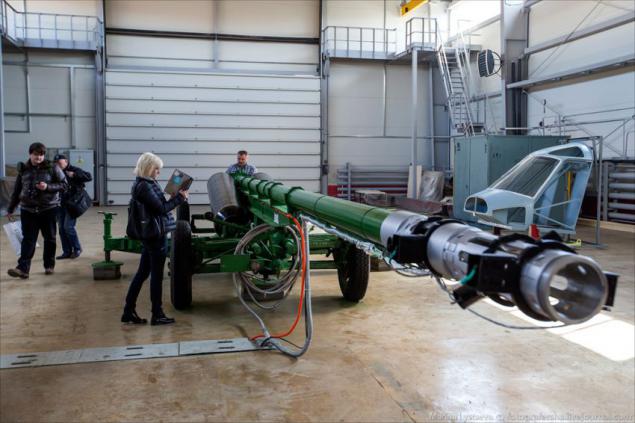
43. The cabin of the helicopter Ka-62 with a trace pound bird strike.
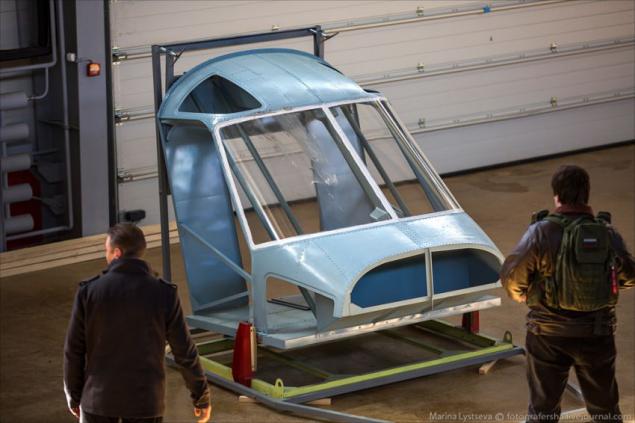
44. The tested model aircraft cabin windows in the back yard. And about a given last week's issue, see otgadku here.
In 2013, the company made:
- More than 70 panels and thermal solar panels for carcases of 11 satellites.
- By now in Earth orbit successfully operates 27 satellites, which included a production of "CVTs" Technology ".
- Manufactured and shipped shell nose cones, transfer compartment 3rd stage gargrot 1st, 2nd and 3rd stages, local fairings Motor 3-Tier:
• 10 carrier rockets "Proton-M"
• 1st rocket "Angara 5"
• 2 carrier rockets "Angara 1.2".
At the end of 2013 was successfully launched a fundamentally new carrier rocket "Soyuz 2.1V" to the block elimination "Volga", which included applied thermal control system of the new generation created on the basis of our panels. This launch was launched into Earth orbit research satellite "Stork" ultra-light carbon-fiber panels with solar panels and satellite body, made, again in Obninsk.
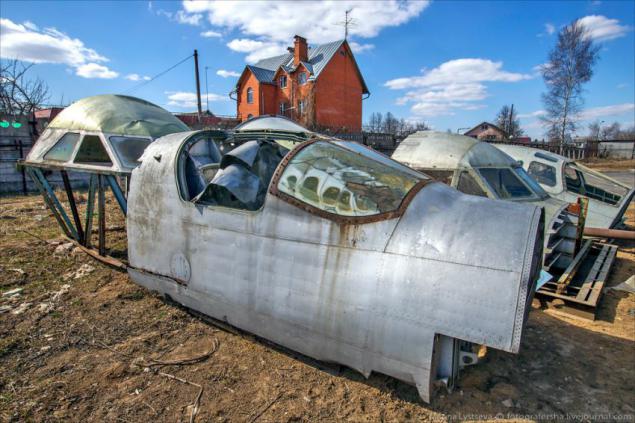
Source: fotografersha.livejournal.com