1709
0,4
2013-05-02
Русская кожа
Автор: Этому процессу много тысяч лет. Возможно, даже скорее всего, человек сначала научился именно ему, а потом уже раздобыл огонь.
Я не про процесс воспроизводства, я про выделку кожи. В России функционирует самый большой в Европе кожевенный завод – Рязанский, он же ЗАО “Русская кожа”. Идемте в гости.
Для начала немного цифр и истории, чтоб понять, так сказать, всю глубину наших глубин. Заводу скоро исполнится сто лет, его открыли за год до октябрьской революции. Он благополучно обрабатывал кожу крупного рогатого скота в советское время, и, что большая редкость, не прекратил своей деятельности ни в 90-е, ни позже. В 1988-ом году он был практически построен заново итальянскими товарищами, а модернизация оборудования происходит постоянно. Сейчас площадь производства в Рязани составляет 480000 квадратных метров, работает более двух тысяч человек. В 2006 году был открыт китайский филиал завода. Он намного меньше и в основном специализируется на обувной коже.
Почти половину своей продукции производство поставляет на экспорт в Италию, Португалию, Испанию, Францию и страны Азии. Я не буду показывать самый первый этап производства. На нем происходит приемка засоленных в бочках кож, их первичная сортировка и вымачивание в отмочно-зольных барабанах. 21 сырьевой филиал принимает кожи практически со всех крупных мясоперерабатывающих производств России. Это примерно 5200 тонн в месяц.
После вымачивания (отмока) лишенные волосяного покрова шкуры попадают на первый конвеер. Тут с ними особо не церемонятся и грузят устрашающего вида аппаратами.
Я так понимаю, в этом агрегате удаляется часть воды. На выходе четверо рабочих осматривают каждую шкуру и обрезают явный брак и остатки тканей и жира.
На первых этапах процесса самая тяжелая работа. Шкуры очень скользкие, ножи острые и вы не представляете, какой там стоит запах. За сутки обрабатывается 6000 шкур.
Далее для кож наступает один из самых ответственных процессов. В этих барабанах происходит дубление. За время этого процесса с помощью специальных химикатов из кож выводятся все микроорганизмы, прекращаются естественные процессы. Т.е. из живого материала кожа превращается в стандартный, соответствующий строгим требованиям, полуфабрикат.
Кожа на этом этапе называется wet-blue и после химической обработки хромом она действительно голубого цвета. Кожу, дубленую по старым рецептам, с использованием органических дубильных веществ, так же можно отличить по цвету. Она либо белая, либо желто-коричневая.
Вместе с wet-blue переместимся в отделочный цех.
Итак, вытащенные и высушенные wet-blue попадают на стол к этим женщинам. Именно они отвечают за сортировку и отбраковку на этом этапе.
Далее материал проходит процесс двоения. С помощью строгальной машины шкура расслаивается на два, а то и три слоя. Получается лицевая сторона и спилок.
Из лицевой стороны производят самую качественную кожу, но и из спилка делают кожи подешевле. Совсем стружку используют для приготовления клеев и технического желатина.
Некоторые заказчики предпочитают не связываться с первичной обработкой кожи, а производить на дальнейших этапах самостоятельную обработку и покупают у завода продукцию в стадии wet-blue. Это международный стандарт, так что в таком решении ничего странного нет.
Далее голубая кожа попадает в красильно-жировальные барабаны.
Они точно такие же, что и для дубления, только процессы в них происходят другие. На этом этапе задаются самые важные свойства будущей кожи: мягкость, износостойкость, упругость, эластичность. Тут же происходит покраска. Как вы понимаете, вариантов конечного продукта великое множество. Завод производит продукцию под заказ, так что судьба каждой единицы материала предопределена заранее.
Подобные барабаны используются не одним поколением кожевенников. Традиционно, сделаны из дерева твердых пород.
Если заглянуть внутрь, в темноте можно рассмотреть отлично отполированные стенки и штыри для дополнительного перемешивания кож.
Обработанные и окрашенные кожи называются краст. Он может быть различного цвета, с различными свойствами. Что-то подумалось, что ни на одном другом производстве я не видел столько брюнеток…
Процесс сушки может быть различным, но начинается чаще всего с отжима. Помните древние бочкообразные стиральные машинки с резиновыми валиками для отжима? Это увеличенная копия.
Кусочек гламура для разнообразия :)
Это атмосферная сушка. Красты совершают большой круг под потолком цеха, обозревают окрестности, заодно и сушатся.
А это другой вид сушки – рамный. На этом посту четверо рабочих принимают раму, снимают высушенные красты и натягивают новые. На замену уходит минуты три.
Рамы ходят по кругу. За стеной находится сушилка, где и происходит сушка. Насколько я понял, такой способ используется для сушки дорогих и мебельных кож. Кстати, тут отлично видно, что стандартный размер краста ровно половина шкуры. Мебельные кожи чаще всего целые.
Пункт очередного контроля качества. Хоть производство и механизировано/автоматизировано на 90%, но человеческий опыт заменить нельзя. Опытный контролер за пару секунд определяет плотность, толщину и качество кожи. Плюс лабораторный и колористический контроль выборочных экземпляров из каждой партии.
Переносимся в отделочный цех №2. Тут происходит конечная обработка и получение готовой продукции. Опять же, некоторые заказчики покупают краст и самостоятельно доводят его до ума, оставшийся краст подвергается финишным операциям.
Если на этапе получения краста вариантов множество, то тут их еще больше. Я даже примерно не представляю, сколько видов кожи можно получить на этих линиях. Во время финишной отделки задаются блеск, дополнительные цвета, тиснение, фактура и прочие спецэффекты. Тут краст обрабатывается с помощью напыления. В длинном конвеере кусок кожи проходит несколько этапов пропитки и просушки.
А тут другой принцип, напоминающий ламинацию или типографию. Кожа проходит через огромный красящий и одновременно высушивающий станок.
После всех этих перипетий на коже практически не остается фактуры. Эта машина состоит из, грубо говоря, утюга и пресса.
На горячую плиту нанесен объемный рисунок, который под прессом переносится на кожу.
Эта кожа скорее всего пойдет на изготовление спецодежды или обуви.
И вот, наконец, готовая кожа попадает на склад конечной продукции.
Происходит завершающий контроль качества, формируются партии. Кожу нельзя складывать конвертом, поэтому она сворачивается в рулоны по нескольку штук.
Время прохождения всех этапов производства очень сильно зависит от сложности выделки.
Производство мебельной кожи идет параллельно и этапами практически повторяет уже увиденное.
После рамной сушки кожи поступают на кунтурирование. Двое женщин с пневмоножами очень шустро обрезают края шкуры. Разглядеть, что именно они делают, мне удалось с третьего или четвертого захода.
Так же происходит финальная пропитка всякими веществами. Кожа для мебели более толстая и должна иметь очень высокие прочностные и износостойкие характеристики.
Ну и финальный контроль качества и сортировка. Кстати, при заводе работает собственная фабрика по изготовлению кожаной мебели, так что можно заказать совершенно эксклюзивные варианты.
Конечно же, нельзя было уйти, не посетив святая святых – лабораторию. Кстати, 500 тысяч квадратных метров это и правда много, рабочие передвигаются на велосипедах.
В лаборатории не только производится контроль качества продукции, но и разрабатываются новые технологии обработки, проверяются новые химические составы. Так же по эксклюзивным заказам тут изготавливаются маленькие партии кож с редкими рецептами обработки.
В небольшом лабораторном цеху можно воспроизвести любой этап процесса. Единственное, что я не нашел, так это пресс для тиснения.
Тут тоже стоят барабаны, только в несколько раз меньше.
Пропитки и краски разрабатываются тут же.
Специально для меня был пожертвован большой кусочек кожи для подбора нового цвета. Обычно, окрашивается кусочек раза в четыре меньше. Меня просили об этом упомянуть :)
Напоследок, меня привели в шоу-рум завода. Заказчику показывают именно его. Несколько десятков видов кож с огромным количеством вариантов тиснения, окраски и плотности. От привычной “кожаной” кожи с естественной фактурой, до чего-то кислотного, на ощупь и разрез больше всего напоминающее линолеум, от толстой ременной до тончайшей перчаточной.
С детства меня сильно интересовал вопрос о том, можно ли в трудные времена сварить из ботинок суп или закусить ремнем. Теперь могу с уверенностью сказать – можно, но бессмысленно и небезопасно для здоровья. После вымачивания в химии или известняке, дублении хромом или танином, питательные свойства кожи стремительно приближаются к нулю. Да и вообще говорить о “естественном природном материале” можно с большой натяжкой. Так что если вы соберетесь в трудный поход, запаситесь вещами из сыромятной кожи – их есть можно :)
Картинка для любителей животных.
Источник: zizis.livejournal.com
Я не про процесс воспроизводства, я про выделку кожи. В России функционирует самый большой в Европе кожевенный завод – Рязанский, он же ЗАО “Русская кожа”. Идемте в гости.
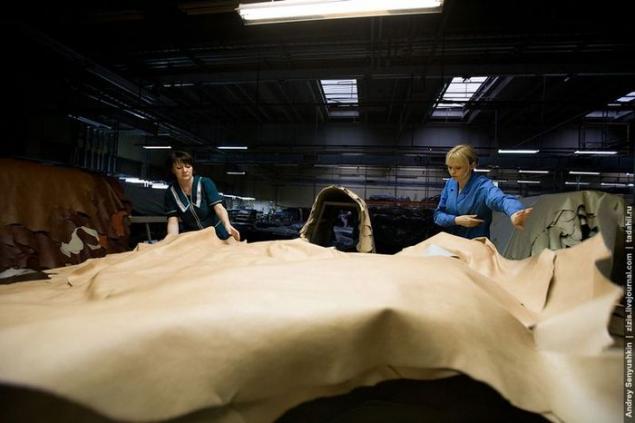
Для начала немного цифр и истории, чтоб понять, так сказать, всю глубину наших глубин. Заводу скоро исполнится сто лет, его открыли за год до октябрьской революции. Он благополучно обрабатывал кожу крупного рогатого скота в советское время, и, что большая редкость, не прекратил своей деятельности ни в 90-е, ни позже. В 1988-ом году он был практически построен заново итальянскими товарищами, а модернизация оборудования происходит постоянно. Сейчас площадь производства в Рязани составляет 480000 квадратных метров, работает более двух тысяч человек. В 2006 году был открыт китайский филиал завода. Он намного меньше и в основном специализируется на обувной коже.
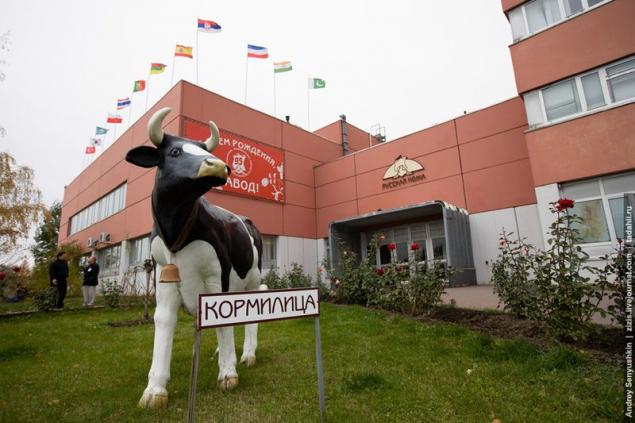
Почти половину своей продукции производство поставляет на экспорт в Италию, Португалию, Испанию, Францию и страны Азии. Я не буду показывать самый первый этап производства. На нем происходит приемка засоленных в бочках кож, их первичная сортировка и вымачивание в отмочно-зольных барабанах. 21 сырьевой филиал принимает кожи практически со всех крупных мясоперерабатывающих производств России. Это примерно 5200 тонн в месяц.
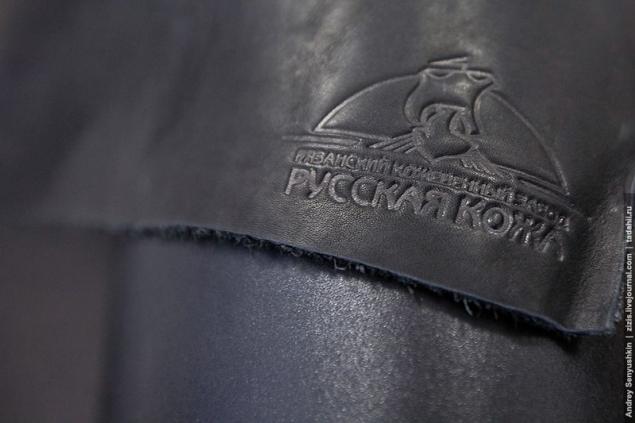
После вымачивания (отмока) лишенные волосяного покрова шкуры попадают на первый конвеер. Тут с ними особо не церемонятся и грузят устрашающего вида аппаратами.
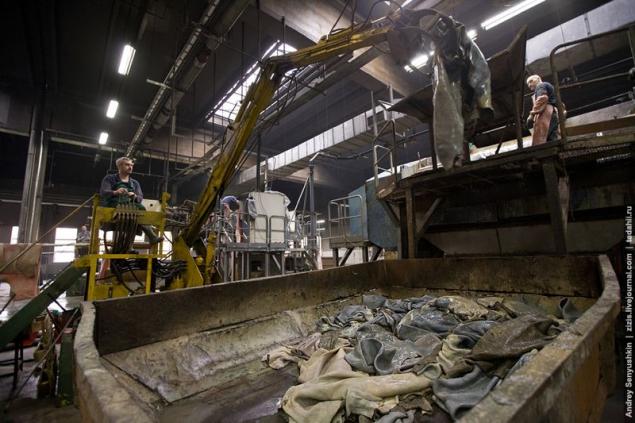
Я так понимаю, в этом агрегате удаляется часть воды. На выходе четверо рабочих осматривают каждую шкуру и обрезают явный брак и остатки тканей и жира.
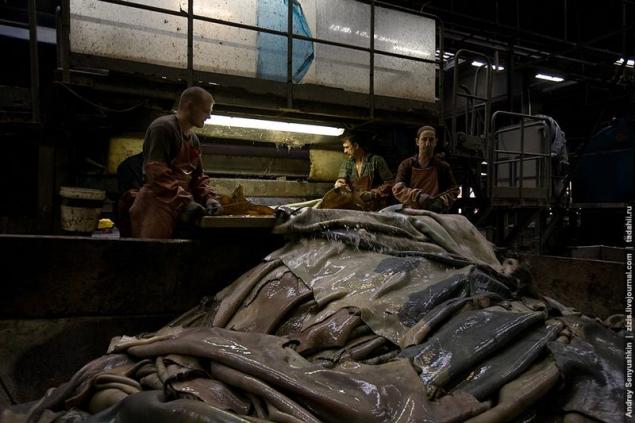
На первых этапах процесса самая тяжелая работа. Шкуры очень скользкие, ножи острые и вы не представляете, какой там стоит запах. За сутки обрабатывается 6000 шкур.
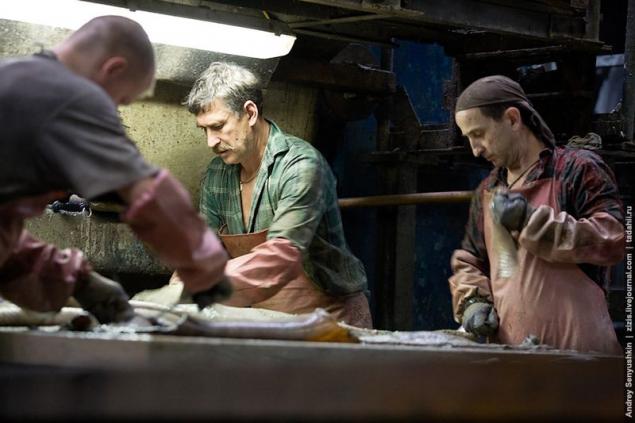
Далее для кож наступает один из самых ответственных процессов. В этих барабанах происходит дубление. За время этого процесса с помощью специальных химикатов из кож выводятся все микроорганизмы, прекращаются естественные процессы. Т.е. из живого материала кожа превращается в стандартный, соответствующий строгим требованиям, полуфабрикат.
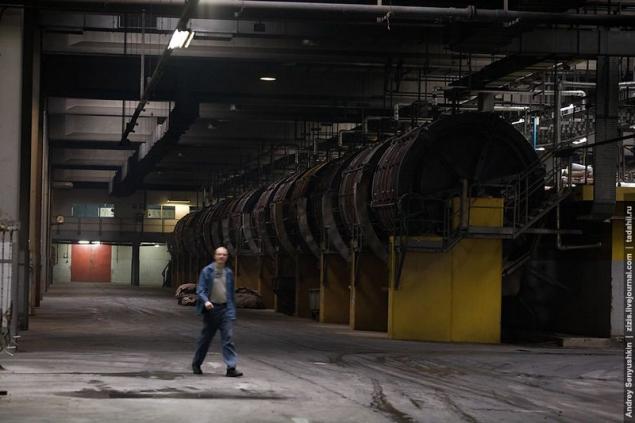
Кожа на этом этапе называется wet-blue и после химической обработки хромом она действительно голубого цвета. Кожу, дубленую по старым рецептам, с использованием органических дубильных веществ, так же можно отличить по цвету. Она либо белая, либо желто-коричневая.
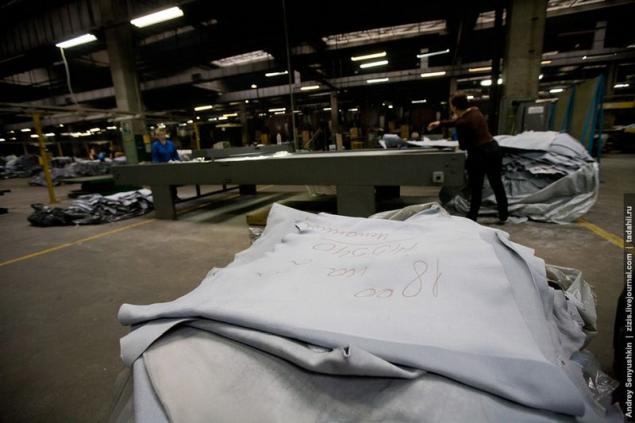
Вместе с wet-blue переместимся в отделочный цех.
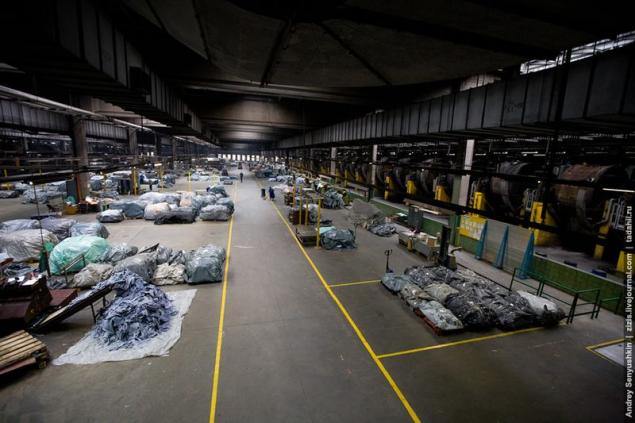
Итак, вытащенные и высушенные wet-blue попадают на стол к этим женщинам. Именно они отвечают за сортировку и отбраковку на этом этапе.
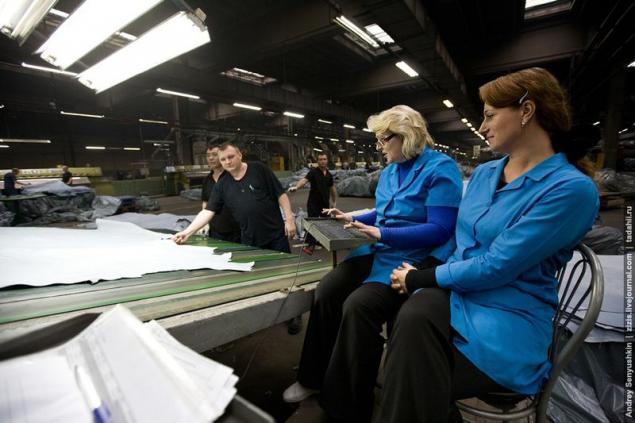
Далее материал проходит процесс двоения. С помощью строгальной машины шкура расслаивается на два, а то и три слоя. Получается лицевая сторона и спилок.
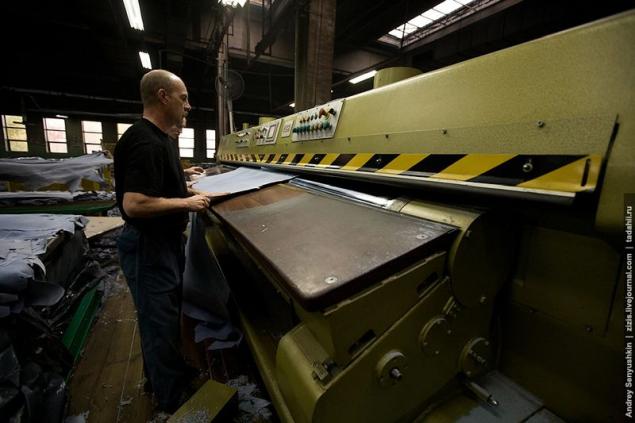
Из лицевой стороны производят самую качественную кожу, но и из спилка делают кожи подешевле. Совсем стружку используют для приготовления клеев и технического желатина.
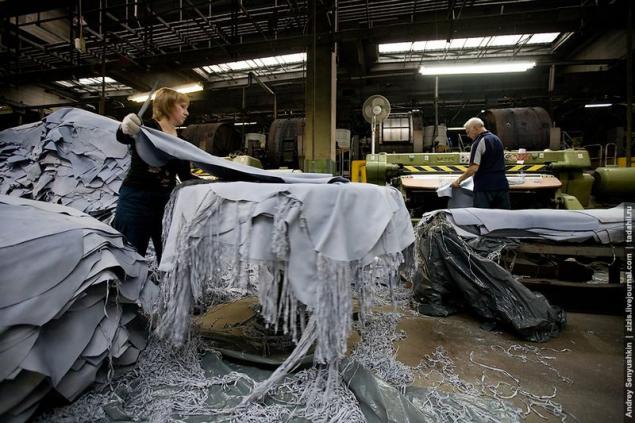
Некоторые заказчики предпочитают не связываться с первичной обработкой кожи, а производить на дальнейших этапах самостоятельную обработку и покупают у завода продукцию в стадии wet-blue. Это международный стандарт, так что в таком решении ничего странного нет.
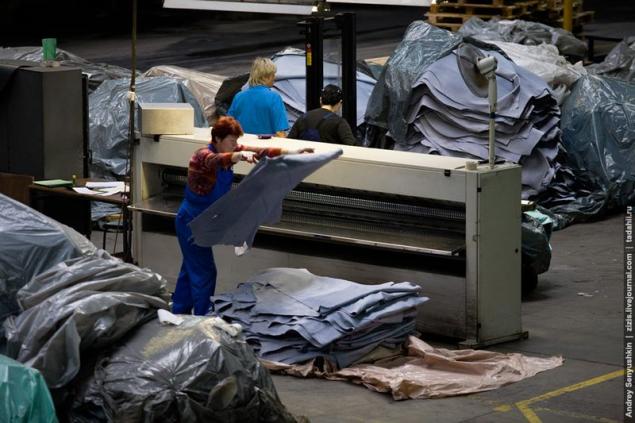
Далее голубая кожа попадает в красильно-жировальные барабаны.
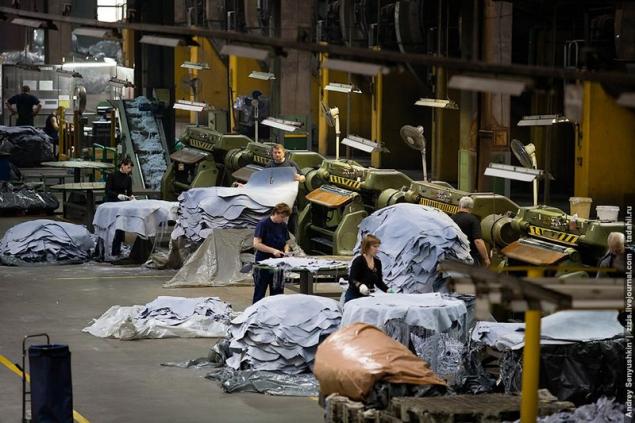
Они точно такие же, что и для дубления, только процессы в них происходят другие. На этом этапе задаются самые важные свойства будущей кожи: мягкость, износостойкость, упругость, эластичность. Тут же происходит покраска. Как вы понимаете, вариантов конечного продукта великое множество. Завод производит продукцию под заказ, так что судьба каждой единицы материала предопределена заранее.
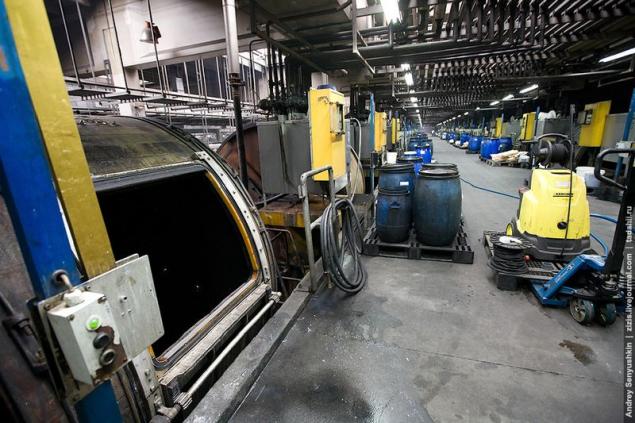
Подобные барабаны используются не одним поколением кожевенников. Традиционно, сделаны из дерева твердых пород.
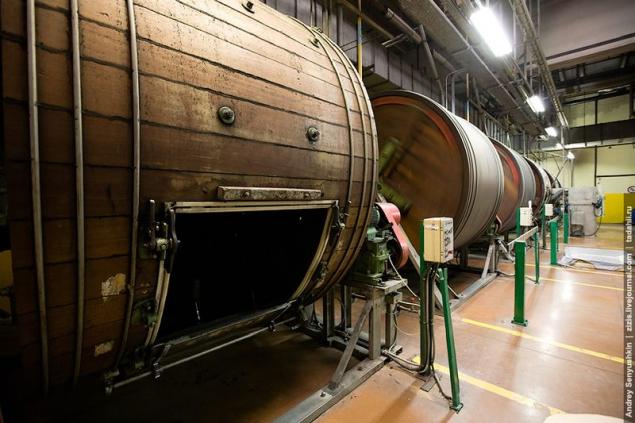
Если заглянуть внутрь, в темноте можно рассмотреть отлично отполированные стенки и штыри для дополнительного перемешивания кож.
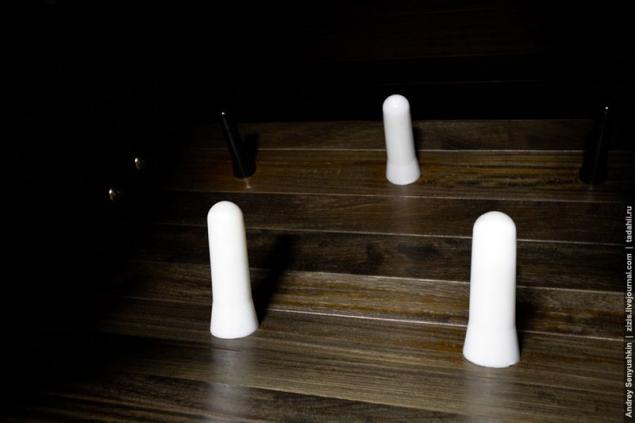
Обработанные и окрашенные кожи называются краст. Он может быть различного цвета, с различными свойствами. Что-то подумалось, что ни на одном другом производстве я не видел столько брюнеток…
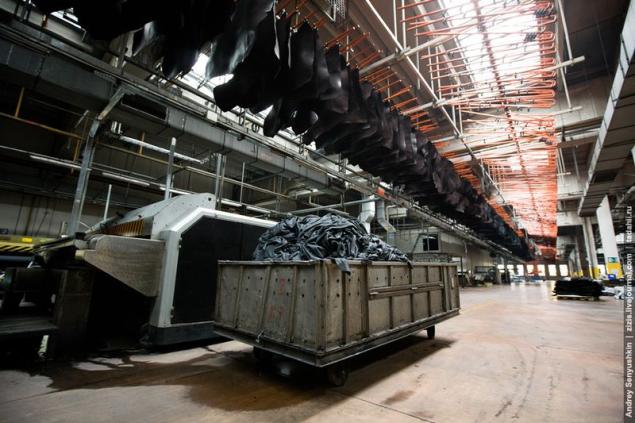
Процесс сушки может быть различным, но начинается чаще всего с отжима. Помните древние бочкообразные стиральные машинки с резиновыми валиками для отжима? Это увеличенная копия.
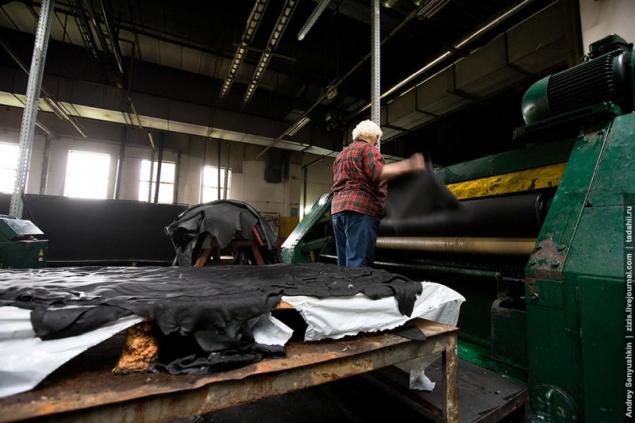
Кусочек гламура для разнообразия :)
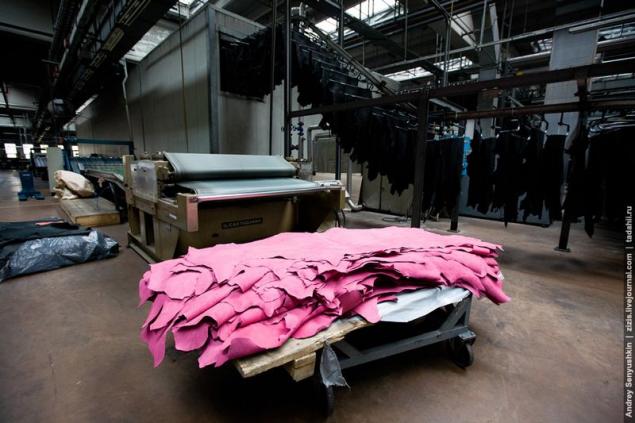
Это атмосферная сушка. Красты совершают большой круг под потолком цеха, обозревают окрестности, заодно и сушатся.
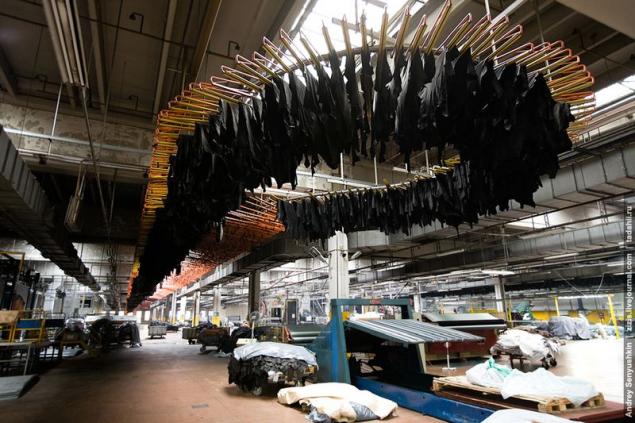
А это другой вид сушки – рамный. На этом посту четверо рабочих принимают раму, снимают высушенные красты и натягивают новые. На замену уходит минуты три.
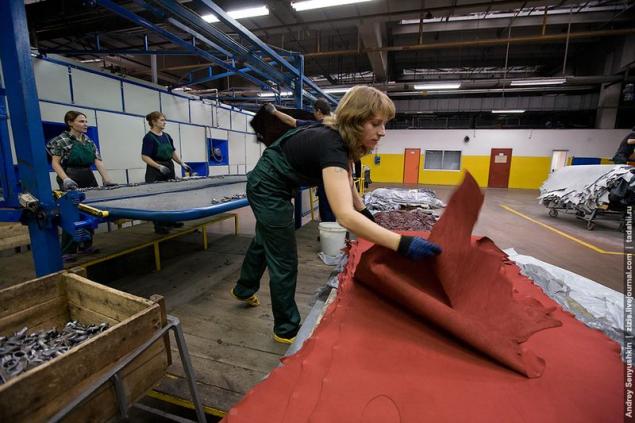
Рамы ходят по кругу. За стеной находится сушилка, где и происходит сушка. Насколько я понял, такой способ используется для сушки дорогих и мебельных кож. Кстати, тут отлично видно, что стандартный размер краста ровно половина шкуры. Мебельные кожи чаще всего целые.
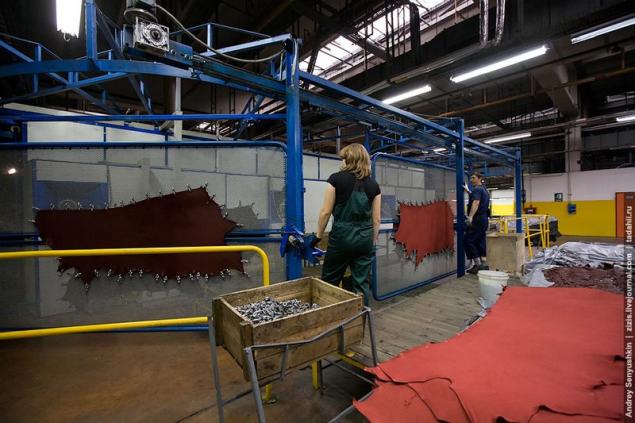
Пункт очередного контроля качества. Хоть производство и механизировано/автоматизировано на 90%, но человеческий опыт заменить нельзя. Опытный контролер за пару секунд определяет плотность, толщину и качество кожи. Плюс лабораторный и колористический контроль выборочных экземпляров из каждой партии.
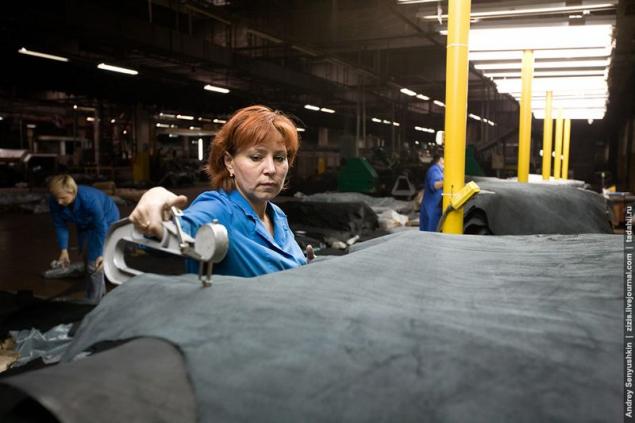
Переносимся в отделочный цех №2. Тут происходит конечная обработка и получение готовой продукции. Опять же, некоторые заказчики покупают краст и самостоятельно доводят его до ума, оставшийся краст подвергается финишным операциям.
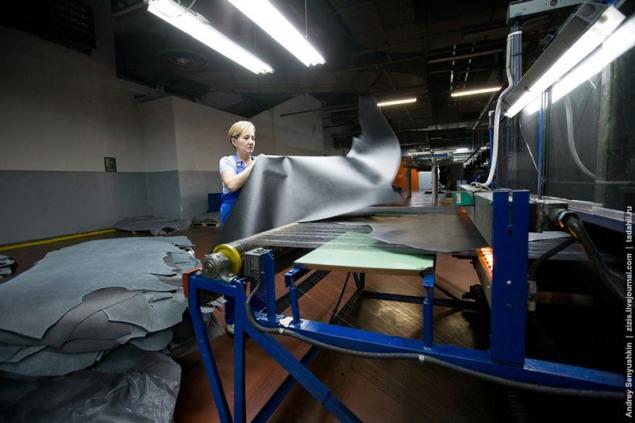
Если на этапе получения краста вариантов множество, то тут их еще больше. Я даже примерно не представляю, сколько видов кожи можно получить на этих линиях. Во время финишной отделки задаются блеск, дополнительные цвета, тиснение, фактура и прочие спецэффекты. Тут краст обрабатывается с помощью напыления. В длинном конвеере кусок кожи проходит несколько этапов пропитки и просушки.
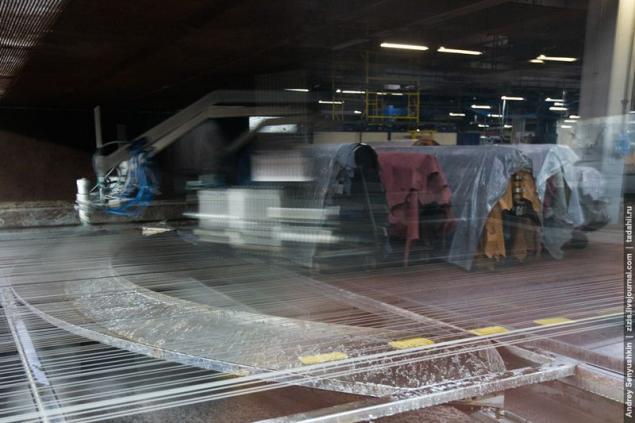
А тут другой принцип, напоминающий ламинацию или типографию. Кожа проходит через огромный красящий и одновременно высушивающий станок.
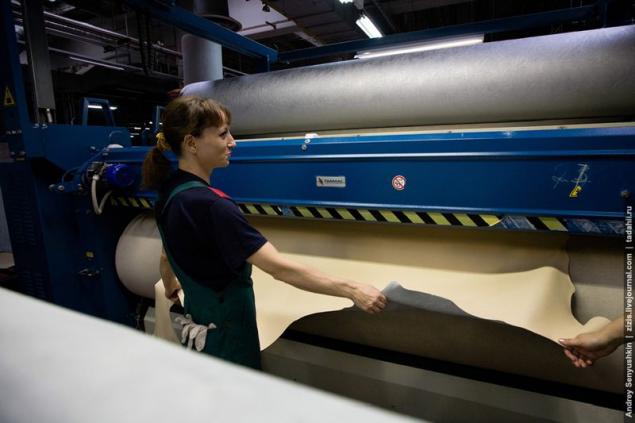
После всех этих перипетий на коже практически не остается фактуры. Эта машина состоит из, грубо говоря, утюга и пресса.
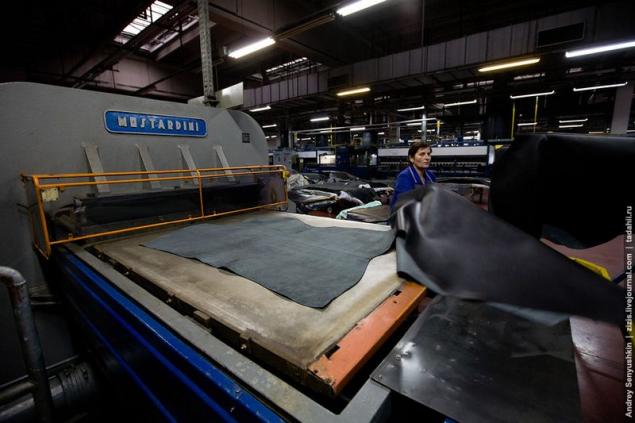
На горячую плиту нанесен объемный рисунок, который под прессом переносится на кожу.
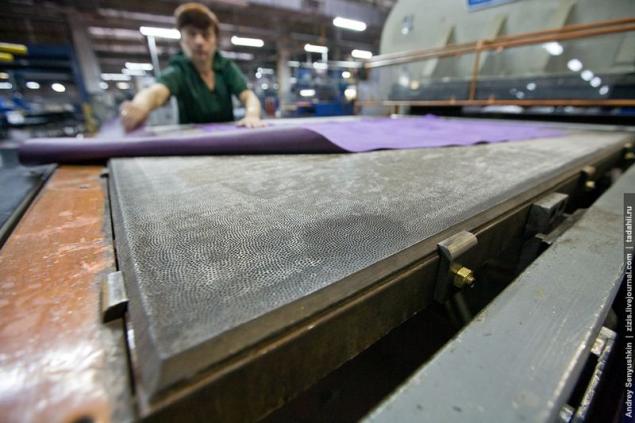
Эта кожа скорее всего пойдет на изготовление спецодежды или обуви.
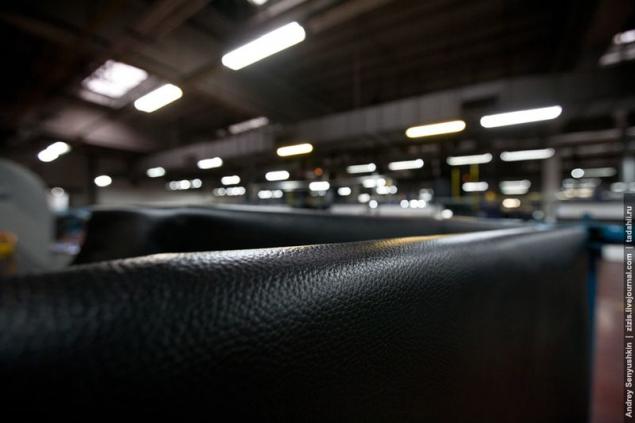
И вот, наконец, готовая кожа попадает на склад конечной продукции.
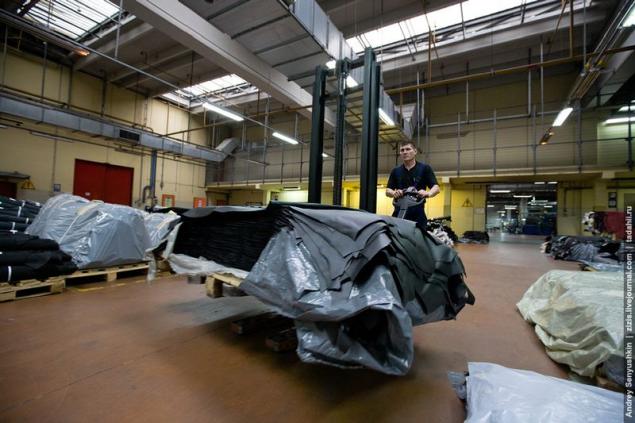
Происходит завершающий контроль качества, формируются партии. Кожу нельзя складывать конвертом, поэтому она сворачивается в рулоны по нескольку штук.
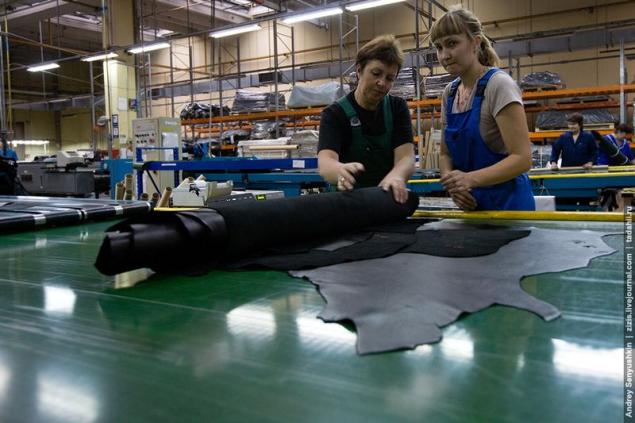
Время прохождения всех этапов производства очень сильно зависит от сложности выделки.
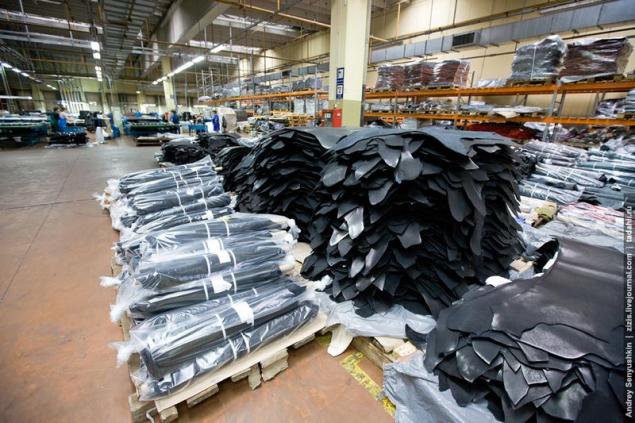
Производство мебельной кожи идет параллельно и этапами практически повторяет уже увиденное.
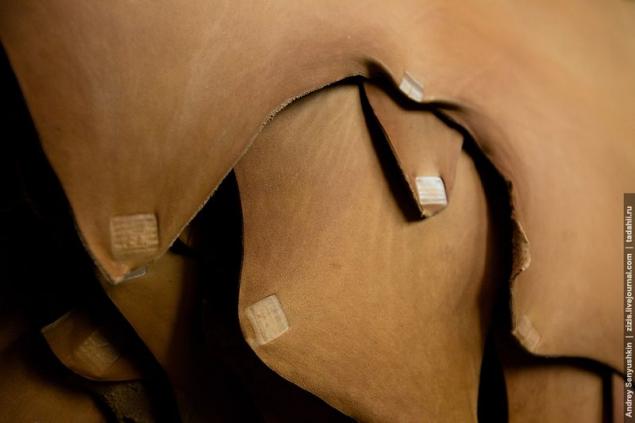
После рамной сушки кожи поступают на кунтурирование. Двое женщин с пневмоножами очень шустро обрезают края шкуры. Разглядеть, что именно они делают, мне удалось с третьего или четвертого захода.
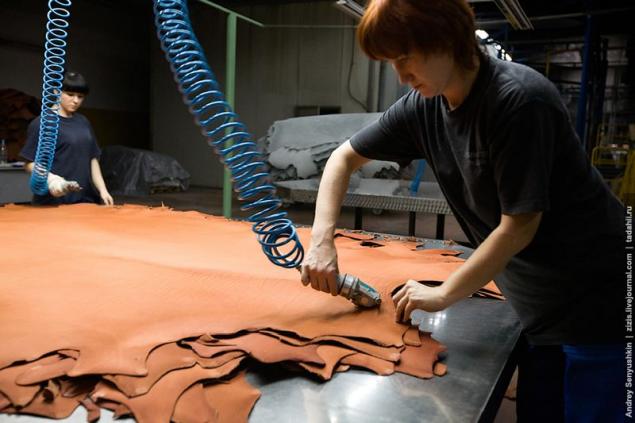
Так же происходит финальная пропитка всякими веществами. Кожа для мебели более толстая и должна иметь очень высокие прочностные и износостойкие характеристики.
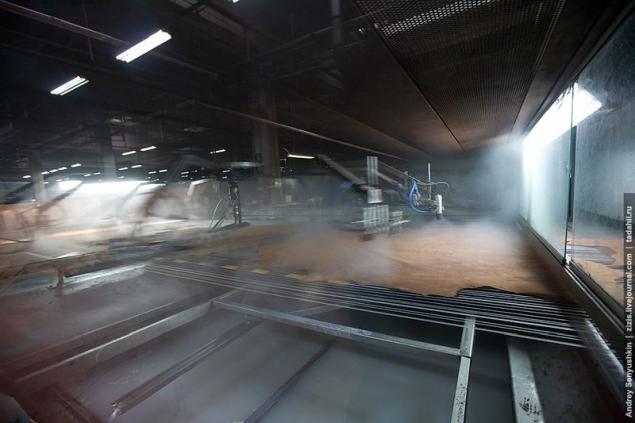
Ну и финальный контроль качества и сортировка. Кстати, при заводе работает собственная фабрика по изготовлению кожаной мебели, так что можно заказать совершенно эксклюзивные варианты.
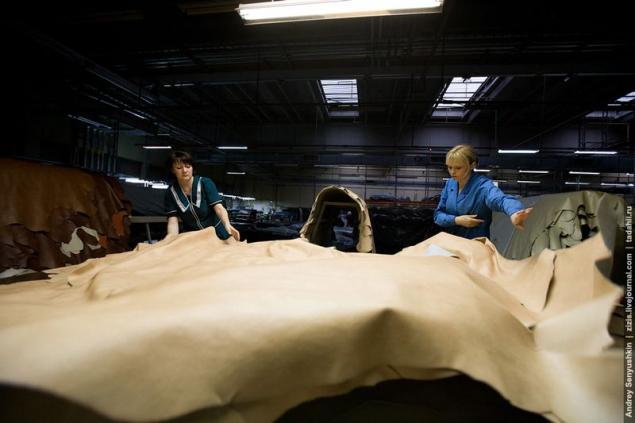
Конечно же, нельзя было уйти, не посетив святая святых – лабораторию. Кстати, 500 тысяч квадратных метров это и правда много, рабочие передвигаются на велосипедах.
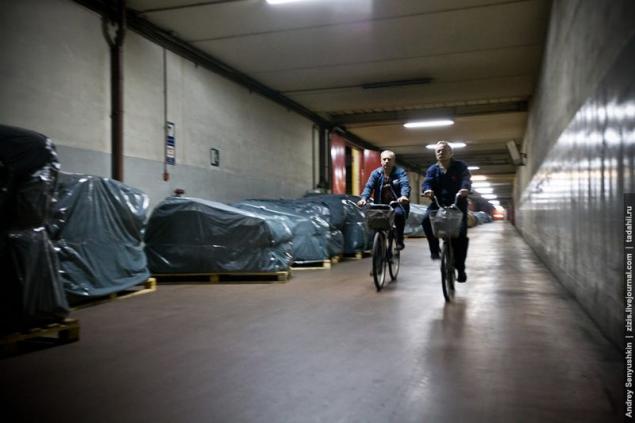
В лаборатории не только производится контроль качества продукции, но и разрабатываются новые технологии обработки, проверяются новые химические составы. Так же по эксклюзивным заказам тут изготавливаются маленькие партии кож с редкими рецептами обработки.
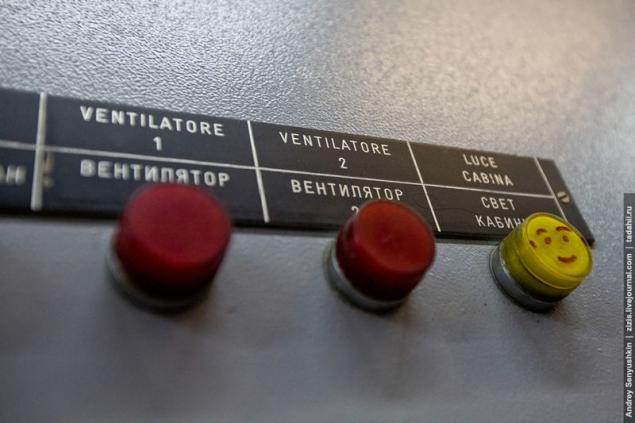
В небольшом лабораторном цеху можно воспроизвести любой этап процесса. Единственное, что я не нашел, так это пресс для тиснения.
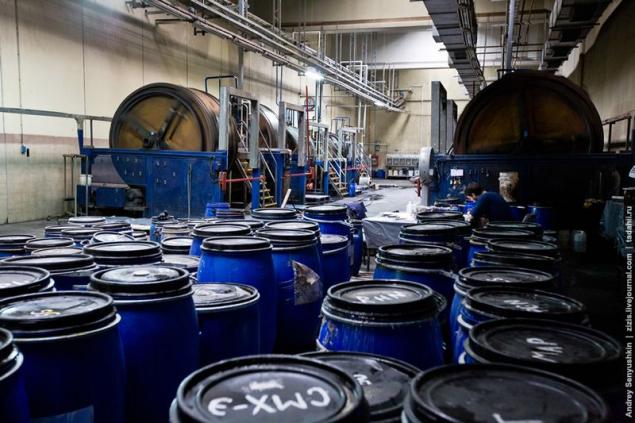
Тут тоже стоят барабаны, только в несколько раз меньше.
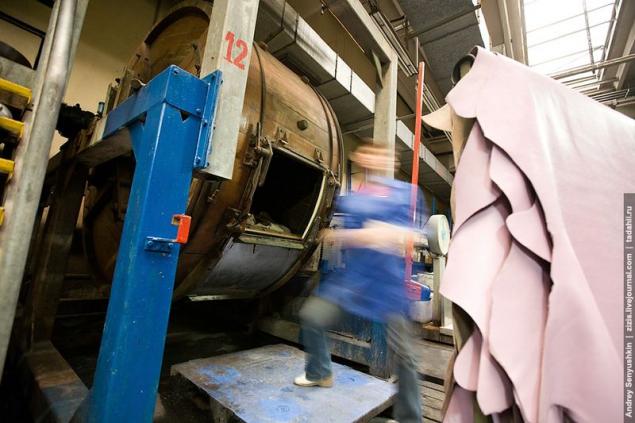
Пропитки и краски разрабатываются тут же.
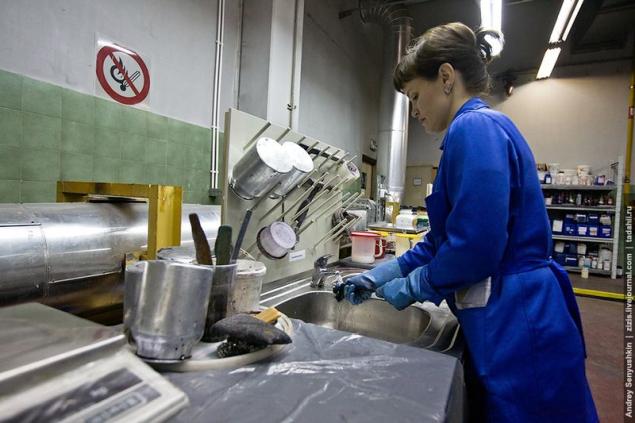
Специально для меня был пожертвован большой кусочек кожи для подбора нового цвета. Обычно, окрашивается кусочек раза в четыре меньше. Меня просили об этом упомянуть :)
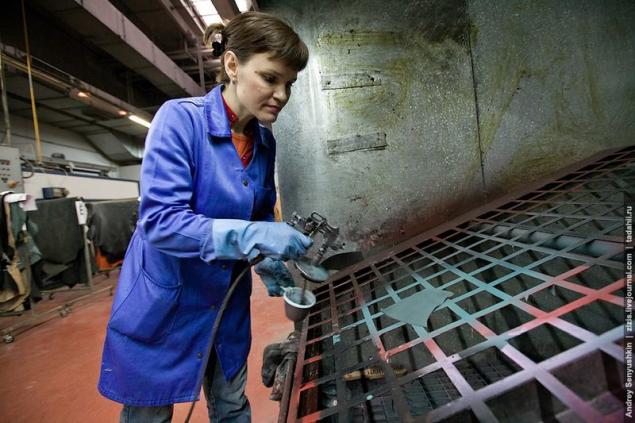
Напоследок, меня привели в шоу-рум завода. Заказчику показывают именно его. Несколько десятков видов кож с огромным количеством вариантов тиснения, окраски и плотности. От привычной “кожаной” кожи с естественной фактурой, до чего-то кислотного, на ощупь и разрез больше всего напоминающее линолеум, от толстой ременной до тончайшей перчаточной.
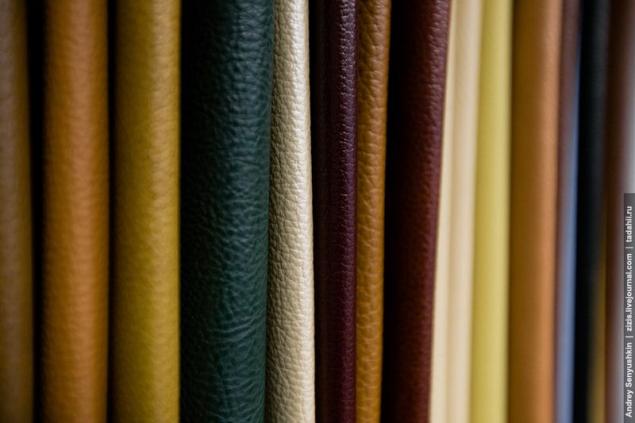
С детства меня сильно интересовал вопрос о том, можно ли в трудные времена сварить из ботинок суп или закусить ремнем. Теперь могу с уверенностью сказать – можно, но бессмысленно и небезопасно для здоровья. После вымачивания в химии или известняке, дублении хромом или танином, питательные свойства кожи стремительно приближаются к нулю. Да и вообще говорить о “естественном природном материале” можно с большой натяжкой. Так что если вы соберетесь в трудный поход, запаситесь вещами из сыромятной кожи – их есть можно :)
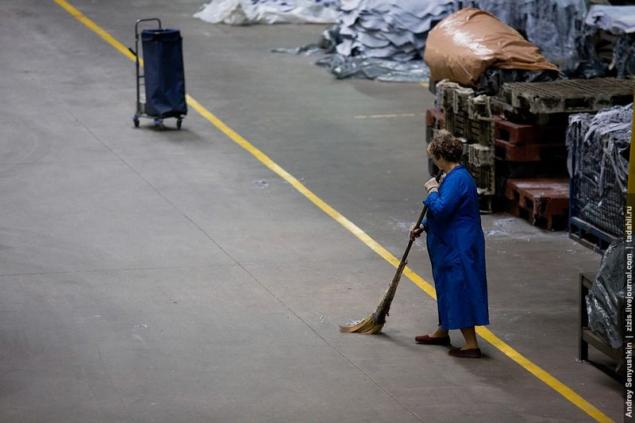
Картинка для любителей животных.
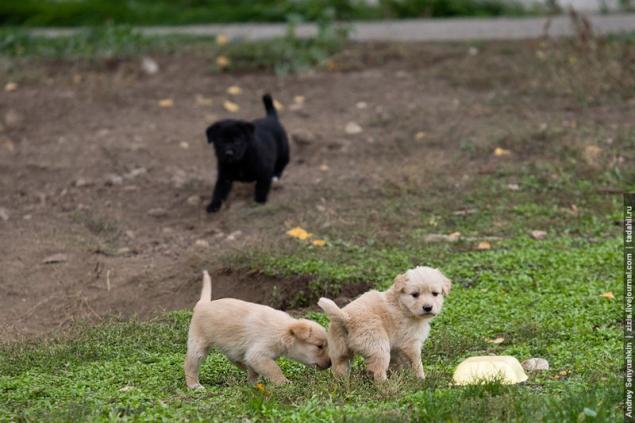
Источник: zizis.livejournal.com