732
Solar panels for space
This photoelectric converters - semiconductor devices that convert solar energy into direct current. Simply put, these are the main elements of the device, which we call "solar panels". With these batteries work space orbit satellites. Do we have such batteries in Krasnodar - the factory "Saturn».
27 photos via drugoi
Enterprise in Krasnodar is part of the Federal Space Agency. "Saturn" - one of the two leaders on the Russian market and the production of solar batteries for the needs of the space industry - civil and military. All profits earned by the "Saturn", is here in Krasnodar, and is on the development of the production base.
So, it all starts here - at the site of the so-called vapor-phase epitaxy. In this room there is a gas reactor, in which on a substrate made of germanium for three hours grown crystal layer, which will serve as the basis for future photocell. The cost of such a facility - about three million euros.
After that, the substrate is still a long way to go: on both sides of the photocell will cause the electrical contacts (and on the working side of the contact is imt "picture-size fits all", the dimensions of which are carefully calculated to maximize the passage of sunlight) on the substrate will be anti-reflection coating, etc. .d. - More than two dozen manufacturing operations at various plants before the photocell will form the basis of solar batteries.
For example, the installation of photolithography. Here on the solar cells are formed, "drawings" of electrical contacts. The machine performs all operations automatically, for a given program. Here and in the light of relevant, that does not harm the photosensitive layer solar cell - as before, in the era of analog photography, we used the "red" lights.
In a vacuum deposition installation using an electron beam are applied to the electrical contacts and insulators as well as antireflection coating applied (they increase the current generated by the photocell 30%).
Well, the photocell is ready and you are ready to assemble the solar cell. By surface photocell soldered tire, then to connect them with each other and are glued to the protective glass, without which the space, in terms of radiation, solar cell can not withstand the load. And, although the thickness of the glass only 0, 12 mm, battery with such solar cells will work in orbit for a long time (in high orbits for more than fifteen years).
08
09
The electrical connection between the solar cells are made of silver contacts (called Shinki) thickness of 0, 02 mm.
To obtain the desired supply voltage generated by a solar battery, solar cells are connected in series. Here is the section of the series-connected solar cells (photovoltaic cells - so right).
Finally, the solar battery is assembled. It shows only a part of the battery - panel layout format. Such panels on a satellite may have up to eight, depending on what is needed power. In today's communications satellites, it reaches 10 kW. These panels will be mounted on a satellite in space, they unfold like wings and with their help we will be watching satellite TV using satellite internet, navigation systems (satellites "Glonass" Krasnodar using solar panels).
13
When the spacecraft is illuminated by the Sun, produced by a solar battery supplies electricity to the machine, and the excess energy is stored in the battery. When the spacecraft is in the shadow of the Earth, the device uses the energy stored in the battery. Nickel-hydrogen battery having a high energy (60 Wh / kg) and virtually inexhaustible resource, is widely used in spacecraft. The production of such batteries - another part of the plant "Saturn».
In this image, the assembly of nickel-hydrogen battery produces Chevalier Medal of the Order "For Services to the Motherland» II degree Anatoly Panin.
15
Land assembly nickel-hydrogen battery. The filling is prepared by placing the battery in the case. Filling - is the positive and negative electrodes are separated by the separator paper - in them, and there is a transformation and accumulation of energy.
Apparatus for electron beam welding in vacuum by which the battery casing is made of thin metal.
The site shop, where body parts and batteries are tested for exposure to high pressure.
Due to the fact that the accumulation of energy in the battery is accompanied by the formation of hydrogen and the pressure inside the battery increases, the leak test - an integral part of the manufacturing process of the battery.
Housing nickel-hydrogen battery - very important detail of all device operating in space. The housing is designed for the pressure of 60 kg · s / cm2, test rupture occurred at a pressure of 148 kg · s / cm2.
Proven on the strength of the electrolyte and the battery is charged with hydrogen, after which they are ready to go.
Housing nickel-hydrogen battery is made of a special metal alloy and must be mechanically strong, lightweight and have a high thermal conductivity. The batteries are installed in the cell and not in contact with each other.
Batteries are collected and subjected to electric battery test on its own production. In space, nothing will be impossible to fix and replace, so there is carefully tested each product.
23
24
The entire space technology is being tested in the mechanical effects of vibration by using the stands that simulate load on removing space vehicles into orbit.
26
In general, the plant "Saturn" made a most favorable impression. Production is well organized, clean and bright workshops, qualified people work, communicate with such experts - a pleasure and a very interesting person, at least to some extent, the interests of our cosmos. Leaving with "Saturn" in a good mood - is always a pleasure to look at us in the place where it is not engaged in idle chatter or shift of paper and make a real, serious business, successfully competing with the same producers in the other countries. More to this in Russia.
Source:
27 photos via drugoi
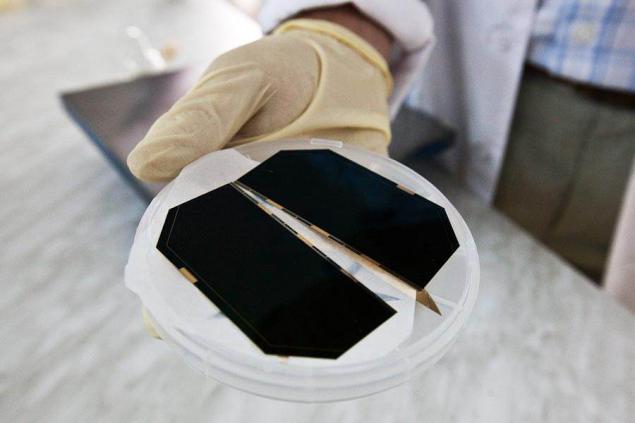
Enterprise in Krasnodar is part of the Federal Space Agency. "Saturn" - one of the two leaders on the Russian market and the production of solar batteries for the needs of the space industry - civil and military. All profits earned by the "Saturn", is here in Krasnodar, and is on the development of the production base.
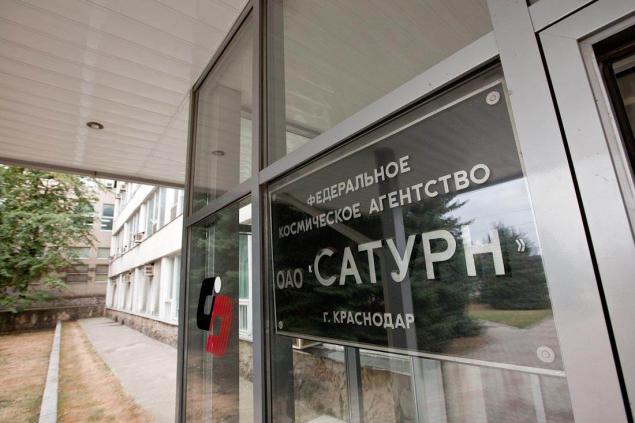
So, it all starts here - at the site of the so-called vapor-phase epitaxy. In this room there is a gas reactor, in which on a substrate made of germanium for three hours grown crystal layer, which will serve as the basis for future photocell. The cost of such a facility - about three million euros.
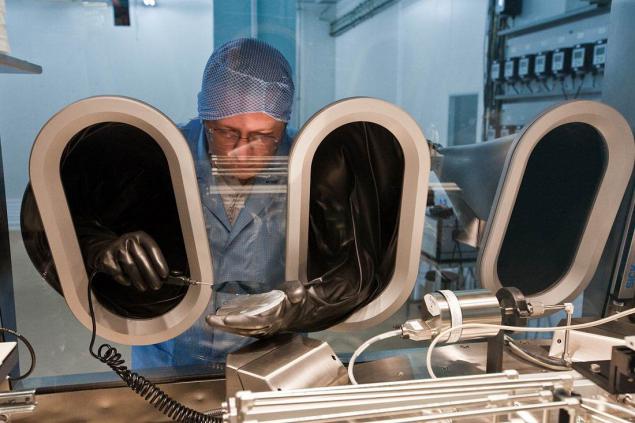
After that, the substrate is still a long way to go: on both sides of the photocell will cause the electrical contacts (and on the working side of the contact is imt "picture-size fits all", the dimensions of which are carefully calculated to maximize the passage of sunlight) on the substrate will be anti-reflection coating, etc. .d. - More than two dozen manufacturing operations at various plants before the photocell will form the basis of solar batteries.
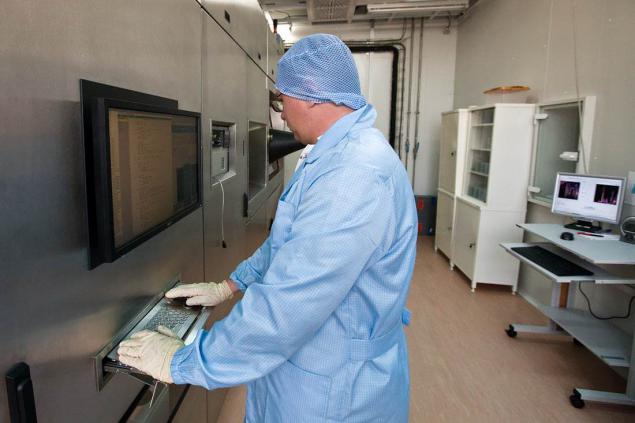
For example, the installation of photolithography. Here on the solar cells are formed, "drawings" of electrical contacts. The machine performs all operations automatically, for a given program. Here and in the light of relevant, that does not harm the photosensitive layer solar cell - as before, in the era of analog photography, we used the "red" lights.
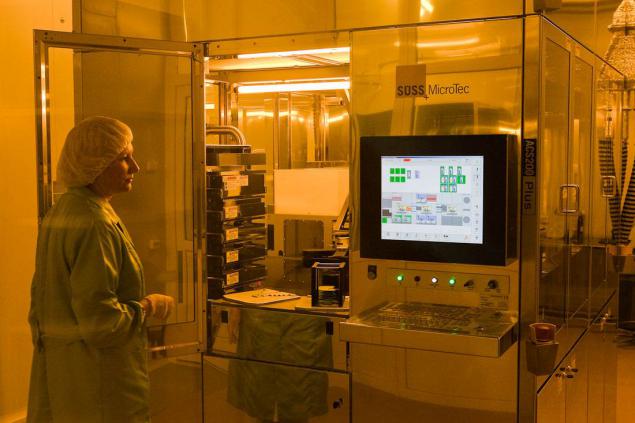
In a vacuum deposition installation using an electron beam are applied to the electrical contacts and insulators as well as antireflection coating applied (they increase the current generated by the photocell 30%).
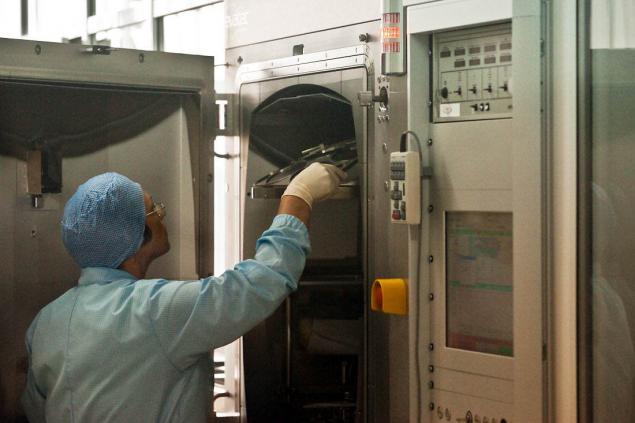
Well, the photocell is ready and you are ready to assemble the solar cell. By surface photocell soldered tire, then to connect them with each other and are glued to the protective glass, without which the space, in terms of radiation, solar cell can not withstand the load. And, although the thickness of the glass only 0, 12 mm, battery with such solar cells will work in orbit for a long time (in high orbits for more than fifteen years).
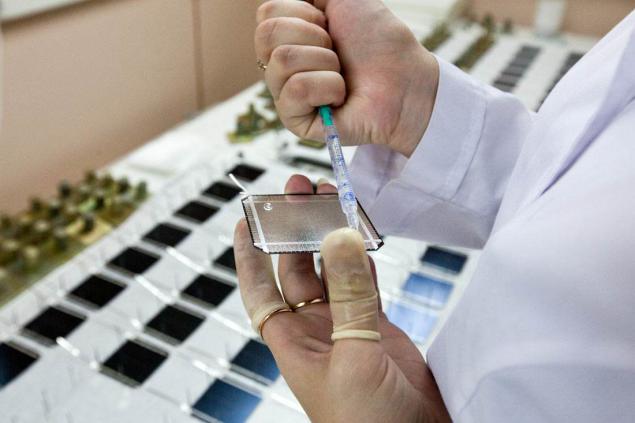
08
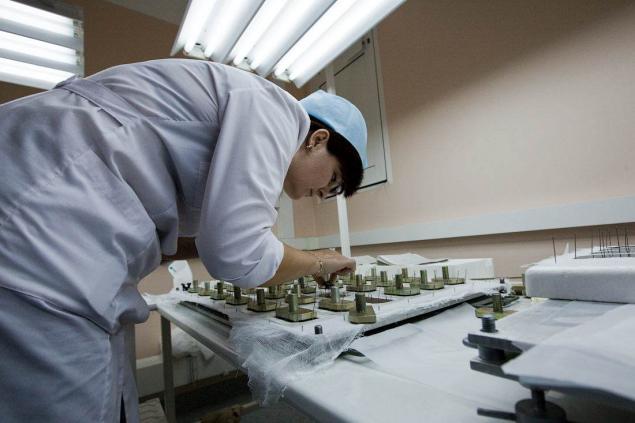
09
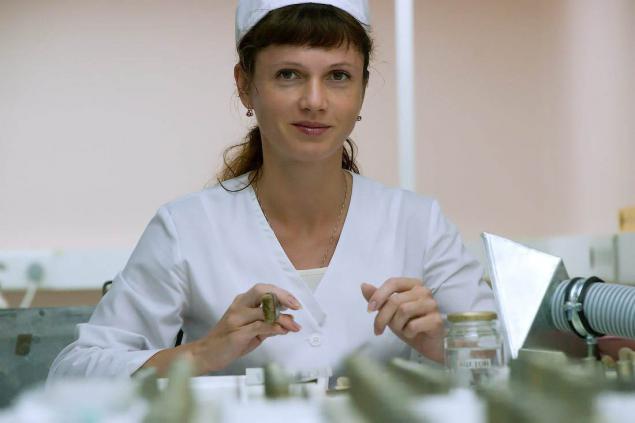
The electrical connection between the solar cells are made of silver contacts (called Shinki) thickness of 0, 02 mm.
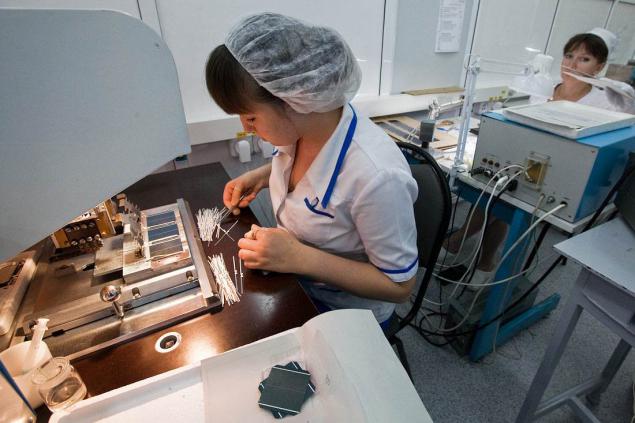
To obtain the desired supply voltage generated by a solar battery, solar cells are connected in series. Here is the section of the series-connected solar cells (photovoltaic cells - so right).
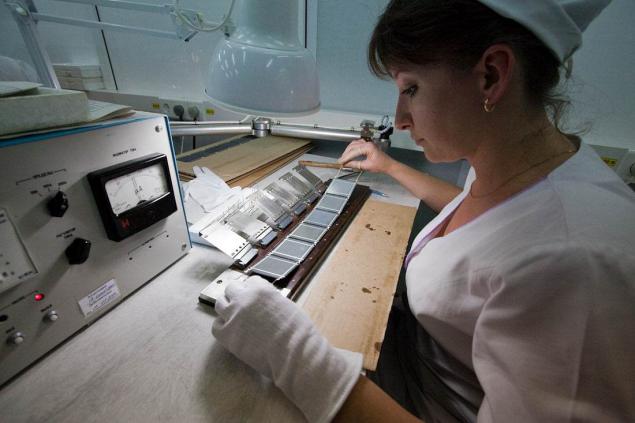
Finally, the solar battery is assembled. It shows only a part of the battery - panel layout format. Such panels on a satellite may have up to eight, depending on what is needed power. In today's communications satellites, it reaches 10 kW. These panels will be mounted on a satellite in space, they unfold like wings and with their help we will be watching satellite TV using satellite internet, navigation systems (satellites "Glonass" Krasnodar using solar panels).
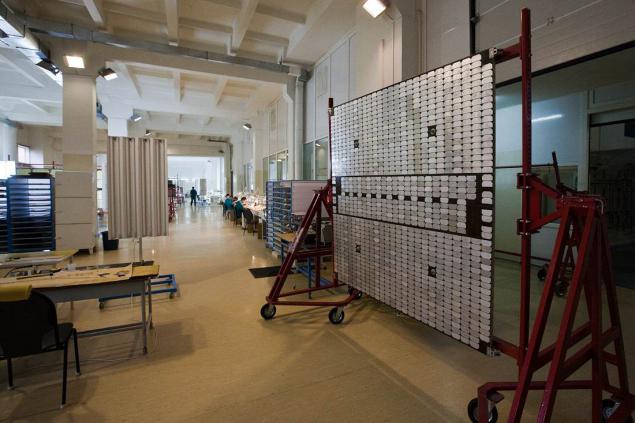
13

When the spacecraft is illuminated by the Sun, produced by a solar battery supplies electricity to the machine, and the excess energy is stored in the battery. When the spacecraft is in the shadow of the Earth, the device uses the energy stored in the battery. Nickel-hydrogen battery having a high energy (60 Wh / kg) and virtually inexhaustible resource, is widely used in spacecraft. The production of such batteries - another part of the plant "Saturn».
In this image, the assembly of nickel-hydrogen battery produces Chevalier Medal of the Order "For Services to the Motherland» II degree Anatoly Panin.
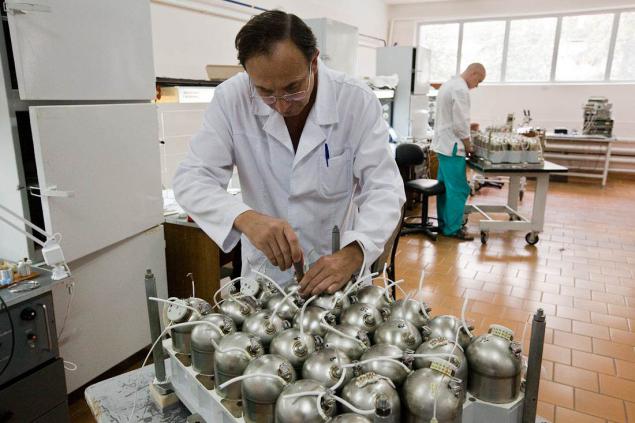
15
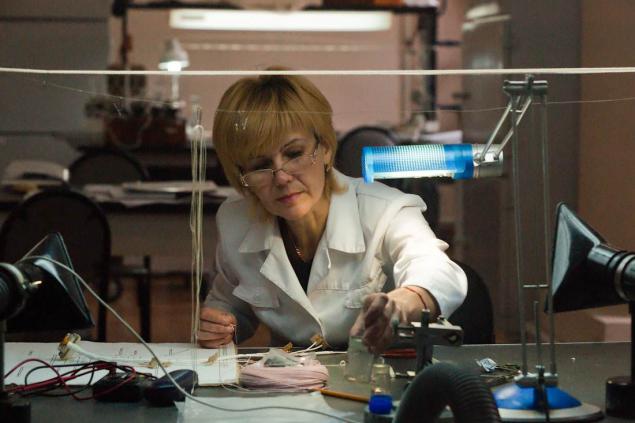
Land assembly nickel-hydrogen battery. The filling is prepared by placing the battery in the case. Filling - is the positive and negative electrodes are separated by the separator paper - in them, and there is a transformation and accumulation of energy.
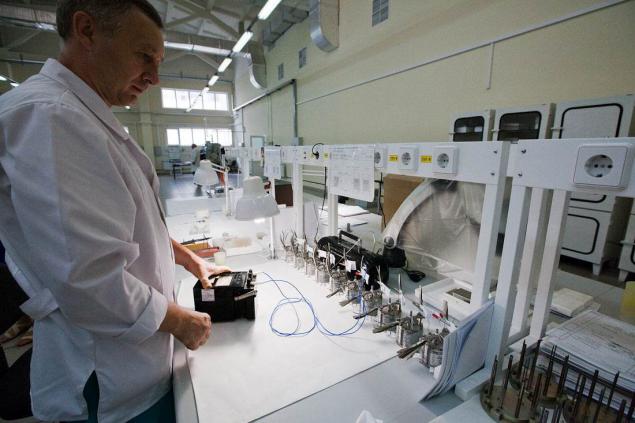
Apparatus for electron beam welding in vacuum by which the battery casing is made of thin metal.

The site shop, where body parts and batteries are tested for exposure to high pressure.
Due to the fact that the accumulation of energy in the battery is accompanied by the formation of hydrogen and the pressure inside the battery increases, the leak test - an integral part of the manufacturing process of the battery.
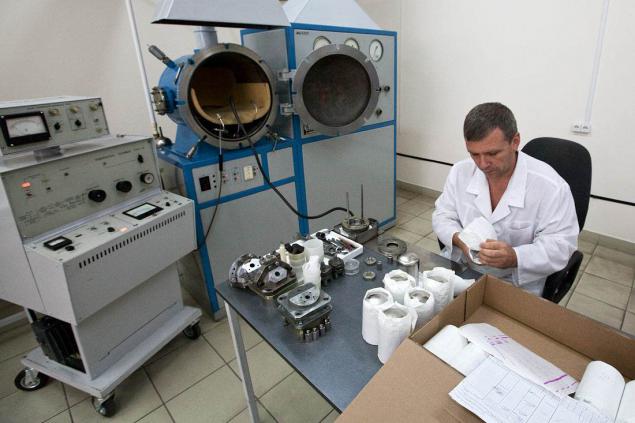
Housing nickel-hydrogen battery - very important detail of all device operating in space. The housing is designed for the pressure of 60 kg · s / cm2, test rupture occurred at a pressure of 148 kg · s / cm2.
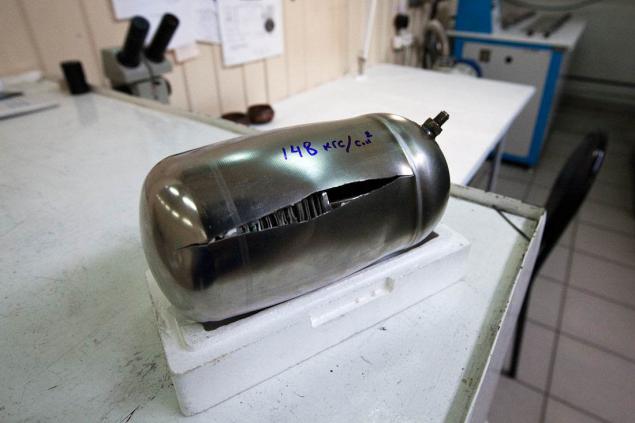
Proven on the strength of the electrolyte and the battery is charged with hydrogen, after which they are ready to go.
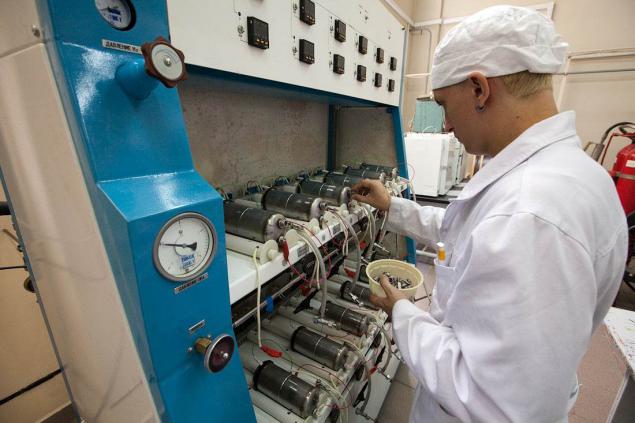
Housing nickel-hydrogen battery is made of a special metal alloy and must be mechanically strong, lightweight and have a high thermal conductivity. The batteries are installed in the cell and not in contact with each other.
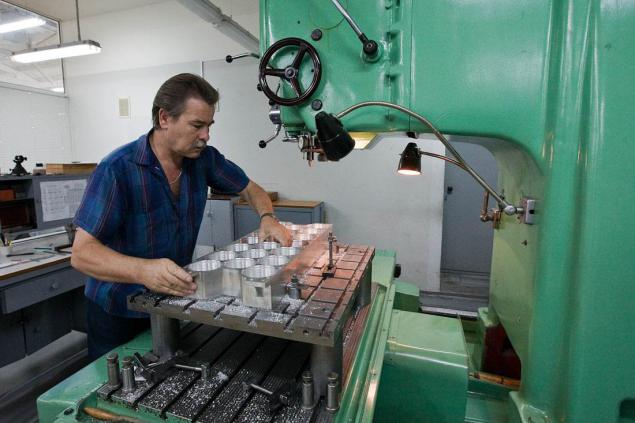
Batteries are collected and subjected to electric battery test on its own production. In space, nothing will be impossible to fix and replace, so there is carefully tested each product.
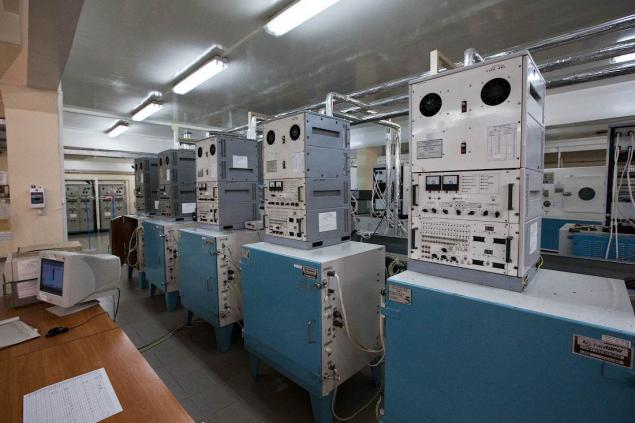
23
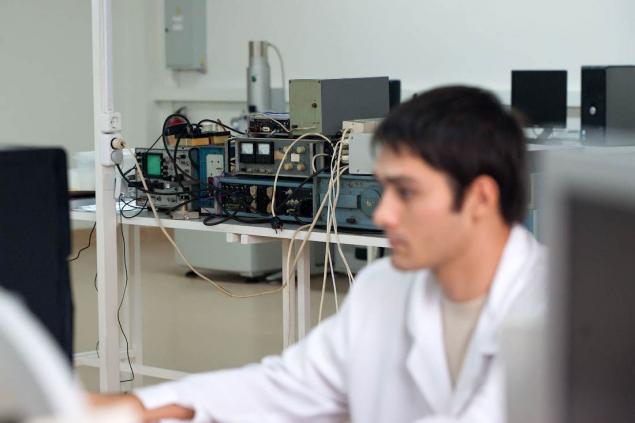
24
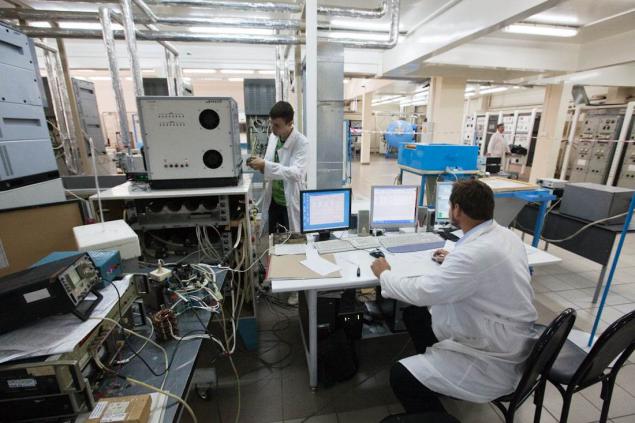
The entire space technology is being tested in the mechanical effects of vibration by using the stands that simulate load on removing space vehicles into orbit.
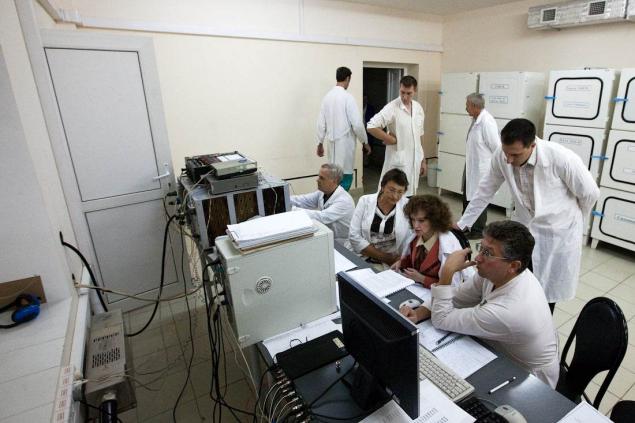
26
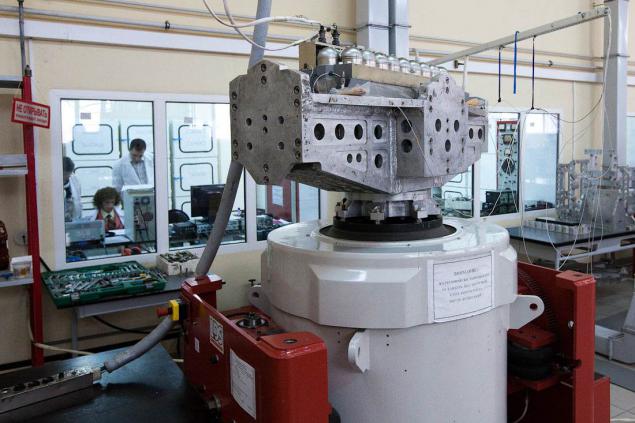
In general, the plant "Saturn" made a most favorable impression. Production is well organized, clean and bright workshops, qualified people work, communicate with such experts - a pleasure and a very interesting person, at least to some extent, the interests of our cosmos. Leaving with "Saturn" in a good mood - is always a pleasure to look at us in the place where it is not engaged in idle chatter or shift of paper and make a real, serious business, successfully competing with the same producers in the other countries. More to this in Russia.
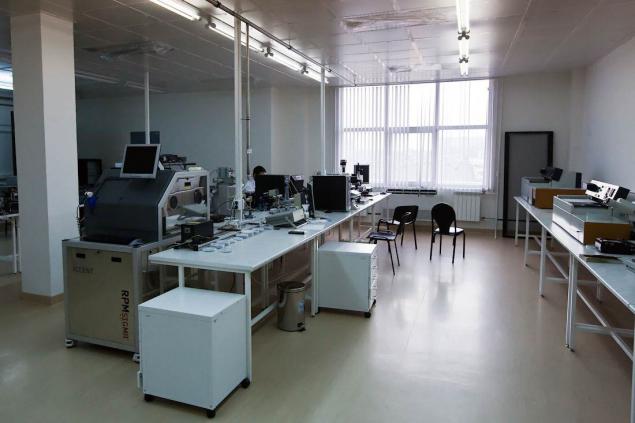
Source: